Text: Jim Woodcock
Additive Manufacturing is far from the first technology to go on the journey of industrialization. This allows us to learn a lot from other technologies that have already taken this step - robotics, for example.
The growth and industrialization of robotics is analogous to that of robotics in many ways. The first robotics systems suffered from complex programming, unreliable operation, lack of flexibility and prohibitive costs. Where a robot could be accommodated it was undertaking simple, repetitive tasks that could be programmed once and run indefinitely. The high upfront costs and relatively slow payback time could only be absorbed by the biggest scale players, such as spray-painting panels on an automotive assembly line.
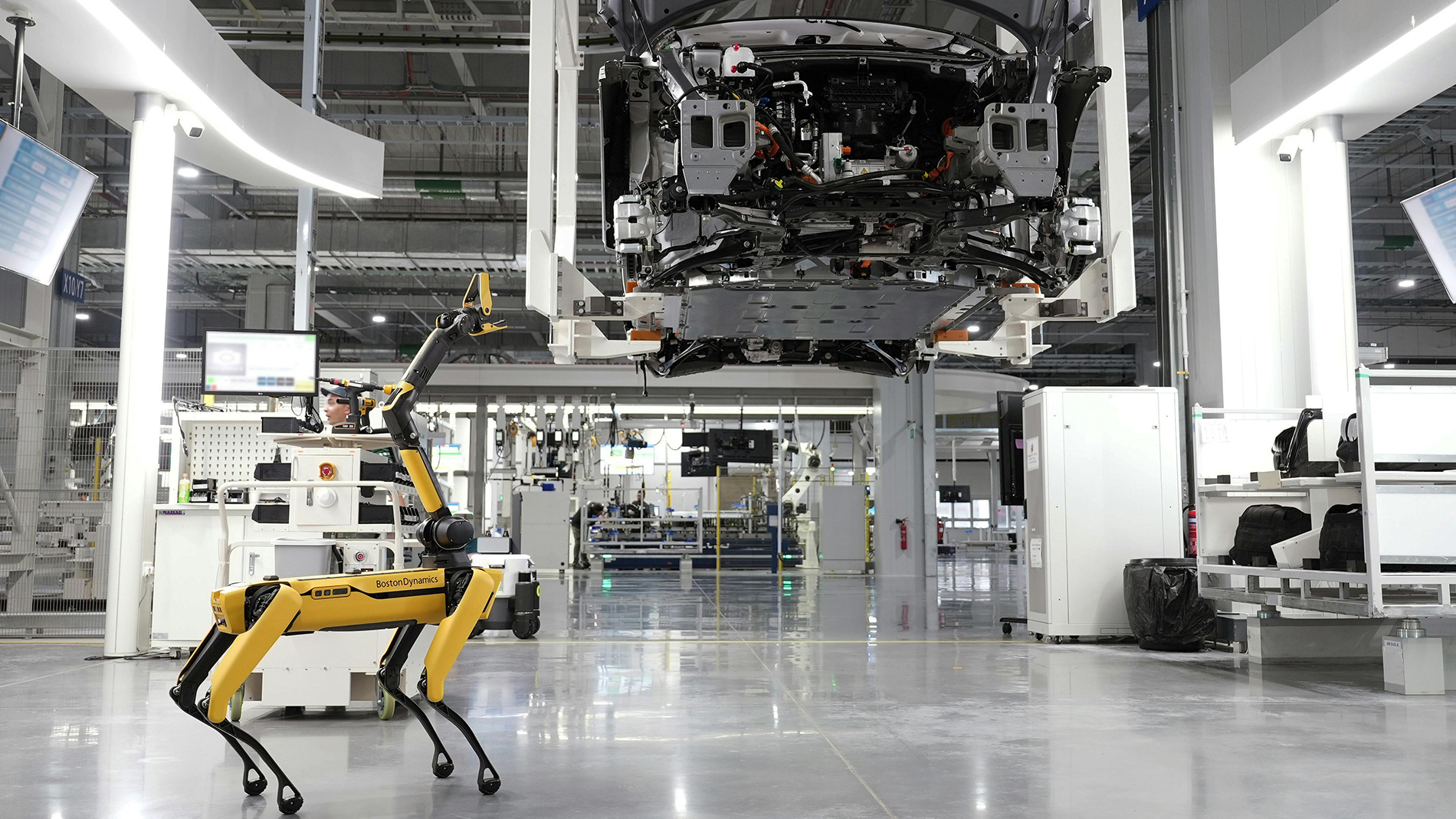
Robotics are now almost ubiquitous not only in manufacturing but also in healthcare, retail, logistics and more. So, what changed?
Standardization & modularity
The rise of standardized interfaces and modular robotic systems made integration easier, reducing costs and increasing scalability. Similarly, AM must develop plug-and-play solutions that work seamlessly within existing production lines.
Programming was revolutionized by AI & machine learning
Easier programming and integration ofAI enabled greater flexibility in deployment and use of robots, allowing for adaptive automation. In AM, AI-driven design optimization and process monitoring could enhance repeatability and efficiency.
Cost reduction
Initially, robots were expensive investments but by leveraging economies of scale, competition, and technological refinements costs were driven down. AM can follow a similar path by streamlining material production and automation to drive down costs.
Collaborative robots (Cobots)
Traditional industrial robots required specialized enclosures, but cobots introduced safety features that allowed seamless human-robot collaboration. While we don’t want to open up AM machines in the same way, opening up AM to a larger percentage of the workforce would aid uptake and create a positive feedback loop.