13 October 2022, Source: 3dpbm
In fact, the industries may drive one another: from faster development to ASSBs, AM technologies will be a key enabler in the electrification of mobility.
The primary advantage of AM is its ability to offer better value in low-volume production with shorter time-to-market. This is a key advantage to all ensuing technologies and new products challenging the established status quo. The space industry is a clear example, with dozens of new space startups able to bring products to market because AM has eliminated the need for scale economies. Something similar can happen in the EV segment, with new startups able to enter the market and large companies more open to experimentation and innovation.
With lower demand and more customized products, the value of using 3D printing increases. With polymers, AM parts can be competitive up to batches of 100,000 units. That applies mainly to small, intricate components, but LFAM technologies are becoming more competitive, especially for small batches of parts needed when a new product is first introduced to the market. AM is therefore ideal for startups and new projects.
As EV volumes increase, so will the productivity of AM machines. This is certainly true today for polymer and composite parts, but soon it could become even more viable for metal parts. At the same time, it is likely that EVs will use more composite and polymer parts for metal replacement than current ICE vehicles.
Fast prototype iterations via increasingly accessible extrusion, stereolithography and laser sintering technologies—including full-size concepts via LFAM technologies such as Massivit’s and Ingersoll Masterprint’s—and custom tooling (including very large composite tools) are both key factors making new vehicle development faster and more cost-effective.
Another element where AM could help accelerate the EV industry is digital warehouses and on-demand spare part production. Production can be distributed to any location with digital manufacturing systems in place by merely sending a file, enabling a more efficient and sustainable supply chain. Combined with the simplified production process for EVs, with many fewer moving parts overall, this could lead to local micro EV factories. In addition, as many new players in the electric vehicle scene don’t have long-standing supply chain loyalties and conventions, they are likely to be more open to adopting a digital supply chain dynamic.
The cost advantage of 3D printing should be quantified by looking at the entire value structure around it, but there are some parts in particular where these benefits may be more evident. Let’s take a look at them.
EV car body parts
AM potential:
Medium term and accelerating, targeting 2–3% of EV market penetration by 2030
EV firm Local Motors was the first to demonstrate the ability to 3D print entire car bodies using LFAM composite 3D printing technologies. The company shut down, failing to successfully enter the competitive and challenging autonomous vehicle market, but AM offered the company the best chance possible for succeeding.
After developing the first fully 3D printed car bodies (the Strati and its successors) starting in 2014, Local Motors followed up with the Olli smart EV shuttle, which also integrated an entirely 3D printed body. The team 3D printed Olli’s upper and lower structures from recyclable polycarbonate material from SABIC (LNP THERMOCOMP) using LSAM large-format extrusion 3D printing technology from Thermwood.
Local Motors shutting down was due more to a lack of demand for AVs than an inability to meet that demand in a cost-effective way: installing its vehicles in 24 sites around the world was not enough to support and finance its continued activity. Yet Local Motors has been responsible for a huge number of AM industry firsts, including the use of LFAM technologies (from Cincinnati Inc then Thermwood) and LFAM composite material from SABIC to produce large automotive final parts. If anything, Local Motors should have been truer to its nature as a 3D printing company, continuing to emphasize and develop this production method and targeting other LFAM applications along with the Olli to expand its business.
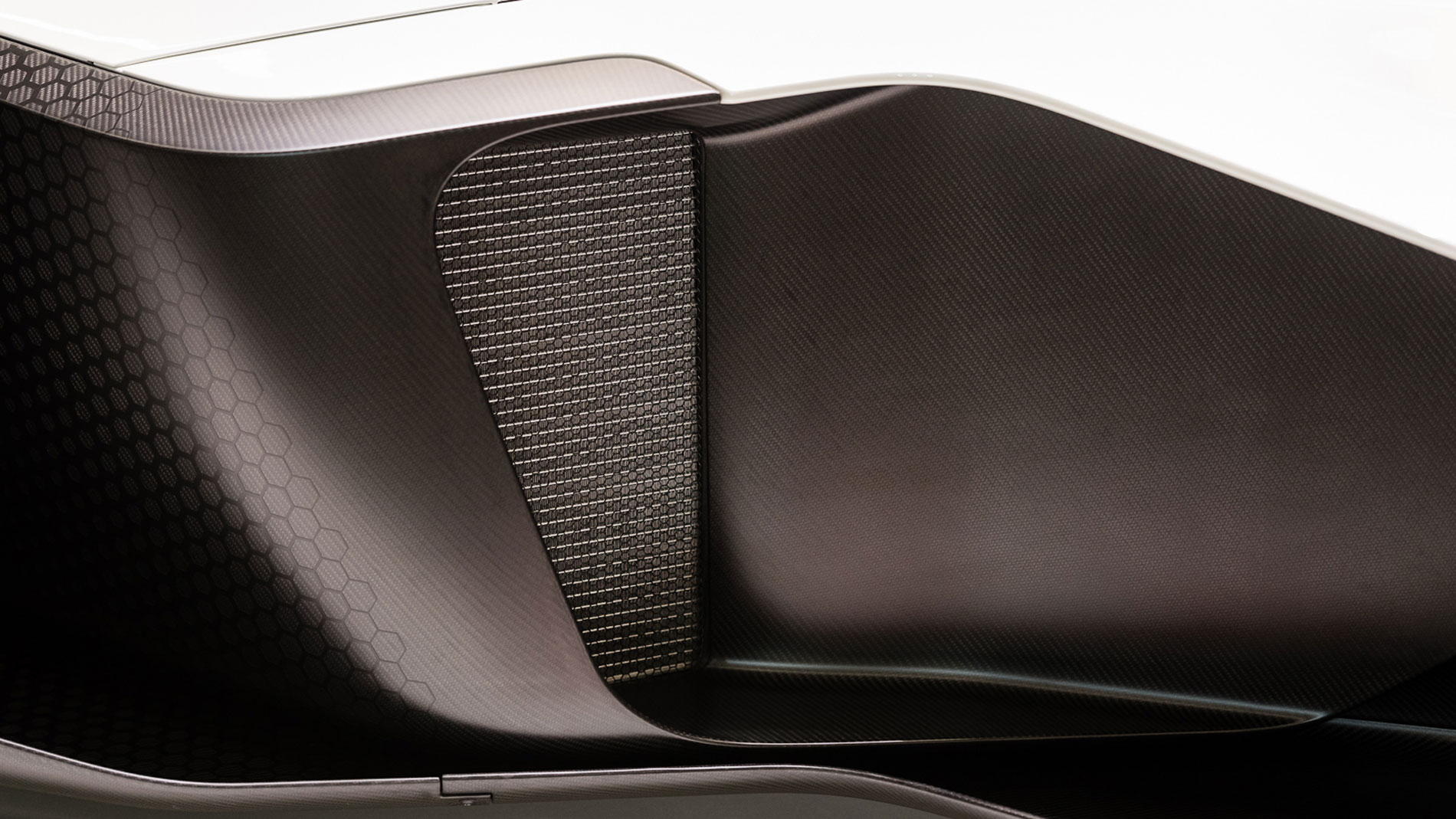
While AM production of EV body components has not yet made it to mass production, other companies are following in the footsteps of Local Motors—or at least intend to.
One of them is XEV, an Italian-Chinese company that developed and commercially launched the YOYO, its first fully electric city car (it can be driven from the age of 16 with a B1 license). The company uses the BigRep PRO LFA 3D printer to print customizable car body parts, although its goal is to use AM for a lot more elements of the car’s body. XEV’s 3D printing production line intends to virtually eliminate the need for limited and resource-intensive tooling, resulting in a flexible and efficient manufacturing process. This technology allows for fewer body components, faster technical updates and significantly reduced production cycles. It also dramatically reduces production costs, meaning the savings can be passed on to customers, with the result that the YOYO is available for just over €10,000 in Italy (with EV incentives). Thanks to a pre-designed and standardized chassis, the 3D printed parts can be modified and changed with significantly less re-engineering. For the final surface quality, the 3D printed parts also go through an automated robotic milling process to guarantee a very smooth surface.
These are just two of the most evident examples of AM adoption in EV body parts production. Other more conceptual projects have involved both large automakers and small, innovative startups. In general, the larger companies, such as FCA and MINI, are more conservatively looking at AM for smaller parts and customizations of their upcoming EVs, while some innovative startups are looking at modular elements to increase functionality. For example, Swiss automobile manufacturer Rinspeed has proposed a unique vision for the future of cars, driven by modularity and efficiency: its MetroSnap concept is an electric and modular vehicle with 3D printed parts that can fulfill multiple functions. The vehicle is based on the company’s innovative concept in which the chassis and body are separated, enabling the body of the vehicle to be swapped out. The patent-pending swappable system enables users to use the electric vehicle for multiple functions, whether it be transporting people or goods.
AM applications in the production of car body parts for EVs started out as a long-term opportunity, but widespread uptake is rapidly approaching as EVs continue to grow in adoption and provide new manufacturing opportunities. Because EVs are expected to have fewer and fewer parts in the future, 3D printing will have a more significant penetration in the EV car body parts production market than in traditional vehicles.
More specifically, lightweighting—one of the primary advantages of implementing AM—is fundamentally important for EV development, as any weight saved or improved distribution of weight helps prolong battery life. 3D printing can help to develop new part geometries that can make the EV lighter without sacrificing safety. As demonstrated in aerospace part development, redesigning parts for AM with parametrically optimized geometries can eliminate material and reduce the weight of the vehicle while maintaining the structural integrity needed for safety. AM also offers the ability to eliminate tools and condense several parts into one. This can be particularly beneficial to companies developing new designs or new startups looking to enter the market.
EV auxiliary electrical systems and electronics
AM potential
Short term and moderate at up to 2–3% market penetration by 2030
This market includes audio/video devices, cameras, low-voltage electrical supply systems, gauges and meters, ignition system components, lighting and signaling systems, as well as several different types of sensors, electrical switches, wiring harnesses and, of course, electronic enclosures that will need to be integrated into the EV’s structure. In terms of applications, AM is already used significantly in the production of custom electronic enclosures and switches. Other key applications include the use of copper, in both metal PBF and bound metal/binder jetting technologies.
AM part production firms and AM factories have demonstrated the cost-efficiency of 3D printing electronic enclosures (and related products). An advantage of high-volume 3D printing is its ability to produce custom parts at scale without the cost of molds. This freedom allows for products to evolve during production and reduces inventory requirements. Electronic enclosures cannot accommodate the millions of PCB designs that are used in cars, which feature more and more electronic elements—a trend that will increase by several orders of magnitude with EVs and with increased demand for customization. With 3D printing, enclosures can be produced on demand, as the parts are sold, with no molding cost.
Nano Dimension has been specializing in the development and production of electronic components via 3D printing. With the rise in demand for Smart Mobility and internet-connected devices (IoT), polymer 3D printing companies are searching for new ways of developing innovative and functional devices, with applications that offer efficiency, improved performance and affordability. Nano Dimension’s DragonFly System is an ideal technology to accelerate in-house electronics development and increase the design freedom to develop new products quickly and cost-effectively.
Additive electronics enable fast prototyping and manufacturing of conductive components, encapsulated sensors and smart surfaces, all of which can offer car makers the flexibility of printing an entire circuit board or just part of a connector, as well as the ability to develop the RF and digital sections of the board in parallel to test concepts on the fly. All of this can lead to the development of customized electronics, including embedded sensors, conductive geometries, molded connected devices, PCBs and more, which can become the backbone to innovative automotive components that will enhance the driver experience.
Similarly, Rogers Corporation worked with Fortify3D to develop the Radix 3D Printable Dielectrics family of products, with the first available material featuring a dielectric constant of 2.8 and low loss characteristics at microwave frequencies. These printable dielectric materials give radio frequency (RF) designers unprecedented design freedom in creating new components, such as automotive radars for automotive braking and collision avoidance, eliminating the need to consider typical manufacturing design constraints.
The application of AM in the production of electronic components—especially enclosures and switches—is expected to increase rapidly to serial production levels, as combustion engines become more compact and EVs become more streamlined. Polymer 3D printing with high-temperature materials already enables the production of several under-the-hood components. With EVs and, in general, smart vehicles, adoption of AM is expected to be even more significant, as temperatures become less of an issue (outside of batteries) and the need for complex electronic parts increases.
Electrified powertrain parts and AM applications
Grandview Research estimated the global electric powertrain market size to be around $20 billion in 2020, growing at a compound annual growth rate of 13.6% from 2020 to 2027 to nearly $40 billion by 2027.
Several powertrain and chassis parts are common to both vehicles with internal combustion engines and EVs, although they may take different forms. Several of these have been 3D printed in some form, starting with the high-profile Czinger 21C hybrid supercar project, which integrates a number of 3D printed parts. Czinger uses additive manufacturing methods to create performance-engineered components, including the chassis derived from the project’s predecessor, the Blade supercar, which was produced using SLM Solutions’ metal PBF technology.
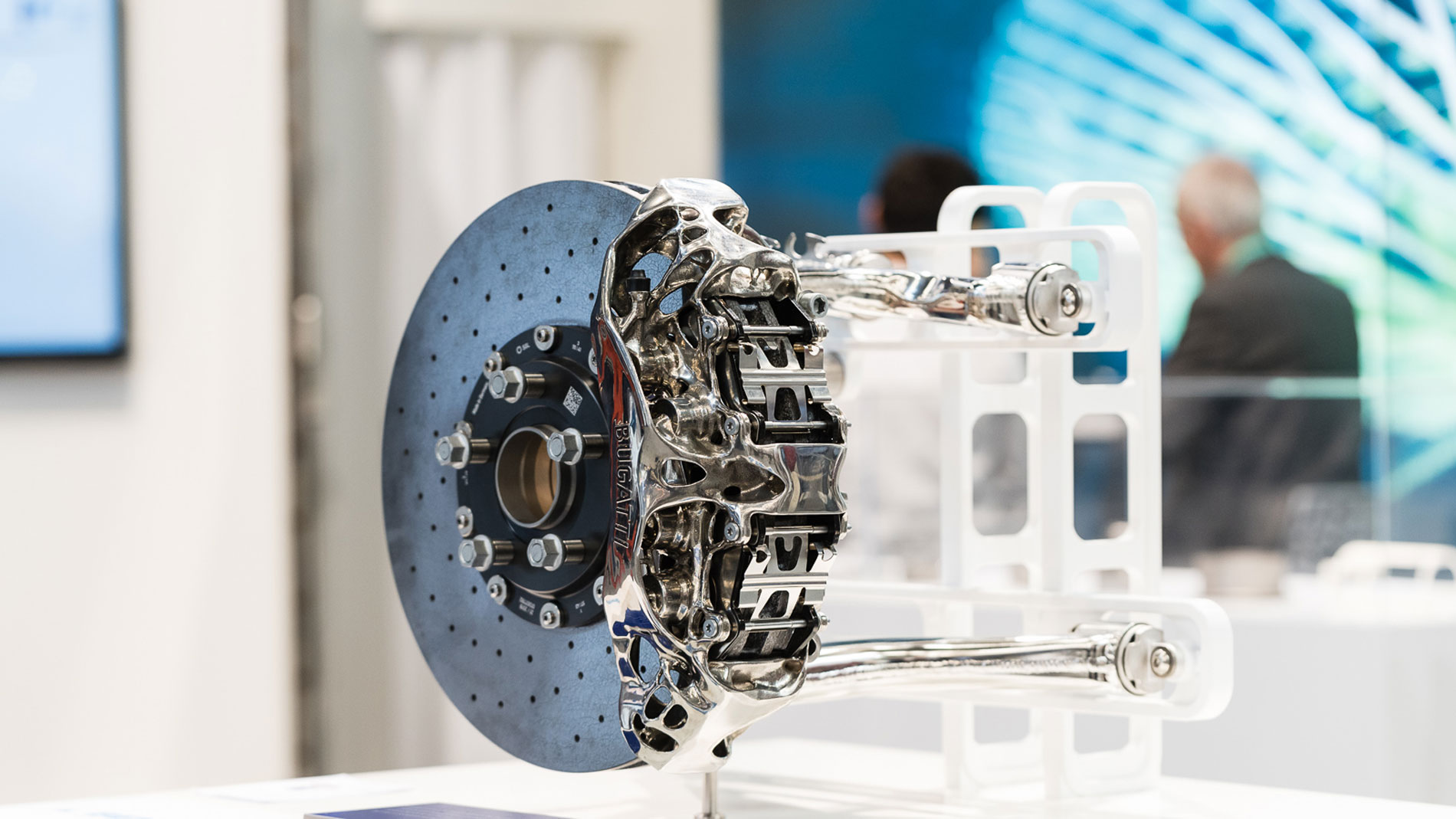
Bugatti is another major combustion-engine supercar manufacturer that is moving closer to electrification after the acquisition by Rimac. Bugatti has used AM on a number of parts, including its revolutionary titanium 3D printed brake calipers. More recently, the company has produced hybrid components, such as the 0.5-meter-long auxiliary drive shaft, combining carbon fibers with a 3D printed titanium end fitting to roughly halve the weight to 1.5 kilograms, improving performance by reducing the rotating masses. Rimac has also been using 3D printing since turning to Materialise in 2011 to produce interior parts for its Concept_One, one of the world’s first electric hypercars. When it comes to hypercars, Lamborghini is another major brand that is looking at both electrification and 3D printing. The Sant’Agata Bolognese company has been working with Carbon on several end-use parts (although not yet for chassis or powertrain) for both its sports cars and its top-selling Urus SUV.
EVs use the electricity saved in the battery to cycle the motor and generate the power necessary for driving. As such, EVs have no need for the engine and transmission, two of the most crucial components for internal combustion vehicles. Instead, EVs carry several components for electric power: the motor, the battery, the on-board charger and the Electric Power Control Unit (EPCU). All are essential components to achieve the conversion of the battery’s electricity into kinetic force.
The motor is also an electric generator: it converts kinetic energy generated while in neutral gear (i.e. while the car is going downhill) into electric energy saved to the battery. The same energy-saving idea applies when the car is slowing down.
In electric motors, a particularly interesting focus area for AM is copper. German firm Additive Drives has presented promising applications cases. One, in cooperation with the Racetech Racing Team eV of TU Freiberg, involves 3D printed single coils used on the racing engine. In another project, copper 3D printed hairpin windings reduced the time required for the development and production of an electric traction motor prototype to one month. In addition, direct production of individual lots was achieved for Dresden-based pedelec (e-bike) manufacturer Binova: using 3D printed individual coils, Binova produced several different types of electric bikes with an unconventional electric motor design and no tool adjustments. More recently, Porsche and SLM Solutions revealed a project centered on manufacturing a complete housing for an electric drive using 3D printing. The 3D printed E-Drive housing on the engine-gearbox unit produced using the additive laser fusion process passed all the quality and stress tests. In the future, this may become a viable production method.
In EVs, the reducer is a kind of transmission that serves to effectively convey the motor’s power to the wheels. The motor has a far higher RPM than that of an internal combustion engine, so with the reduced RPM, the EV powertrain can take advantage of the resulting higher torque. This part is a fairly complex metallic component that could, in the future, be optimized with AM for fast production, improved performance and weight reduction. The Electric Power Control Unit is another complex enclosure that could benefit from AM processes. It includes the inverter (which converts the battery’s DC into AC and is used to control the motor speed), the low-voltage DC-DC Converter, which supplies the vehicle’s various electronic systems) and the Vehicle Control Unit. The VCU oversees nearly all the vehicle’s power control mechanisms, including the motor control, regenerative braking control, A/C load management and power supply for the electronic systems.
EV batteries
AM potential
Medium term to long term and very significant at above 5% market penetration by 2030
In 2019, the global electric vehicle battery market reached a size of almost $50 billion. Projections forecast a market increase by a compound annual growth rate of 14.1% between 2019 and 2030, amounting to over $212 billion in 2030, as data from NMSC shows.
The battery stores electrical energy and is the equivalent of a fuel tank in an internal combustion engine: the higher the capacity, the higher the driving distance. However, the battery’s size and weight also have large implications on vehicle performance. A larger and heavier battery takes away from cabin/storage space and worsens the energy efficiency and fuel economy. The best way to optimize performance, then, is to maximize the battery’s energy density—that is, having a small, lightweight battery that stores as much electric energy as possible.
Batteries will be a particularly interesting (albeit tricky) area for AM in the rapidly approaching future. Several efforts have been made to produce batteries using different 3D printing technologies, with both polymer and ceramic materials. Because batteries can take many different shapes and sizes for improved efficiency, AM could prove instrumental for testing—and eventually manufacturing—several new design iterations. The batteries used in EVs today are basically rows of hundreds of small-sized batteries fastened together to increase capacity. The Tesla 85kWh pack, for instance, is made up of 7,104 cells roughly the size of AAs. With 3D printing, the individual cells don’t have to be manufactured and assembled: the module can be designed and printed in the desired overall shape. AM can also make a difference in the structure of the electrodes of a battery: porous electrodes increase energy density, and AM is ideally suited to build electrode materials into lattice shapes that have more exposed surface area for the chemical reactions to take place, resulting in a more efficient battery.
Swiss firm Blackstone Resources has recently achieved a series of important milestones for its proprietary 3D printing technology to print lithium-ion solid-state batteries (SSBs). Blackstone’s 3D printing process claims to offer substantial advantages over conventional battery cell designs that use liquid electrolytes. These include significantly lower costs, a higher level of production flexibility regarding the cell format and a 20% increase in energy density. Moreover, by using this technology, the number of materials that do not store energy (such as copper and aluminum) could be reduced by up to 10%. The Swiss company also developed a workflow to mass-produce these batteries in 2021 in any shape or form using proprietary battery printing technology.
Blackstone is not the only company developing 3D printed SSBs. In the US, Sakuú Corporation (formerly Keracell) has raised $62 million to finance development of an automated, multi-material, multi-process AM technology to produce 3D printed SSBs.
In the 2020–21 period, Sakuú increased the energy density of its first-generation battery from 40Wh/l to 600Wh/l, while increasing the cell layer count from 1 to 30 and growing cell capacity from 2.3mAh to 3000mAh, setting a new benchmark in the race for SSBs for EVs. These batteries will be very competitive with current Li-Ion batteries in terms of energy density while bringing the inherent safety benefits of solid-state technology. The company reported that it is on the path to full commercialization of its first-generation SSBs, targeting high volume production in the second half of 2022. Last year, Sakuú also printed the world’s first fully ceramic SSB battery as an early demonstration of its second-generation ASSB (All-Solid State Battery).
In electric vehicle powertrains, the use of additive manufacturing is particularly effective for part size reduction, leading to weight reduction and performance improvements. Part reduction, in turn, enables greater mileage. However, the actual penetration of additive manufacturing in EVs—beyond applications shared with combustion engine powertrains, such as chassis, brakes and fluid flow applications—is highly dependent on the ability to implement additive manufacturing in serial battery manufacturing. Relevant efforts in this area are already underway, but we are still a few years away from it becoming a consolidated business opportunity.
*This article was originally published in 3dpbm’s AM Focus Automotive AM eBook 2022. Published monthly, all 3dpbm’s AM Focus eBooks are available for free and include an analysis of the reference vertical segment.
FURTHER INFORMATION:
Tags
- Automotive
- Sustainability