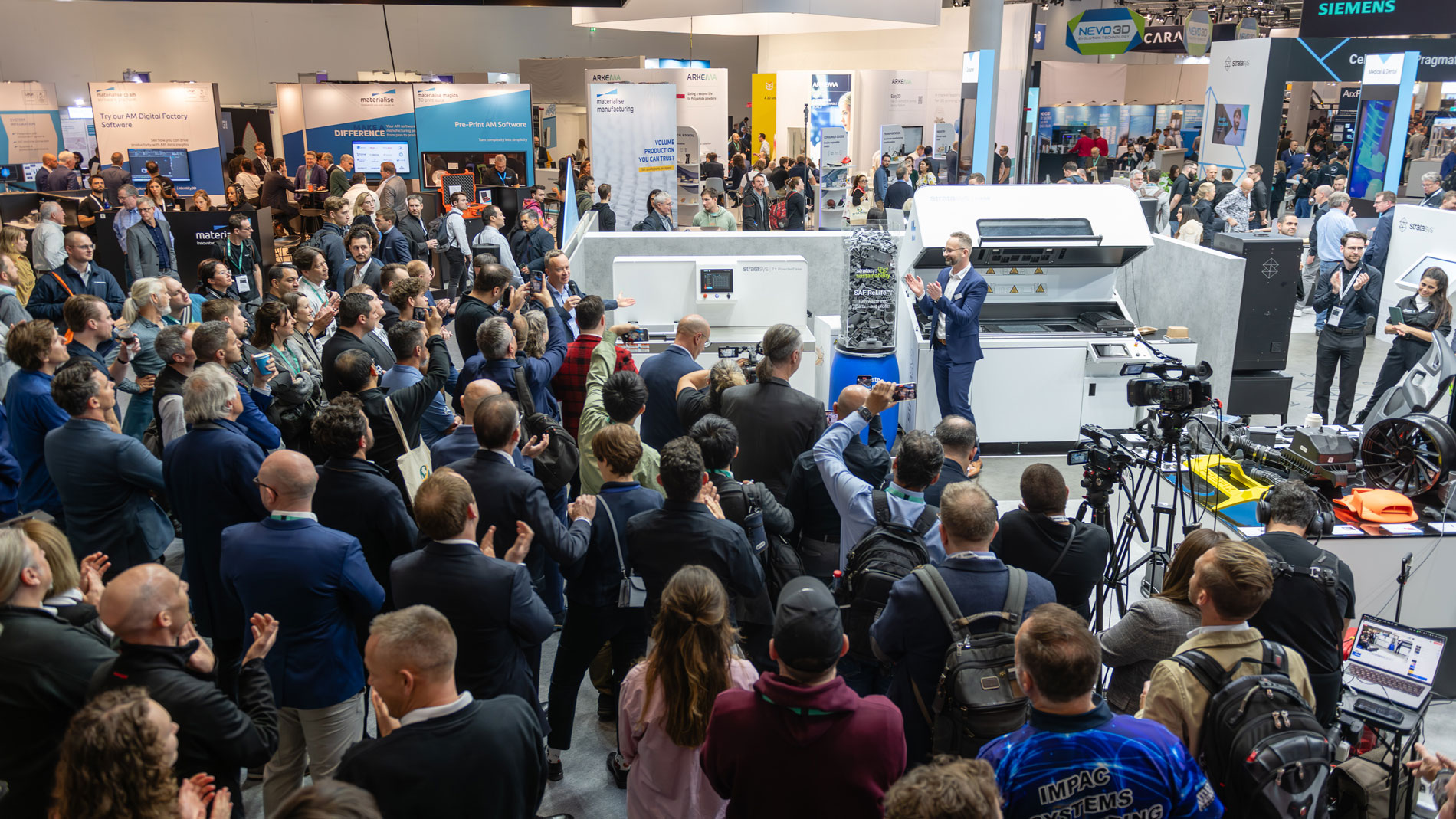
The demand for lower production costs is as old as additive manufacturing itself, and of course Formnext 2024 was also about producing 3D-printed components more cost-effectively. Progress was made in all exhibition halls and along the entire process chain, ranging from improved exposure strategies and innovations in materials and post-processing to improved software solutions that accelerate the design process or reduce waste. The highlights once again included the presentations of new hardware systems. The large number of visitors in attendance showed just how great the industry's interest in greater efficiency is.
There was a packed floor at the launch of the EOS PE Next, for example. With this new SLS 3D printer, EOS promises up to 50 percent higher productivity, exceptional part quality, and support for biocompatible materials.
The Stratasys booth was no less busy with the presentation of the new PowderEase T1 system, which the company launched together with the Rösler brand AM Solutions – 3D Post Processing Technology. Designed for the Stratasys H350 SAF powder bed printer, the three-in-one post-processing solution is said to save 50 minutes per print while reducing powder waste. The PowderEase T1 is manufactured at AM Solutions' German site.
Caracol picked up on the important trade fair trend in the large-format additive manufacturing (LFAM) of metals with its new Vipra AM system, which the company presented with some fanfare and an accompanying panel discussion. The system uses wire-arc additive manufacturing (WAAM) technology and, according to Caracol, is suitable for large-format applications in the railroad, automotive, shipbuilding, aircraft construction, and furniture manufacturing sectors. It also combines robot-assisted AM technology with automation.