13.10.2022, Quelle: 3dpbm
Die beiden Branchen können sich sogar gegenseitig unterstützen: Von den kürzeren Entwicklungszeiten bis hin zu den neuen ASSBs werden additive Fertigungstechnologien eine Schlüsselrolle bei der Elektrifizierung der Mobilität spielen.
Der Hauptvorteil der additiven Fertigung (Additive Manufacturing – AM) liegt darin, dass sie bei der Kleinserienproduktion ein besseres Preis-Leistungs-Verhältnis und eine kürzere Markteinführungszeit bietet. Dies ist ein entscheidender Vorteil für alle Folgetechnologien und neuen Produkte, die den etablierten Status quo herausfordern. Die Raumfahrtindustrie ist ein gutes Beispiel: Dutzende neuer Start-ups in dieser Branche können neue Produkte auf den Markt bringen, weil durch die additive Fertigung keine Skalenvorteile mehr erforderlich sind. Eine ähnliche Entwicklung ist auch im Elektrofahrzeug-Segment (Electric Vehicle – EV) möglich, wo neue Start-ups dem Markt beitreten können und große Unternehmen offener für Experimente und Innovationen sind.
Angesichts geringerer Nachfrage und einer Zunahme individuell angepasster Produkte wird der Einsatz von 3D-Druckverfahren immer lohnender. Mit Polymerwerkstoffen können AM-gefertigte Teile bis zu einer Chargengröße von 100.000 Stück wettbewerbsfähig sein. Das gilt vor allem für kleine, komplexe Bauteile, aber auch großformatige LFAM-Technologien (Large Format Additive Manufacturing) werden immer wettbewerbsfähiger – vor allem bei kleineren Stückzahlen, wie sie bei der Markteinführung eines neuen Produkts benötigt werden. Die additive Fertigung eignet sich daher ideal für Start-ups und neue Projekte.
Mit der zunehmenden Verbreitung von E-Fahrzeugen wird sich auch die Produktivität der Maschinen für die additive Fertigung erhöhen. Dies ist bei Kunststoff- und Verbundwerkstoffteilen heute bereits der Fall, könnte aber schon bald auch bei Metallteilen noch mehr an Bedeutung gewinnen. Auch werden bei Elektrofahrzeugen voraussichtlich mehr Verbundwerkstoff- und Polymerbauteile als Ersatz für Metallkomponenten zum Einsatz kommen als bei den aktuellen Verbrennerfahrzeugen.
Schnelle Prototyp-Iterationen durch immer leichter zugängliche Extrusions-, Stereolithografie- und Lasersintertechnologien – einschließlich Konzeptstudien in Originalgröße durch Einsatz von LFAM-Technologien wie von Massivit und Ingersoll Masterprint – sowie individuell angepasste Werkzeuge (einschließlich sehr großer Verbundwerkzeuge) – dies sind die beiden Schlüsselfaktoren, die die Entwicklung neuer Fahrzeuge schneller und kostengünstiger werden lassen.
Ein weiterer Bereich, in dem die additive Fertigung die Elektromobilität unterstützen könnte, sind digitale Lager sowie die Herstellung von Ersatzteilen auf Abruf. Die Produktion kann auf beliebige Orte mit digitalen Fertigungssystemen verteilt werden, indem einfach eine Datei versandt wird; so werden effizientere und nachhaltigere Lieferketten möglich. In Verbindung mit dem einfacheren Produktionsprozess für Elektrofahrzeuge, die insgesamt eine deutlich kleinere Zahl beweglicher Teile aufweisen, könnte dies die Einrichtung lokaler Mikrofabriken für Elektrofahrzeuge ermöglichen. Da viele neue Akteure in der Elektrofahrzeugszene in ihren Lieferketten keine langjährigen Bindungen und Traditionen aufgebaut haben, dürften sie der Dynamik einer digitalen Lieferkette offener gegenüberstehen.
Um den Kostenvorteil des 3D-Drucks quantifizieren zu können, sollte die gesamte ihn umgebende Wertschöpfungsstruktur betrachtet werden; es gibt jedoch einige Bereiche, in denen diese Vorteile besonders deutlich zutage treten. Schauen wir sie uns an.
Karosserieteile für Elektrofahrzeuge
Potenzial für die additive Fertigung:
mittelfristig und mit zunehmender Tendenz, mit dem Ziel einer Marktdurchdringung von 2–3 % bis 2030
Der Elektrofahrzeugbauer Local Motors hat als erstes Unternehmen gezeigt, dass sich mit LFAM-Verbundwerkstoff-3D-Druck ganze Fahrzeugkarosserien herstellen lassen. Das Unternehmen musste seinen Betrieb mittlerweile einstellen, da es ihm nicht gelingen konnte, erfolgreich in den wettbewerbsintensiven und anspruchsvollen Markt für autonome Fahrzeuge einzusteigen; dabei hatte die additive Fertigung (AM) dem Unternehmen die bestmöglichen Erfolgschancen geboten.
Nachdem Local Motors ab 2014 die ersten Fahrzeuge mit vollständig 3D-gedruckter Karosserie entwickelt hatte (den Strati und seine Nachfolgemodelle), folgte der intelligente Elektro-Shuttlebus Olli, dessen Karosserie ebenfalls vollständig im 3D-Druck hergestellt wurde. Das Team druckte die obere und untere Struktur des Olli aus recyclingfähigem Polycarbonat von SABIC (LNP THERMOCOMP) und setzte dabei die LSAM-Großformat-Extrusions-3D-Drucktechnologie von Thermwood ein.
Dass Local Motors den Betrieb einstellen musste, lag eher an der mangelnden Nachfrage nach autonomen Fahrzeugen als daran, dass man diese Nachfrage nicht auf kosteneffiziente Weise hätte decken können: Die Einführung der Fahrzeuge an 24 Standorten weltweit reichte nicht aus, um die weitere Geschäftstätigkeit zu tragen und zu finanzieren. Auf Local Motors gehen jedoch eine Vielzahl von Premieren in der AM-Branche zurück, unter anderem der Einsatz von LFAM-Technologien (zunächst von Cincinnati Inc., dann Thermwood) sowie von LFAM-Verbundwerkstoffen von SABIC für die Herstellung großer Automobilkomponenten. Vielleicht hätte Local Motors sich stärker auf seine Kernkompetenz als 3D-Druckunternehmen fokussieren, diese Produktionsmethode weiter in den Vordergrund stellen und neben dem Olli auch andere LFAM-Anwendungen ins Visier nehmen sollen, um sein Geschäft auszubauen.
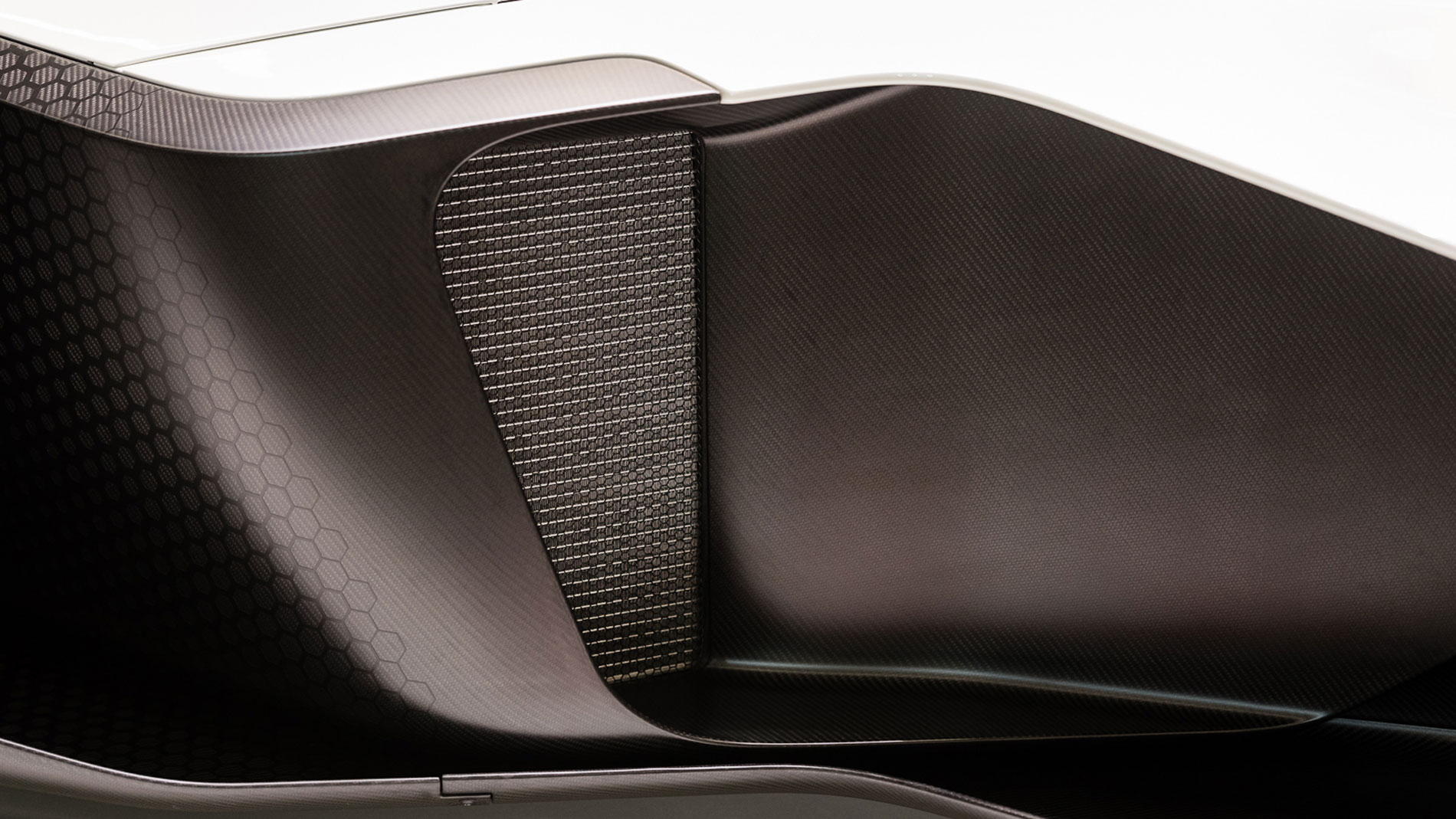
Die additive Fertigung von Karosserieteilen für Elektrofahrzeuge ist zwar noch nicht in der Massenproduktion angekommen, aber andere Unternehmen treten in die Fußstapfen von Local Motors – oder haben dies zumindest vor.
Dazu gehört beispielsweise XEV: ein italienisch-chinesisches Unternehmen, das mit dem YOYO sein erstes vollelektrisches Stadtauto entwickelt und auf den Markt gebracht hat (das Modell darf ab 16 Jahren mit einem Führerschein der Klasse B1 gefahren werden). Das Unternehmen verwendet den LFA-3D-Drucker BigRep PRO zur Herstellung individuell anpassbarer Karosserieteile, möchte künftig aber noch wesentlich mehr Elemente der Fahrzeugkarosserie additiv fertigen. Die 3D-Druck-Produktionslinie von XEV soll die nur begrenzt einsetzbaren, ressourcenintensiven Werkzeuge praktisch eliminieren und so einen flexiblen und effizienten Herstellungsprozess möglich machen. Diese Technologie ermöglicht weniger Karosserieteile, schnellere technische Updates und deutlich kürzere Produktionszyklen. Außerdem führt sie zu einer drastischen Senkung der Produktionskosten. Diese Einsparungen können an die Kunden weitergegeben werden, sodass der YOYO in Italien für nur knapp über 10.000 € erhältlich ist (Förderprämien für Elektrofahrzeuge eingerechnet). Dank eines vorgefertigten und standardisierten Chassis können die 3D-gedruckten Teile mit deutlich weniger Nacharbeit modifiziert und angepasst werden. Zur Erzielung der endgültigen Oberflächengüte durchlaufen die 3D-gedruckten Teile außerdem einen automatisierten Roboterfräsprozess, der für eine sehr glatte Oberfläche sorgt.
Dies sind nur zwei der offensichtlichsten Beispiele für den Einsatz additiver Fertigung bei der Herstellung von Karosserieteilen für Elektrofahrzeuge. An anderen, eher konzeptionellen Projekten waren sowohl große Automobilhersteller als auch kleine, innovative Start-ups beteiligt. Im Allgemeinen gehen die größeren Unternehmen wie FCA und MINI eher konservativ vor und setzen die additive Fertigung für kleinere Teile und für Anpassungen ihrer kommenden Elektrofahrzeuge ein, während einige innovative Start-ups auf modulare Elemente setzen, um die Funktionalität zu verbessern. Der Schweizer Automobilhersteller Rinspeed hat zum Beispiel eine einzigartige Vision für die Zukunft des Autos entworfen, die auf Modularität und Effizienz setzt: Seine Konzeptstudie MetroSnap ist ein modular aufgebautes Elektrofahrzeug mit 3D-gedruckten Teilen, die mehrere Funktionen erfüllen können. Bei dem innovativen Fahrzeugkonzept des Unternehmens sind Chassis und Karosserie voneinander getrennt, sodass die Fahrzeugkarosserie ausgetauscht werden kann. Durch das zum Patent angemeldete Wechselsystem kann das Elektrofahrzeug für mehrere Funktionen genutzt werden und z. B. wahlweise Personen oder Güter transportieren.
AM-Anwendungen in der Fertigung von Karosserieteilen für Elektrofahrzeuge (EVs) wurden zunächst nur als langfristige Möglichkeit gesehen, doch mit der zunehmenden Verbreitung von EVs und den damit verbundenen neuen Fertigungschancen rückt eine breite Akzeptanz in greifbare Nähe. Da für Elektrofahrzeuge in Zukunft immer weniger Teile benötigt werden, wird der 3D-Druck bei der Herstellung von Karosserieteilen für Elektroautos eine größere Marktdurchdringung erreichen als bei konventionellen Fahrzeugen.
Insbesondere die Gewichtsreduzierung – einer der Hauptvorteile der additiven Fertigung – ist für die Entwicklung von Elektrofahrzeugen von entscheidender Bedeutung, da jede Gewichtseinsparung oder Verbesserung der Gewichtsverteilung die Lebensdauer der Batterien verlängert. Der 3D-Druck kann dabei helfen, neue Teilegeometrien zu entwickeln, die das Elektrofahrzeug leichter werden lassen, ohne die Sicherheit zu beeinträchtigen. Wie schon bei der Entwicklung von Teilen für die Luft- und Raumfahrt zu beobachten war, kann durch die Neugestaltung von Teilen für die additive Fertigung mit parametrisch optimierten Geometrien Material eingespart und das Gewicht des Fahrzeugs reduziert werden, während die für die Sicherheit erforderliche strukturelle Integrität erhalten bleibt. Zudem bietet die additive Fertigung die Möglichkeit, Werkzeuge überflüssig zu machen und mehrere Teile zu einem einzigen zusammenfassen. Dies kann besonders für Unternehmen von Vorteil sein, die neue Designs entwickeln, oder für neue Start-ups, die dem Markt beitreten wollen.
Elektrische Hilfssysteme und Elektronik für Elektrofahrzeuge
Potenzial für die additive Fertigung
Kurzfristig und moderat mit bis zu 2–3 % Marktdurchdringung bis 2030
Dieser Markt umfasst Audio-/Videogeräte, Kameras, Niederspannungs-Stromversorgungssysteme, Messgeräte und Zähler, Komponenten der Zündanlage, Beleuchtungs- und Signalsysteme sowie verschiedene Arten von Sensoren, elektrische Schalter, Kabelbäume und natürlich Elektronikgehäuse, die in die Struktur des Elektrofahrzeugs integriert werden müssen. Was die Anwendungen betrifft, so wird die additive Fertigung bereits in großem Umfang bei der Herstellung von kundenspezifischen Elektronikgehäusen und Schaltern eingesetzt. Bei weiteren wichtigen Anwendungen kommt Kupfer zum Einsatz, und zwar bei den Verfahren Metal PBF (Metall-Pulverbettfusion) sowie Bound Metal und Metal Binder Jetting.
Sowohl die Unternehmen für die AM-Teileproduktion als auch die AM-Fabriken haben die Kosteneffizienz des 3D-Drucks von Elektronikgehäusen (und verwandten Produkten) nachweisen können. Ein Vorteil des großvolumigen 3D-Drucks ist die Möglichkeit, kundenspezifische Teile in großem Maßstab ohne die Kosten für Spritzwerkzeuge zu produzieren. Diese Freiheit ermöglicht die Weiterentwicklung der Produkte noch während der Produktion und reduziert den Lagerbedarf. Elektronikgehäuse können nicht auf die Millionen von Leiterplattendesigns abgestimmt werden, die in den Fahrzeugen mit ihrer immer größeren Zahl elektronischer Bauteile zum Einsatz kommen – ein Trend, der sich mit den Elektrofahrzeugen und der zunehmenden Nachfrage nach kundenspezifischen Anpassungen noch um mehrere Größenordnungen verstärken wird. Mit dem 3D-Druck können die Gehäuse auf Anforderung genau dann produziert werden, wenn die betreffenden Teile verkauft werden, ohne dass Kosten für Spritzgusswerkzeuge anfallen.
Nano Dimension hat sich auf die Entwicklung und Produktion von elektronischen Komponenten mittels 3D-Druck spezialisiert. Angesichts der steigenden Nachfrage nach Smart Mobility und internetfähigen Geräten (IoT) suchen Unternehmen, die Polymer-3D-Druck einsetzen, nach neuen Wegen zur Entwicklung innovativer und funktioneller Geräte mit Anwendungen, die Effizienz, verbesserte Leistung und Erschwinglichkeit bieten. Das DragonFly System von Nano Dimension ist eine ideale Technologie, um die interne Elektronikentwicklung zu beschleunigen und die Freiheit beim Design zu erhöhen, damit neue Produkte schnell und kostengünstig entwickelt werden können.
Die additive Elektronikfertigung ermöglicht ein schnelles Prototyping und die Herstellung von leitfähigen Komponenten, gekapselten Sensoren und intelligenten Oberflächen. All dies bietet den Automobilherstellern die Flexibilität, eine ganze Leiterplatte oder nur einen Teil eines Steckverbinders zu drucken; außerdem ist es möglich, die HF- und Digitalbereiche der Leiterplatte parallel zu entwickeln, um Konzepte im laufenden Betrieb testen zu können. All dies kann es ermöglichen, individuell angepasste Elektronikkomponenten zu entwickeln wie z. B. eingebettete Sensoren, leitfähige Geometrien, spritzgegossene Schaltungsträger (MIDs), Leiterplatten und viele weitere Bauteile, die das Grundgerüst für innovative Automobilkomponenten zur Verbesserung des Fahrerlebnisses bilden können.
In ähnlicher Weise hat die Rogers Corporation in Zusammenarbeit mit Fortify3D die Radix 3D Printable Dielectrics Produktfamilie entwickelt; das erste bisher verfügbare Material weist eine Dielektrizitätskonstante von 2,8 und nur geringe Verluste bei Mikrowellenfrequenzen auf. Diese druckbaren dielektrischen Werkstoffe bieten den Entwicklern von HF-Schaltungen eine noch nie dagewesene Designfreiheit bei der Entwicklung neuer Komponenten, z. B. von Fahrzeugradaren zur Brems- und Kollisionsvermeidung, da die typischen Einschränkungen bei der Fertigung nicht mehr berücksichtigt werden müssen.
Es wird erwartet, dass der Einsatz von AM bei der Herstellung elektronischer Komponenten – insbesondere Gehäuse und Schalter – schnell auf Serienproduktionsniveau ansteigen wird, da Verbrennungsmotoren immer kompakter und Elektrofahrzeuge immer aerodynamischer werden. Der Polymer-3D-Druck mit Hochtemperaturwerkstoffen ermöglicht schon heute die Herstellung diverser Komponenten unter der Motorhaube. Bei Elektrofahrzeugen und allgemein bei intelligenten Fahrzeugen dürfte der Einsatz von additiver Fertigung sogar noch zunehmen, da hohe Temperaturen immer weniger ein Thema sind (mit Ausnahme der Batterien) und der Bedarf an komplexen elektronischen Bauteilen steigt.
Komponenten des elektrischen Antriebsstrangs und AM-Anwendungen
Grandview Research schätzt den weltweiten Markt für elektrische Antriebe im Jahr 2020 auf etwa 20 Milliarden USD und erwartet, dass er von 2020 bis 2027 mit einer durchschnittlichen jährlichen Wachstumsrate von 13,6 % auf fast 40 Milliarden USD im Jahr 2027 ansteigen wird.
Einige Teile des Antriebsstrangs und des Chassis sind sowohl bei Fahrzeugen mit Verbrennungsmotor als auch bei Elektrofahrzeugen gleich, auch wenn sie unterschiedlich aussehen können. Mehrere von ihnen wurden in irgendeiner Form 3D-gedruckt, angefangen mit dem viel beachteten Projekt des Hybrid-Supersportwagens Czinger 21C, bei dem eine Reihe von 3D-gedruckten Teilen zum Einsatz kommen. Czinger verwendet additive Fertigungsverfahren zur Herstellung von Hochleistungskomponenten. Dazu gehört auch das Chassis, das vom Vorgängerprojekt, dem Supersportwagen Blade, abgeleitet ist und mit der Metall-PBF-Technologie von SLM Solutions hergestellt wurde.
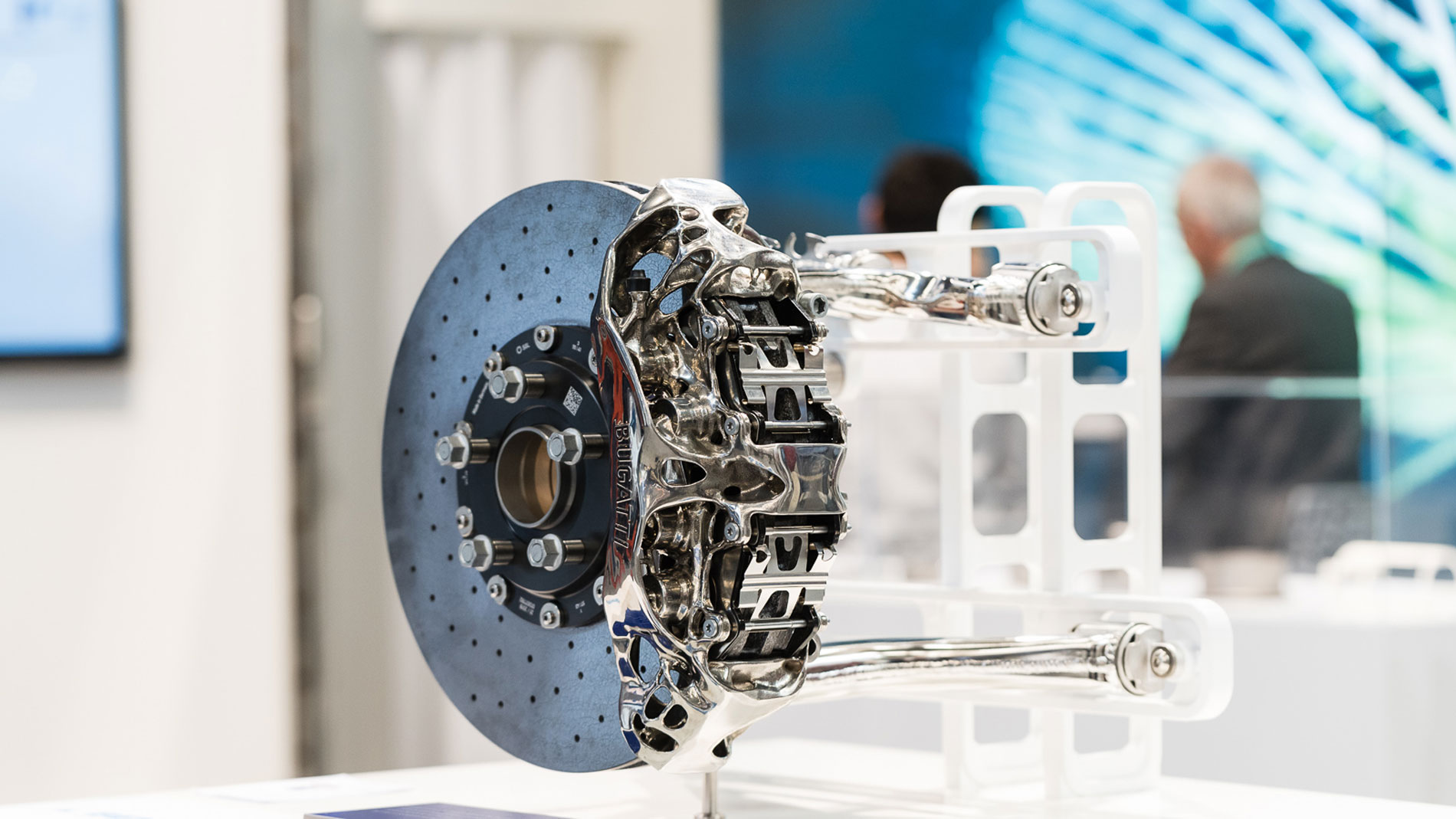
Bugatti ist ebenfalls ein großer Hersteller von Supersportwagen mit Verbrennungsmotor, der sich nach der Übernahme durch Rimac der Elektrifizierung annähert. Bugatti hat die additive Fertigung bereits bei einer Reihe von Teilen eingesetzt, darunter die revolutionären 3D-gedruckten Bremssättel aus Titan. In neuerer Zeit hat das Unternehmen hybride Komponenten hergestellt wie z. B. die 0,5 Meter lange Nebenwelle, bei der Carbonfasern mit einem 3D-gedruckten Titan-Endstück kombiniert wurden, um das Gewicht auf 1,5 Kilogramm zu halbieren und die Performance durch die Reduzierung der rotierenden Massen zu verbessern. Auch Rimac arbeitet mit 3D-Druck, seit sich das Unternehmen 2011 an Materialise gewandt hat, um Teile für den Innenraum seines Concept_One herzustellen zu lassen – eines der weltweit ersten elektrischen Hypercars. Im Bereich der Hypercars ist Lamborghini eine weitere große Marke, die sowohl Elektrifizierung als auch 3D-Druck in Betracht zieht. Das Unternehmen aus Sant'Agata Bolognese verwendet Carbon für verschiedene Endbauteile (allerdings noch nicht im Chassis oder Antriebsstrang) sowohl bei seinen Sportwagen als auch bei seinem sehr erfolgreichen SUV Urus.
Elektrofahrzeuge (EVs) nutzen die in der Batterie gespeicherte elektrische Energie, um einen Elektromotor anzutreiben und die für das Fahren notwendige Leistung zu liefern. Somit benötigen EVs weder Verbrennungsmotor noch Getriebe – zwei der wichtigsten Komponenten für Verbrennerfahrzeuge. Stattdessen verfügen Elektrofahrzeuge über mehrere Komponenten für den elektrischen Antrieb: den Elektromotor, die Batterie, das Bordladegerät sowie die Electric Power Control Unit (EPCU) als Steuergerät. Alle diese Komponenten sind erforderlich, um mit der in der Batterie gespeicherten elektrischen Energie eine Antriebskraft erzeugen zu können.
Der Motor ist zugleich ein elektrischer Generator: Er wandelt die kinetische Energie, die im Leerlauf erzeugt wird (z. B. während das Auto bergab fährt), in elektrische Energie um, die in der Batterie gespeichert wird. Das gleiche Energiesparprinzip gilt, wenn das Fahrzeug verlangsamt.
Bei Elektromotoren ist ein für die additive Fertigung besonders interessanter Fokusbereich das Kupfer. Hier hat die deutsche Firma Additive Drives vielversprechende Anwendungsbeispiele vorgestellt. Eines davon – in Zusammenarbeit mit dem Racetech Racing Team e. V. der TU Freiberg – betrifft 3D-gedruckte Einzelspulen für den Einsatz in Rennmotoren. In einem anderen Projekt konnten im Kupfer-3D-Druck hergestellte Hairpin-Wicklungen den Zeitbedarf für die Entwicklung und Produktion des Prototyps für einen elektrischen Traktionsmotor auf einen Monat verkürzen. Für den Dresdener Pedelec-(E-Bike-)Hersteller Binova wurde die direkte Produktion von individuellen Chargen realisiert: Mit Hilfe von 3D-gedruckten Einzelspulen konnte Binova mehrere unterschiedliche Typen von Elektrofahrrädern mit einem unkonventionellen Elektromotor-Design produzieren, ohne dass Werkzeuganpassungen erforderlich waren. Unlängst haben Porsche und SLM Solutions ein Projekt vorgestellt, das die Herstellung eines kompletten Gehäuses für einen Elektroantrieb im 3D-Druck zum Ziel hat. Das 3D-gedruckte E-Antrieb-Gehäuse der Motor-Getriebe-Einheit, das im additiven Laserschmelzverfahren hergestellt wurde, hat sämtliche Qualitäts- und Belastungsprüfungen bestanden. Dieses Verfahren könnte also zukünftig zu einer praktikablen Produktionsmethode werden.
Das Reduziergetriebe in einem Elektrofahrzeug dient dazu, die vom Motor gelieferte Kraft effektiv auf die Räder zu übertragen. Der Elektromotor hat eine erheblich höhere Drehzahl als ein Verbrennungsmotor. Durch die niedrigere Drehzahl kann der Antriebsstrang des Elektrofahrzeugs das daraus resultierende höhere Drehmoment ausnutzen. Diese Komponente ist ein relativ komplexes Metallbauteil, das in Zukunft mittels additiver Fertigung optimiert werden könnte, um die Produktion zu beschleunigen, die Leistungsfähigkeit zu verbessern und das Gewicht zu reduzieren. Auch das komplexe Gehäuse der Electric Power Control Unit könnte von AM-Prozessen profitieren. Sie besteht aus dem Wechselrichter (der den Gleichstrom der Batterie in Wechselstrom umwandelt und die Motordrehzahl steuert), dem Niederspannungs-DC/DC-Wandler, der die verschiedenen elektronischen Systeme des Fahrzeugs versorgt, und der Vehicle Control Unit. Die VCU überwacht fast alle Leistungssteuerungsprozesse des Fahrzeugs; dazu gehören die Motorsteuerung, die Steuerung der regenerativen Bremsen, das Lastmanagement der Klimaanlage sowie die Energieversorgung der elektronischen Systeme.
Batterien für Elektrofahrzeuge
Potenzial für die additive Fertigung:
Mittel- bis langfristig und sehr erheblich, mit einer Marktdurchdringung von über 5 % bis 2030
2019 erreichte der weltweite Markt für Elektrofahrzeugbatterien ein Volumen von fast 50 Milliarden USD. Prognosen gehen davon aus, dass der Markt zwischen 2019 und 2030 mit einer durchschnittlichen jährlichen Zuwachsrate von 14,1 % auf über 212 Milliarden USD im Jahr 2030 wachsen wird, wie Daten von NMSC zeigen.
Die Batterie speichert elektrische Energie und ist die Entsprechung zum Kraftstofftank eines Verbrennungsmotors: Je höher die Kapazität, desto größer die Reichweite. Aber auch die Größe und das Gewicht der Batterie haben großen Einfluss auf die Leistungsfähigkeit des Fahrzeugs. Eine größere und schwerere Batterie beansprucht Platz im Fahrgast- und Kofferraum, verschlechtert die Energieeffizienz und erhöht den Verbrauch. Die beste Möglichkeit zur Leistungsoptimierung besteht also darin, die Energiedichte der Batterie zu maximieren, das heißt, eine kleine, leichte Batterie einzusetzen, die so viel elektrische Energie wie möglich speichert.
Batterien werden schon sehr bald ein besonders interessanter (wenn auch schwieriger) Anwendungsbereich für die additive Fertigung sein. Es wurden bereits verschiedene Versuche unternommen, Batterien mit unterschiedlichen 3D-Drucktechnologien herzustellen – sowohl mit Polymer- als auch mit Keramikwerkstoffen. Da Batterien in vielen verschiedenen Formen und Größen gestaltet werden können, um ihre Effizienz zu verbessern, könnte sich die additive Fertigung als nützliches Verfahren erweisen, um mehrere neue Designs iterativ zu testen und schließlich herzustellen. Die heute in Elektrofahrzeugen eingesetzten Batterien bestehen im Wesentlichen aus Hunderten von kleinen Akkuzellen, die zur Erhöhung der Kapazität zusammengeschaltet sind. Das 85-kWh-Akkupaket von Tesla beispielsweise besteht aus 7.104 Zellen, die ungefähr die Größe von AA-Akkus haben. Beim 3D-Druck müssen keine einzelnen Zellen produziert und zusammengefügt werden: Das Modul kann direkt in der gewünschten Gesamtform entworfen und gedruckt werden. Durch additive Fertigung lässt sich auch die Struktur der Batterieelektroden verändern: Poröse Elektroden ermöglichen eine höhere Energiedichte, und die additive Fertigung eignet sich ideal, um aus den Elektrodenwerkstoffen Gitterstrukturen aufzubauen, die eine größere exponierte Oberfläche für die chemischen Reaktionen bieten und so den Wirkungsgrad der Batterie erhöhen.
Das Schweizer Unternehmen Blackstone Resources hat kürzlich eine Reihe wichtiger Meilensteine für seine proprietäre 3D-Drucktechnologie zur Herstellung von Lithium-Ionen-Festkörperbatterien (SSBs) erreicht. Nach Aussage des Unternehmens bietet sein 3D-Druckverfahren erhebliche Vorteile gegenüber herkömmlichen Batteriezellen, die mit flüssigen Elektrolyten arbeiten. Dazu gehören deutlich niedrigere Kosten, eine höhere Produktionsflexibilität hinsichtlich des Zellenformats und eine um 20 % höhere Energiedichte. Zudem könnte durch den Einsatz dieser Technologie die Menge der Materialien, die keine Energie speichern (wie Kupfer und Aluminium), um bis zu 10 % reduziert werden. Das Schweizer Unternehmen hat außerdem einen Workflow entwickelt, mit dem diese Batterien ab 2021 mithilfe einer eigenen Batteriedrucktechnologie in jeder beliebigen Form in Massenproduktion hergestellt werden können.
Blackstone ist aber nicht das einzige Unternehmen, das 3D-gedruckte SSBs entwickelt: In den USA hat die Sakuú Corporation (ehemals Keracell) 62 Millionen USD aufgebracht, um die Entwicklung einer automatisierten Multimaterial-Multiprozess-AM-Technologie zur Herstellung von 3D-gedruckten SSBs zu finanzieren.
Im Zeitraum von 2020 bis 2021 hat Sakuú die Energiedichte seiner Batterie der ersten Generation von 40 Wh/l auf 600 Wh/l erhöht, gleichzeitig die Anzahl der Zellschichten von 1 auf 30 erhöht und die Zellkapazität von 2,3 mAh auf 3000 mAh gesteigert und damit im Wettlauf um SSBs für Elektrofahrzeuge einen neuen Maßstab gesetzt. Diese Batterien werden hinsichtlich der Energiedichte sehr wettbewerbsfähig gegenüber den derzeitigen Li-Ionen-Batterien sein und gleichzeitig die inhärenten Sicherheitsvorteile der Festkörpertechnologie bieten. Das Unternehmen befindet sich nach eigenen Angaben auf dem Weg zur vollständigen Kommerzialisierung seiner SSBs der ersten Generation und strebt für die zweite Hälfte 2022 die Massenproduktion an. Außerdem druckte Sakuú im vergangenen Jahr die weltweit erste vollkeramische SSB-Batterie als frühe Demonstration der zweiten Generation seiner ASSB (All-Solid State Battery).
Im Antriebsstrang von Elektrofahrzeugen trägt die additive Fertigung besonders effektiv zur Reduzierung der Teilegröße bei, die eine Gewichtsreduzierung und Leistungssteigerung ermöglicht. Die Teilereduzierung wiederum ermöglicht eine höhere Laufleistung. Die tatsächliche Marktdurchdringung der additiven Fertigung bei Elektrofahrzeugen – über die Anwendungen hinaus, die mit den Antriebssträngen von Verbrennerfahrzeugen identisch sind, wie z. B. Chassis, Bremsen und Fluidstromanwendungen – hängt jedoch in hohem Maße von der Möglichkeit ab, die additive Fertigung in der Serienproduktion der Batterien einzusetzen. Entsprechende Arbeiten in diesem Bereich sind bereits im Gange, aber es wird noch einige Jahre dauern, bis sich daraus eine konsolidierte Geschäftschance ergibt.
*Dieser Artikel wurde ursprünglich im „AM Focus Automotive AM eBook 2022“ von 3dpbm veröffentlicht. Die AM Focus eBooks von 3dpbm erscheinen einmal monatlich kostenlos und enthalten jeweils eine Analyse des vertikalen Referenzsegments.
WEITERE INFORMATIONEN UNTER:
Tags
- Automotive
- Nachhaltigkeit