Text: Thomas Masuch; Fotos: Forust Corporation — 10.09.2020
Der 3D-Druck-Veteran Andrew Jeffery hat jede Menge Ideen für die Verwendung von 3D-gedrucktem Holz. In den Büroräumen in der Bay Area von San Francisco arbeitet der CEO von Forust mit einem eigens modifizierten 3D-Drucker, um verschiedene Holzmaterialien und Rezepte zu testen.
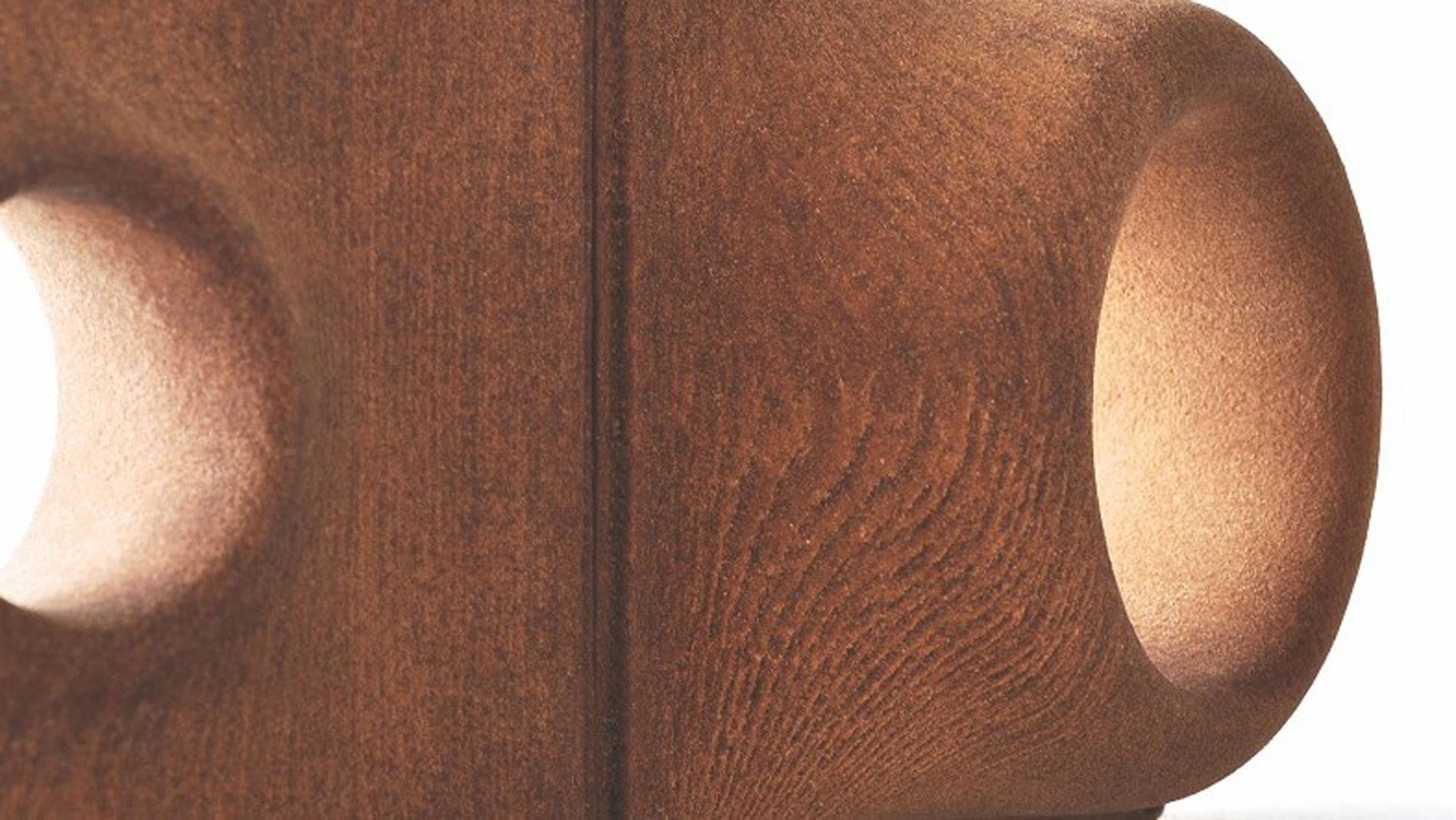
»Holz ist ein natürliches, ökologisches und schönes Material«, schwärmt Jeffery im Interview mit dem Formnext Magazin. Einen Großteil seiner früheren Karriere hat er sich 3D-gedruckten Keramiken gewidmet, inzwischen ist er vom nachhaltigen und wiederverwertbaren Charakter von Holz begeistert: »Wir drucken mit Sägemehl, also landwirtschaftlichen Abfällen, und unser Verfahren schafft Produkte, die leicht, funktionell, schön anzusehen und nachhaltig sind.«
Forust ist inzwischen ein Jahr alt. Zu den Gründern des jungen Unternehmens zählen auch Virginia San Fratello, Professorin für Innenarchitektur an der San José State University, und Ronald Rael, Professor für Architektur an der University of California Berkeley. Im Jahr 2010 hatten San Fratello und Rael bereits Emerging Objects ins Leben gerufen – einen »Make Tank«, der Materialien und Bauanwendungen für den 3D-Druck entwickelt. Rael und San Fratello entwickelten den 3D-Druck von Holz als Teil ihrer Forschung an ihren jeweiligen Universitäten.
"Wir befinden uns in einem sehr frühen Stadium und haben noch viel Entwicklungsarbeit zu leisten."
Mit Jeffery haben sie sich zusammengetan, um eine 3D-Druck-Kollektion von Holzfliesen und -blöcken für Innenarchitekten zu entwickeln. Daneben haben sie auch Ideen für die Entwicklung von Beleuchtungskörpern, Möbeln, leichten Bildschirmen zur Unterteilung von Büros und öffentlichen Räumen, Schreibtischzubehör, Lüftungsabdeckungen und vielen anderen Produkten für den Innenbereich. Sogar der 3D-Druck von hölzernen Musikinstrumenten wurde erforscht. Diese ganzen Vorhaben drehen sich um die zentrale Frage, wie der Rohstoff Holz im 21. Jahrhundert verwendet werden kann, erklärt Jeffery. »Das verbindet sich zur Hoffnung, dass es möglich wird, solche Produkte für zu Hause oder das Büro in einem Geschäft vor Ort zu kaufen.«
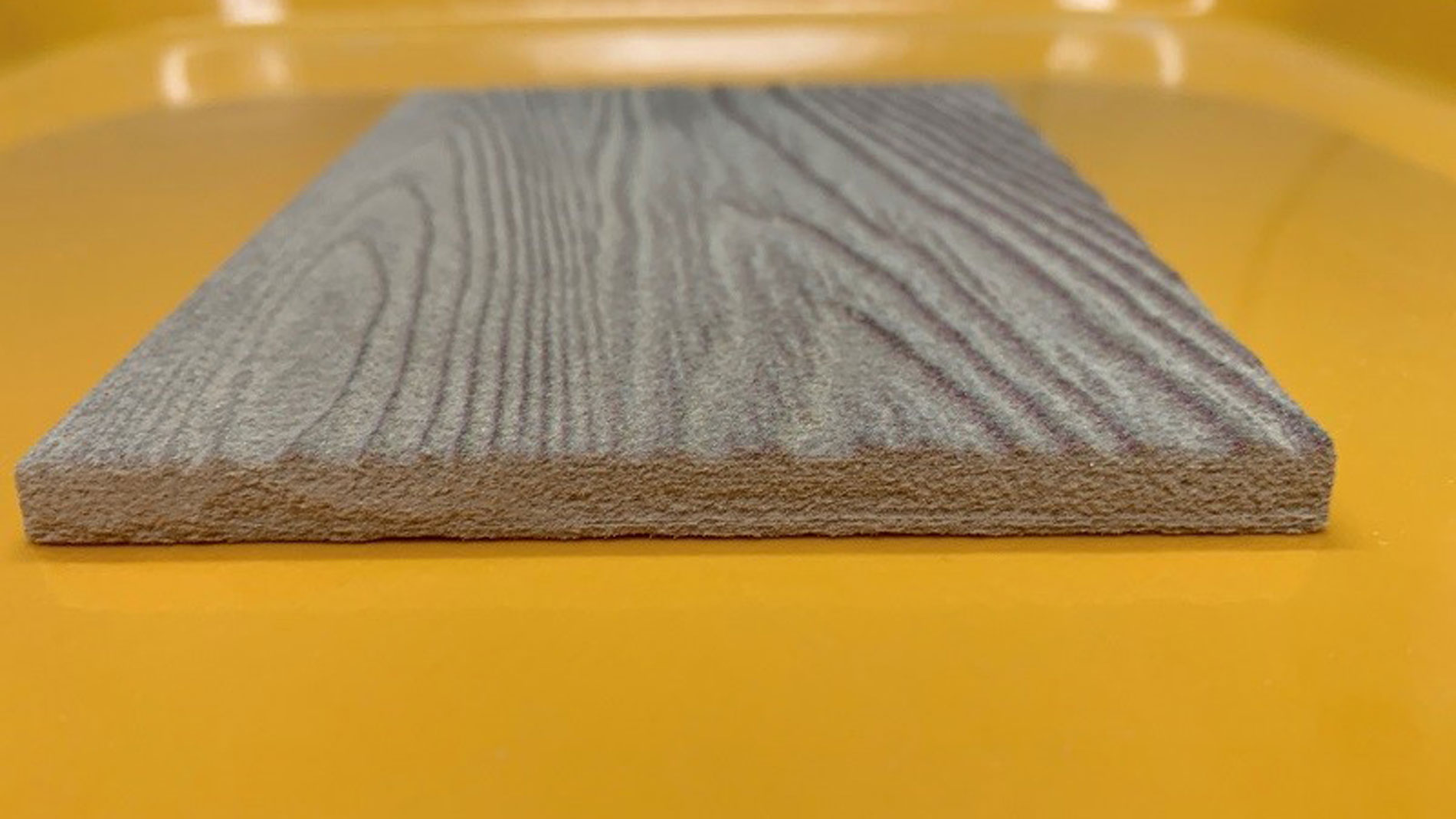
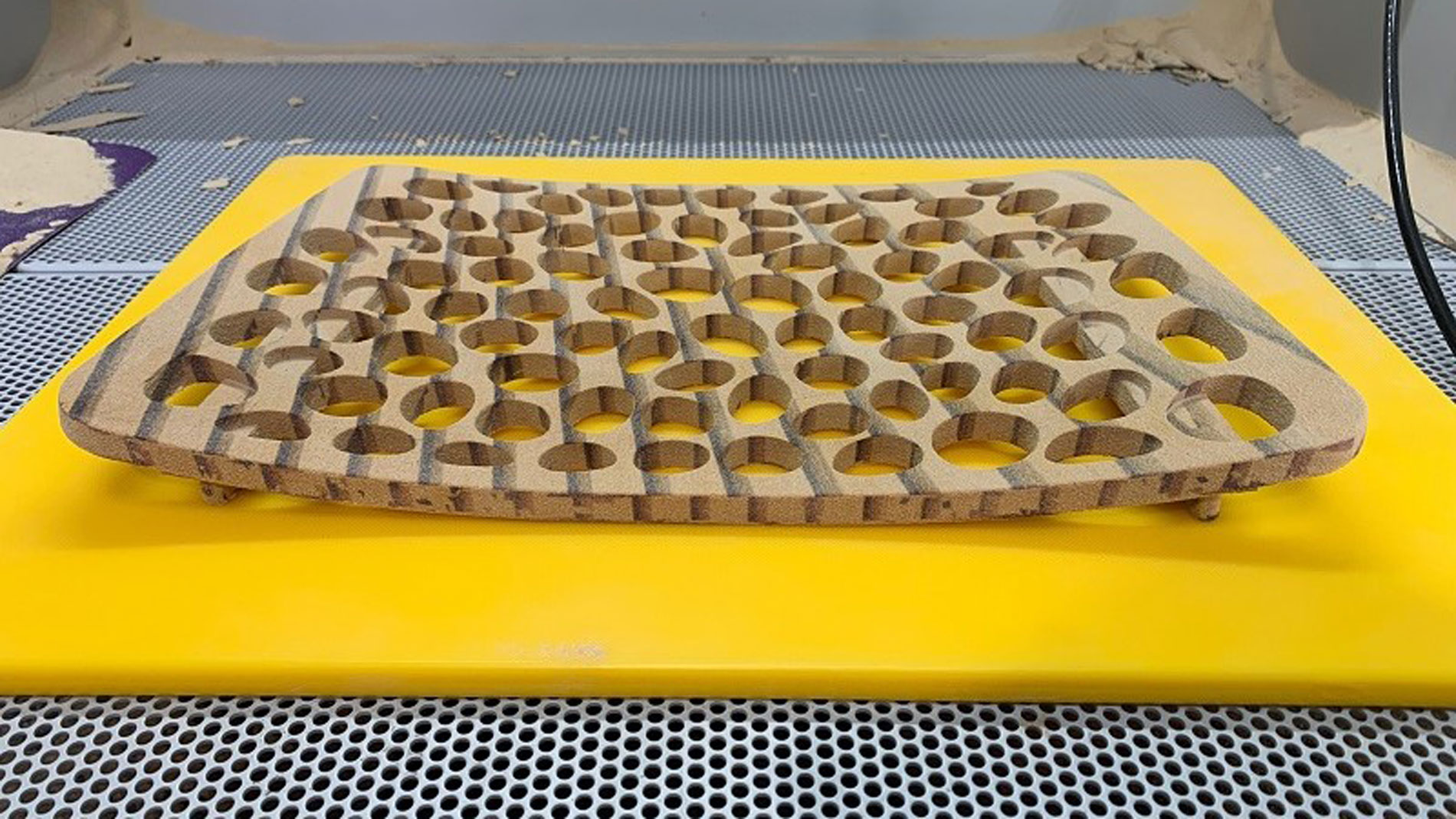
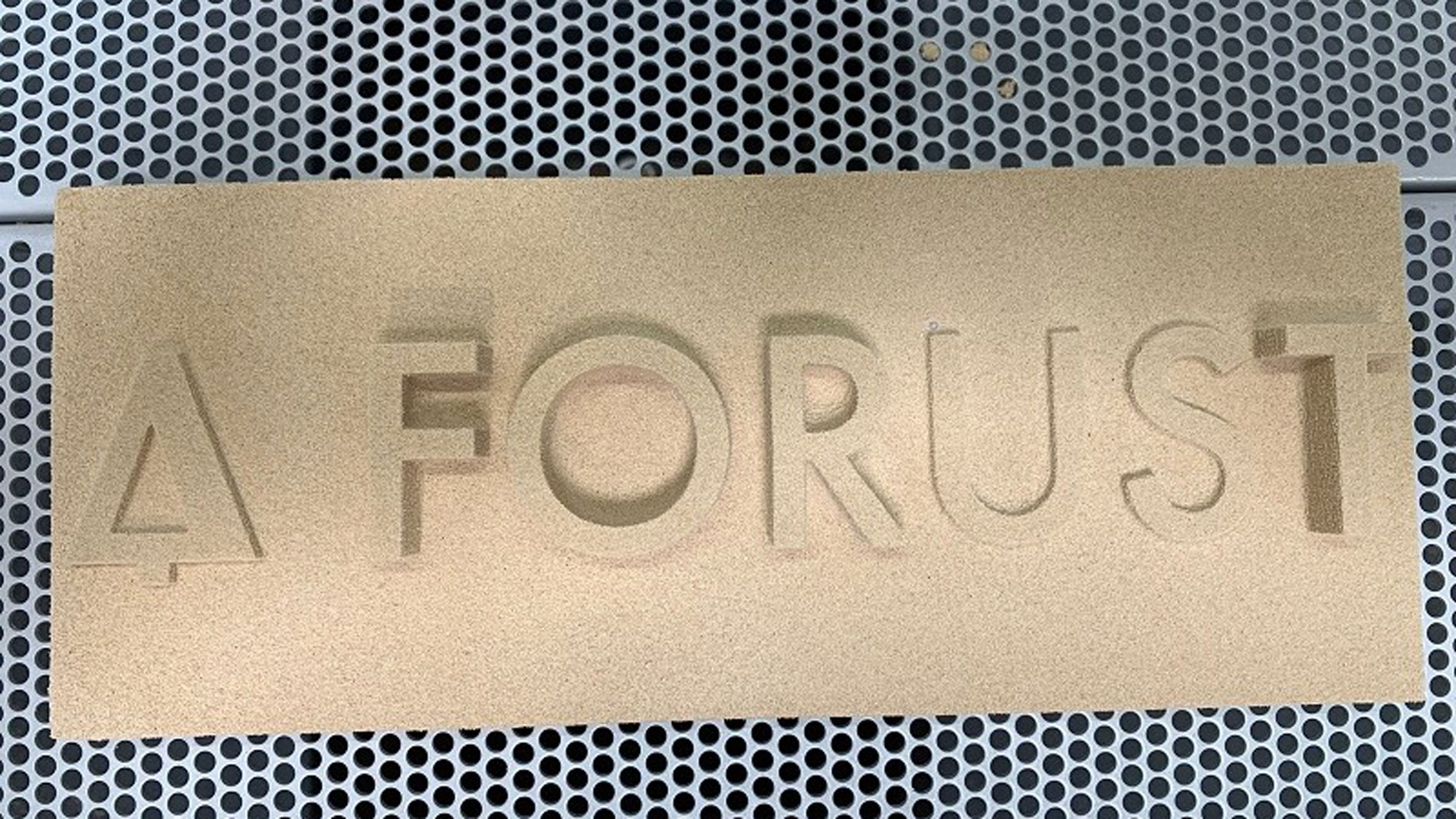
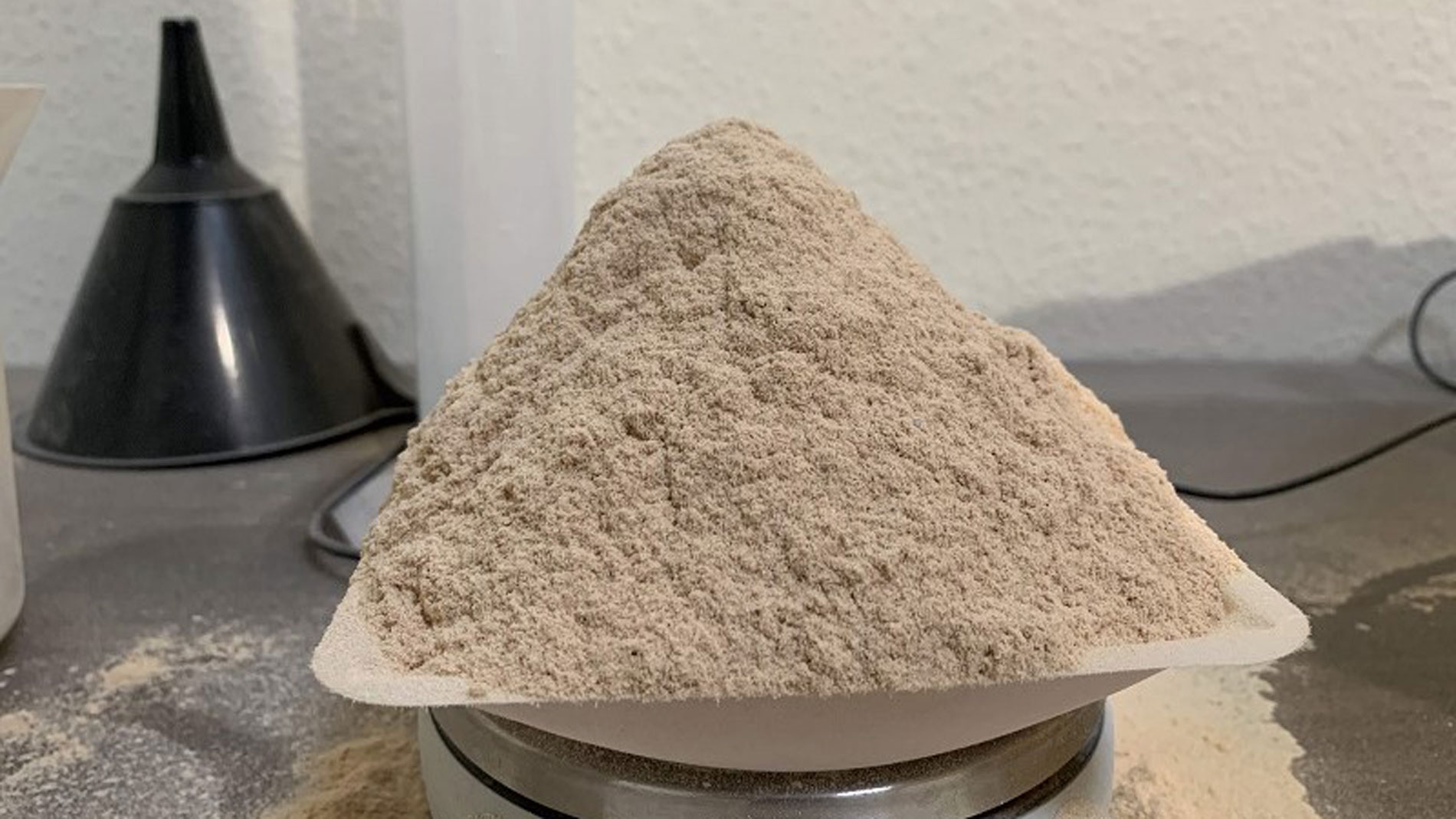
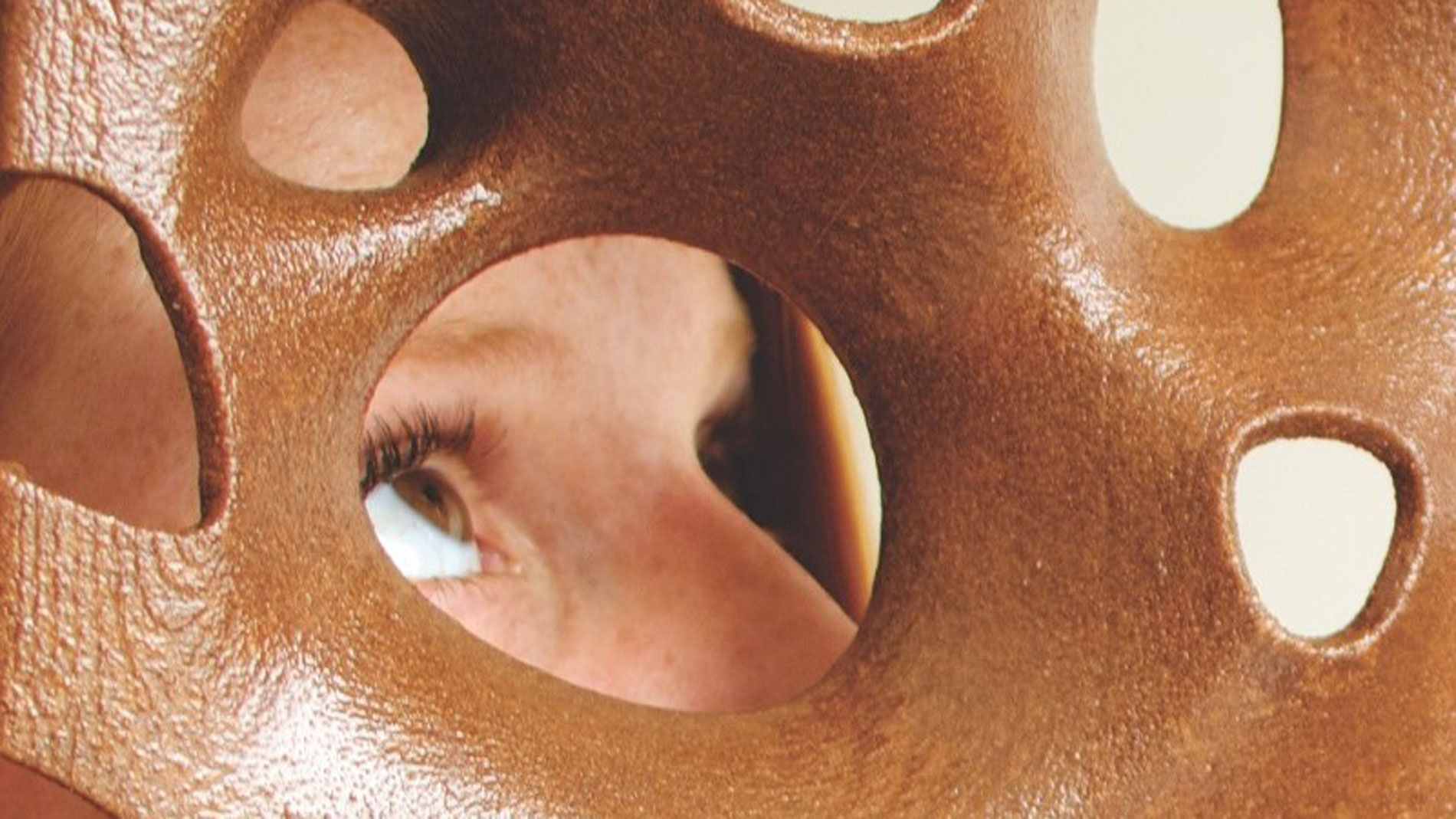
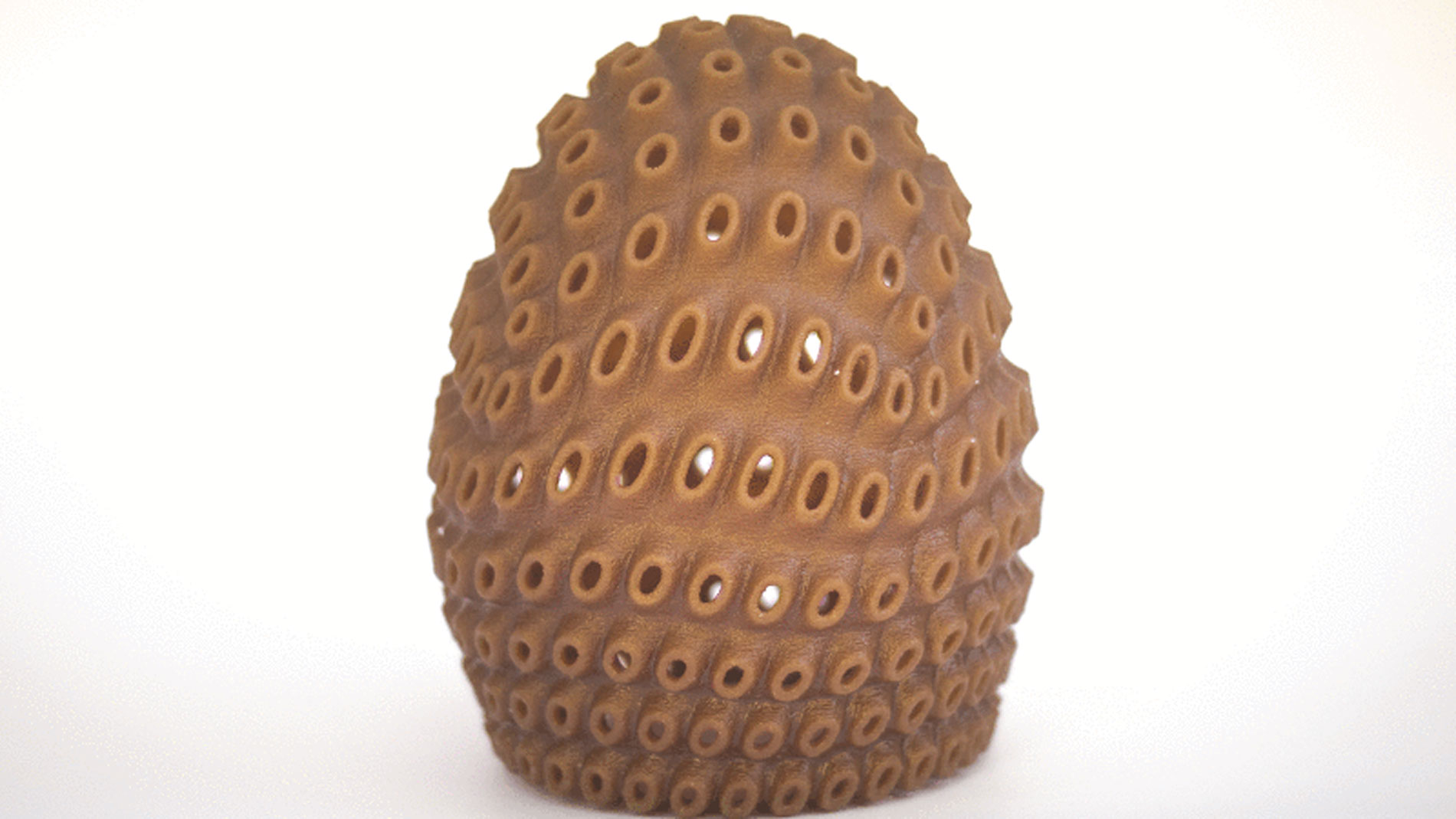
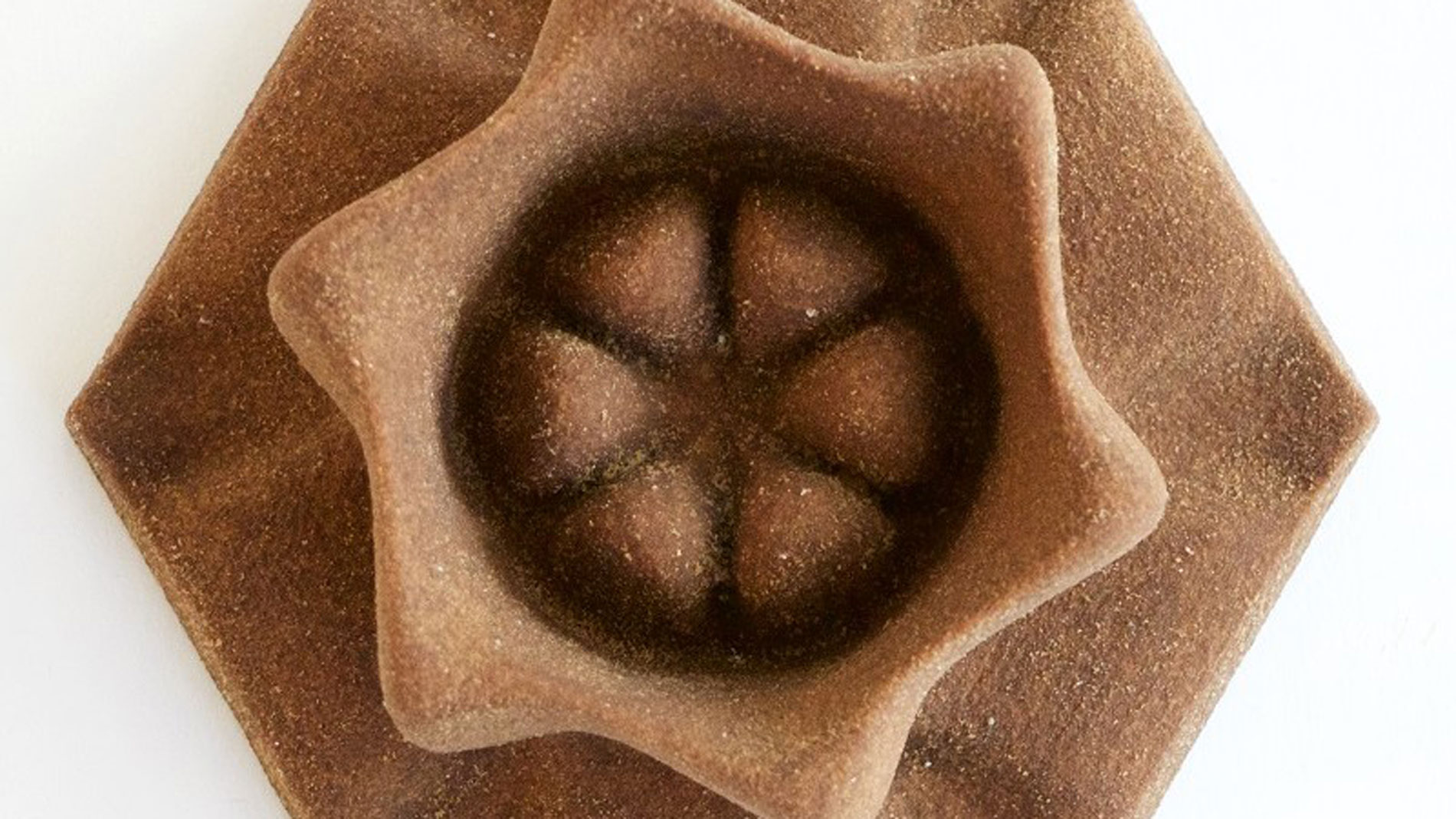
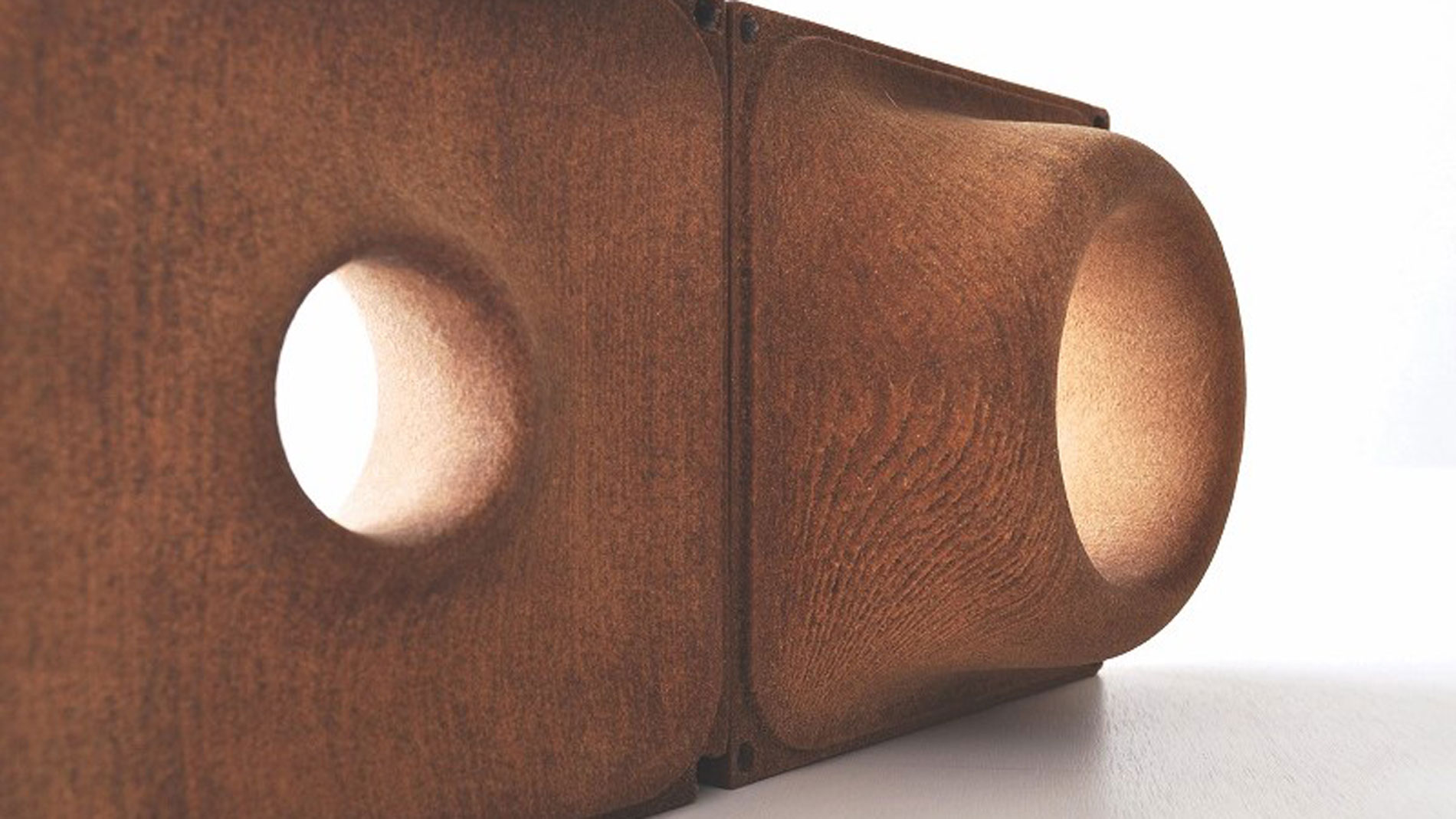
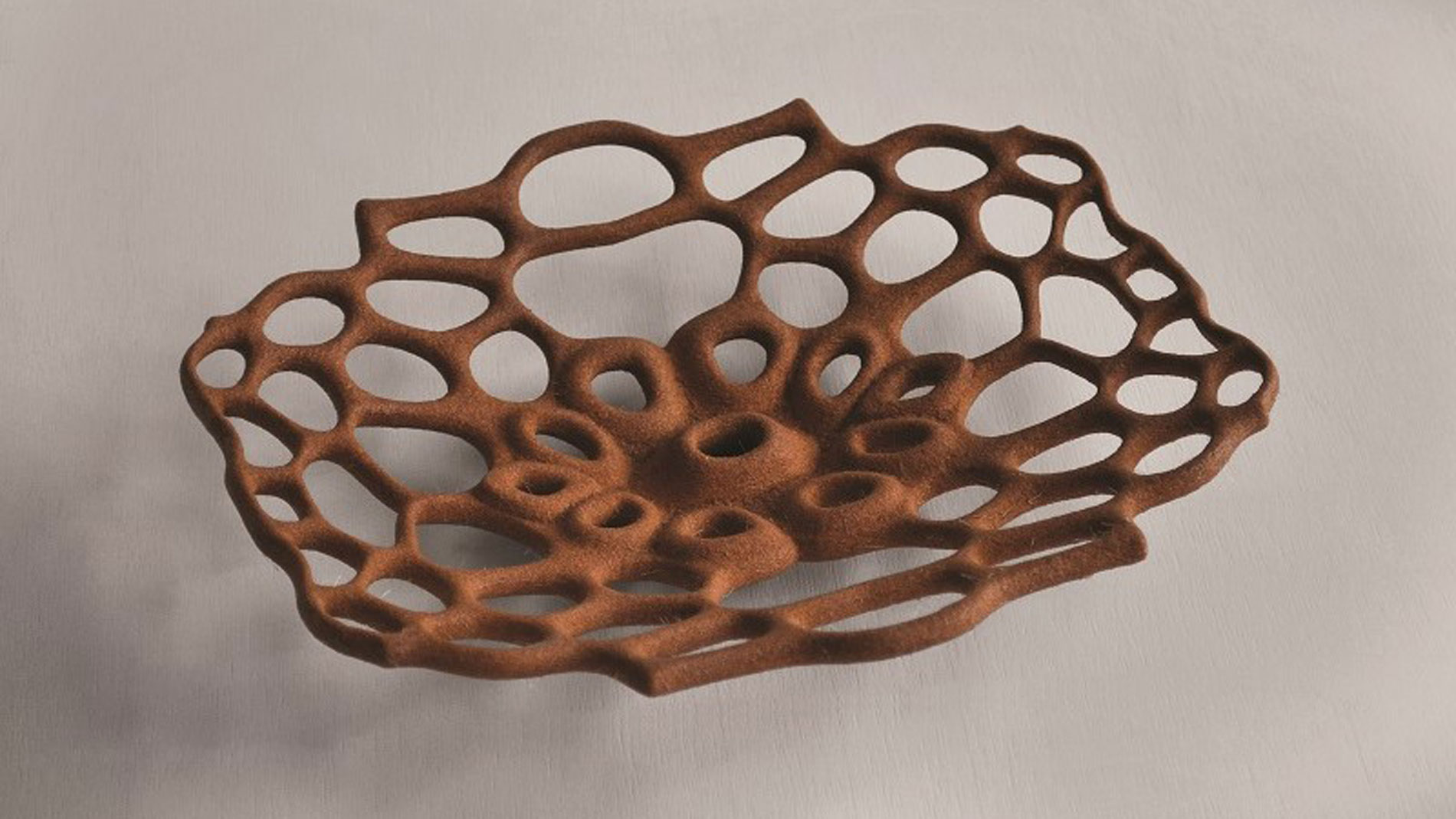
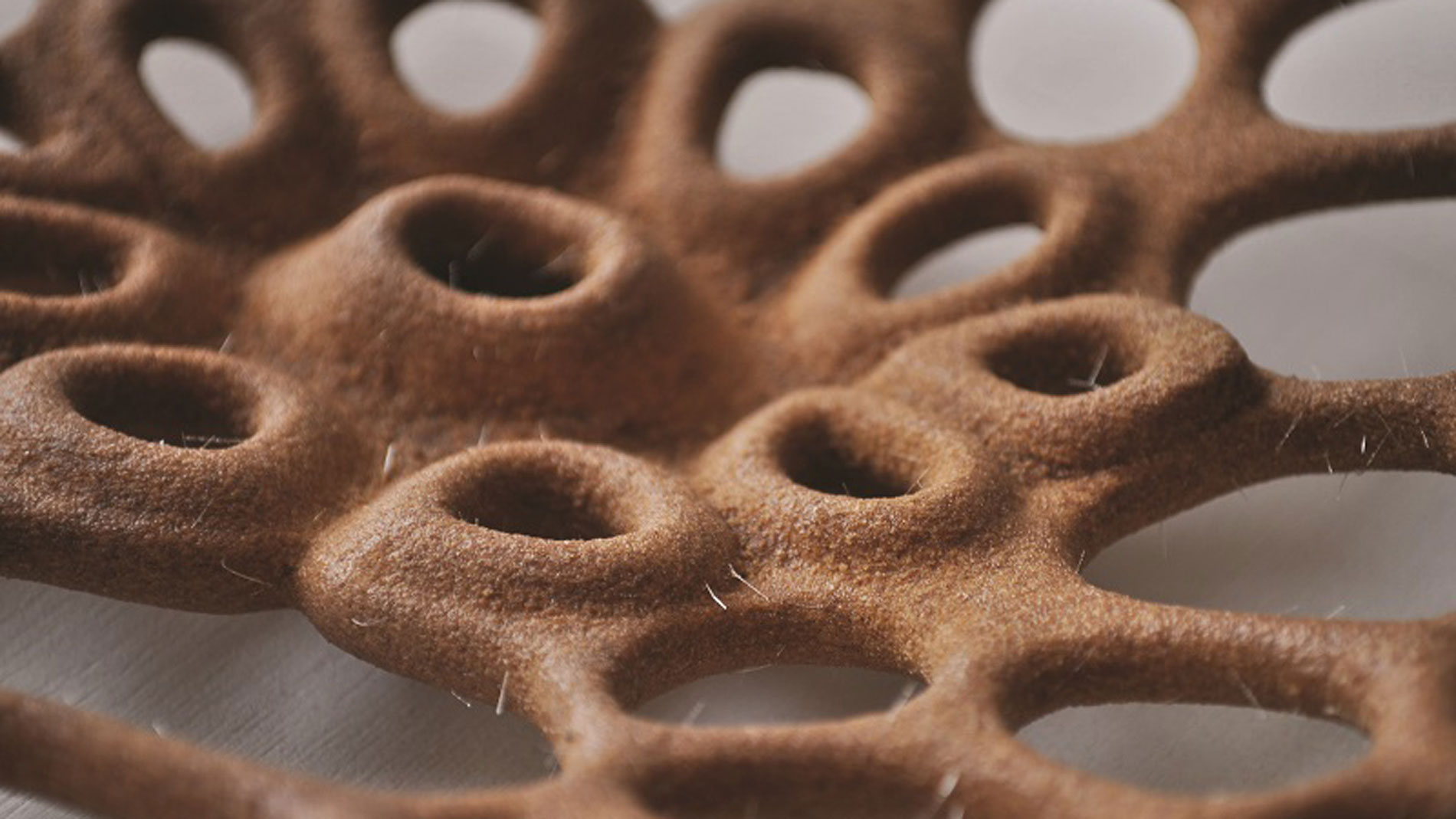
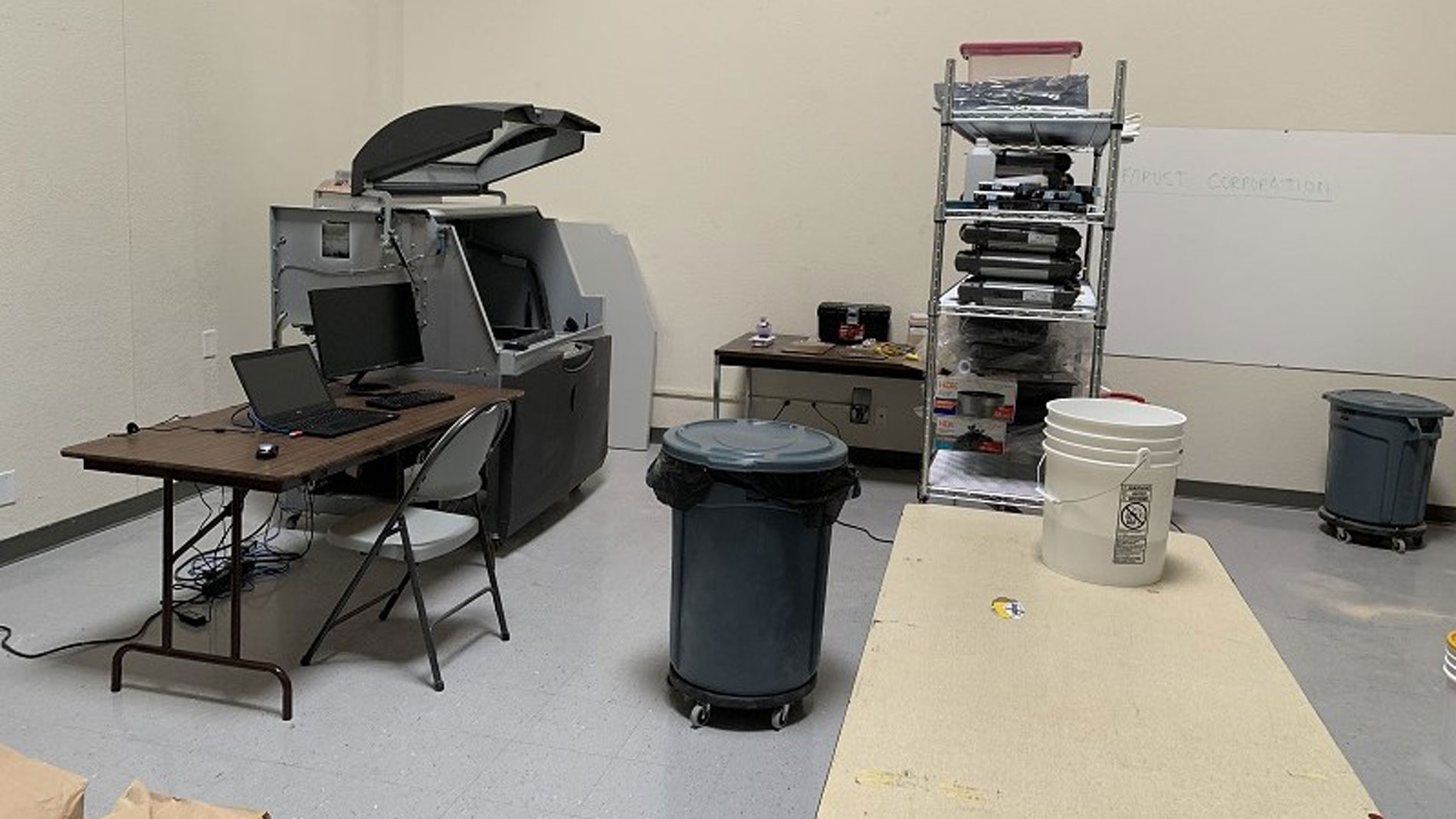
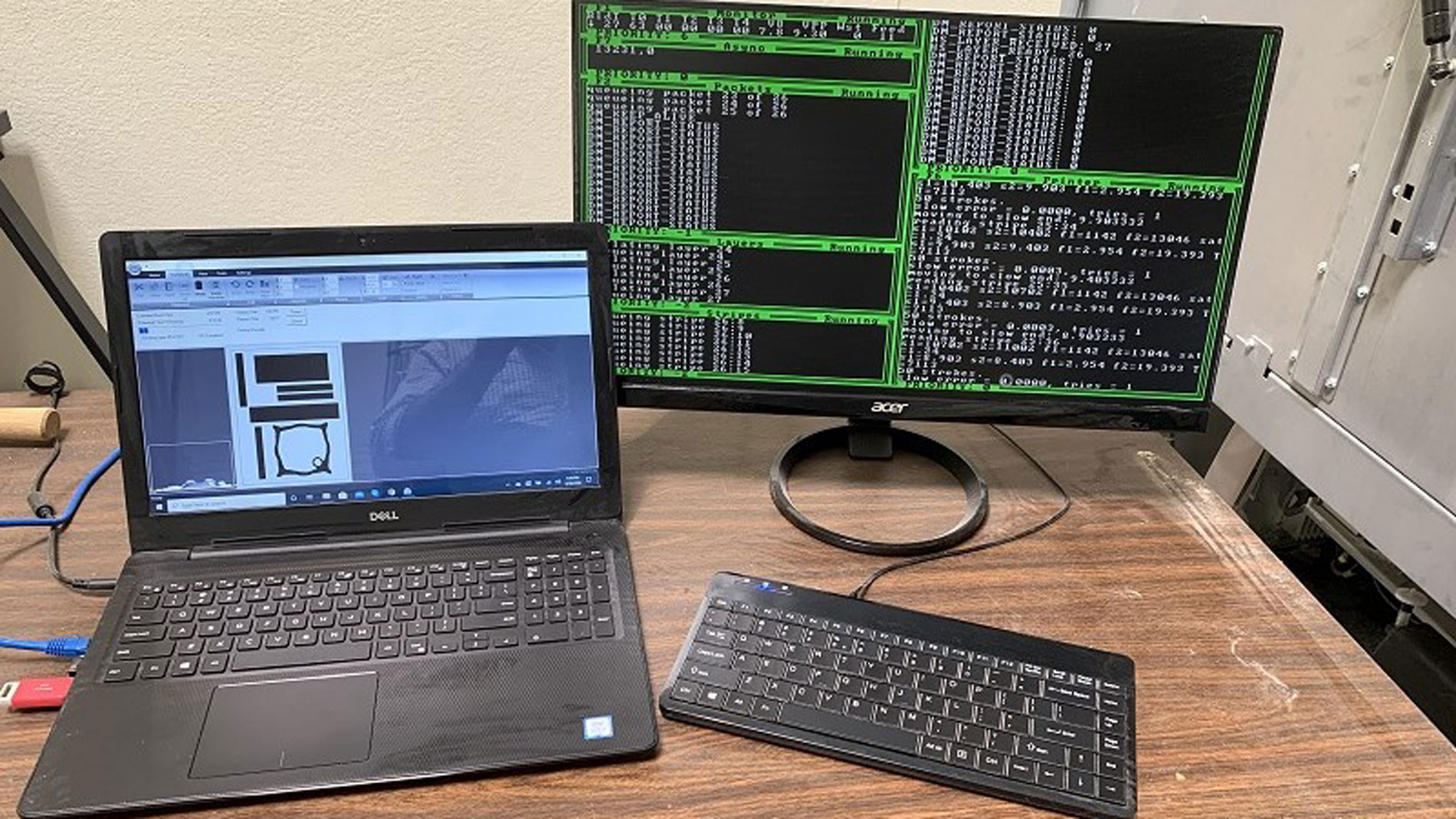
Bevor eine solche konkrete Umsetzung beginnen kann, haben Jeffery und seine beiden Mitstreiter noch einen langen, arbeitsreichen Weg vor sich. »Wir befinden uns in einem sehr frühen Stadium und haben noch viel Entwicklungsarbeit zu leisten«, erklärt Jeffery. Gegenwärtig werden zahlreiche Prototypen gebaut und auf dem neuen ProJet 860 von 3D Systems getestet. Auch am Drucker selbst werden Modifikationen vorgenommen: Zum Beispiel wurde die Tintendüse abgeklemmt und die Pulverzufuhr an die Rauheit des Holzes angepasst. »Wir haben auch die Dicke der Schichten deutlich erhöht, um die Druckzeit zu minimieren«, so Jeffery. »Dadurch entsteht eine strukturiertere Oberfläche, die mehr an Holzmaserung erinnert.«
Das verdruckte Material ist eine Mischung aus Sägemehl, Holzresten, Holzkleber und Wasser. Der hohe Nachhaltigkeitsfaktor entstehe dadurch, dass das Holzmaterial im Prinzip nur aus günstigen Abfällen aus der Holzindustrie bestehe, die zum Beispiel normalerweise zu einem Preis von 70 Euro je Tonne an Kraftwerke verkauft und dort verfeuert werden. Für den 3D-Druck lässt sich laut Jeffrey auch recht günstiges Bauholz verwenden, das sonst für Möbel ungeeignet wäre. Außerdem laufen Versuche mit Bambus.
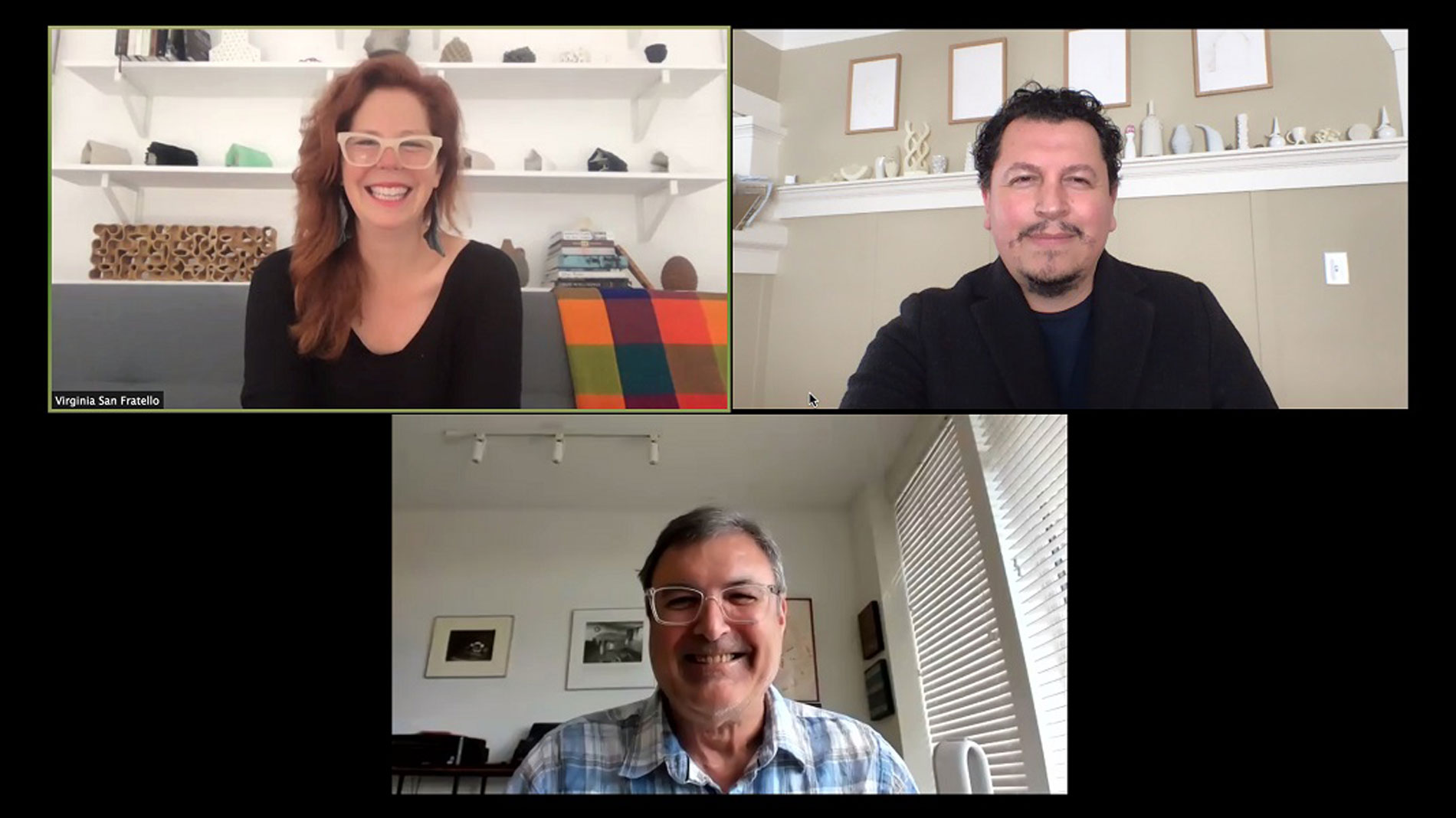
Die technischen Modifikationen des Verfahrens und des 3D-Druckers waren keine großen Herausforderungen für Jeffery, der sich als Ingenieur seit Anfang der 1990er-Jahre mit dem 3D-Druck beschäftigt. »Damals steckte die Technologie ja noch in den Kinderschuhen.« Zudem hat er auch Erfahrung mit Start-ups und der Gründung neuer Unternehmen: Eines seiner frühen 3D-Druckprojekte hieß Specific Surface Corporation, deren Technologie die Grundlage für sein nächstes Unternehmen Figulo war, das 2013 an 3D Systems verkauft wurde. Zu seinen weiteren Karriereschritten zählt Jeffery auch, dass er maßgeblich an der Gründung von Boston Ceramics im Jahr 2017 beteiligt war – einer späteren Tochtergesellschaft der deutschen FIT AG. 2019 wurde das Unternehmen allerdings geschlossen und die 3D-Druckproduktion an den FIT-Hauptsitz im bayerischen Lupburg verlegt.
Ende 2019 zog Jeffery nach Kalifornien, um zusammen mit Rael und San Fratello Forust aufzubauen. »Wir sind zwar aktiv auf der Suche nach Investoren, aber in der aktuellen ungünstigen Wirtschaftslage finanziert sich das Unternehmen selbst. Wir erforschen und entwickeln Produkte für den Verkauf, um Einnahmen zu erzielen«, erklärt Jeffery. Die erste Kollektion von hölzernen 3D-Druckprodukten soll bis Ende 2020 zur Marktreife gelangen.
MEHR INFORMATIONEN UNTER:
Tags
- Werkstoffe und Halbzeuge