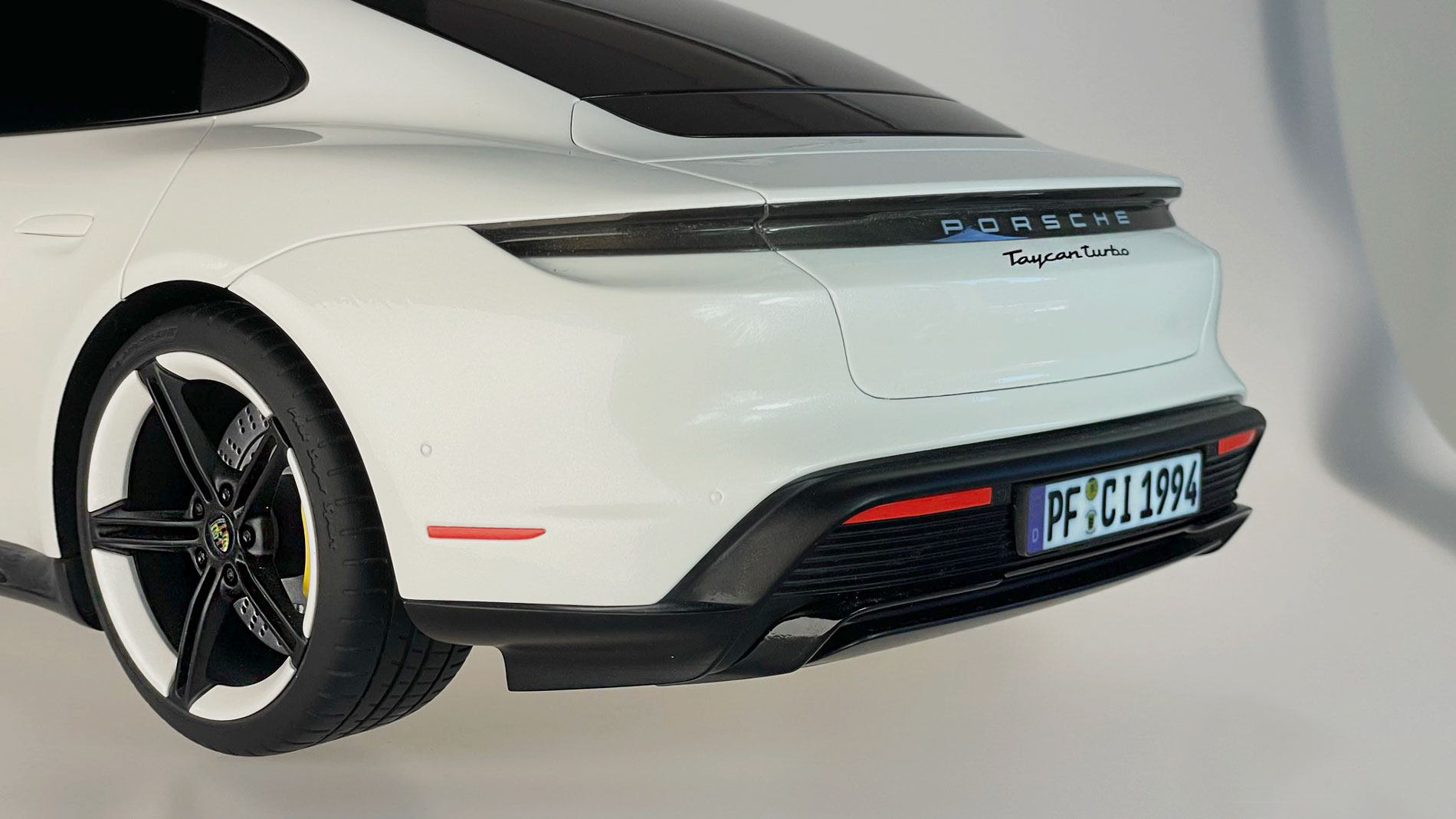
Cirp is a leading provider of 3D printing services in southern Germany that celebrated its 30th anniversary in 2024. Since its foundation, it has considered itself a partner for plastic components starting from a batch size of one with a dedication to additive manufacturing, rapid tooling, and injection molding. Indeed, the company’s machine park now comprises more than 25 industrial AM systems, including SLA, polyjet, SLS, and FDM installations with varying build spaces and a broad range of supported materials. The various technologies it works with are one of the main reasons why cirp attaches a great deal of importance to offering tailored guidance. This enables customers to benefit from the decades of experience its 70 employees can bring to bear.
In cases involving special material requirements or quantities anywhere between 50 and 10,000, for example, injection molding is often the better, more reliable option. Here, cirp has established its own process chain with highly standardized workflows and solutions. Its seven modern, fully electric injection-molding machines are capable of up to 450 tons of clamping force, and each has its own dedicated master mould. This means cirp only needs to manufacture tool inserts for specific customers and components. From tool design and programming all the way to the processing of high-strength aluminum on four machining centers with three or five axes, the entire process takes place under the same roof. This enables cirp to proceed from an initial order to a first batch of standard-material components in record time – two to three weeks in most cases. If a project is super urgent, the company can even provide assistance within a week.
Broad customer base
cirp supplies a wide variety of industries. In the greater Stuttgart area, a particular focus is on the automotive industry and related suppliers. Over the decades, cirp has grown continuously to meet their requirements and now supplies numerous other sectors such as mechanical engineering, robotics, capital goods, electronics, household appliances, battery technology, aviation, two-wheelers, medical technology, architecture, and furniture. At the same time, cirp’s broad base of clients ranges from start-ups and freelance designers to numerous midsized companies and well-known DAX corporations.
The team at cirp also enjoys receiving more exotic inquiries involving things like museum exhibits or trophies for special competitions. Challenges like these typically require more than expertise in manufacturing and materials: Data specialists need to process scanned information, provide support in production-oriented design, and serve as helpful “sparring partners” in discussions with customers. Finally, cirp places special emphasis on the careful finishing of additively manufactured parts. Grinding, polishing, dyeing, painting, and assembly are required for a large portion of its projects. Transparent components – which happen to be one of cirp’s greatest strengths – have to meet particularly high standards in this regard.
Pushing the envelope in AM
At cirp’s headquarters in Heimsheim, no one is ever satisfied with the current state of the art. The company’s in-house research team is always immersing itself in innovations and actively seeking to push the boundaries of processes, materials, and applications in AM. For proof of its regular participation in funded research collaborations, one need look no further than the exhibits cirp brings to Formnext every year: Custom software for lattice generation, an SLS and powder management process based on Industry 4.0, artificial organs for surgical training, 3D-printed free-form lenses, and much more amaze and inspire vistors.
Further information:
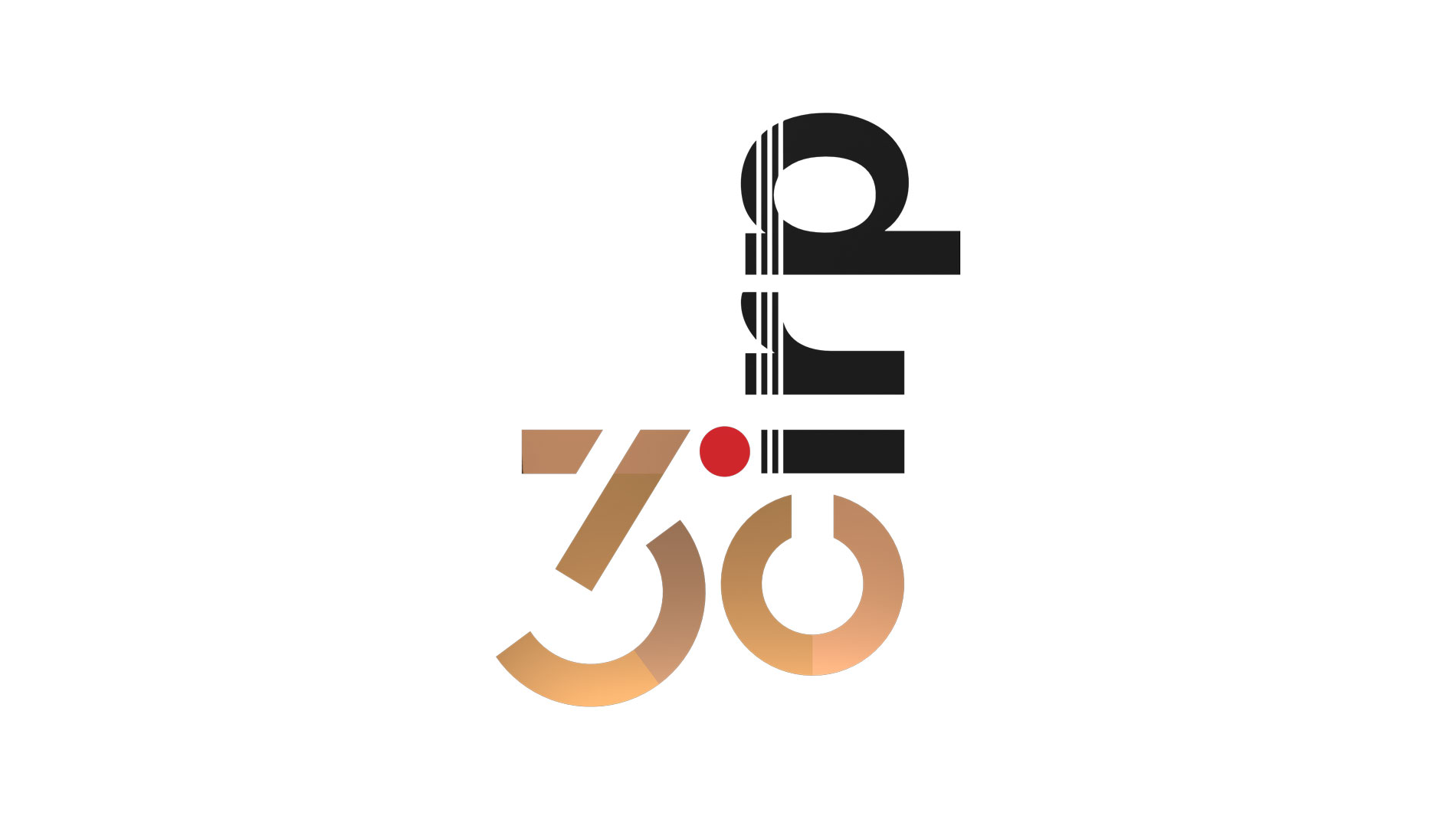
cirp GmbH
Römerstraße 8
71296 Heimsheim, Germany
Phone +49 07033 30987-0
info@cirp.de
cirp.de