Text: Thomas Masuch; Photos: Forust Corporation — 10 September 2020
3D printing veteran Andrew Jeffery has loads of ideas for the use of 3D printed wood. In his studio in the Bay Area of San Francisco, the CEO of Forust works with a specially hacked 3D printer to test different wood materials and recipes for 3D Printing.
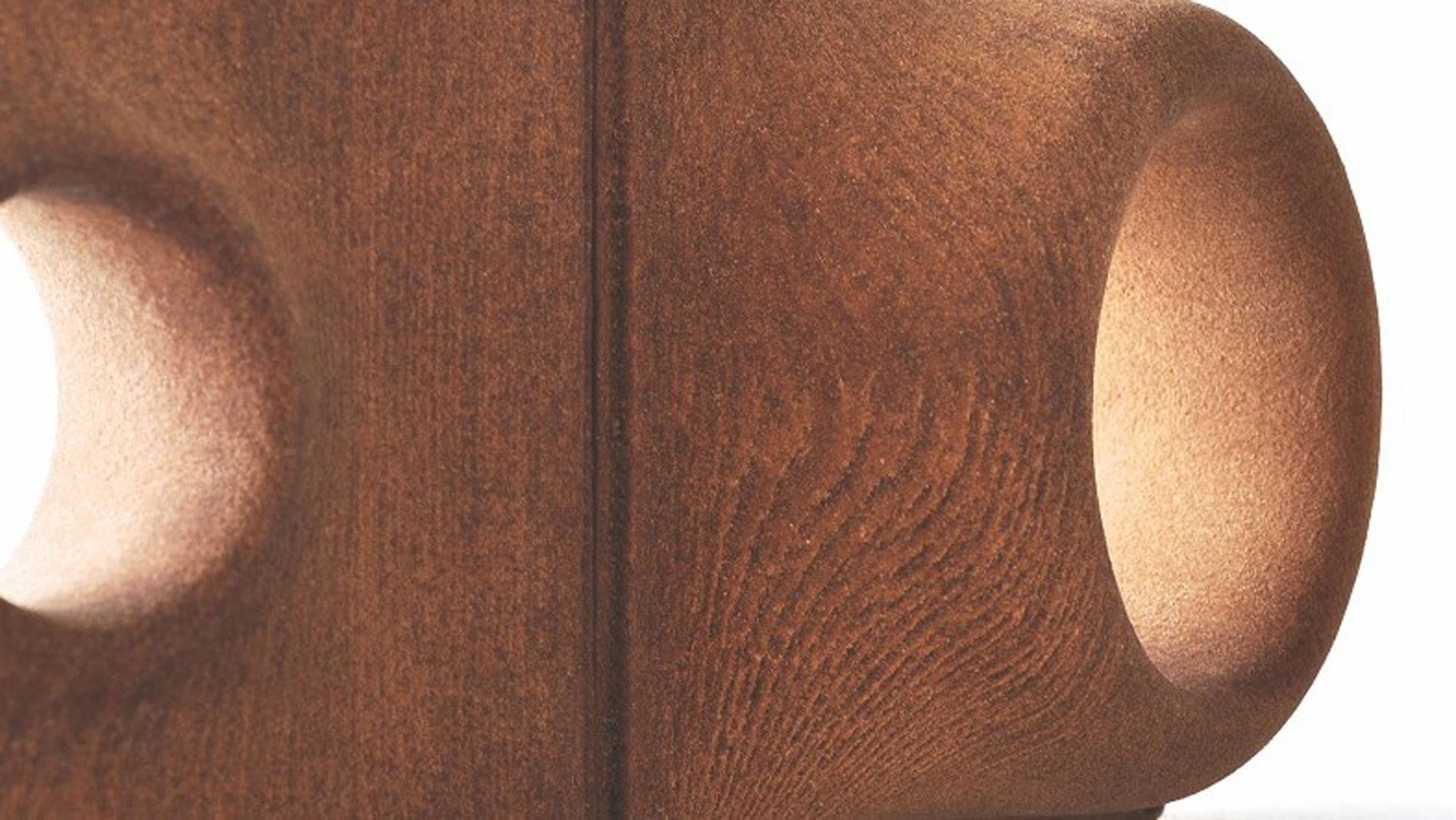
»Wood is a natural, ecological, and beautiful material,« explains Jeffery talking to Formnext Magazine. He spent much of his previous career working with 3D printed ceramics, and now is delighted with the sustainable and recyclable origins of the material wood. »We are printing with sawdust, agricultural waste, our process makes products that are lightweight, functional, beautiful and sustainable.«
Forust was founded last year together with Virginia San Fratello, professor of interior design at San José State University, and Ronald Rael, professor of architecture at The University of California Berkeley. In 2010 San Fratello and Rael founded Emerging Objects – a »Make Tank«, that develops materials and building applications for 3D Printing. Rael and San Fratello developed 3D printing wood as part of their research at their respective universities.
"We are at a very early stage and still have a lot of development work to do."
They’ve joined forces with Jeffery to develop a 3D printed collection of wood tiles and blocks for interior designers. They also have ideas for developing light fixtures, furniture, lightweight screens for partitioning offices and public spaces, desktop accessories, vent covers and a host of other products for the interior. They are even exploring the notion of 3D printing wood musical instruments. As Jeffery explains, the whole endeavor raises questions about how wood is used in the 21 century. »This is linked to the hope that it may be possible to buy such products for your home or business in your own a local shop.«
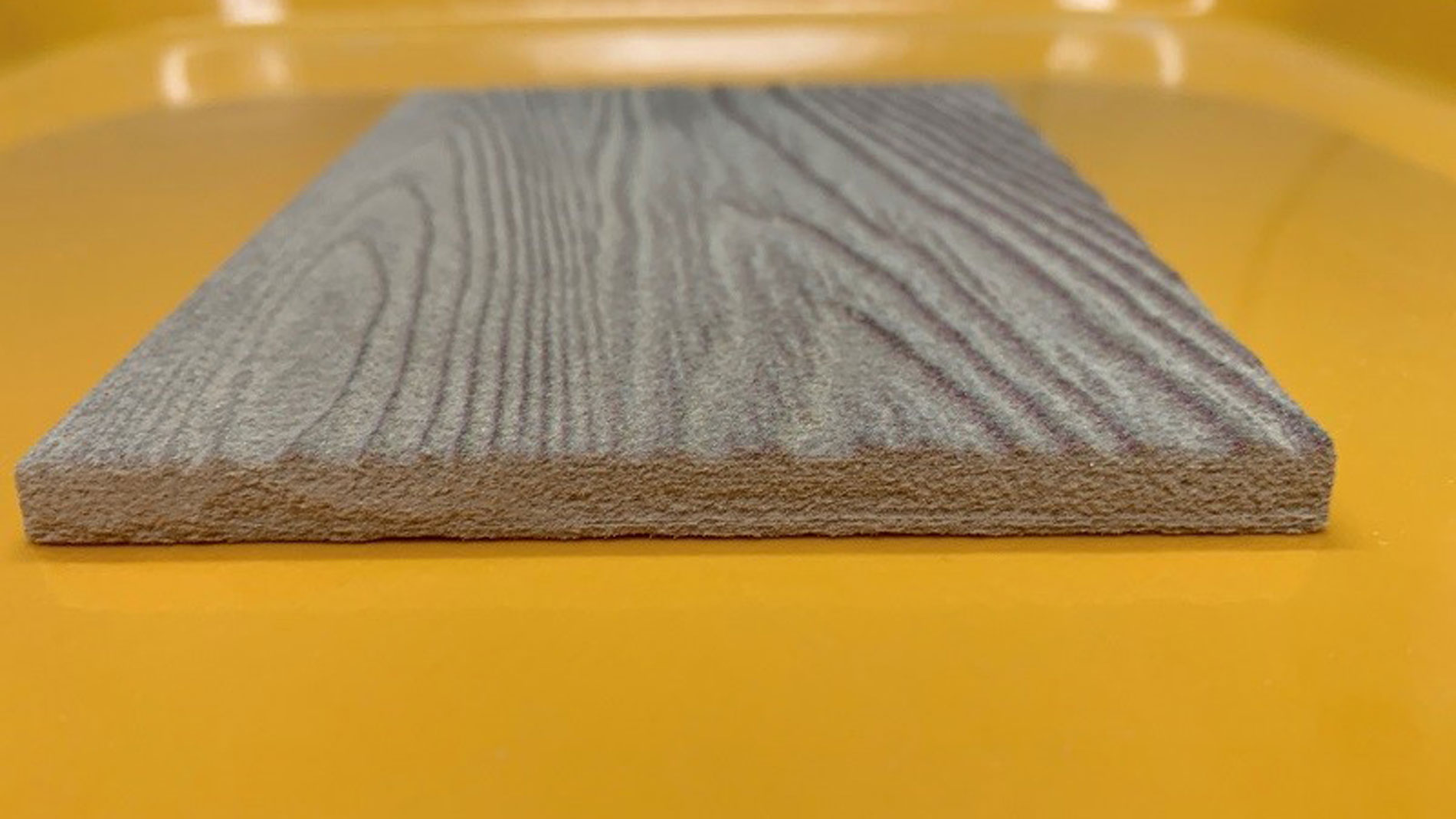
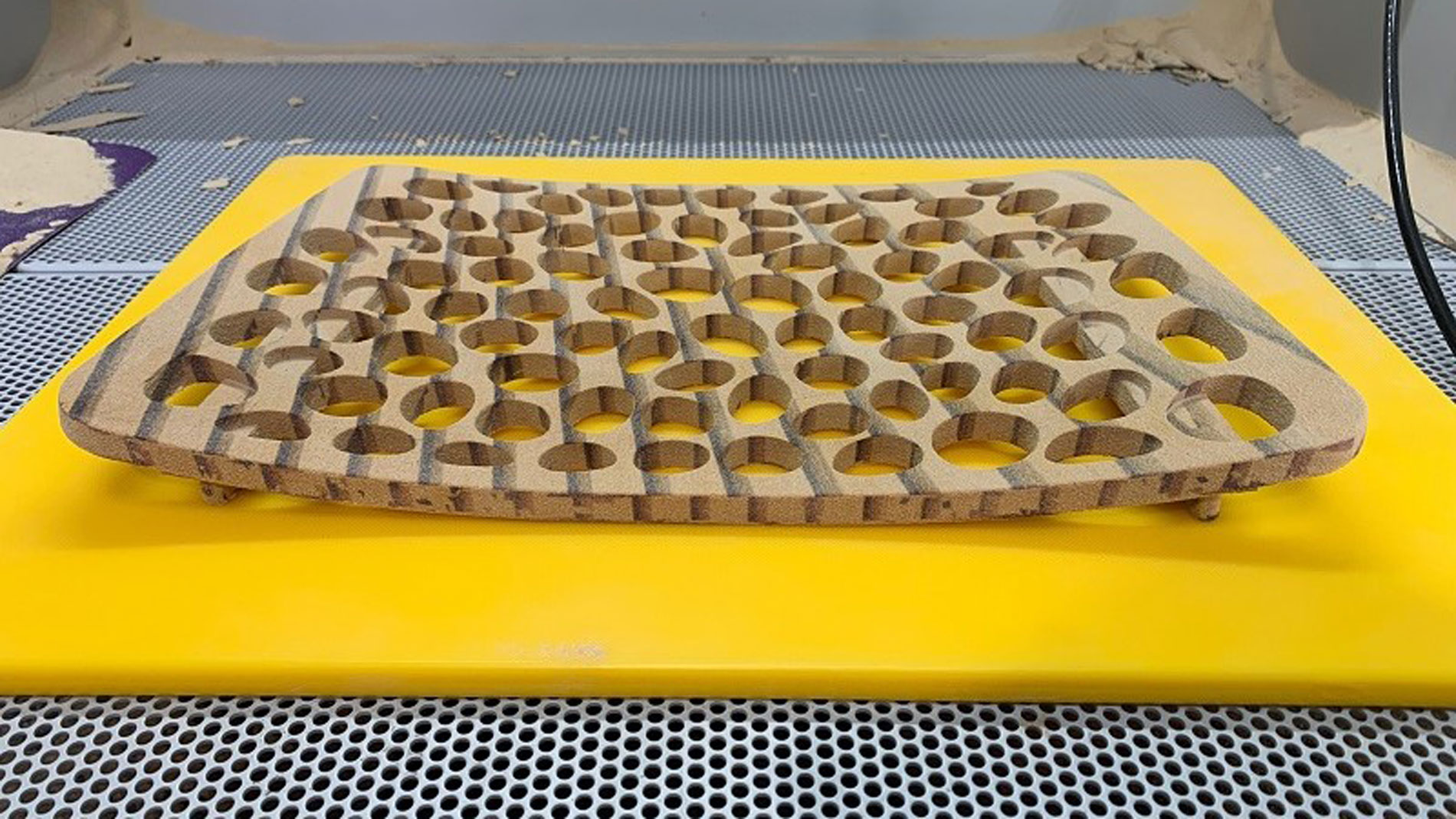
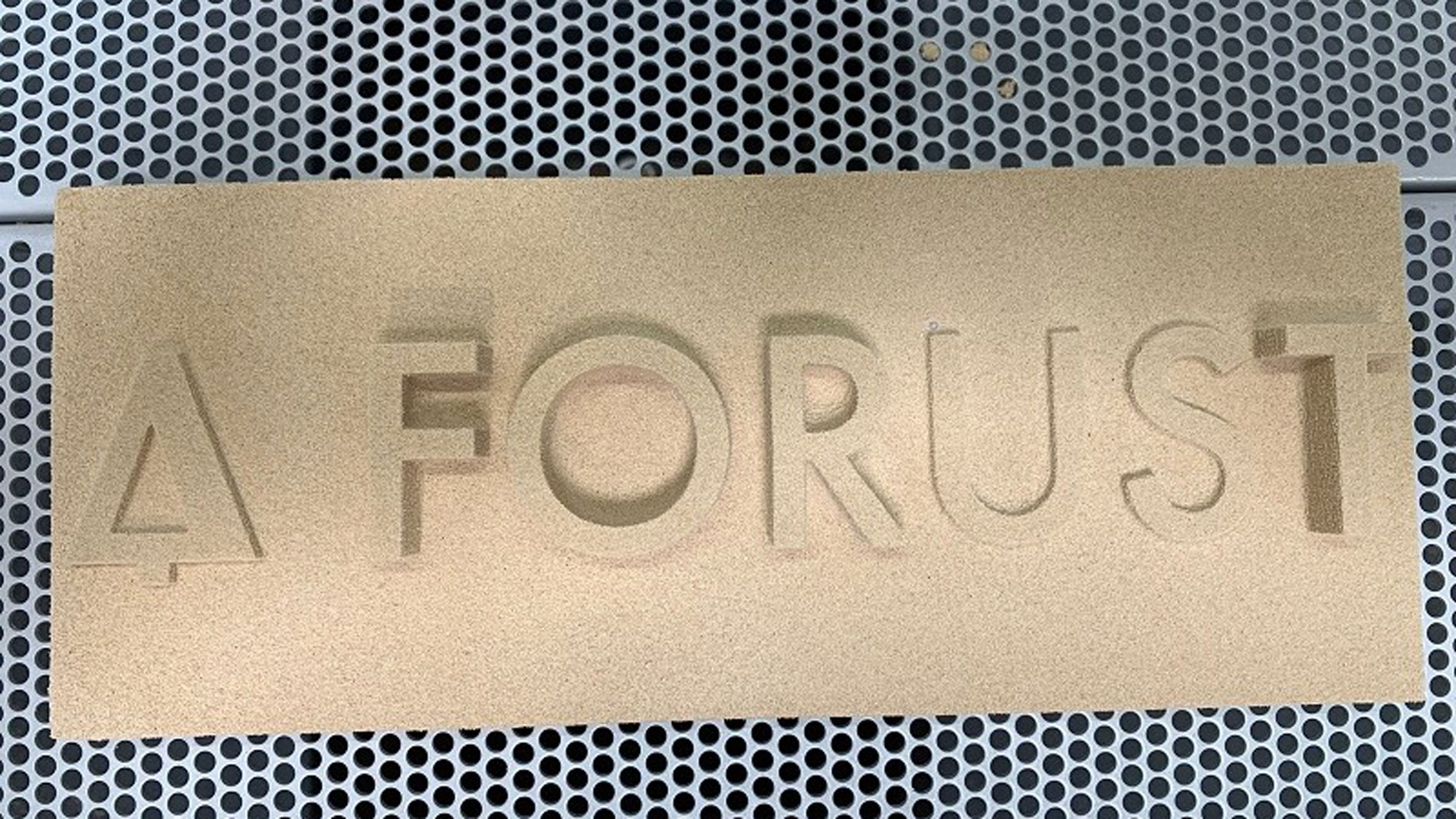
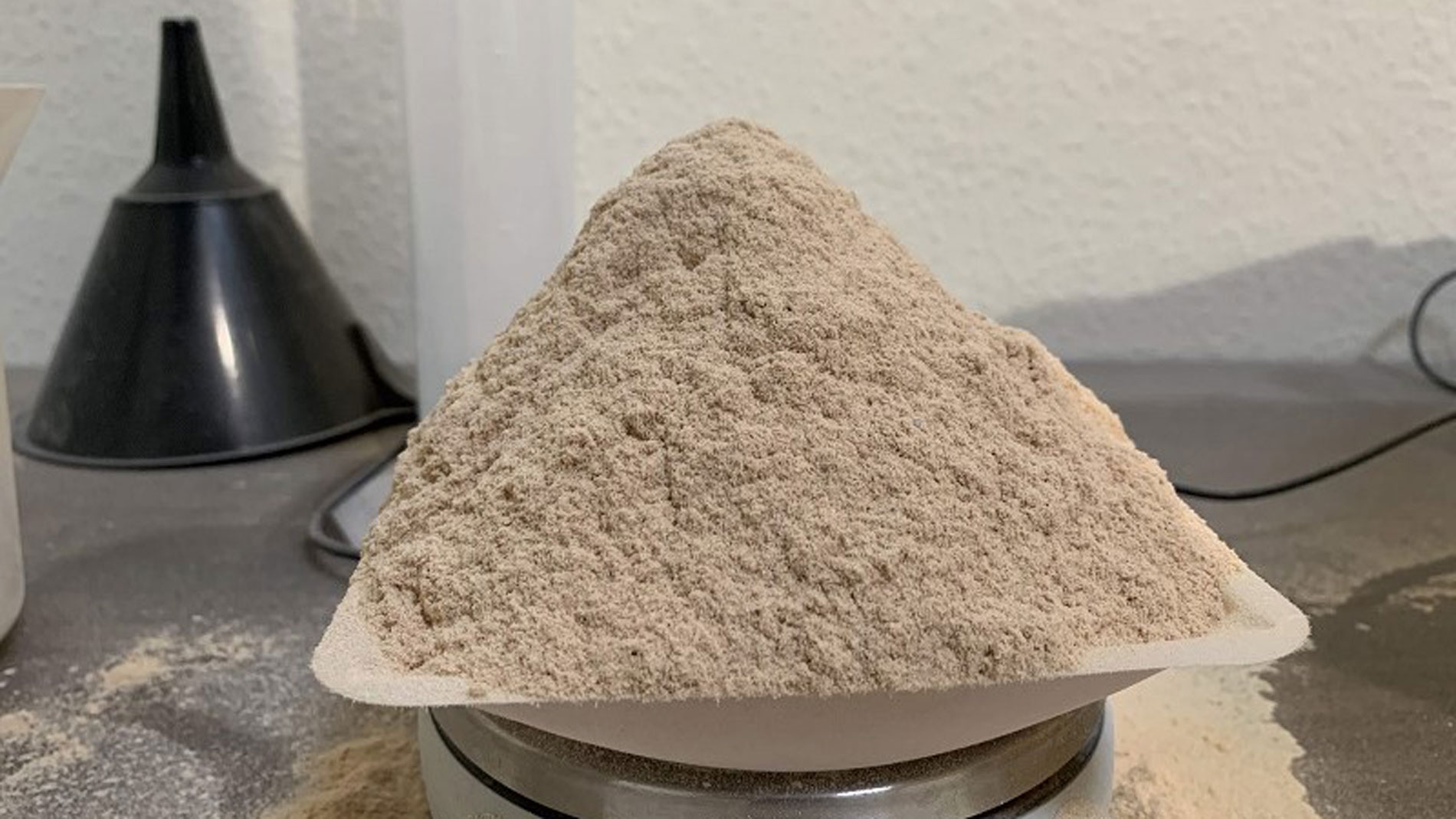
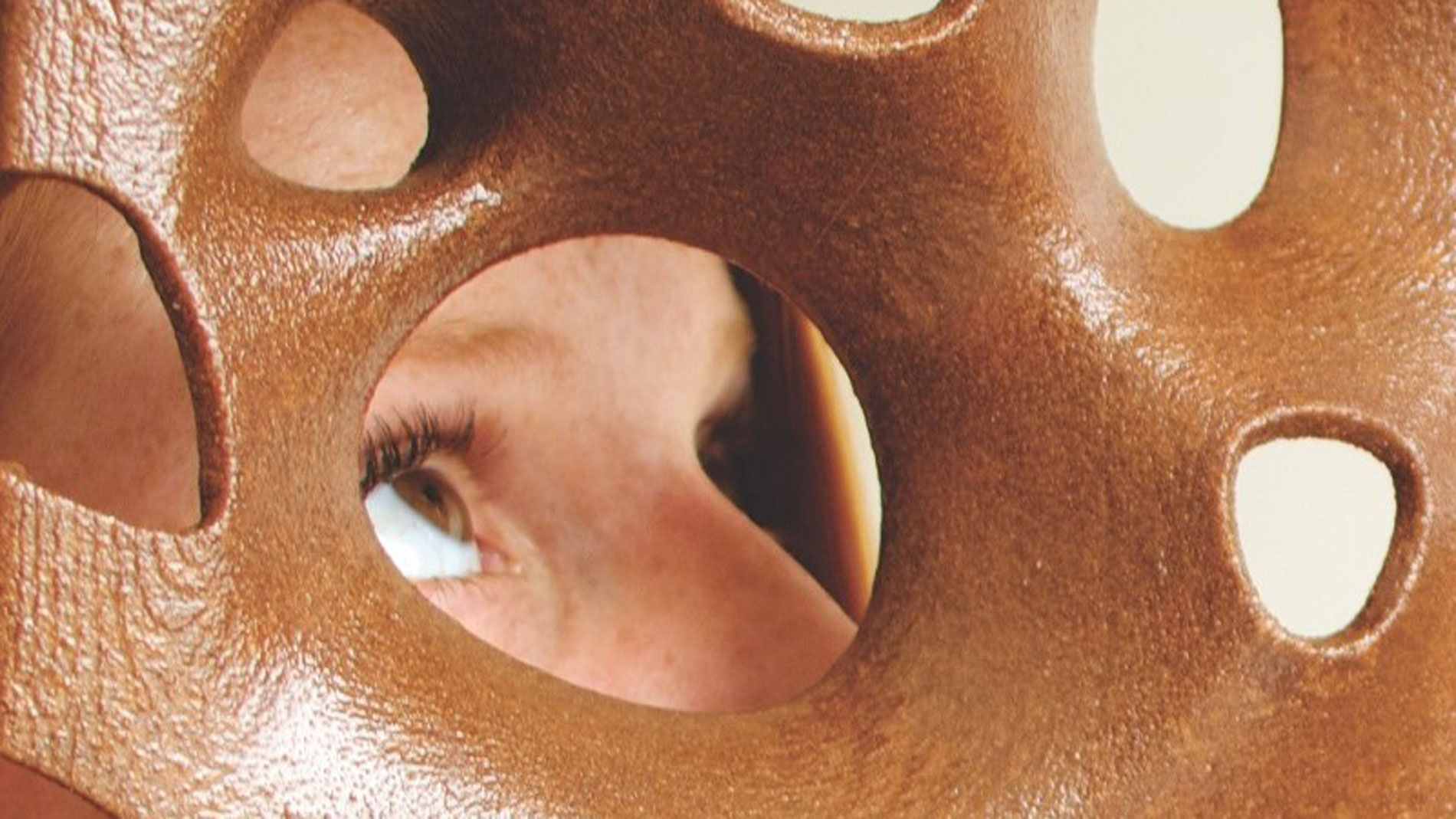
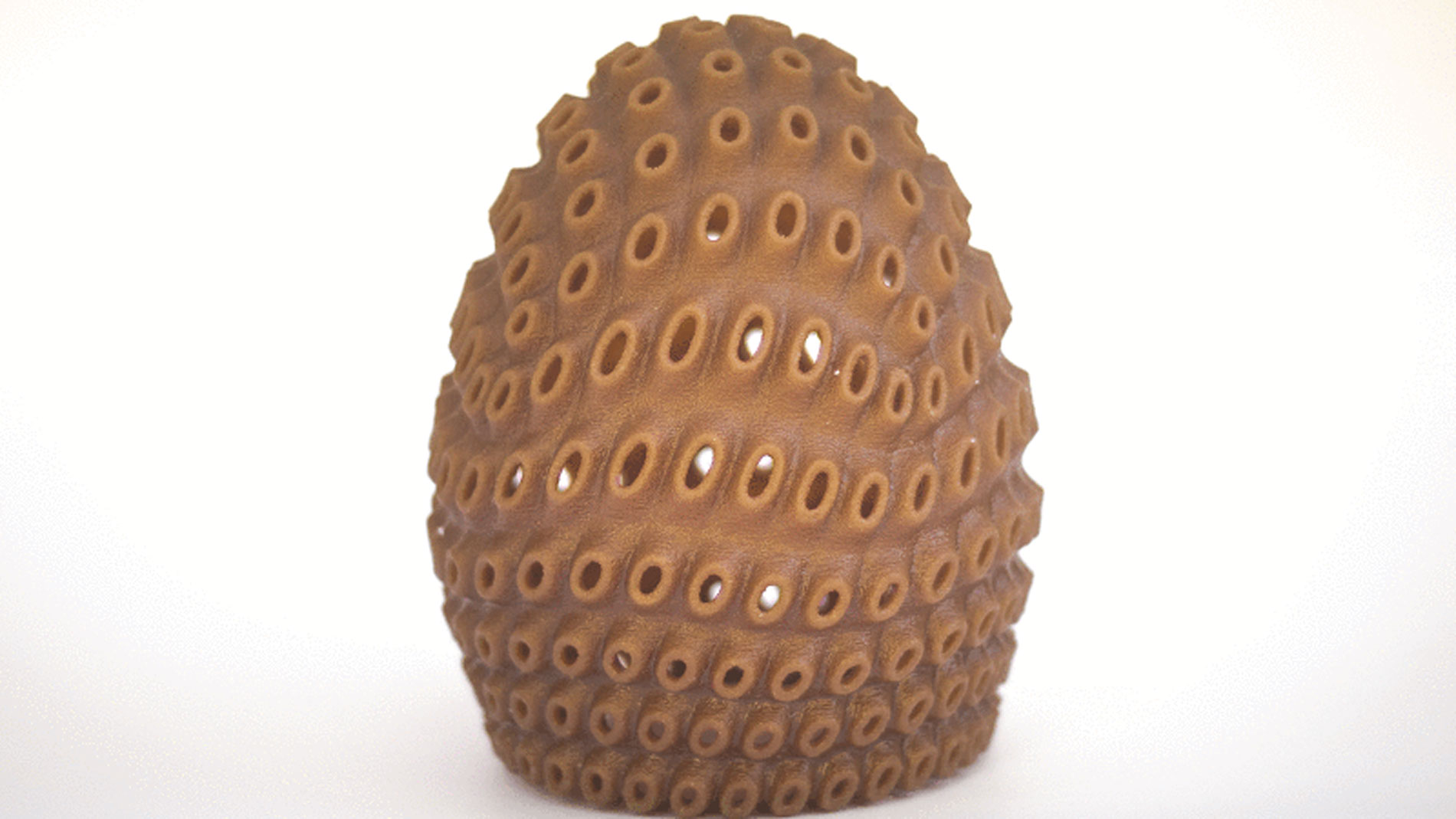
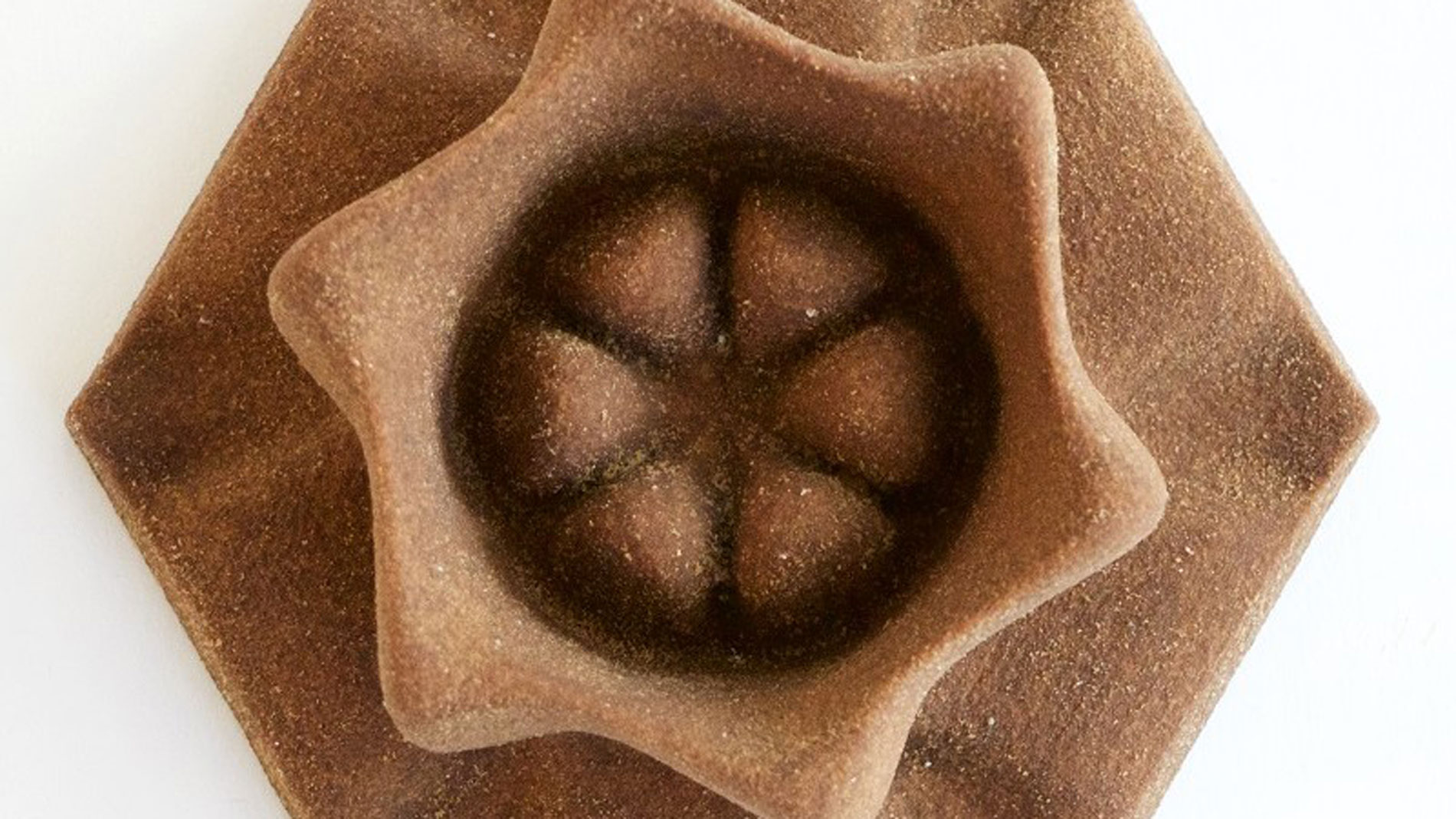
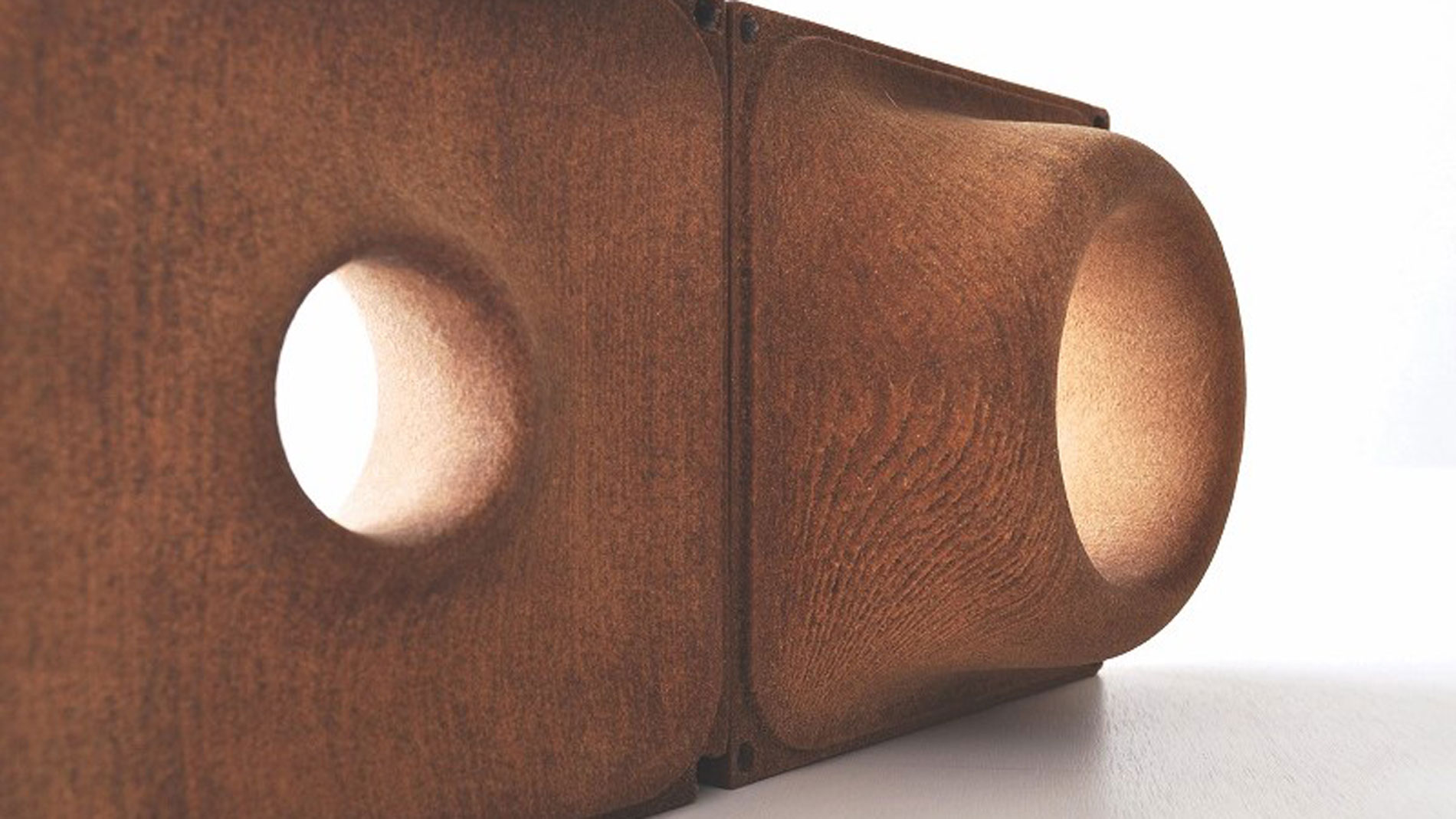
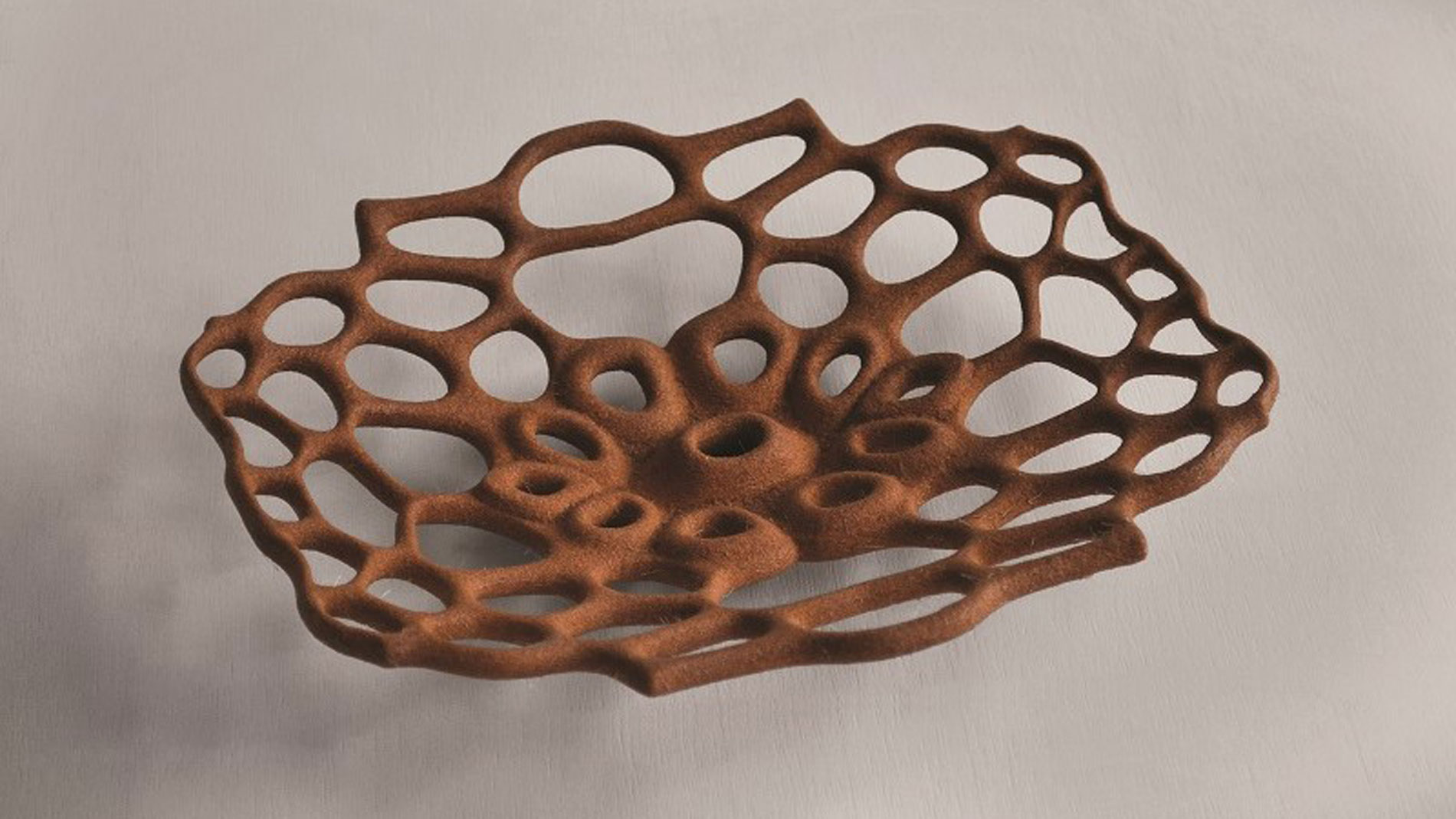
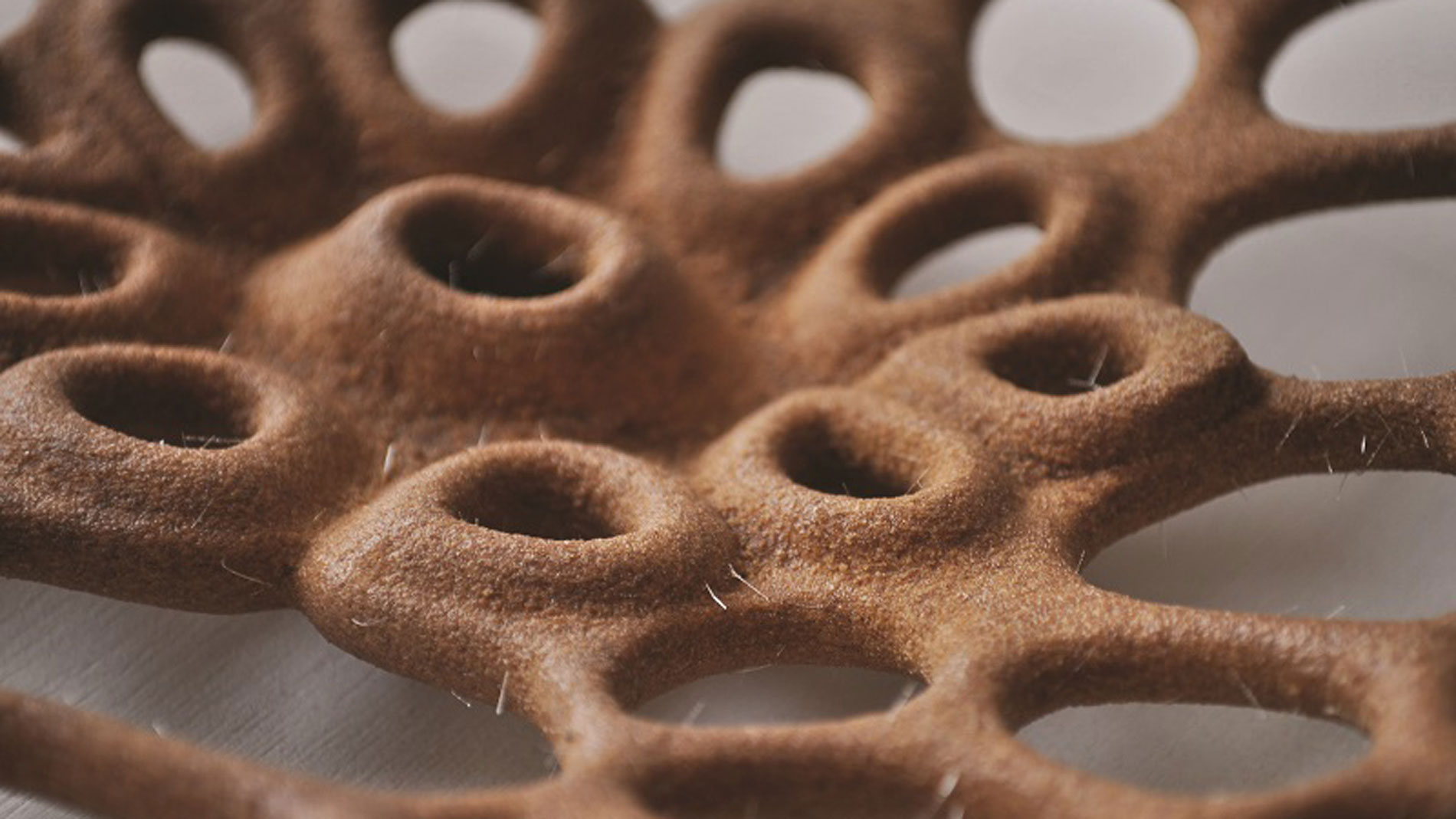
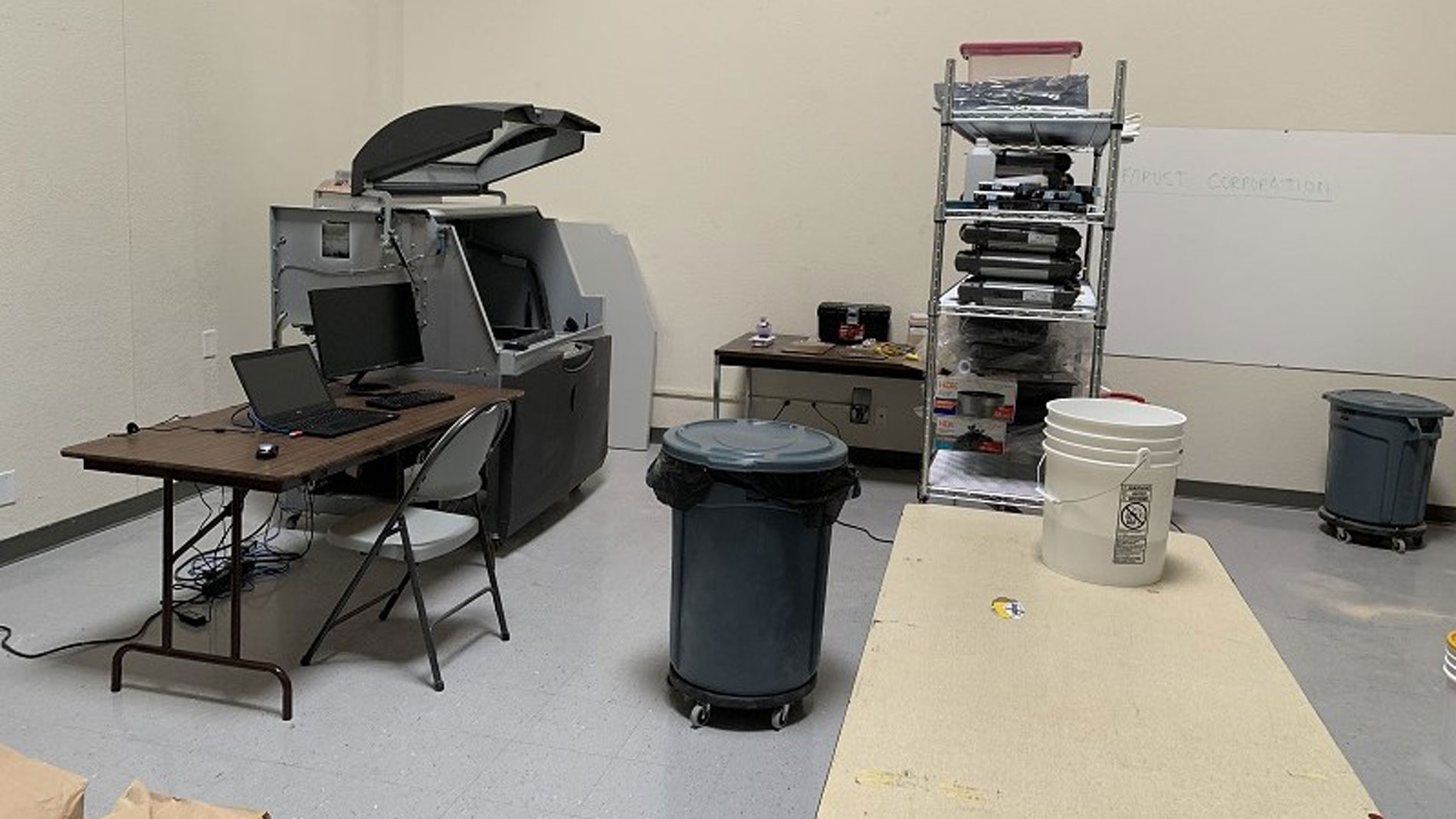
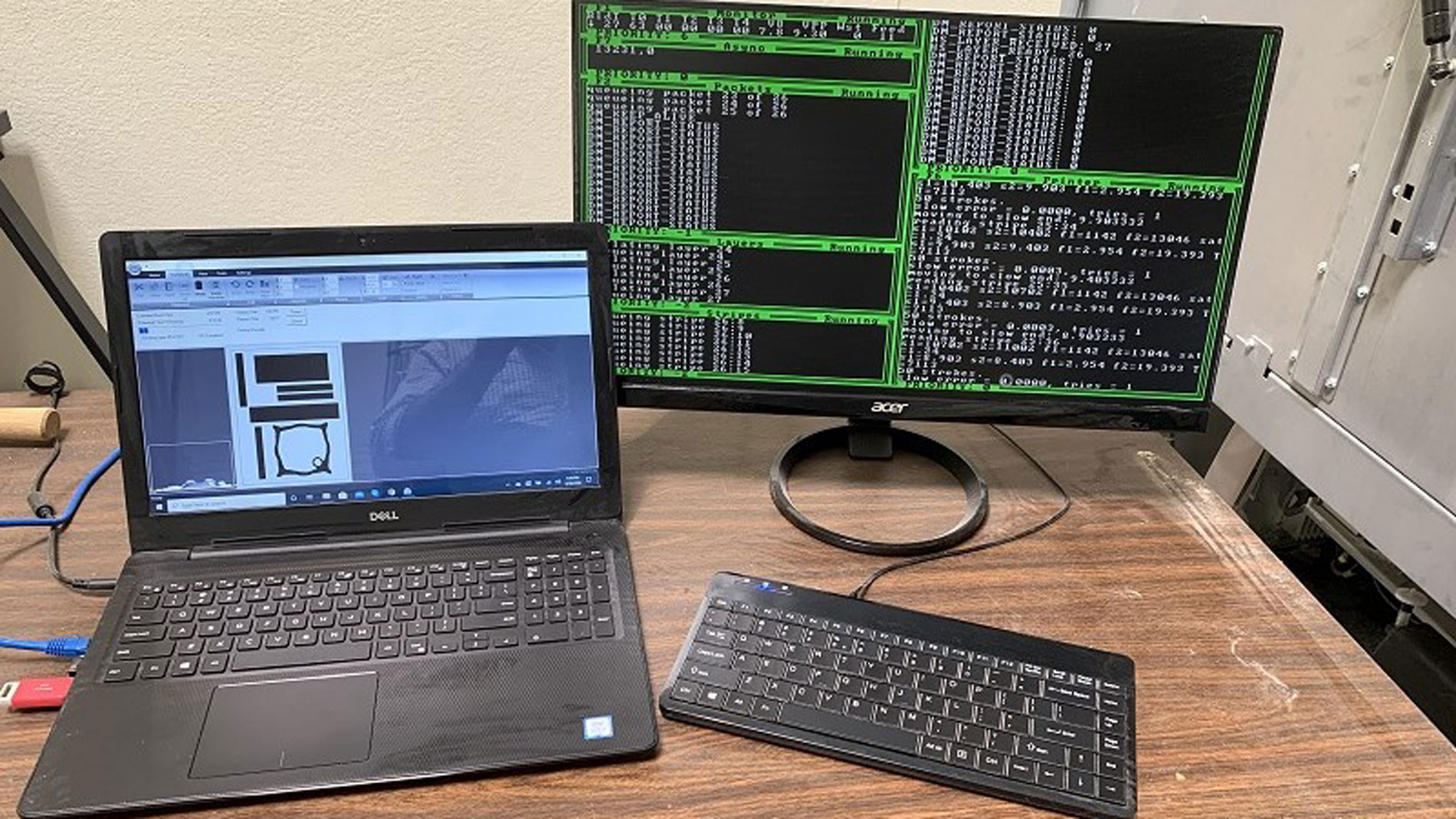
Before such concrete implementation can begin, Jeffery and his two comrades-in-arms still have a long, busy road ahead of them. »We are at a very early stage and still have a lot of development work to do«, explains Jeffery. Numerous prototypes are currently being built and tested on our new Projet 860 from 3D Systems. Modifications to the printer itself are also being made, for example the ink nozzle has been disconnected and the powder supply has been adapted for the coarseness of the wood. »We have also increased the thickness of the layers significantly in order to minimize print time,« explains Jeffery »which creates a more textured surface one that is more reminiscent of wood grain«.
The printed material is a mixture of sawdust, wood debris, wood glue, and water. The high sustainability factor comes from the fact that the printable matrix consists of waste material from the wood industry that is normally sold to power stations at a price of 70 euros per ton, for example, and is then burned there. According to Jeffery, 3D Printing can also be done using fairly inexpensive timber that would otherwise be unsuitable for furniture. Trials are also being conducted using bamboo.
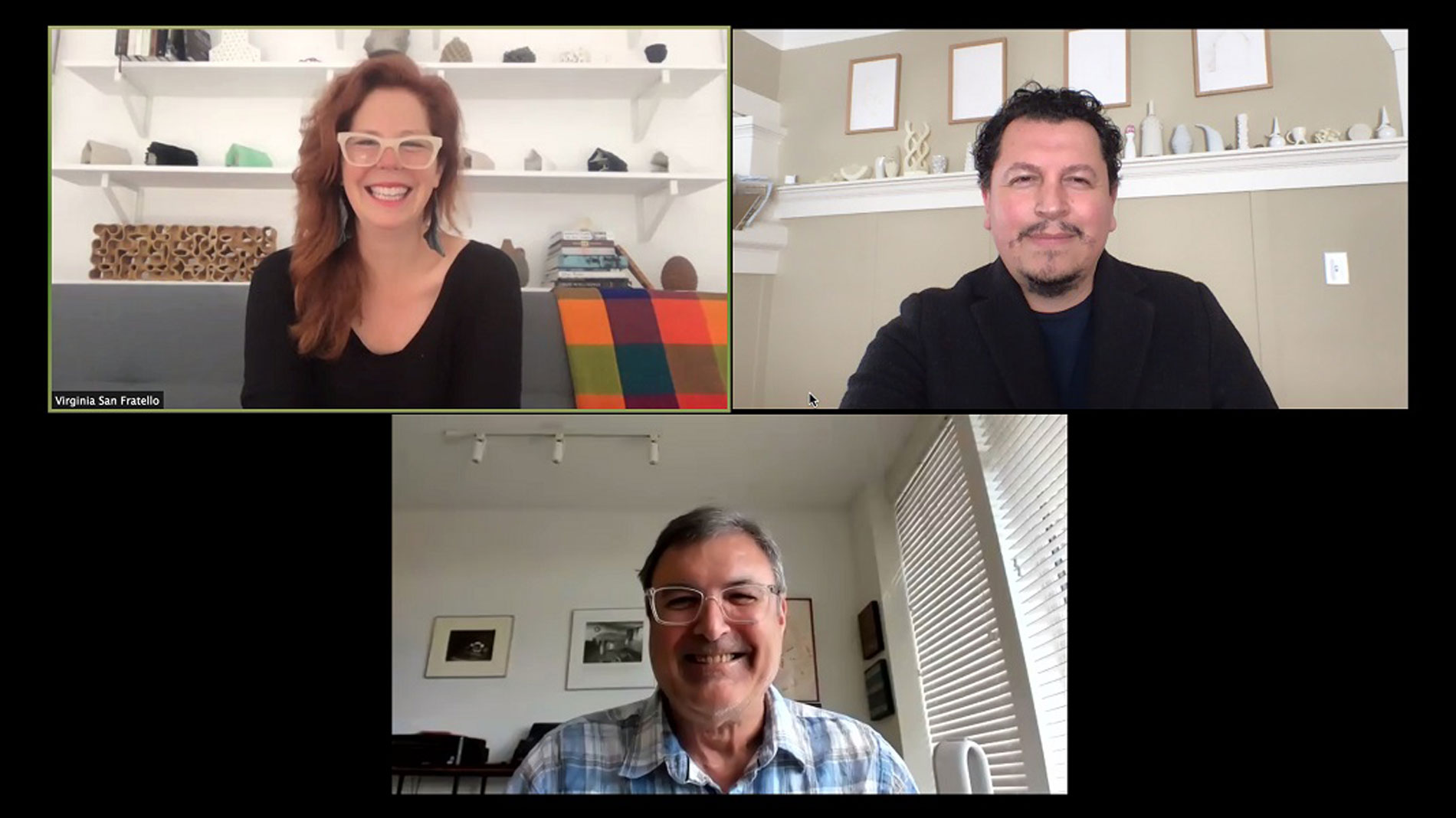
The technical modifications to the process and the 3D-printer were not a great challenge for Jeffery, as an engineer, he has been involved with 3D Printing since the early 90’s »when the technology was in its infancy.« He also has experience with start-ups and founding new companies: One of his early 3D printing projects was called Specific Surface Corporation whose technology formed the basis for his next venture Figulo, which was sold to 3D Systems in 2013. Again, in 2017, Jeffery was instrumental in starting Boston Ceramics a subsidiary of German company FIT AG who then moved the Boston-based 3D printing production to their facility in Bavaria in 2019.
In late 2019 Jeffery moved to California to start Forust with Rael and San Fratello. »Although we are actively seeking investors, but in the current adverse economic climate the company is currently self-funded and exploring and developing products for sale to generate revenue.« explains Jeffery. Their goal is to have their first collection of 3D printed products ready for market by the end of 2020.
FURTHER INFORMATION:
Tags
- Tool and die making