Text: Jim Woodcock
Once hyped alongside nanotech and MEMS, Micro-AM is now bridging design innovation with manufacturability in real-world applications and shares much with its ‘macro scale’ siblings.
In many ways, the experience of making micro-scale parts through 3D Printing processes directly mirrors that of the macro world. The technologies themselves, while highly specialised, are mostly analogous or at least closely related to macro systems, ditto the materials and finishing processes. And the ongoing journey from prototyping / short-run manufacturing through to serial production is a common goal. But, there are important technological considerations for the manufacture of tiny parts. Whether for prototypes or end-use parts.
Technology overview
A range of technologies are available for fabricating microscale parts from polymers, ceramics, metals and even biological materials. Some reach into nanoscale feature sizes, connecting the micro and nano-manufacturing domains.
1. Two-Photon Polymerization (2PP)
Two-photon polymerization deploys femtosecond (10-15 of a second) laser pulses to selectively polymerize photoresins at microscopic focal points. Only where the two light sources intersect is the energy sufficient to drive the polymerisation proces. This process allows printing with sub-micrometer resolution, surpassing the classical diffraction limit (which is to say, the smallest point that a light source can be focused to, as determined by its wavelength) of conventional photolithography. Features as small as 100nm are achievable, enabling the creation of complex 3D structures impossible by other AM techniques. Leading commercial platforms such as Nanoscribe’s Photonic Professional GT2, UpNano’s NanoOne, and Microlight3D’s microFAB-3D have opened up this technology for advanced research and precise industrial applications.
2. Projection Micro-Stereolithography (PµSL)
Projection micro-stereolithography uses digital light processing (DLP) or LCD technologies to project ultraviolet (UV) patterns onto a photoreactive resin, curing it with precision ranging between 2 and 10µm. This technique offers some balance between resolution, speed and scalability, making it suitable for rapidly prototyping micro-scale devices, micro-optical components, precision connectors and medical components. Boston Micro Fabrication (BMF) offers specialized equipment and custom-engineered resins tailored for demanding industrial uses based on this technology.
3. Micro Laser Sintering/Melting
Micro laser sintering and melting adapt metal powder-bed fusion methods to microscale manufacturing. By employing powders with particle sizes between 5 and 10µm and laser spot sizes of approximately 30µm or smaller (versus 15–45µm powder and 70–100µm laser spot sizes for standard LBPF systems), these methods produce fully dense, high-strength metal components. Ideal applications include precision medical implants, micro-components for aerospace and intricate parts in electronics. Companies such as 3DMicroPrint, EOS, Trumpf, and Additive Industries are active this field, providing specifically designed machines and optimized materials for micro-scale metal AM.
4. Micro Inkjet and Aerosol Jet Printing
Micro inkjet and aerosol jet printing techniques deposit minuscule droplets or aerosol streams of functional materials, often conductive inks or biocompatible polymers, to create finely detailed 2.5D (with only a few layers built up) and multi-layered structures. These processes excel in printed electronics, flexible circuitry, sensors, wearables and biological applications such as cell patterning. Companies like Optomec and nScrypt offer customizable platforms that bridge electronics manufacturing and bioprinting.
5. Femtosecond Laser Processing in Glass
Although technically a subtractive method, femtosecond laser processing modifies transparent materials internally, enabling highly precise and complex 3D structures through subsequent chemical etching. This technology is crucial for creating sophisticated microfluidic devices, optical waveguides and integrated optics. Players like Femtoprint, LightFab, and 3D-Micromac have commercialized this specialized processing method and it should be seen as an interesting adjunct to true additive processes.
6. Lithography-based Metal Manufacturing (LMM)
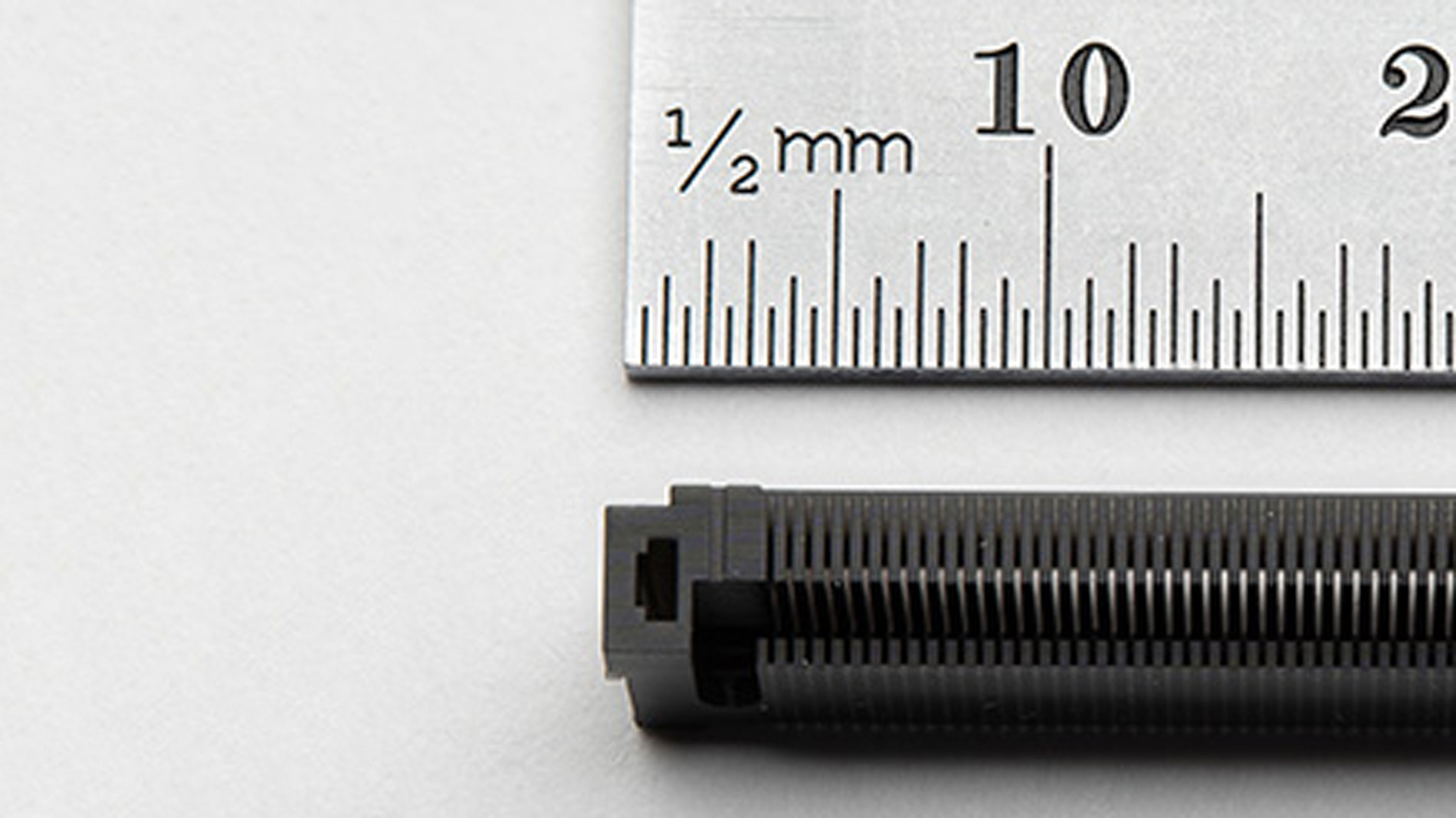
LMM builds upon the principles of stereolithography (SLA), using a photo-reactive resin loaded with fine metal powder. During the printing process, a light source selectively cures the resin layer by layer to create a “green part.” This is followed by thermal debinding and sintering — much like a standard binder jetting technology — which remove the polymer binder and fuse the metal particles into a dense, fully metallic component. Incus3D provides platforms based on this technology for a range of metals and alloys.
7. Direct Electrochemical Deposition (Electroplating AM)
Direct electrochemical deposition, pioneered by companies such as Exaddon with their CERES system, enables nozzle-based precision electroplating at microscopic scales without powders or lasers. This approach delivers exceptionally precise, fully metallic structures with strong electrical and mechanical properties, essential for micro-electronics, micro-sensors, antenna structures and miniature heat exchangers.
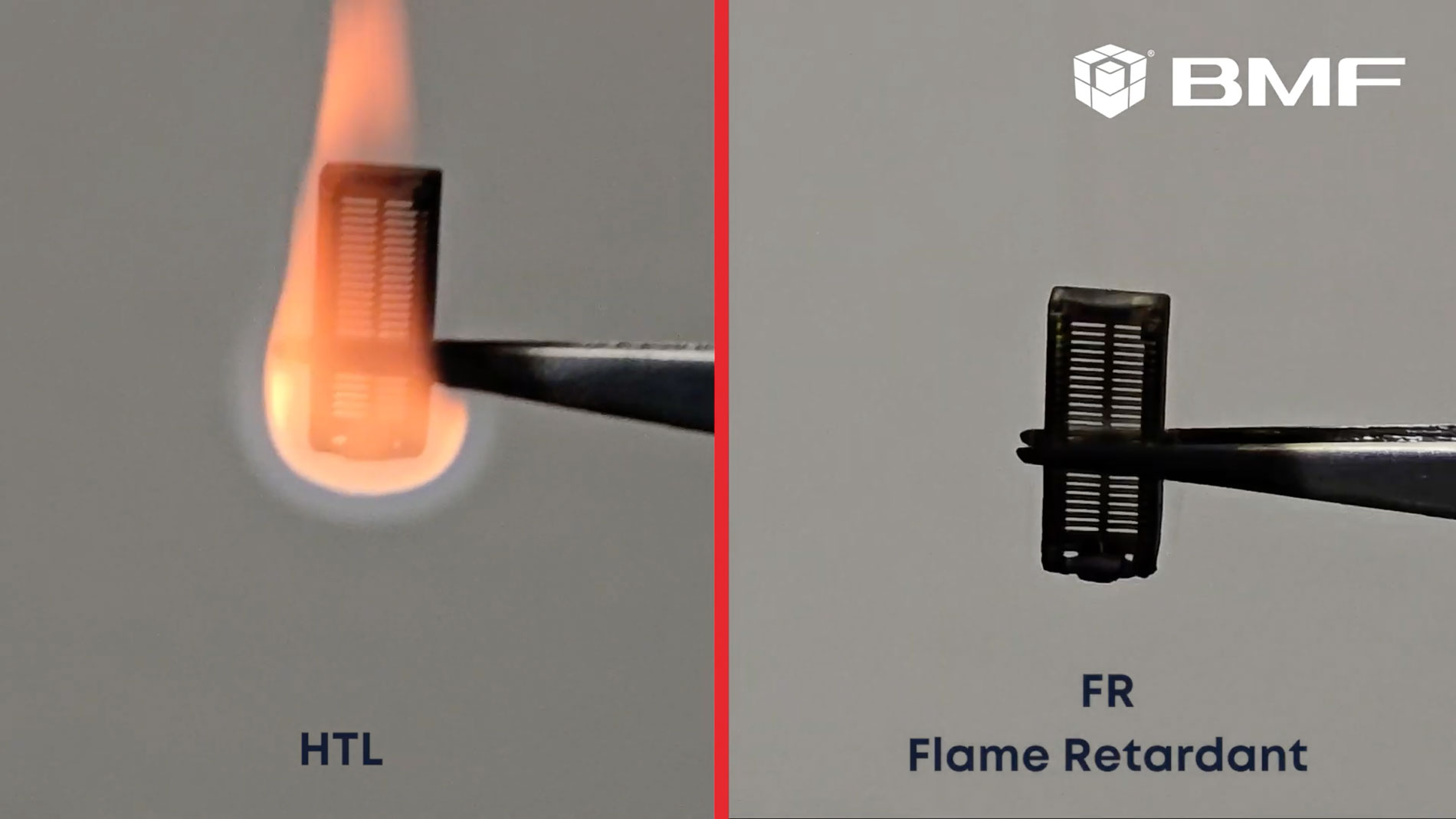
Micro technology is an ecosystem
Materials commonly seen in macro-scale 3D Printing behave differently when used to make parts at the micro-level because of factors such as surface-area-to-volume ratios, heat dissipation, and curing dynamics. These changes to mechanical properties at smaller scales necessitates specialized formulation and rigorous validation at for materials intended for use at micro scales.
Electronics are getting smaller and so too are any 3D printed components. The materials deployed need to be tailored to the micro scale, but most retain characteristics like flame retardancy or biocompatibility. Flame-retardant photopolymers, needed for micro scale electronic connectors and housings, have been developed by companies including BASF, Loctite, and 3D Creations. Biocompatible and bioresorbable resins are important for medical and biotechnology applications, allowing for the creation of precise surgical guides, microneedles, tissue scaffolds and implants.
Scaling up from prototype to production
Despite impressive advances micro-AM remains complex, requiring skilled handling and a high degree of user expertise. Systems manufacturers have tried to span the gap between ’plug and play’ and power with systems that can work ’out of the box’ but also have the ability for advanced setups. Nevertheless, extensive collaboration with vendors for iterative design and rigorous benchmarking remains standard practice, especially in highly regulated industries such as medical device manufacturing.
Post-processing at micro scales presents unique challenges, particularly around support removal, surface finishing, and internal feature cleaning. Just like the macro world, Design for Additive Manufacturing (DfAM) has emerged as essential in efforts to make the most of micro scale 3D Printing with the aims of reducing post-processing complexity and enhancing print accuracy.
Numerous exhibits on various stands at Formnext 2024 also highlighted the significance of Micro 3D Printing. Images: Mesago / Marc Jacquemin
Applications and future directions
Micro 3D Printing is increasingly vital in numerous industries:
- Healthcare: Precision components for minimally invasive surgery, microfluidics for diagnostics, and advanced biocompatible devices.
- Electronics: Customized, rapid prototyping of connectors, sockets, flexible circuitry, and micro-scale sensors.
- Optics: Fabrication of complex optical waveguides, lenses, and micro-optical elements previously unattainable with traditional methods.
- Biotechnology: Microfluidic devices for ‘lab-on-a-chip’ applications, cell patterning and advanced biosensors.
Micro-AM should continue growing in reliability, precision and scalability in response to the demands of the electronics, medical and optics industries. Like the ‘larger’ industry, moving beyond prototyping into mainstream production for increasingly complex and miniaturized devices is one of the challenges and opportunities. Smaller parts often mean tighter tolerances, novel materials and high expectations for performance, which makes Micro 3D Printing an increasingly essential technology in cutting-edge R&D and product development. The smaller the part, the greater the opportunity.