Text: Jim Woodcock
Vor einigen Jahren hatte Mikro-AM einen ähnlichen Hype ausgelöst wie Nanotechnologie oder MEMS. Inzwischen schlägt die Technologie eine Brücke von Designinnovation und bis zu realen Anwendungen und hat viel mit ihren „Makro-Geschwistern“ gemeinsam.
Viele Entwicklungen der Additiven Mikrofertigung ähneln denen aus dem Marko-3D-Druck. Die Technologien selbst sind hochspezialisiert, basieren aber oft auf Vorbildern im Makrobereich – ähnliches gilt für Materialien und des Postprocessing. Auch der Weg vom Prototyping und der Kleinserienfertigung bis hin zur Serienproduktion ist der gleiche. Allerdings gibt es bei der Herstellung von Kleinstteilen technologisch auch einiges zu beachten – das reicht von Prototypen bis zu Fertigteilen.
Technologie-Überblick
Für die Herstellung von Teilen im Mikrobereich aus Polymeren, Keramik, Metallen oder sogar biologischen Materialien stehen eine Reihe von Technologien zur Verfügung. Manche fertigen sogar im Nanobereich und verbinden die Bereiche Mikro- und Nanofertigung.
1. Zwei-Photonen-Polymerisation (2PP)
Bei der Zwei-Photonen-Polymerisation werden Laserpulse im Femtosekundenbereich (10-15 einer Sekunde) eingesetzt, um Photoresine an mikroskopischen Brennpunkten selektiv zu polymerisieren. Nur dort, wo sich die beiden Lichtquellen kreuzen, reicht die Energie aus, um den Polymerisationsprozess voranzutreiben. Dieses Verfahren ermöglicht das Drucken mit einer Auflösung im Submikrometerbereich und übertrifft damit die klassische Beugungsgrenze der herkömmlichen Fotolithografie (d. h. den kleinsten Punkt, auf den eine Lichtquelle fokussiert werden kann, bestimmt durch die Wellenlänge). Es lassen sich Strukturen mit einer Größe von bis zu 100 nm realisieren, was die Herstellung komplexer 3D-Strukturen ermöglicht, die mit anderen AM-Techniken nicht möglich sind. Führende Plattformen wie Photonic Professional GT2 von Nanoscribe, NanoOne von UpNano und microFAB-3D von Microlight3D haben diese Technologie für die Spitzenforschung und für präzise industrielle Anwendungen erschlossen.
2. Projektions-Mikro-Stereolithographie (PµSL)
Bei der Projektions-Mikro-Stereolithographie werden mittels „Digital Light Processing“ (DLP) oder LCD-Technologien ultraviolette Muster auf ein photoreaktives Harz projiziert und mit einer Präzision zwischen 2 und 10 µm ausgehärtet. Diese Technik bietet ein ausgewogenes Verhältnis zwischen Auflösung, Geschwindigkeit und Skalierbarkeit und eignet sich daher für die schnelle Herstellung von Prototypen von Mikrogeräten, mikrooptischen Komponenten, Präzisionsverbindungen und medizinischen Komponenten. Boston Micro Fabrication (BMF) bietet spezielle Anlagen und individuelle Harze für industrielle Anwendungen, die auf dieser Technologie basieren.
3. Mikro-Lasersintern
Das Mikro-Lasersintern passt die LPBF-Verfahren an die Fertigung im Mikrobereich an. Mit Pulvern mit Partikelgrößen zwischen 5 und 10 µm und Laserspotgrößen von ca. 30 µm oder weniger (im Vergleich zu 15-45 µm Pulver und 70-100 µm Laserspotgrößen bei Standard-LBPF-Systemen), erzeugen diese Verfahren vollständig dichte, hochfeste Metallkomponenten. Passenden Anwendungen sidn zum Beispiel medizinische Präzisionsimplantate, Mikrobauteile für die Luft- und Raumfahrt und komplizierte Teile in der Elektronik. Unternehmen wie 3DMicroPrint, EOS, Trumpf und Additive Industries sind in diesem Bereich aktiv und bieten speziell entwickelte Maschinen und optimierte Materialien an.
4. Mikro-Tintenstrahl- und Aerosol-Jet-Druck
Beim Mikro-Tintenstrahl- und Aerosol-Jet-Druckverfahren werden winzige Tröpfchen oder Aerosolströme von Funktionsmaterialien, häufig leitfähige Tinten oder biokompatible Polymere, aufgebracht, um fein detaillierte 2,5D- (mit nur wenigen Schichten) und vielschichtige Strukturen zu erzeugen. Diese Verfahren eignen sich hervorragend für gedruckte Elektronik, flexible Schaltkreise, Sensoren, Wearables und biologische Anwendungen wie die Strukturierung von Zellen. Optomec und nScrypt bieten anpassbare Plattformen an, die sich für Elektronikfertigung oder Bioprinting eignen.
5. Femtosekunden-Laserbearbeitung in Glas
Technisch gesehen handelt es sich hierbei eigentlich im ein subtraktives Verfahren: Die Femtosekunden-Laserbearbeitung formt transparente Materialien von innen heraus und ermöglicht durch anschließendes chemisches Ätzen hochpräzise und komplexe 3D-Strukturen. Diese Technologie ist entscheidend für die Herstellung anspruchsvoller mikrofluidischer Geräte, optischer Wellenleiter und integrierter Optiken. Femtoprint, LightFab und 3D-Micromac bieten Lösungen für die Fertigungstechnologie, die als interessante Ergänzung zu echten additiven Verfahren gesehen werden kann.
6. Lithografiebasierte Metallfertigung (LMM)
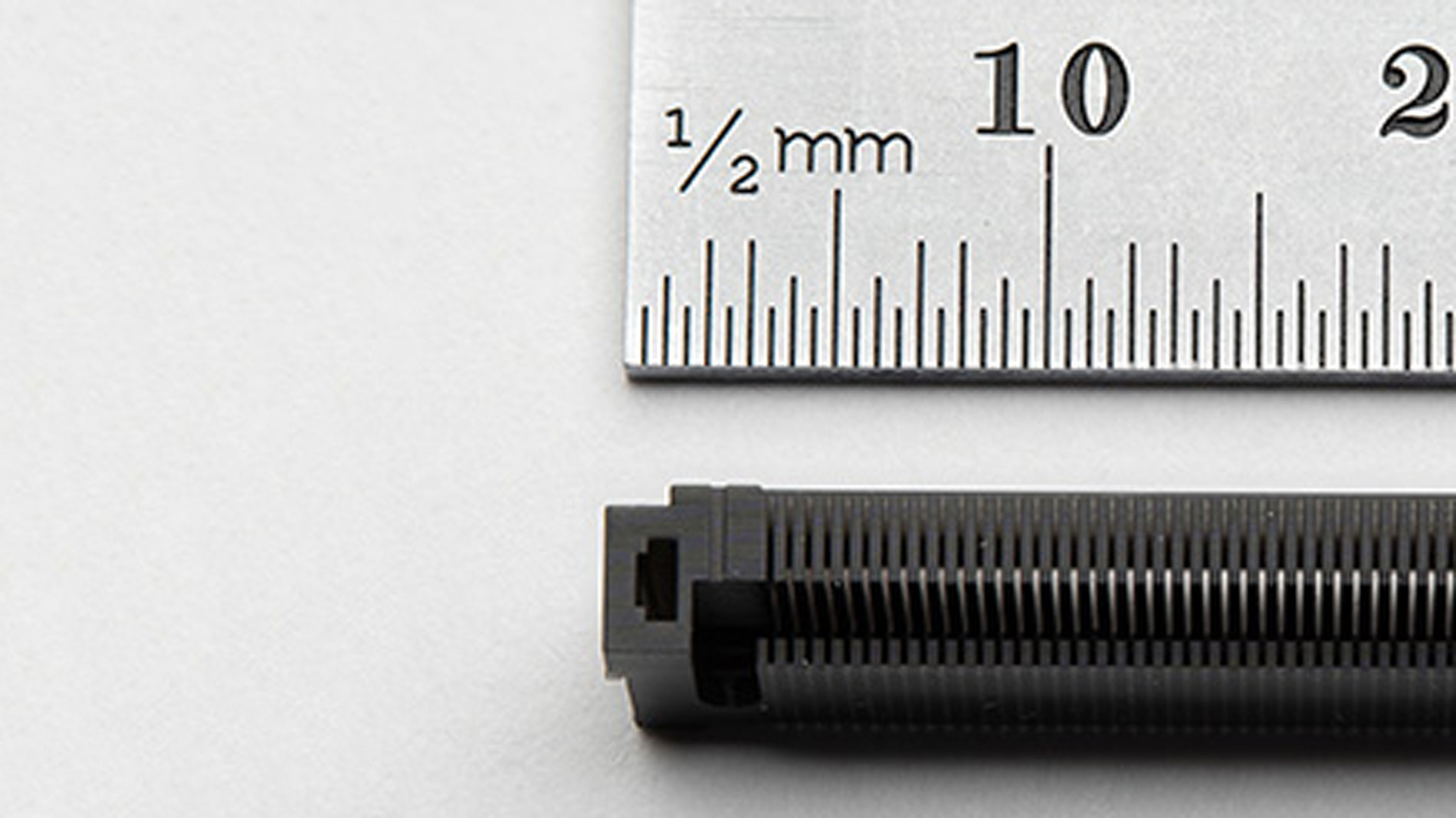
LMM basiert auf den Grundsätzen der Stereolithografie (SLA) und verwendet ein mit feinem Metallpulver vermischtes fotoreaktives Harz. Während des Druckvorgangs härtet eine Lichtquelle das Harz selektiv Schicht für Schicht aus, sodass ein „grünes Teil“ entsteht. Im Anschluss erfolgt das thermische Entbindern und Sintern, bei dem das Polymerbindemittel entfernt und die Metallpartikel zu einem dichten, vollmetallischen Bauteil verschmolzen werden – ähnlich wie bei einer Standard-Binder-Jetting-Technologie. Incus3D bietet Systeme auf der Grundlage dieser Technologie für eine Reihe von Metallen und Legierungen an.
7. Direkte elektrochemische Abscheidung (Electroplating AM)
Dieses Verfahren, das unter anderem Exaddon mit seinem CERES-System geprägt hat, ermöglicht eine düsenbasierte Präzisionsgalvanisierung im mikroskopischen Maßstab ohne Pulver oder Laser. Dieser Ansatz liefert außergewöhnlich präzise, vollmetallische Strukturen mit starken elektrischen und mechanischen Eigenschaften und ermöglicht wertvolle Anwendungen für Mikroelektronik, Mikrosensoren, Antennenstrukturen und Miniaturwärmetauscher.
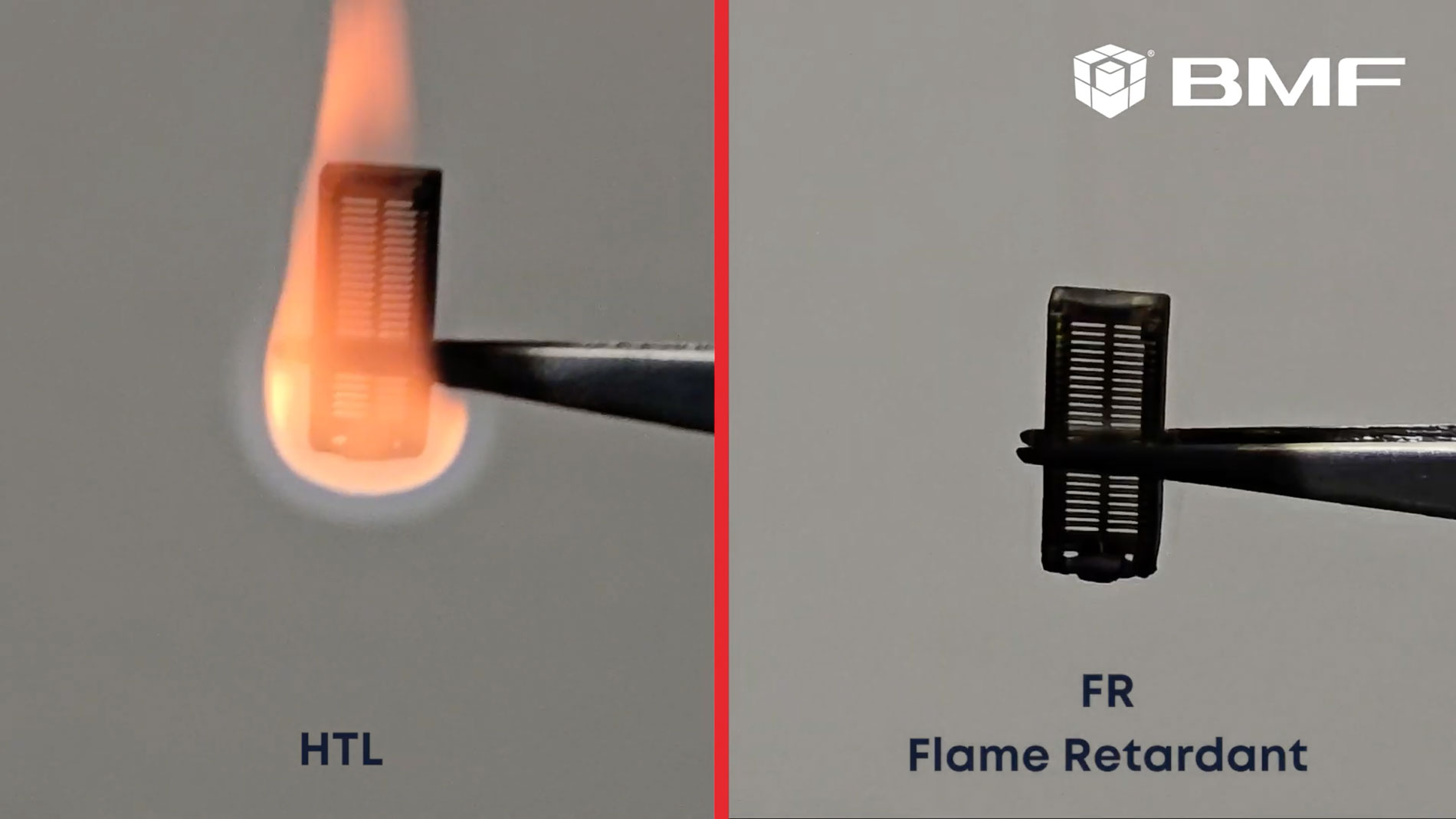
Die Mikrotechnologie ist ein Ökosystem
Die Materialien, die üblicherweise im 3D-Druck im Makromaßstab verwendet werden, zeigen im Mirko-3D-Druck ein anderes Verhalten. Faktoren sind dabei unter anderem das Verhältnis von Oberfläche zu Volumen, die Wärmeableitung und die Aushärtungsdynamik. Die veränderten mechanischen Eigenschaften im Mikro-3D-Druck erfordern eine spezielle Formulierung und strenge Validierung der Materialien.
Da die Elektronik immer kleiner wird, müssen auch die 3D-gedruckten Komponenten entsprechend kleiner werden. Die eingesetzten Materialien müssen auf die Mikroskala zugeschnitten sein, behalten aber in der Regel Eigenschaften wie Flammschutz oder Biokompatibilität bei. Flammhemmende Fotopolymere, die für elektronische Anschlüsse und Gehäuse im Mikrobereich benötigt werden, wurden beispielsweise von den Unternehmen BASF, Loctite und 3D Creations entwickelt. Biokompatible und bioresorbierbare Harze sind für medizinische und biotechnologische Anwendungen wichtig und ermöglichen die Herstellung präziser chirurgischer Führungen, Mikronadeln, Gewebegerüste und Implantate.
Maßstabsvergrößerung vom Prototyp zur Produktion
Trotz beeindruckender Fortschritte bleibt Mikro-AM komplex und erfordert eine geschickte Handhabung sowie ein hohes Maß an Fachkenntnis in der Anwendung. Die Systemhersteller versuchen, die Lücke zwischen „Plug-and-Play“ und der System-Leistung mit Anlagen zu schließen, die „out of the box“ funktionieren, aber auch fortgeschrittene Setups ermöglichen. Nichtsdestotrotz ist eine umfassende Zusammenarbeit mit den Anbietern von iterativem Design und ein strenges Benchmarking nach wie vor Pflicht – vor allem in stark regulierten Branchen wie der Medizintechnik.
Die Nachbearbeitung im Mikromaßstab ist mit besonderen Herausforderungen verbunden, insbesondere beim Entfernen von Stützmaterial, der Oberflächenbearbeitung und der Reinigung von innenliegenden Strukturen. Genau wie in der Makrowelt ist Design for Additive Manufacturing (DfAM) unerlässlich, um auch im Mikromaßstab das volle Potenzial des 3D-Drucks zu erschließen. So lässt sich die Komplexität der Nachbearbeitung verringern und die Druckgenauigkeit verbessern.
Auch auf der Formnext 2024 war der Mikro-3D-Druck mit Exponaten an zahlreichen Ständen ein wichtiges Thema. Bilder: Mesago / Marc Jacquemin
Anwendungen und zukünftige Entwicklungen
Der Mikro-3D-Druck gewinnt in zahlreichen Branchen zunehmend an Bedeutung:
- Gesundheitswesen: präzise Komponenten für minimalinvasive Chirurgie, Mikrofluidik für die Diagnostik, moderne, biokompatible Anwendungen
- Elektronik: schnelles, kundenspezifisches Prototyping von Steckern, Buchsen, flexiblen Schaltkreisen und Sensoren im Mikrobereich
- Optik: Herstellung komplexer optischer Wellenleiter, Linsen und mikrooptischer Elemente, die mit herkömmlichen Methoden bisher nicht realisierbar waren
- Biotechnologie: Mikrofluidische Geräte für „Lab-on-a-Chip“-Anwendungen, Zellmusterung und fortgeschrittene Biosensoren.
Die Zuverlässigkeit, Präzision und Skalierbarkeit der Mikro-AM dürfte angesichts der Anforderungen der Elektronik-, Medizin- und Optikindustrie weiter zunehmen. Wie in der „großen“ Industrie bringt der Übergang von der Prototypenfertigung zur Serienfertigung gleichzeitig Herausforderungen und Chancen mit sich – und das bei immer komplexeren und miniaturisierten Geräten. Kleinere Teile erfordern in der Regel engere Toleranzen, neuartige Materialien und hohe Erwartungen an die Leistung der AM-Systeme. Das macht den Mikro-3D-Druck zu einer immer wichtigeren Technologie in der Spitzenforschung und Produktentwicklung. Je kleiner das Teil, desto größer die Chance.