Text: James Woodcock, 3 September 2024
Is Additive Manufacturing a sustainable method of production? How can this technology help improve one’s ecological footprint? We’ve analyzed the factors that determine the answers to questions like these.
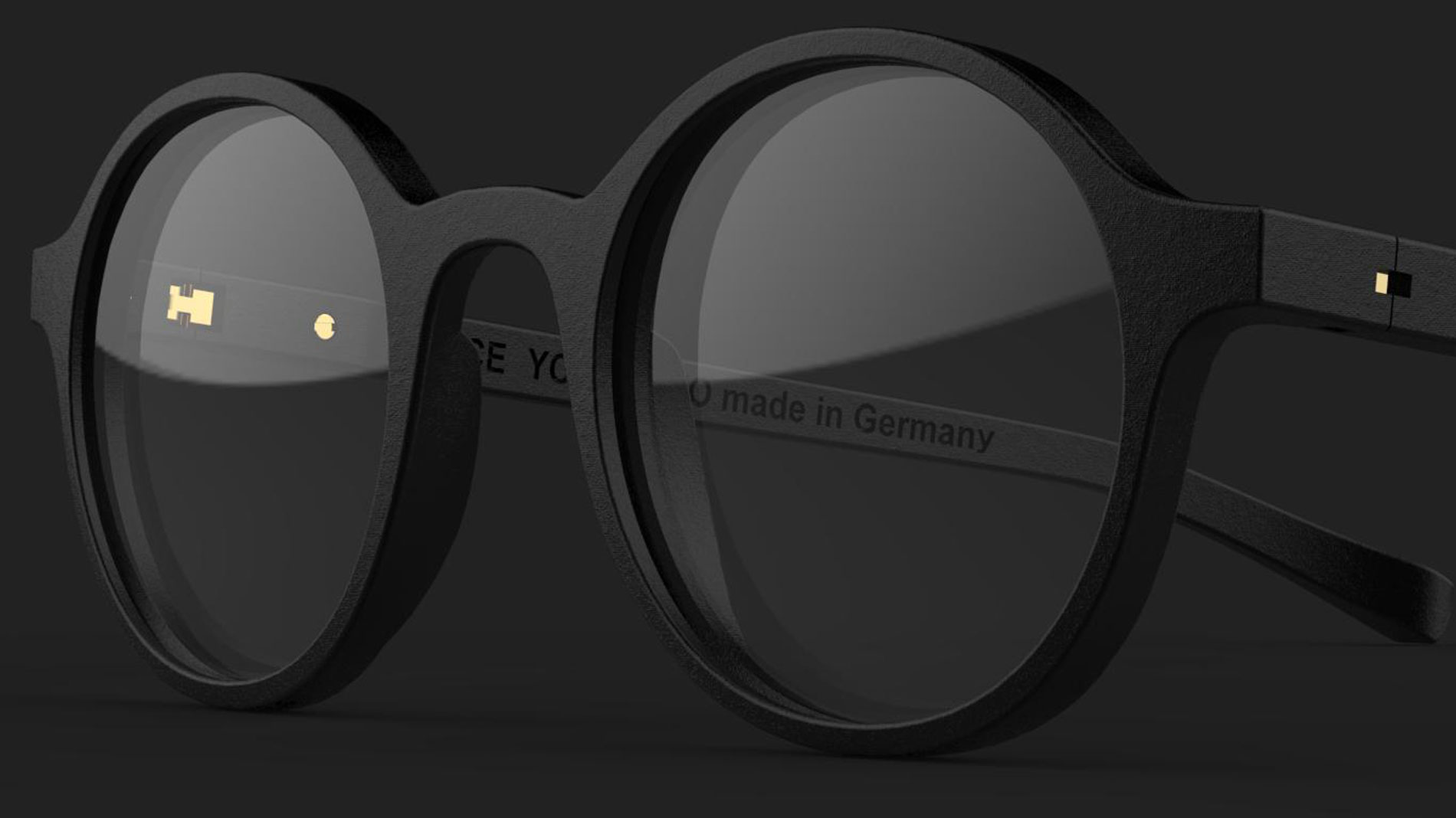
There are three angles we can look at when we talk about sustainability and Additive Manufacturing (AM). First is the sustainability (or otherwise) of the technologies themselves, for which we must consider the supply chain, the machine manufacture and operation, the resources consumed, the energy required and the waste streams created. Second is the impacts that AM can have on traditional manufacturing chains in terms of overall sustainability, including helping to improve efficiency of existing manufacturing chains. Third is the sustainability implications of additively manufactured parts in their end-use life.
Each of these three topics encompass a vast number of variables to measure, trade-offs to balance and angles to explore.
So, how sustainable is AM as a set of processes?
Evaluating the environmental sustainability of any process is very sensitive to the scope of the exploration. Taking a view that is too narrow or too wide can prove or disprove pretty much any hypothesis and leaves room for interpretation. For AM this is compounded by the fact that we could be talking about any one of a dozen processes, from hundreds of vendors, working any one of a thousand materials.
Some fundamental principles apply across the board however. All AM processes use energy — some more, some less — and how this energy is generated contributes a great deal towards the overall sustainability picture. Running an energy intensive process on renewable electricity could be more sustainable than a more efficient process reliant on fossil-fuel derived power.
Materials too play a role. Virgin materials come with 100% of the extraction, processing, and transportation impacts. Recycled materials can be better, but that depends on the energy needed for the recycling process (and again where that energy comes from is crucial).
As an example of the complexity of the situation, consider also the construction of the machines themselves. In seeking to keep the weight of the system down, aluminum may be used for the structural elements. Replacing this aluminum with steel would drastically reduce the carbon footprint of the machine build (~1.9–2.8 tons CO2 per ton of steel vs ~11.5-13.00 tons of CO2 per ton of aluminum), while slightly increasing the carbon intensity of the usually minimal movement of the system to the end user.
Ultimately, AM delivers sustainability benefits most when sustainability is considered at the conception and design phases. Re-designing existing parts — or simply using AM technology to create a part previously produced another way — can only ever have a relatively minor impact on the sustainability profile. By ‘designing for AM’, manufacturers can make the most of the opportunity to only use the materials where it is required.
Plastics — and specifically plastic waste — is a major focus of the wider sustainability charge worldwide. For the AM world, this offers both challenge and opportunity. As an example, photopolymers have historically been impossible or exceptionally difficult to recycle. While the parts made with photopolymers may have benefits in their real-world use, the waste generated is unfortunately just waste. Incineration and landfill are the only viable means of disposal today.
A number companies are forging ahead with bio-polymer based photopolymers that have improved recyclability and are less onerous to dispose of. For existing materials strides are being made to remove or reduce the carbon footprint at the point of sale, to improve recyclability and to create circular waste streams.
The use of pellets as feedstock for polymer-based 3D printers also opens up sustainability opportunities for manufacturers. Not only is the feedstock less heavily processed before printing (i.e., extruded into filament, wound, etc.) but pellet systems can more easily use directly recycled polymers that have been ground to the correct size profile.
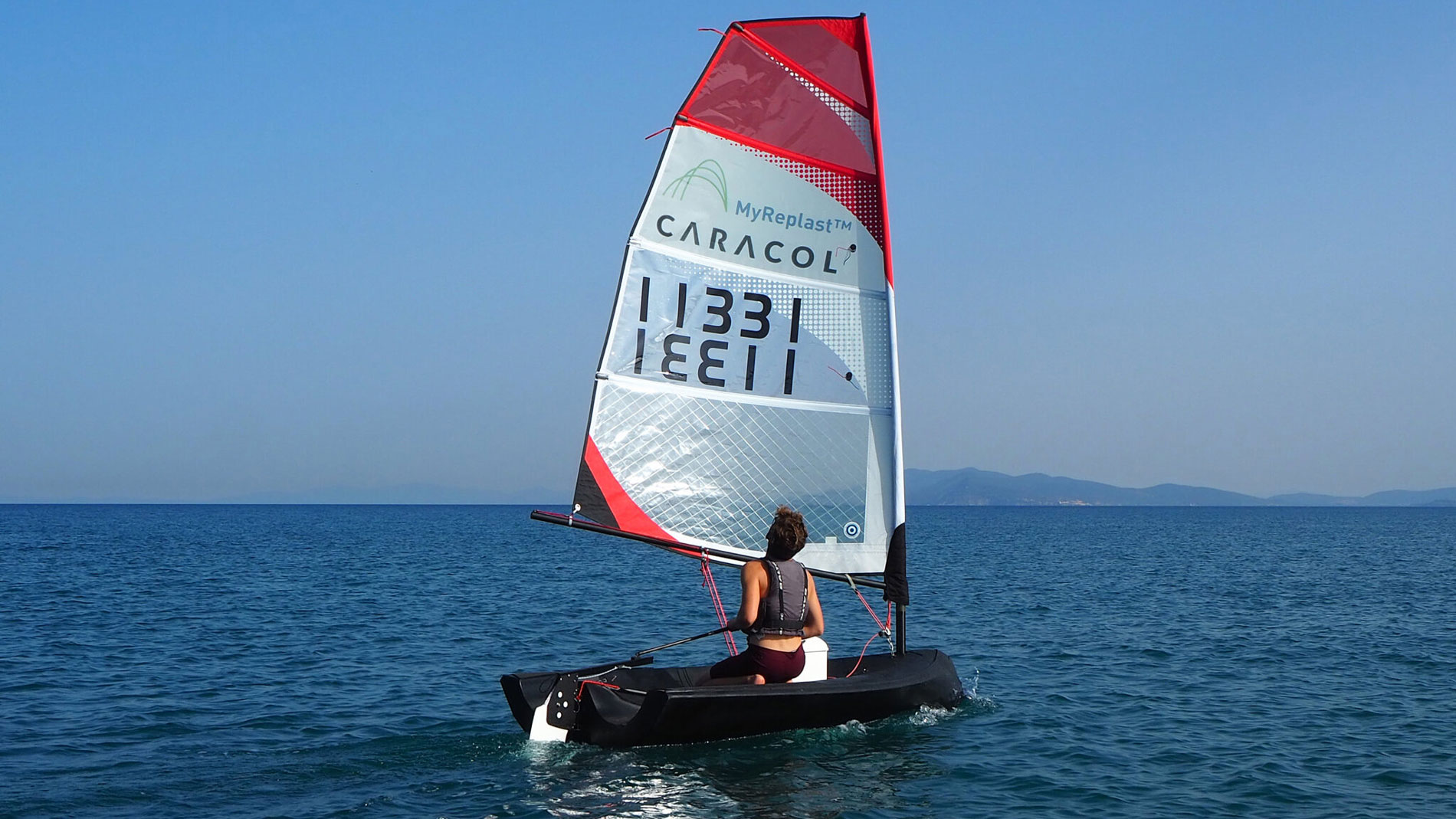
Metal powder: frustration and opportunities
For metal AM, materials are the biggest source of frustration and opportunity. For the most commonly used metal AM technologies, materials must be powdered and have specific morphologies and chemistries. Traditional metal powder production has a high environmental impact to start, but for AM applications this is further exacerbated by the relatively low-yield of usable material. Each kilogram of AM powder therefore bears not only the environmental cost of its own production therefore, but also the cost of unusable powder that may need to be re-processed as great environmental and economic cost.
This was not lost on any of the exhibiting companies and each was keen to demonstrate their unique take on the challenge. For some, the ability to tap into local renewable power immediately positively impacts their carbon footprint when compared with a fossil fuel powered competitor, even if the process is the same. For others, development of high-yield, energy efficient and flexible platforms provide an opportunity to help downstream customers. And across the show floor recycling of end-of-life parts, scrap and out-of-spec material was a consideration, especially for high value metals and alloys.
Reduced impact applications
AM remains a potential net benefit for those looking at commercial and environmental sustainability because of the unique ability to create parts that would otherwise be impossible. Anyone who has more than a passing interest in AM will be well aware of the myriads of topologically optimized, bio-inspired and otherwise natural looking geometries that go hand-in-hand with the technology.
It is this design freedom and the potential for additively manufactured parts to be lighter, stronger and more resistant to heat and wear that opens up huge opportunities for the sustainable manufacturing sector.
One of the best know examples is in aerospace, where weight is one of the enemies of efficiency. By harnessing the design freedoms opened up by AM, manufacturers can shave weight from components that may have a lifespan of decades. Every flight that makes use of these parts has a lower fuel consumption which, when considering the percentage of time an aircraft is airborne and the anticipated service life, adds up to significant savings.
The exhibition floor proved that AM companies are looking more holistically at the sustainability challenges and their role in providing the solution. Life cycle analysis of parts is becoming much more of the sales strategy that in previous years, with a real focus on the cradle-to-grave impacts of additively manufactured parts and components.
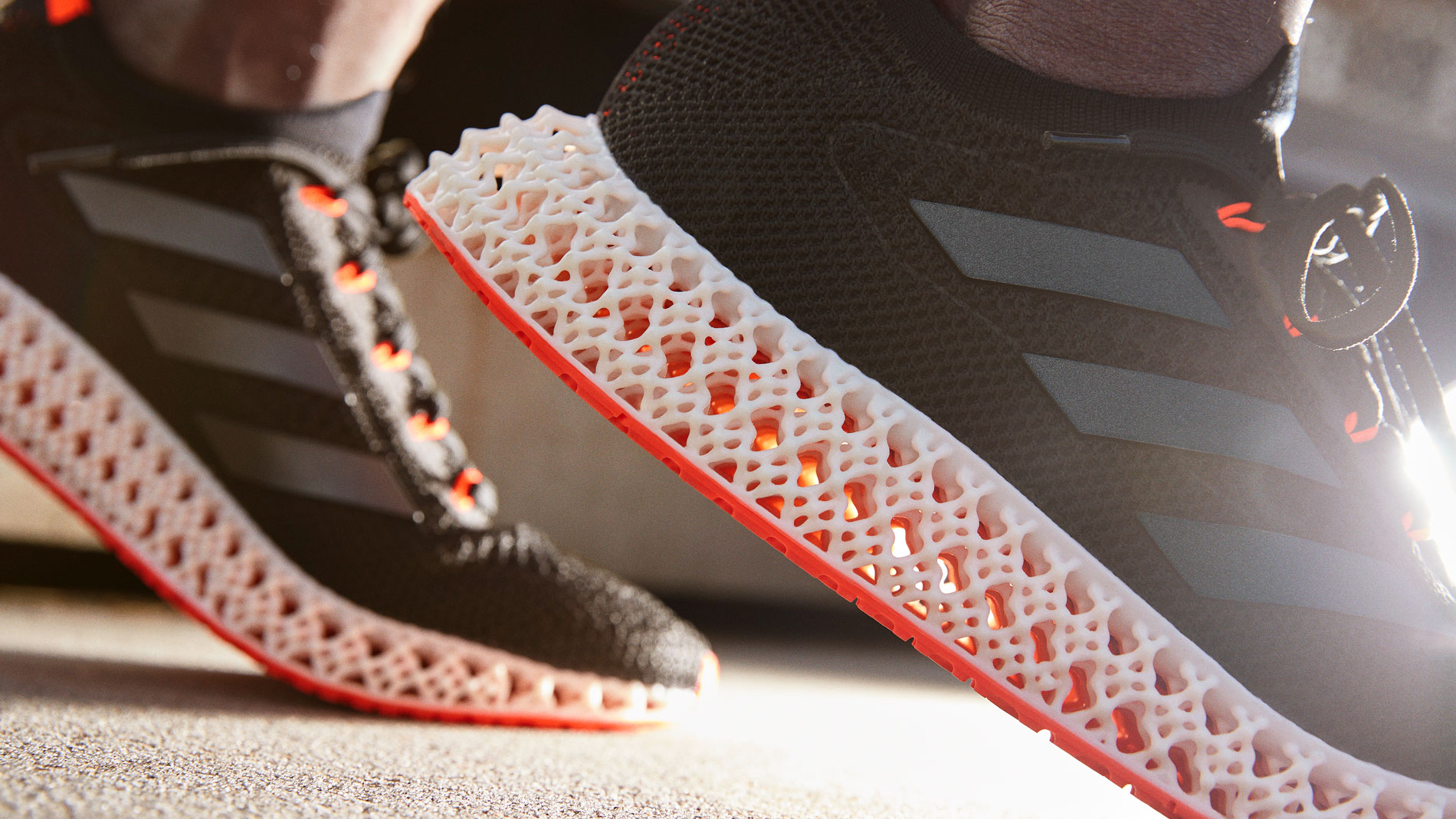
The bigger the part, the bigger the (potential) benefit
Applications in AM are often limited by the build volume of the AM equipment deployed, however a number of larger systems catering for both metallic and non-metallic printing (e.g., Large Format AM (LFAM) and some Directed Energy Deposition (DED) systems) are available in the market.
Tackling larger components highlights the potential sustainability of AM processes in a number of ways:
- Where a large part if subtractively manufactured, the resulting waste stream is proportionally higher. Here AM’s ability to use just the material needed can result in substantial savings of time and material, and reduce waste streams.
- Larger parts also pose challenges for logistics, and the ability to manufacture at or close to the required deployment site is extremely beneficial. Shipping, handling, and storage of large parts is responsible for a significant proportion of their environmental impact.
A big picture, with fine details
AM offers a potentially transformative pathway to reshape how we produce, consume, and think about the lifecycle of our products. Deployed well it can minimise waste, optimize design for efficiency, and make the most of sustainable materials. With the renewable electrification of industry and circular economy principles adopted within the AM sector, it becomes clear that this technology is not just a tool for creation but a potential beacon of sustainable progress. With pressures coming from end users, supply chain partners and regulators, AM’s sustainable future looks bright.
Ultimately the breadth of AM technologies, materials and their applications make sweeping generalization both difficult and not especially useful. Each time a process is put to use the myriad factors involved must be considered when thinking about sustainability.
Getting green energy is a good start, designing to maximize the benefits of the production method certainly helps, and leveraging the ability to manufacture close to the point of need is crucial.
FURTHER INFORMATION:
Tags
- Sustainability