Today’s battery cells are developed in multiple phases – from the laboratory scale and initial functional samples to industrial series production. However, one thing is often overlooked: Throughout the entire process, cell housings are usually only needed in very small quantities where conventional manufacturing technologies quickly run up against their limits.
Methods such as deep drawing or impact extrusion require more complex tools that take significant amounts of both time and money to procure. In fact, a single tool can easily run into the hundreds of thousands. Meanwhile, conventional alternatives such as machining or combinations of bending and welding present their own challenges.
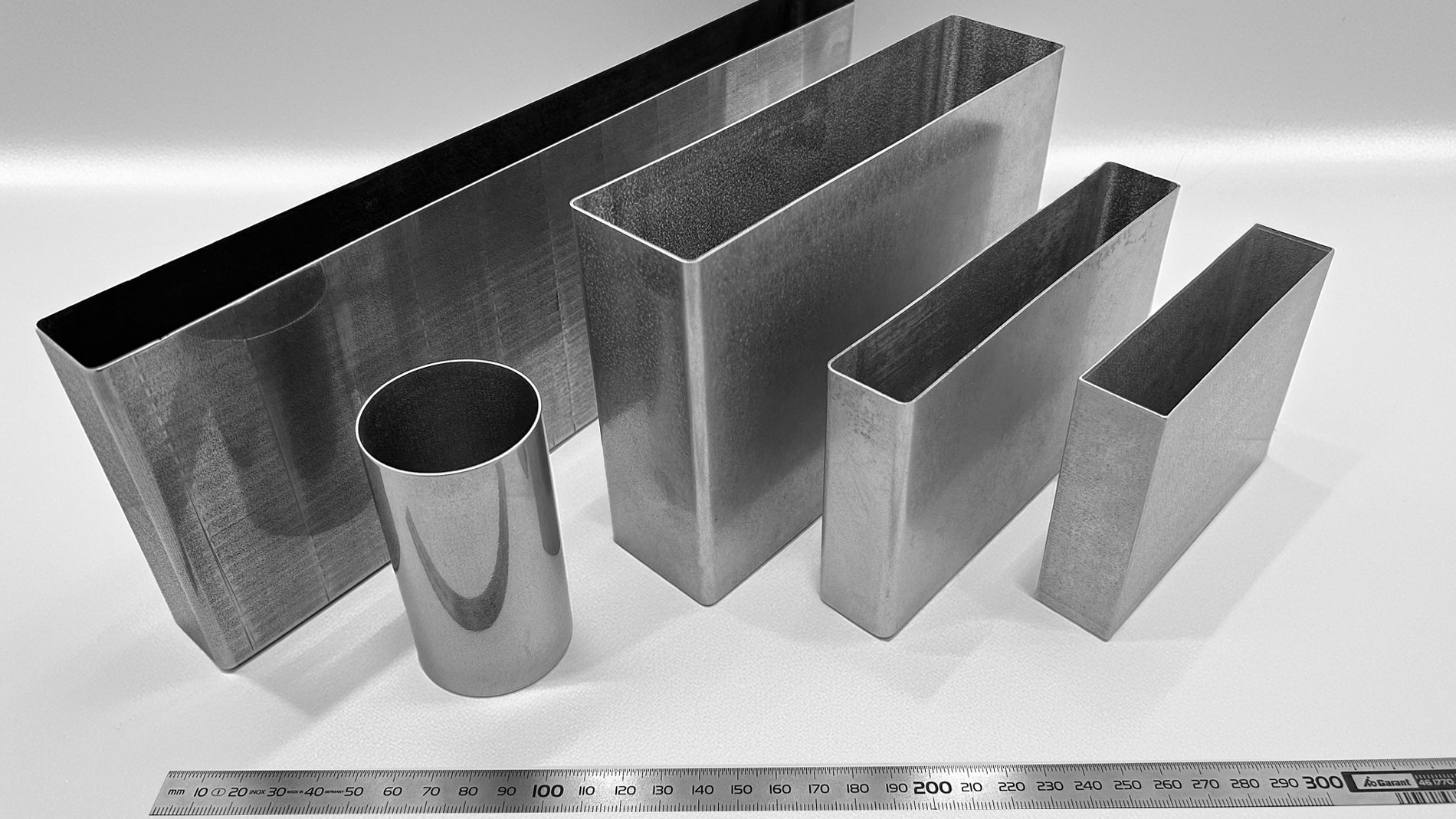
Pure aluminum for battery cell housings
This is where additive manufacturing based on PBF techniques offers a number of key advantages. For instance, it makes it possible to carry out design iterations in short order without additional tooling costs, which is ideal for early phases in cell development where speed, flexibility, and efficiency in the provision of housings are essential.
In its research efforts, the Fraunhofer Institute for Casting, Composite, and Processing Technology IGCV recently succeeded in qualifying pure aluminum as a material for the additive manufacturing of battery cell housings. By making targeted adjustments to its exposure strategy and employing vertical support structures, it was able to produce thin-walled cell housings with high dimensional accuracy and minimal warpage.
The components produced exhibited impressive integrity, as well, passing helium leak tests with a wall thickness of just 0.8 mm. This confirmed the production method as suitable for functional prototypes and pre-series applications. In addition, a downstream surface treatment technique involving vibratory grinding makes it possible to achieve an average surface roughness (Ra) of less than 5 μm.
More information:
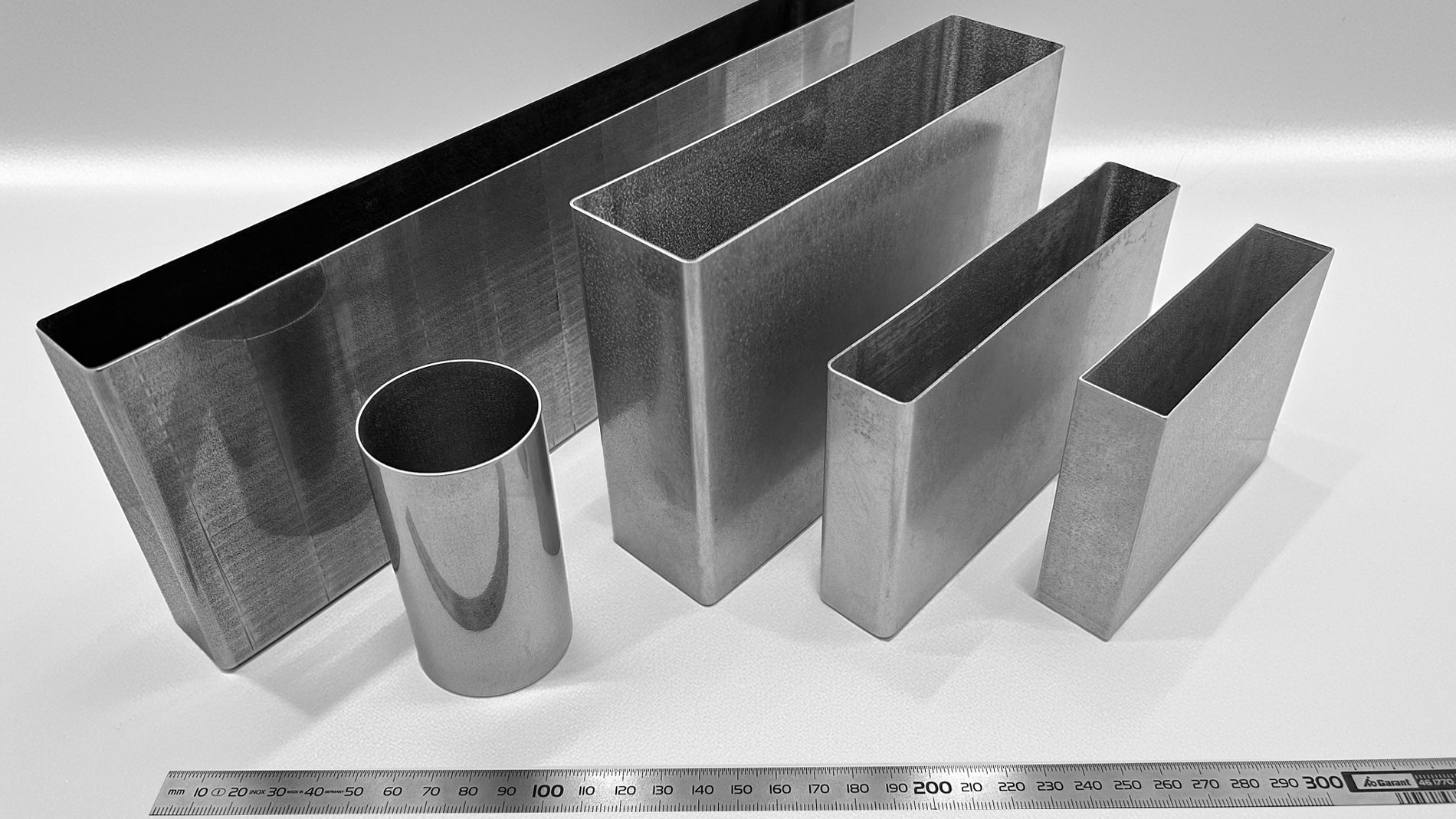
Fraunhofer Institute for Casting, Composite, and Processing Technology IGCV