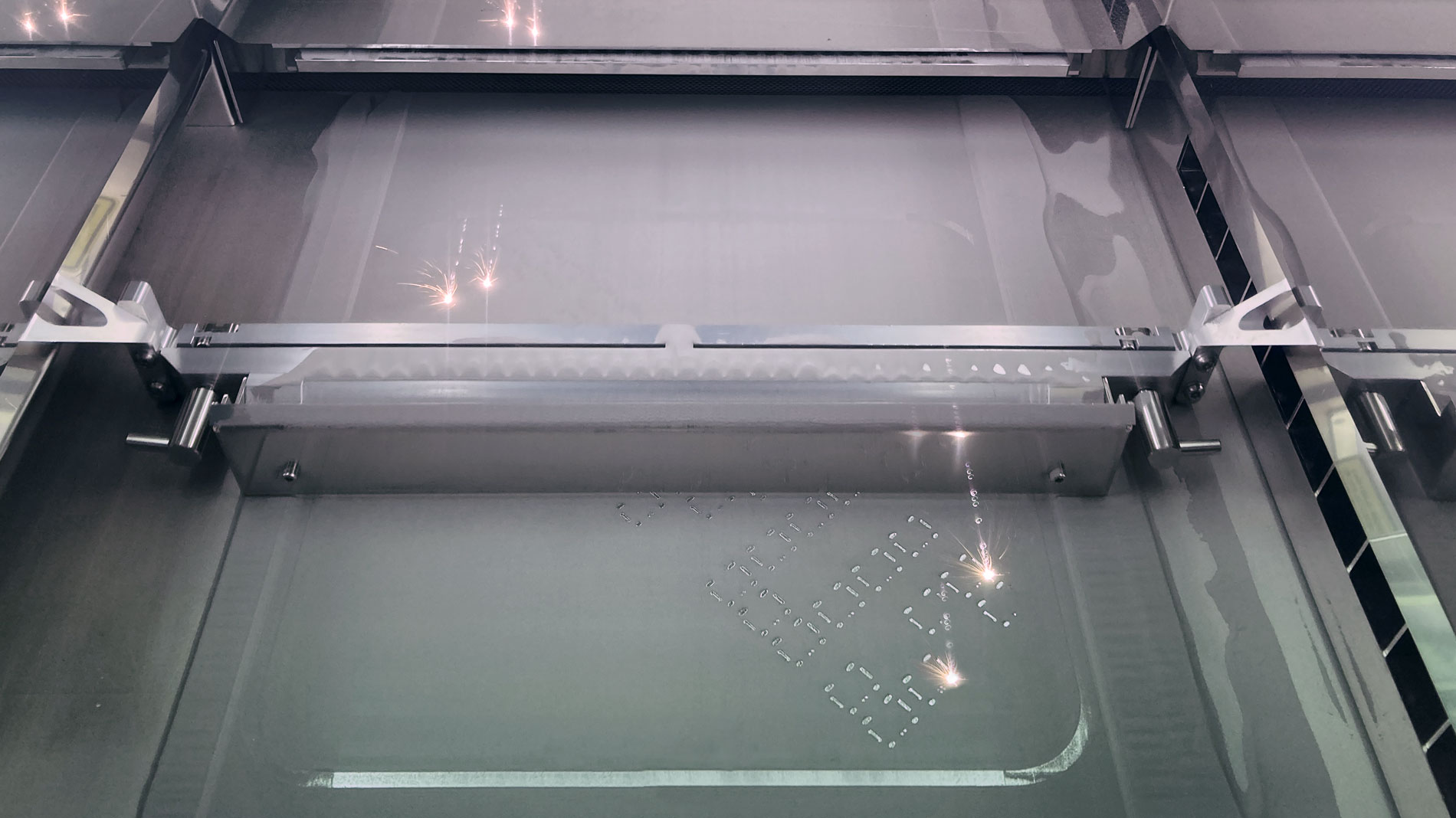
Reducing cost per part is crucial for additive manufacturing (AM) adoption. The main cost factor is the time spent building the part. System suppliers can increase machine productivity by increasing machine size or laser power, but these options raise costs for the end user.
However, Renishaw has found a way to lower cost per part without driving up entry barriers.
Renishaw's patented TEMPUS technology offers a solution by allowing the laser to fire while the recoater moves, saving up to nine seconds per layer. This innovation significantly reduces build times without compromising quality. Higher time savings are typically achieved when building parts with thin, vertical features, but all part geometries can experience some productivity benefits.
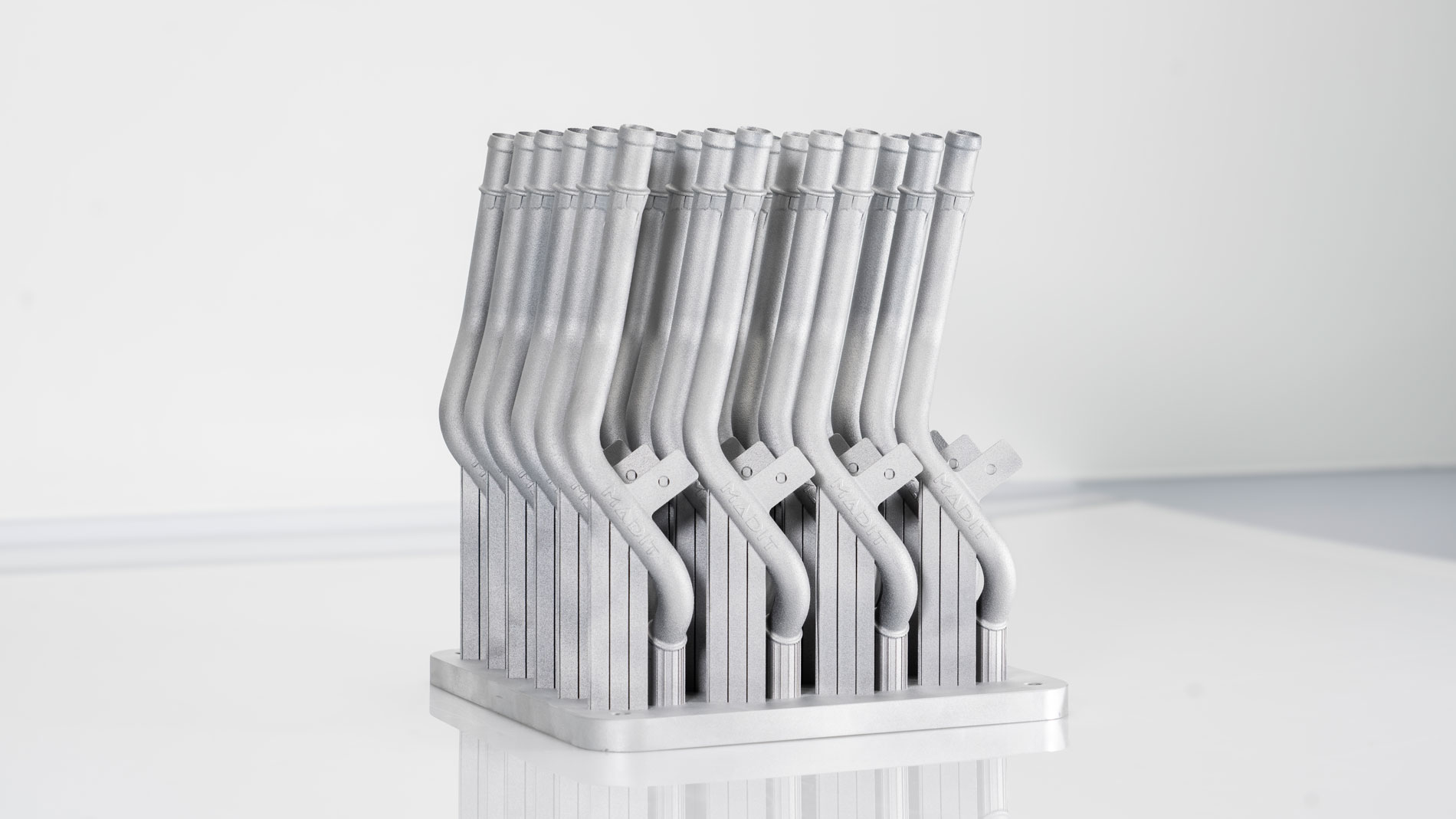
For example, MADIT, a specialist in the use of metal additive manufacturing for industrial production, has trialled the new TEMPUS technology and achieved convincing results, reducing the build times of parts by between 25 and 50 per cent without compromising on quality. The time saving means MADIT has doubled the productivity.
With productivity improvements lowering the entry barrier for metal AM, businesses can now both expand the use of AM into novel applications more easily, and upscale existing processes. Those already using AM can experience better margins, opening up the opportunity to invest in more equipment and to grow.
MORE INFORMATION:
Renishaw plc.
New Mills, Wotton-under-Edge, Glos, GL12 8JR, UK
+44 (0) 1453 524524 | uk@renishaw.com