Text: Thomas Masuch; Photos: Daimler Buses — 06 September 2020
Up to this point, the 3D Printing of spare parts has been one of the proven – if somewhat unspectacular – applications of Additive Manufacturing. At Daimler Buses, however, the tremendous potential of this field and the business models it could enable in the future are now coming into focus.
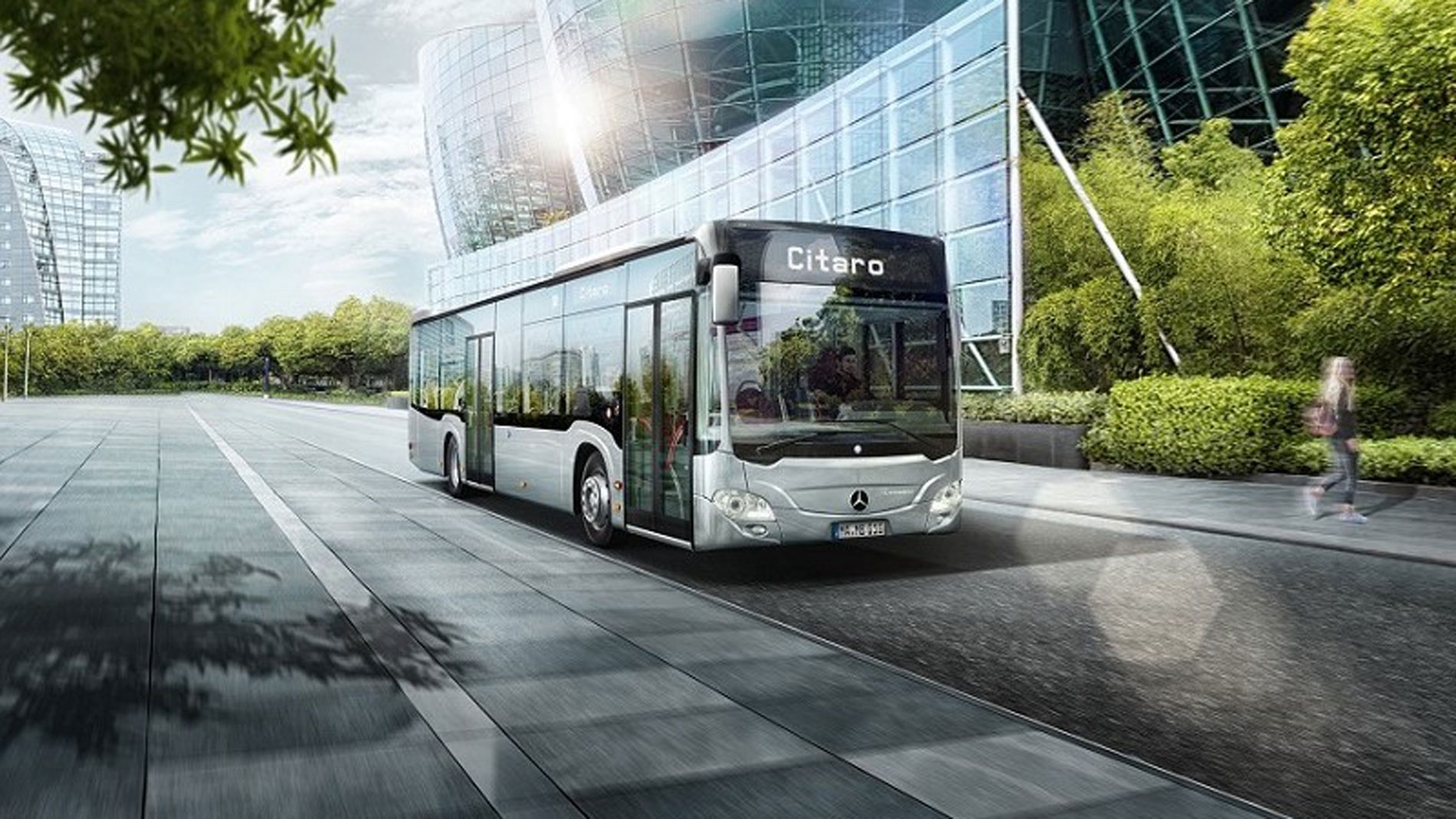
When a bus company orders new custom-designed handholds for the seats on a Setra or Mercedes-Benz bus, the officially labeled handhold inserts are made by a 3D printer. These plastic components are manufactured by a certified service provider of Daimler Buses, which then inspects the parts itself before sending them on to the customer. »This is already the established process for more than 350 3D-printed spare parts in our bus and truck division. In terms of fully approved small-series components, that makes us one of the world’s pioneers in 3D printing,« says Ralf Anderhofstadt, who heads the Center of Competence 3D-Printing, a facility that was founded at Daimler Trucks & Buses in early 2019. This leading position is the result of all of Daimler Buses’ development efforts with regard to materials and related approval processes, as well as in component identification and certification. Meanwhile, the 38-year-old pace-setter in 3D Printing has already been thinking about the next big thing for some time: the decentralized, autonomous manufacturing of the future, for example, which Anderhofstadt believes will raise the current model to a new level.
"As a result, our potential is always increasing."
Over 318,000 active spare parts in the bus sector
For now, however, let’s stay in the present. Daimler Buses currently has more than 318,000 active spare parts for its fleet. The company keeps 120,000 of them in a storage facility that is replenished daily by around 50 truck deliveries bearing up to 1,300 pallets. In addition to guaranteeing an availability period of 15 years for its spare parts, Daimler Buses strives to ensure that its customers have the best possible access to components. »In certain situations, that can be a real challenge,« Anderhofstadt reveals. »After a good number of years, it’s often the case that suppliers no longer have certain tools – or even worse, the suppliers simply don’t exist anymore. That’s when it’s twice as problematic: Customers spend more time waiting for the parts they need, and we face additional costs. We want to use Additive Manufacturing not only to relieve our internal pain points in this area, but especially to offer our customers much shorter delivery times, as well.«
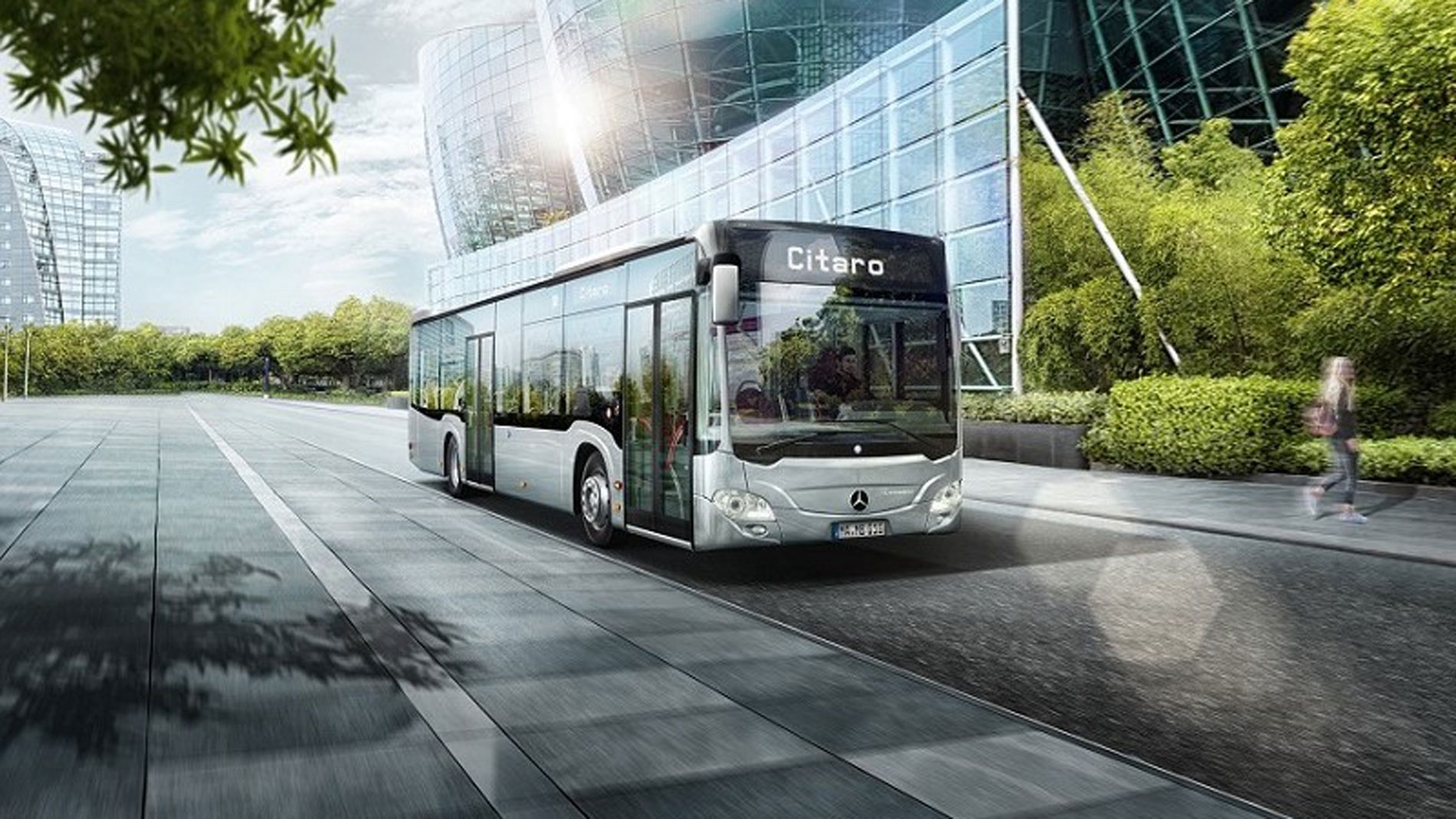
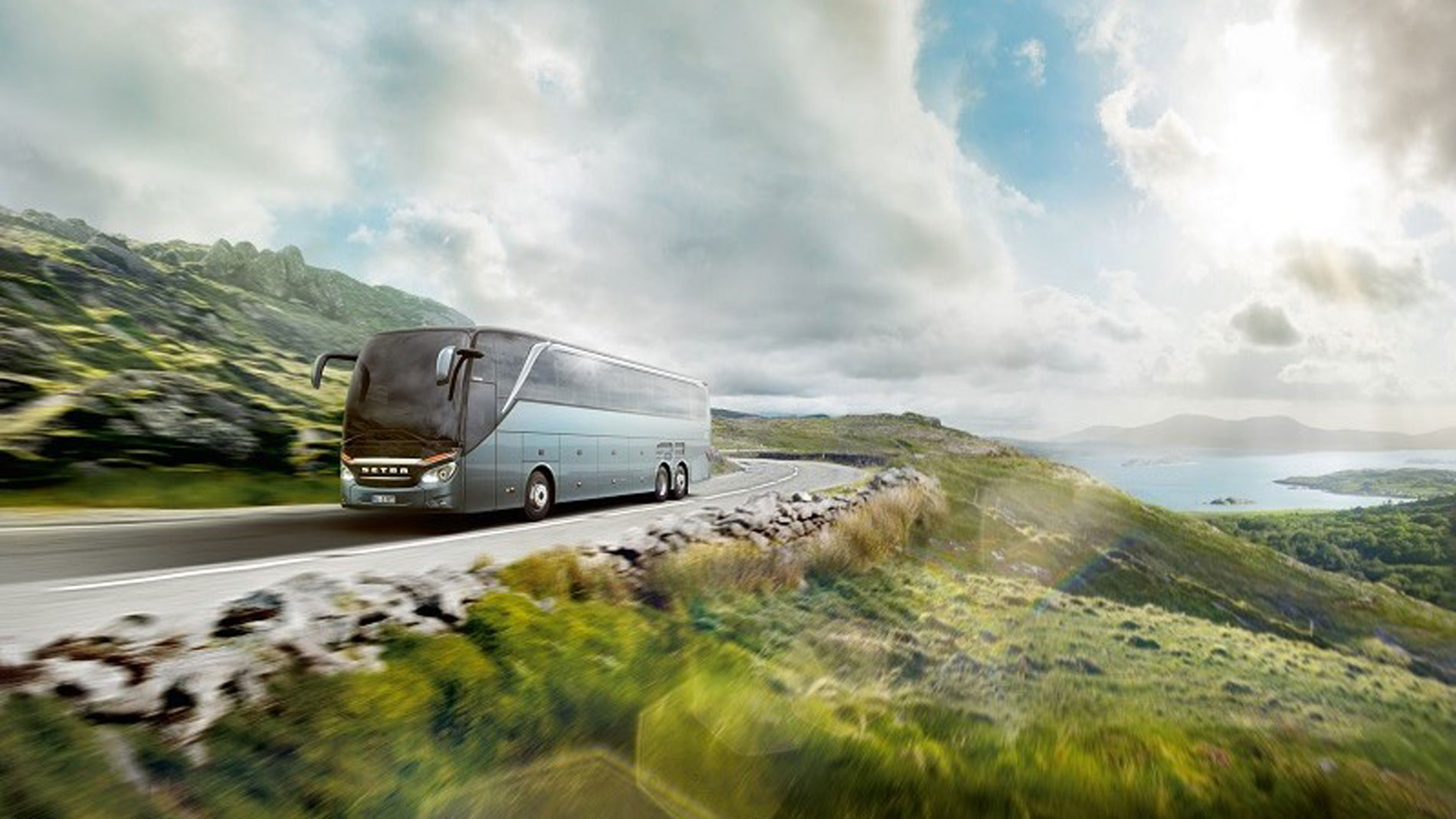
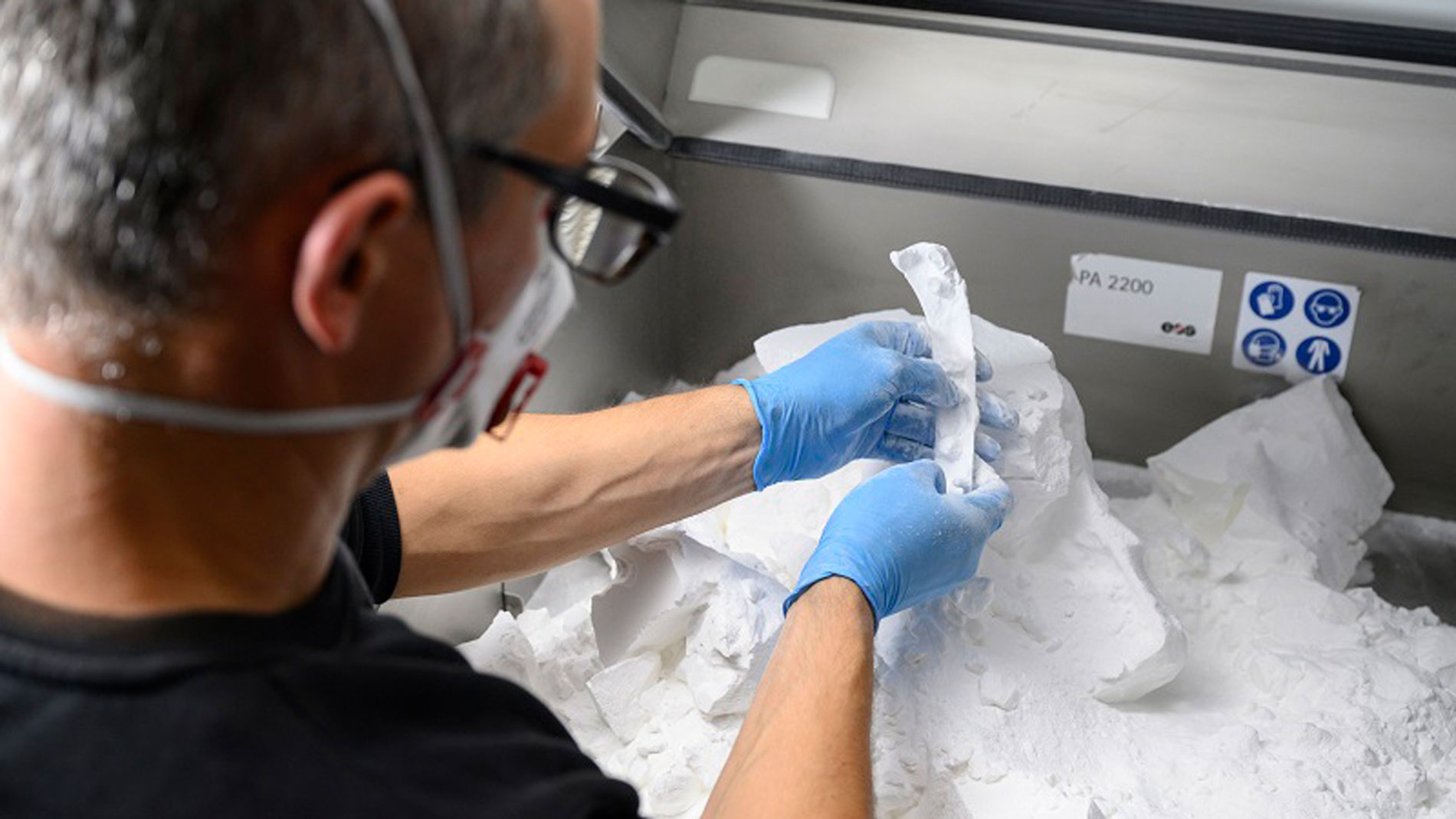
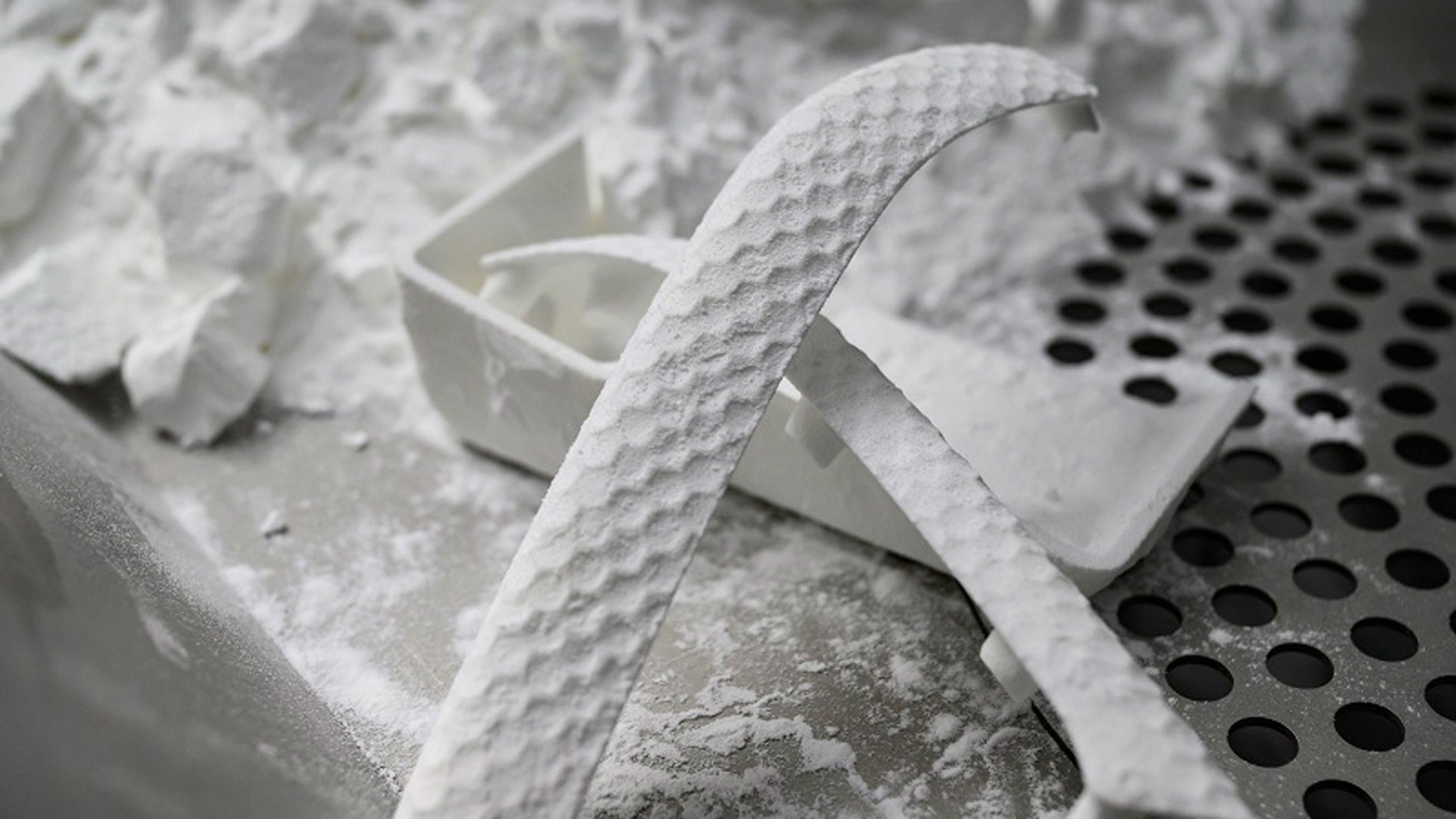
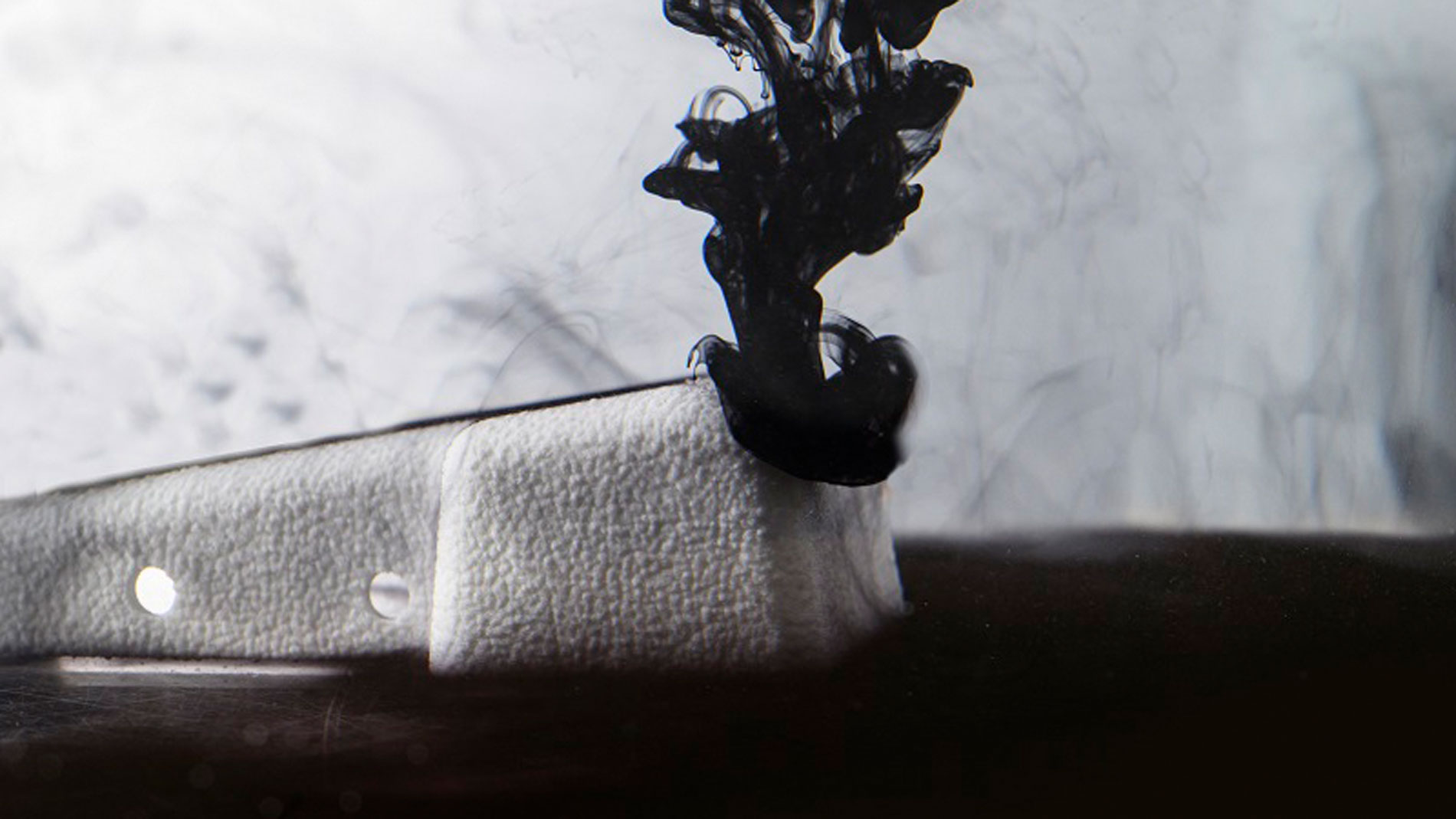
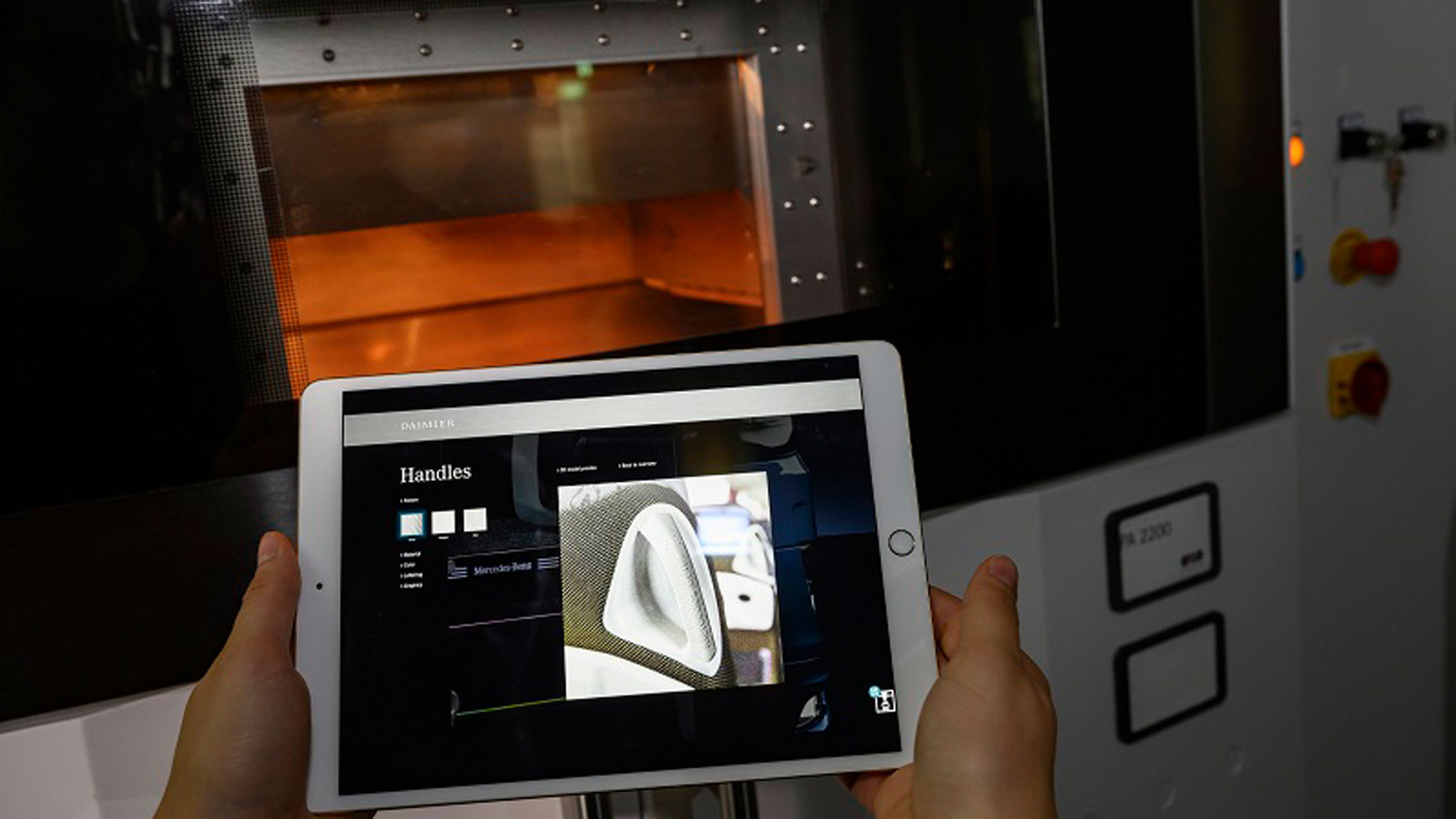
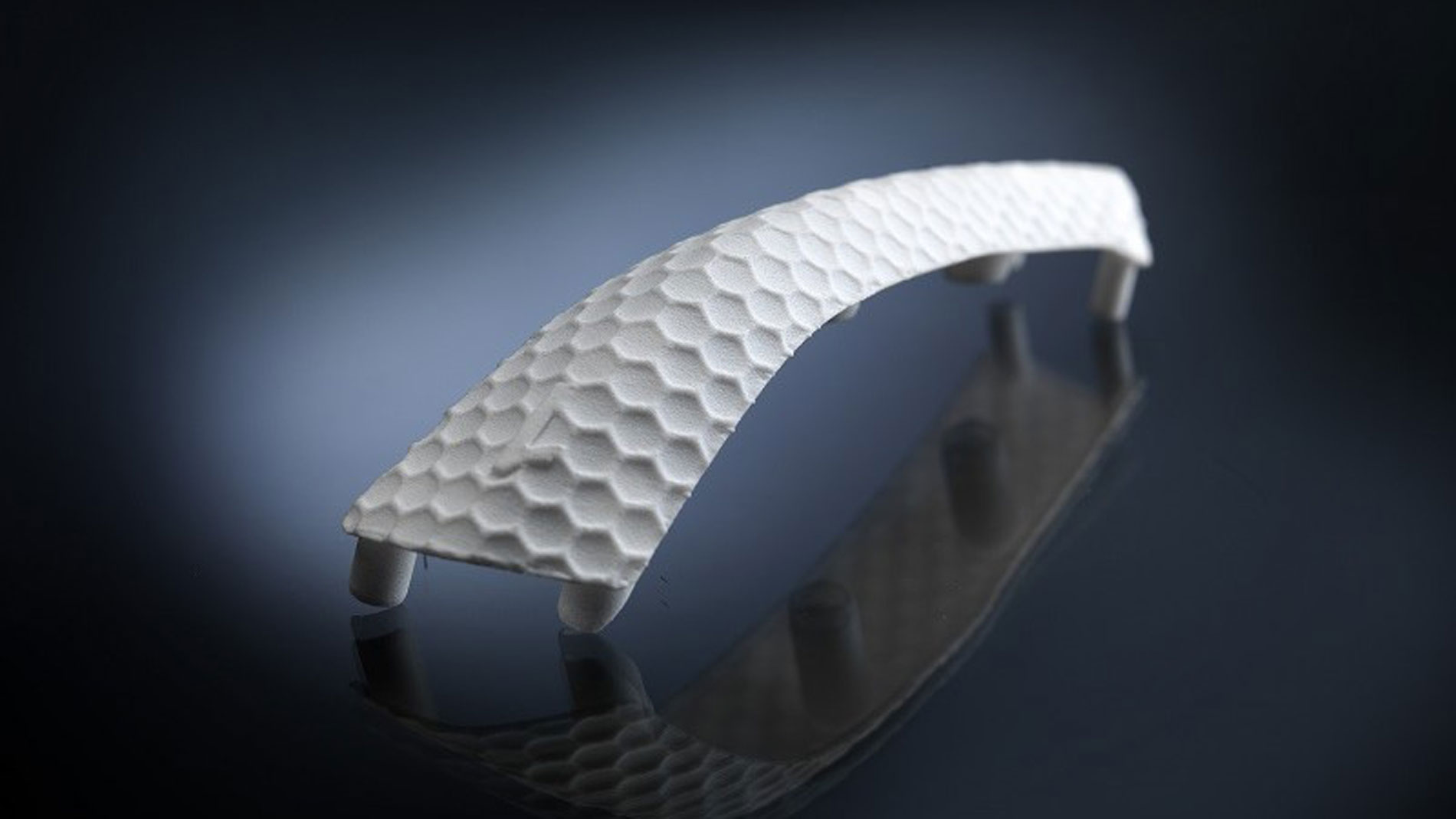
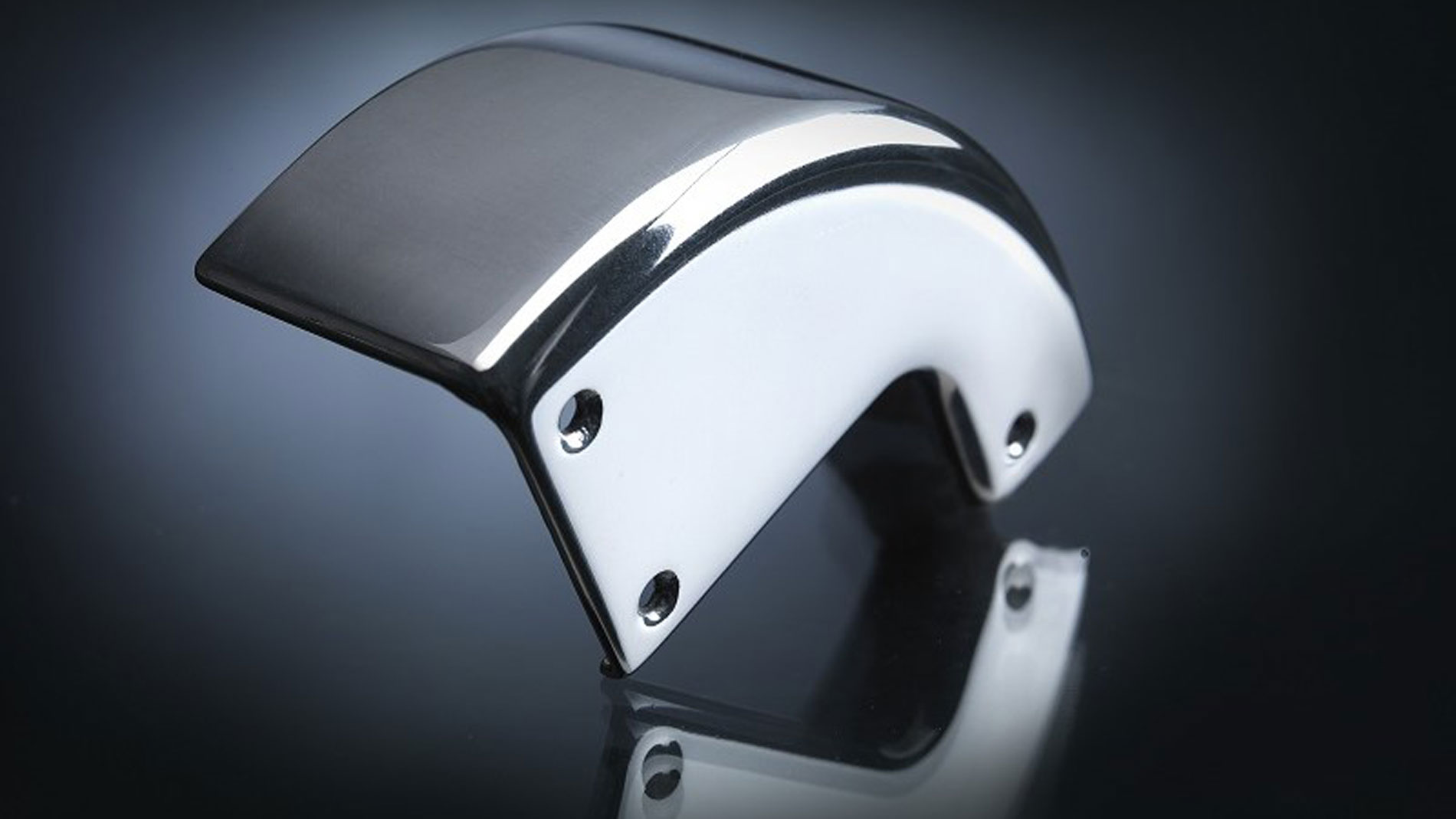
This is why Anderhofstadt, who is also the head of 3D printing projects at Daimler Buses, has a cross-functional team that »started by focusing on the spare parts that were giving us trouble«. He goes on to describe having »already generated a lot of added value« with the more than 350 spare parts that are now certified and being 3D-printed by the company’s service providers. Among other things, this required the development of a special material that would meet the strict fire-prevention requirements that apply in the field of passenger transportation.
The spare parts that already support 3D Printing include interior coverings, the aforementioned handhold inserts, and individual seating components, as well as metal parts like the mounts in exhaust systems. Customers that request these components now receive 3D-printed deliveries. »The response has been nothing but positive,« Anderhofstadt reports. »At the end of the day, the ability to obtain high-quality parts in short order is what counts for the customer. It isn’t all that important how a part was made; the bus it’s for just needs to get back on the road as quickly as possible.«
3D Printing isn’t the right production method for every spare part, of course. Anderhofstadt estimates that 8-10% of his company’s overall range of bus components is compatible with Additive Manufacturing at the moment – but he makes a point of stressing those last three words. Indeed, new production techniques and materials (involving glass, rubber, and metal, for instance) are expanding the scope of 3D-printable spare parts. »As a result, our potential is always increasing,« he points out.
Procurement model set to undergo transformation
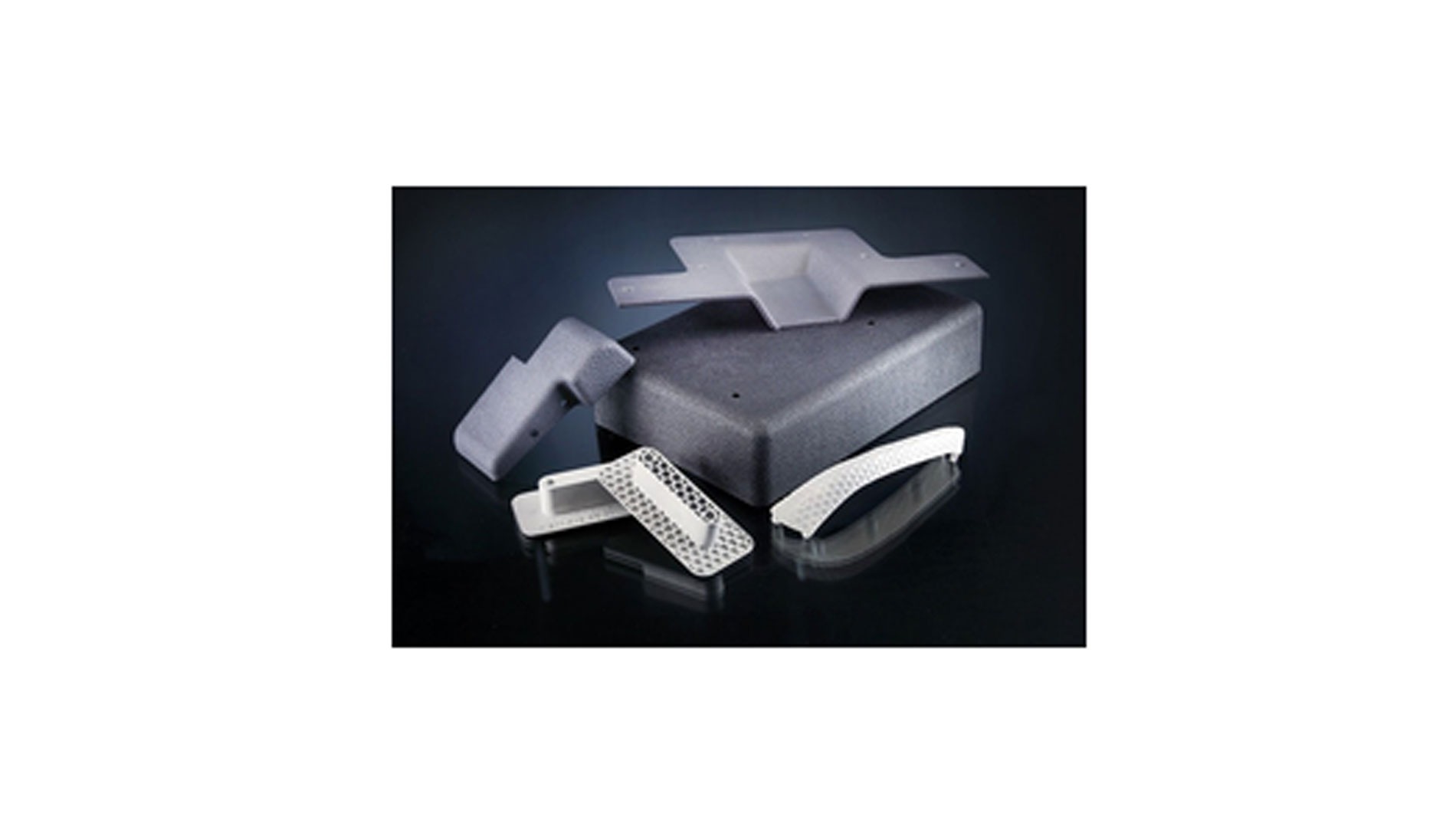
Anderhofstadt and his team – which works closely with more than 25 other departments at Daimler AG, including legal affairs, IT, training, and component manufacturing – also want to leverage the potential of Additive Manufacturing to transform their conventional procurement from »a purely physical into a digital business model«. Here, the concept of manufacturing at independent locations across the globe without the need for specific tools presents a huge opportunity. In other words, Daimler Buses wants to enable its partners to 3D-print spare parts right at the point of sale. Additive Manufacturing could thus be a game-changer that revolutionizes the traditional business of purchasing, quality assurance, and shipping.
Daimler Buses’ goal is to offer digital datasets as a supplement to its current business model. This will give customers the option to 3D-print select parts themselves or reach out to one of Daimler Buses’ certified production partners. To ensure that only the ordered quantity of components is actually printed, the coraresponding data deletes itself once the process is complete. What might sound like a vision of the distant future is already becoming a reality at Daimler, which is currently carrying out a pilot project with an initial partner company.
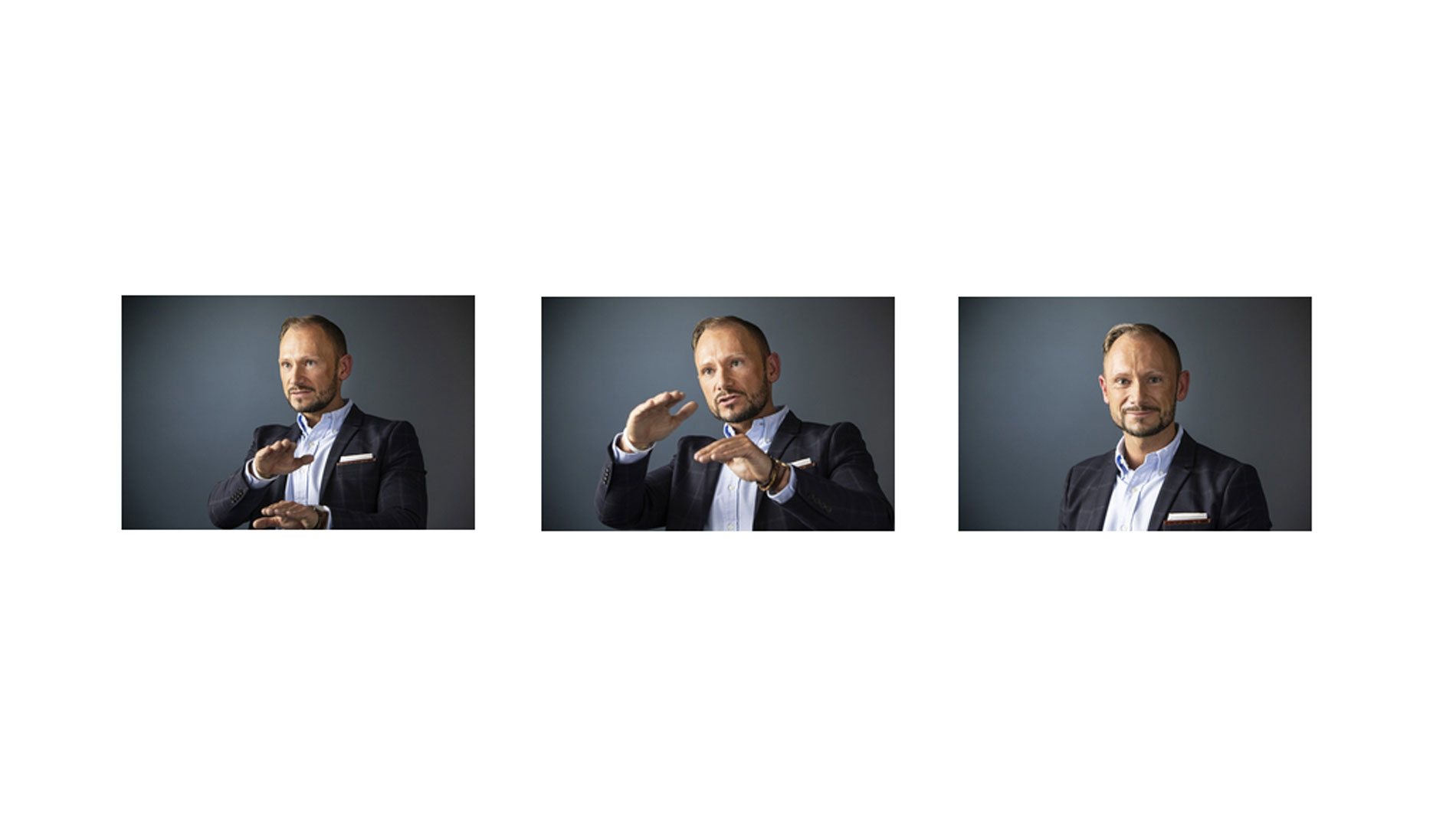
In this digital business model, Daimler provides not only the designs, but key process information regarding hardware, materials, the printing parameters required, and more. The quality of parts 3D-printed in this way has to match that of components that used to be manufactured conventionally, after all – including when external partners are involved. »For a premium manufacturer like us, quality is a top priority,« Anderhofstadt affirms.
A radical shift like this does come with challenges at many levels, however, from data security to the question of which materials and machines should be used. Daimler Buses is considering both the establishment of its own 3D printing centers at external organizations and cooperations with certified partners. »Ultimately, we’re going to have a hybrid format in which we also take regional and cultural particularities into account,« Anderhofstadt predicts.
Anderhofstadt sees the transition from prototyping to series production as an essential step in this regard. Although spare parts fall within the scope of small-series manufacturing, he says all the approval processes in series production still need to be ensured. »This means that a part I print today in Germany has to be identical to a part I have printed two weeks from now in a defined decentralized location, whether that’s within or outside of Europe,« he explains. This reproducibility is an integral element of the Daimler Buses model and a development topic for AM system manufacturers, service bureaus, and IT experts alike.
An integrated marker to prevent product piracy
Meanwhile, the opportunities 3D Printing is presenting at Daimler Buses could quickly become risks, as well, which is why brand protection is playing a prominent role in this development. As ongoing advancements continue to be made in scanning technology, reverse engineering methods are becoming increasingly sophisticated. It’s now quite easy to generate data from a physical component and use it to create copies on a 3D printer. »This could make it possible to pirate products even more quickly despite the hurdles involved,« Anderhofstadt warns.
To prevent this, his company adds special protection to its 3D-printed parts that enable it to definitively tell whether a component was made by Daimler Buses or a certified partner – or originated from some other source.
Daimler Buses
Daimler Buses belongs to Daimler Truck AG, which makes it a division of the Daimler group. It employs around 18,000 people and sold 32,600 buses and chassis in 2019, generating €4.7 billion.
daimler-truck.com/marken/buses
Tags
- Automotive