Although the "additive printing process" itself is key to the procedure, it is just one small part of a complex process chain. From the idea through to the final, finished product, there are lots of process steps to run through.
The Additive Manufacturing process as a whole
In order to make the best possible use of generative manufacturing technologies, one must have a command of the entire process. What's more, the detailed steps involved can vary considerably, depending on the AM process, the materials and other aspects. In practice, there are entire AM processes consisting solely of manual individual steps, but at the other end of the spectrum, there are entire AM processes which are highly automated and integrated (e.g. in dentistry).
Here are some handy questions for manufacturers when it comes to using AM processes:
- What material is required?
- Are the components prototypes or production parts? What quantities are required?
- Do similar comparable AM applications already exist?
- Are there any providers who offer this service?
- How must the existing organizational structure be modified to meet the demands of AM?
- How must the development process be modified to match the AM process?
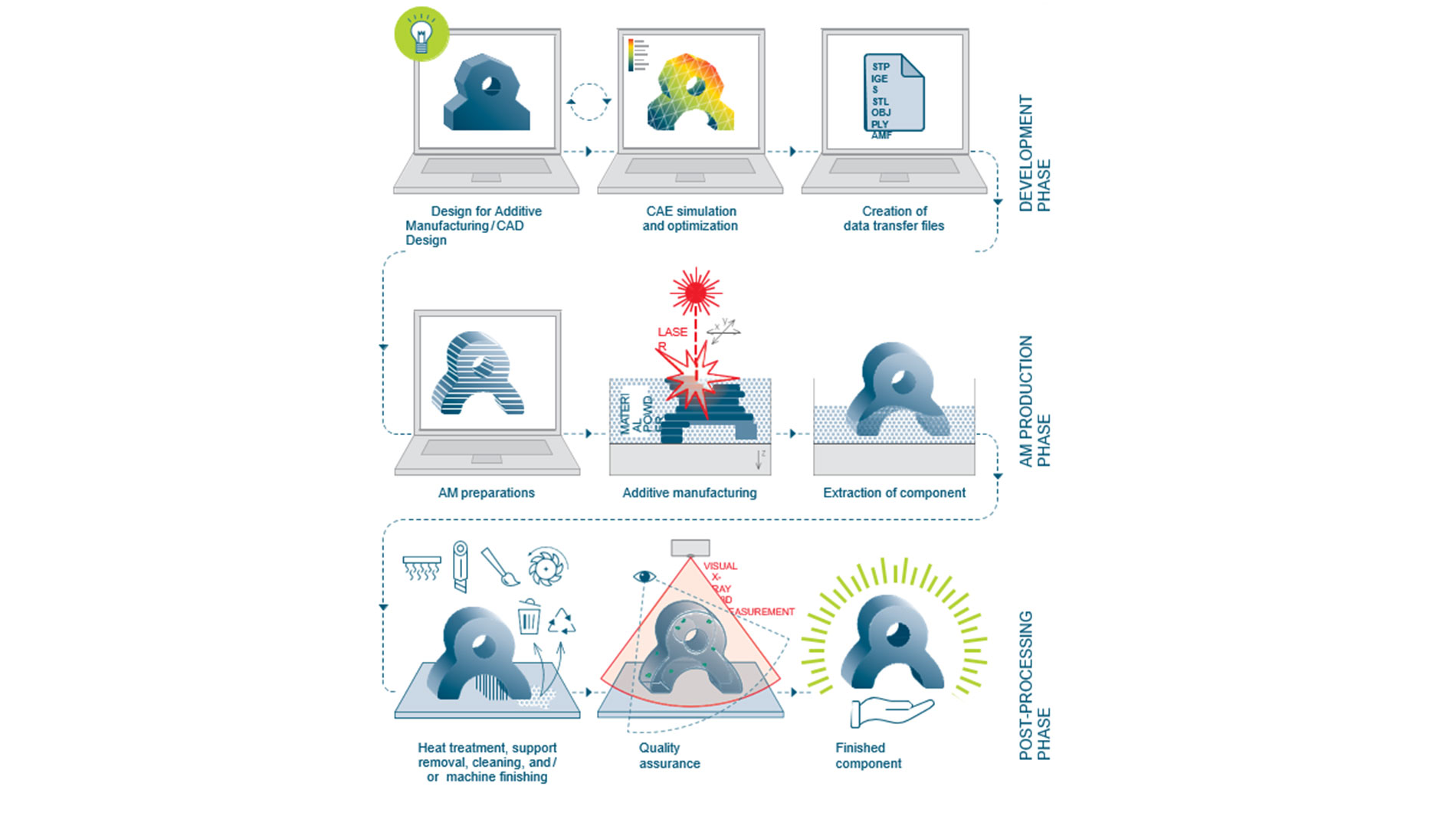
Development phase
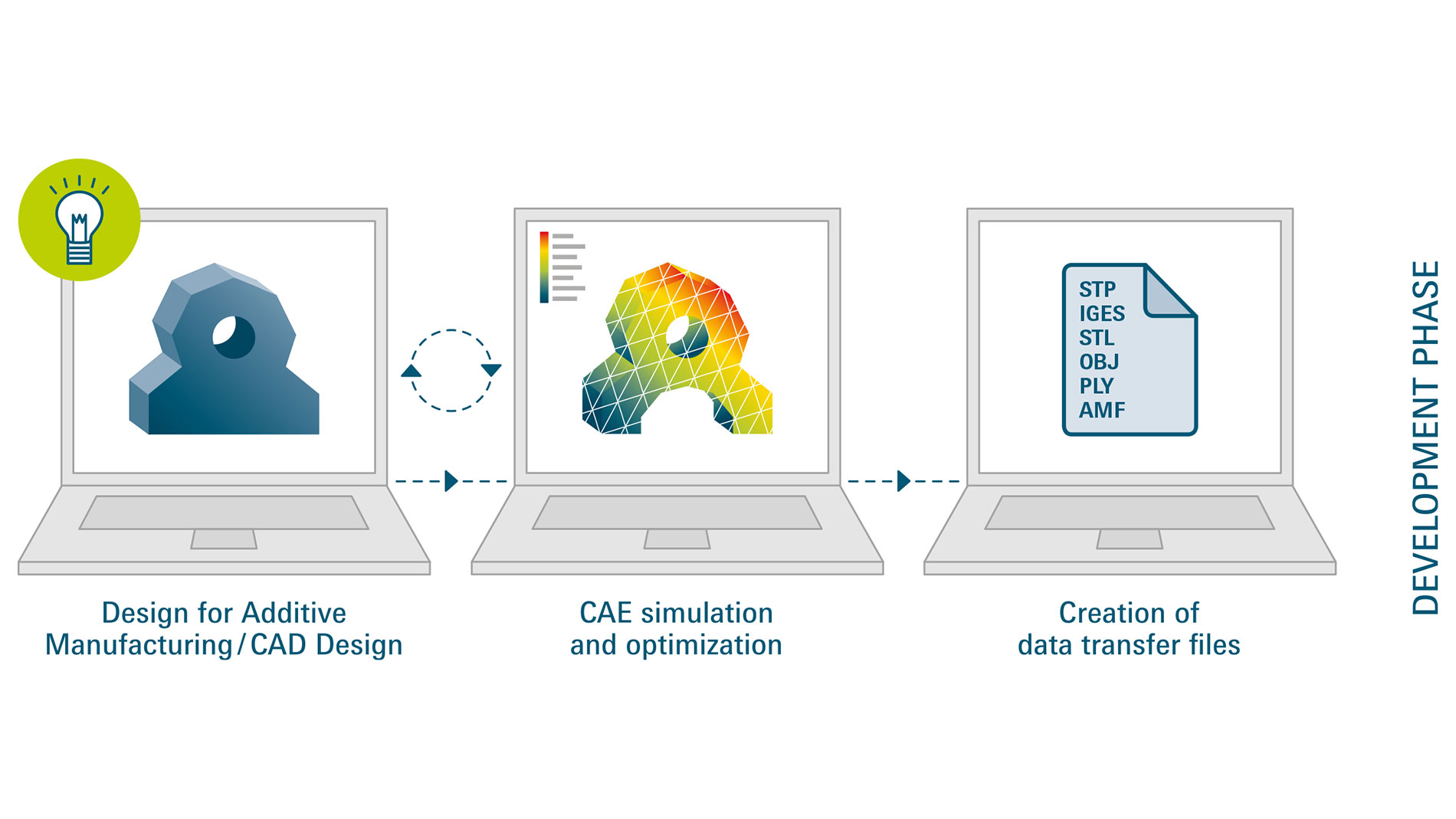
Questions in the development phase
- What component and material properties MUST the AM component have?
- Has the material been qualified or validated in general or for the particular application in question?
- What must be specifically noted for the "design for Additive Manufacturing" step?
- Are there particular design specifications that apply to components compatible with AM?
- What design options do components compatible with AM provide?
- In what format must the part-model CAD data be provided?
- Is a specific AM process particularly well suited to the components in question?
AM production phase
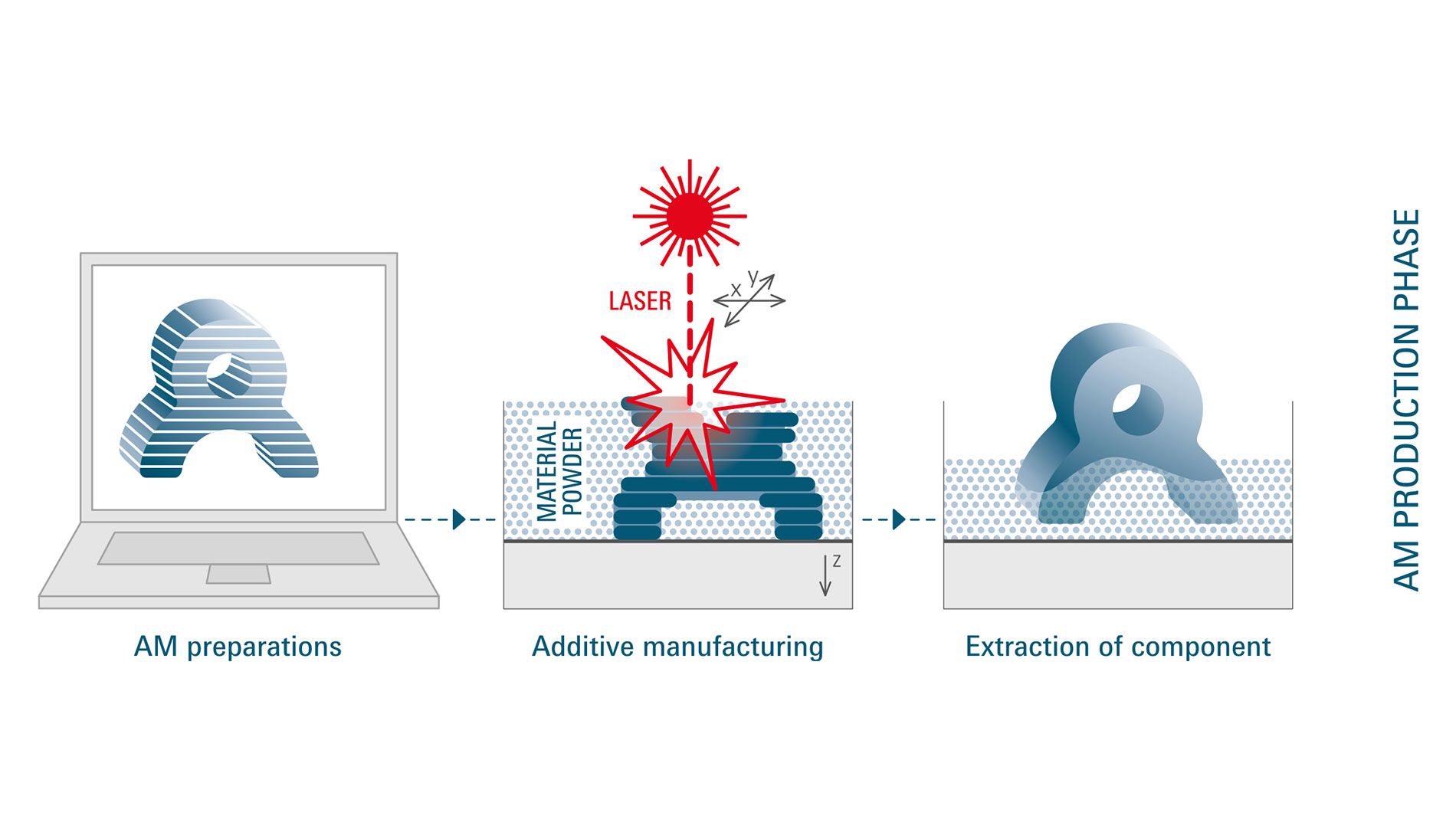
Questions in the AM production phase
- Can the AM process be integrated into existing processes?
- What support expenses are associated with the AM process in question?
- What are the expected maintenance costs for the AM process?
- Are the materials freely available or can they only be purchased as originals from the system manufacturer?
- Is the system a black box or can the production parameters be customized?
- Are there any specific safety requirements to meet for people and the environment?
- What is the production/construction speed of the AM process?
Post-processing phase
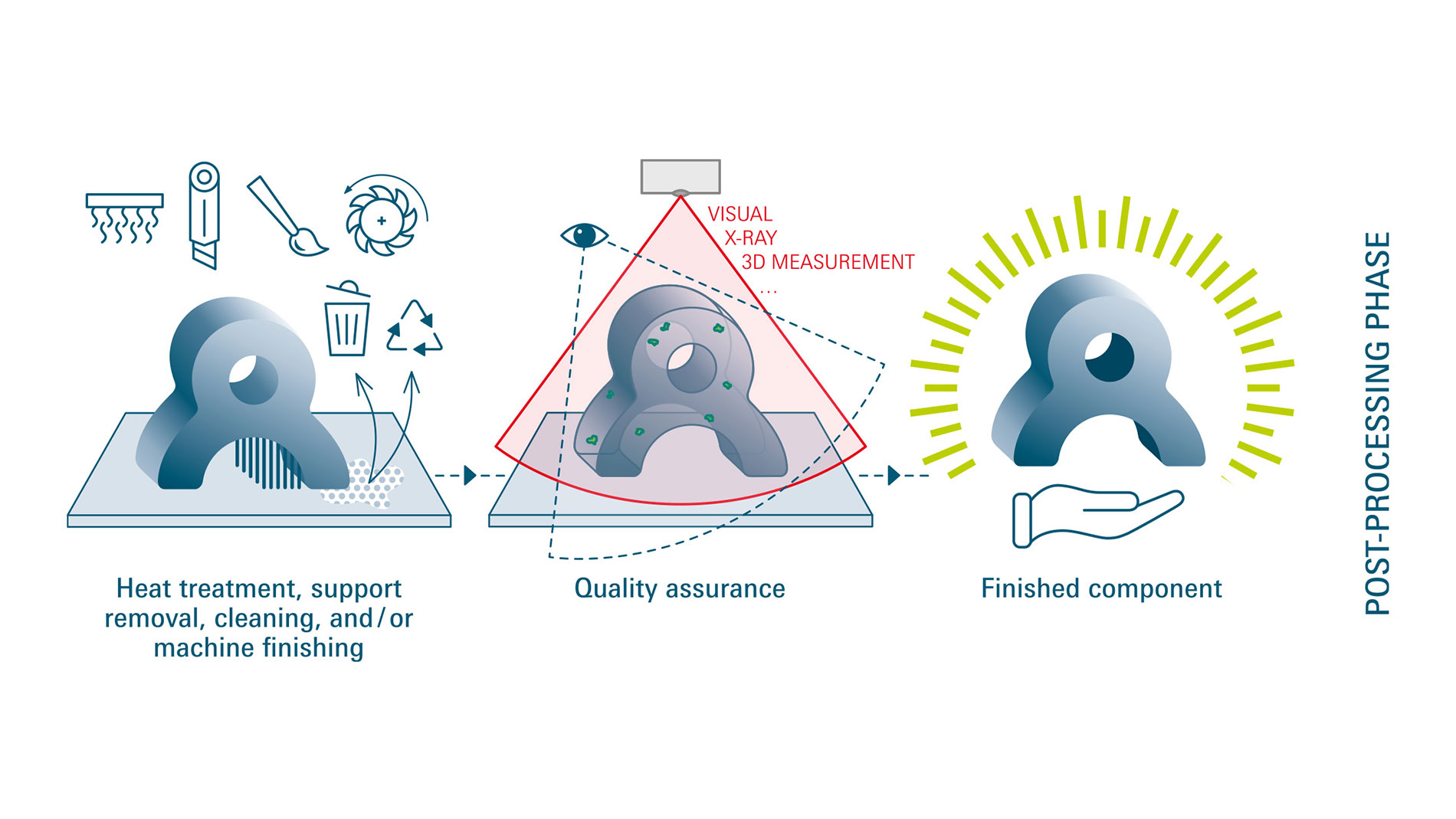
Questions in the post-processing phase
- What specific finishing work has to be done on the AM components?
- Do the AM components need to be post-treated in a subsequent process step?
- Can material not used during the AM process be reused?
- What must be done with material that has been consumed?
- Does component quality need to be verified via a qualification procedure such as non-destructive testing?
The amount of work involved in post-processing AM components varies greatly depending on the application, material and process that have been used. Sometimes it can far outweigh the effort that went into the printing process itself. At the moment, a large proportion of the post-processing steps carried out after the actual printing process are manual, independent individual processes with a low level of automation. In-depth knowledge is required if one is to master all the individual processes involved and meet the desired quality standards in order to produce high-quality AM components.
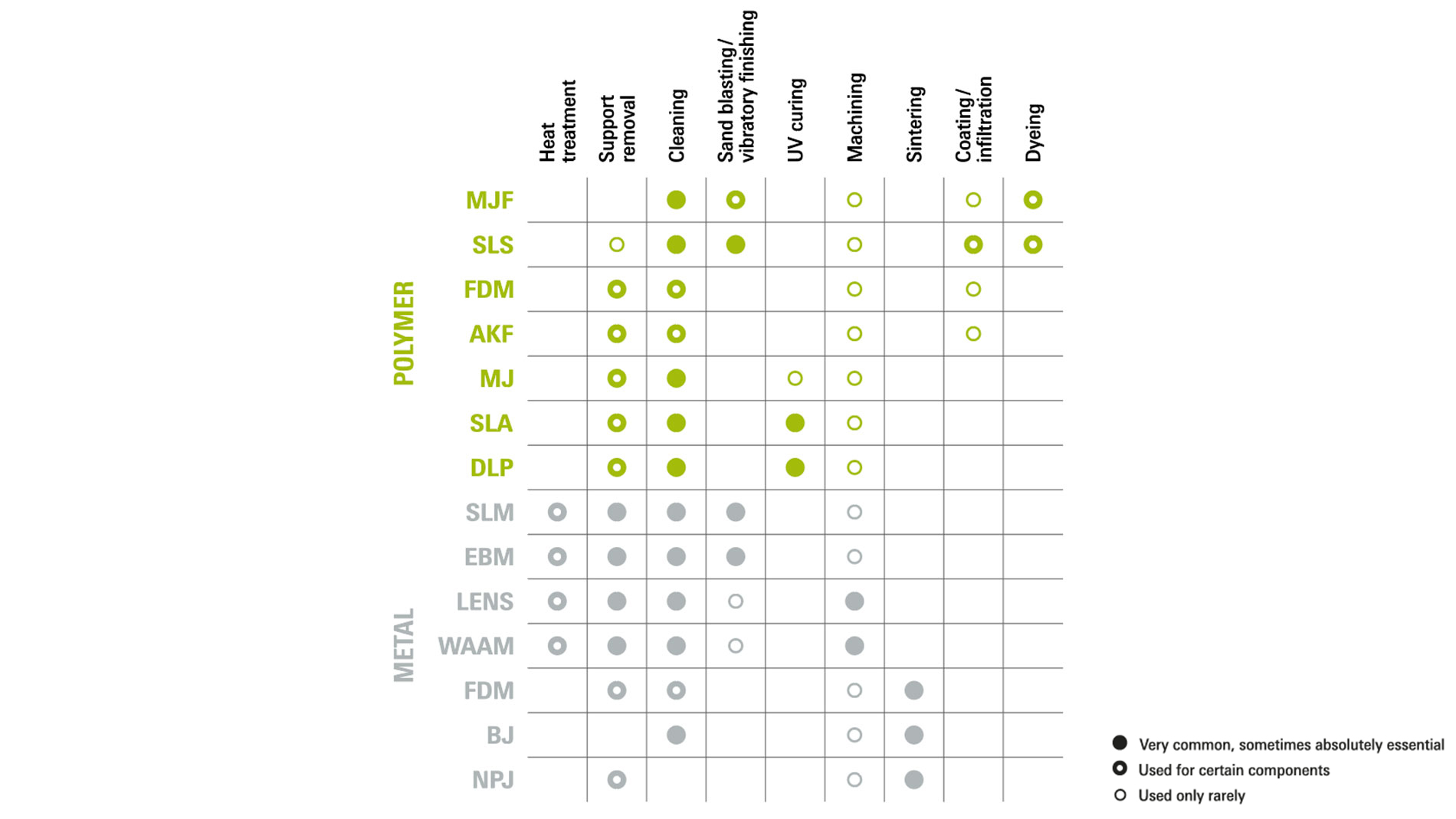
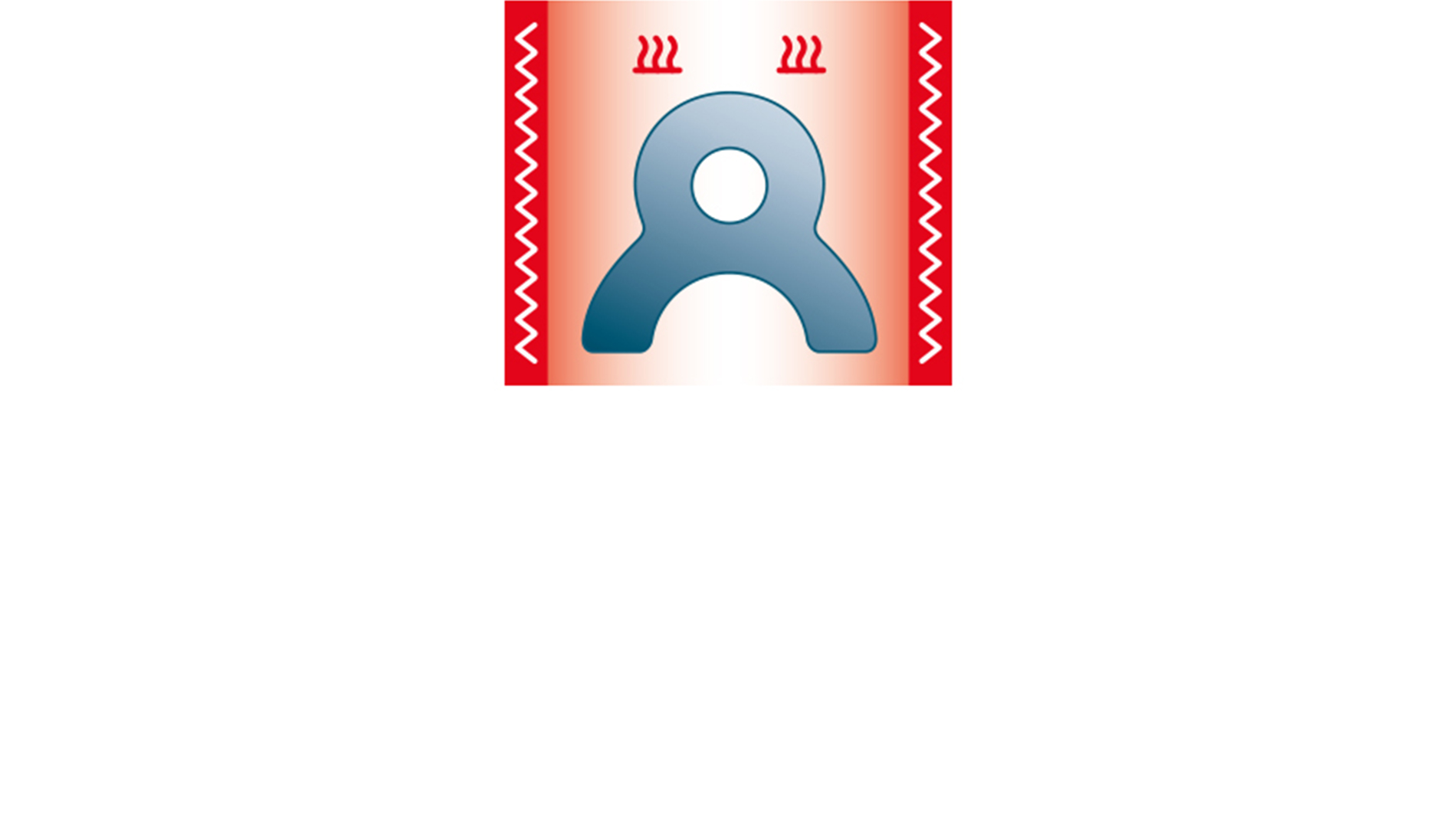
Heat treatment
Heat treatment usually follows the most common metal processes in order to relieve the internal stress that is created by adding the layers. Only then are the components removed from their support.
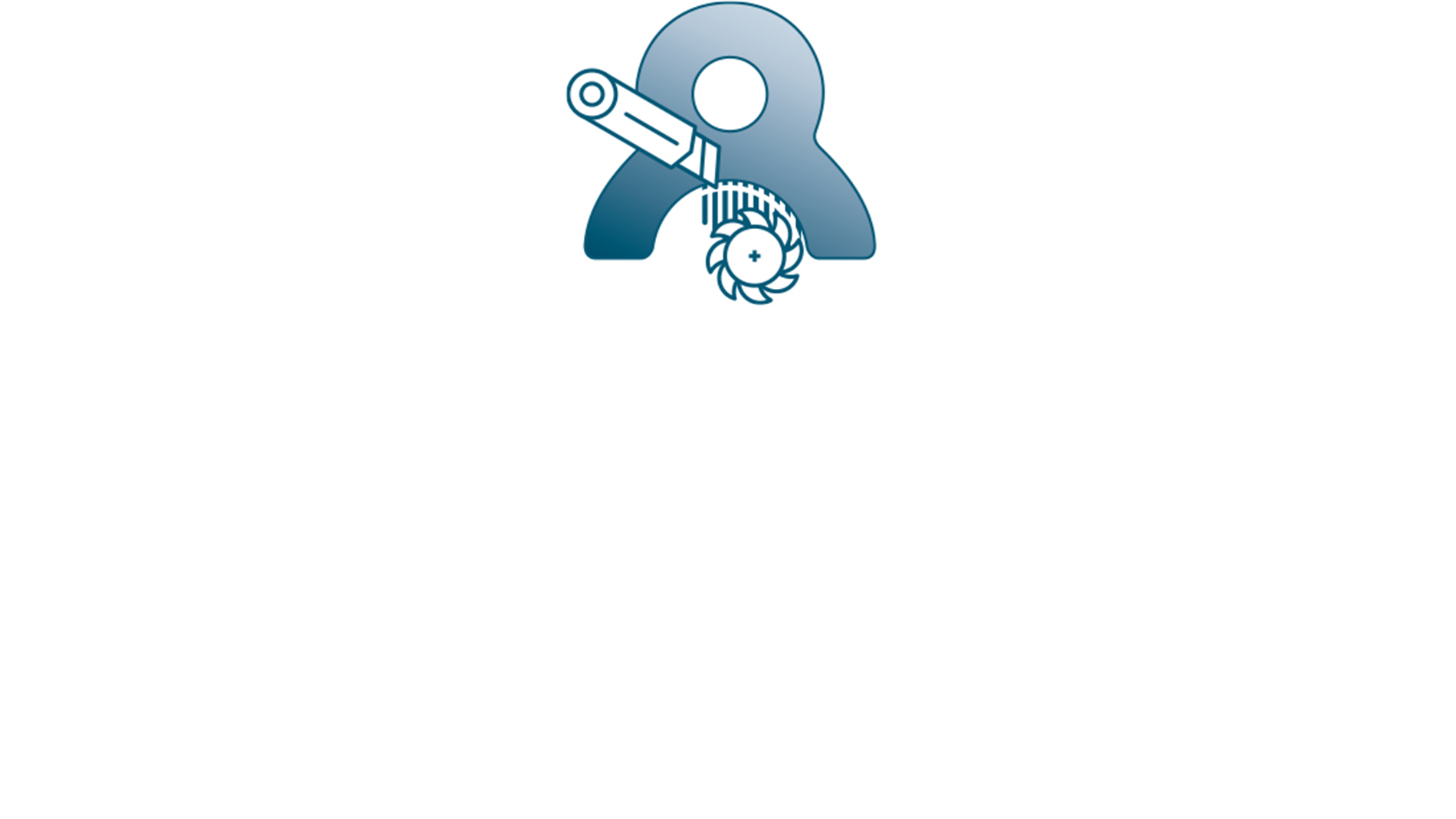
Support removal
3D components are attached to the corresponding base plates by scaffolding and support structures, thus enabling overhanging structures to be created or reducing the degree of warp. These supports are then removed after the actual additive manufacturing process has been performed.
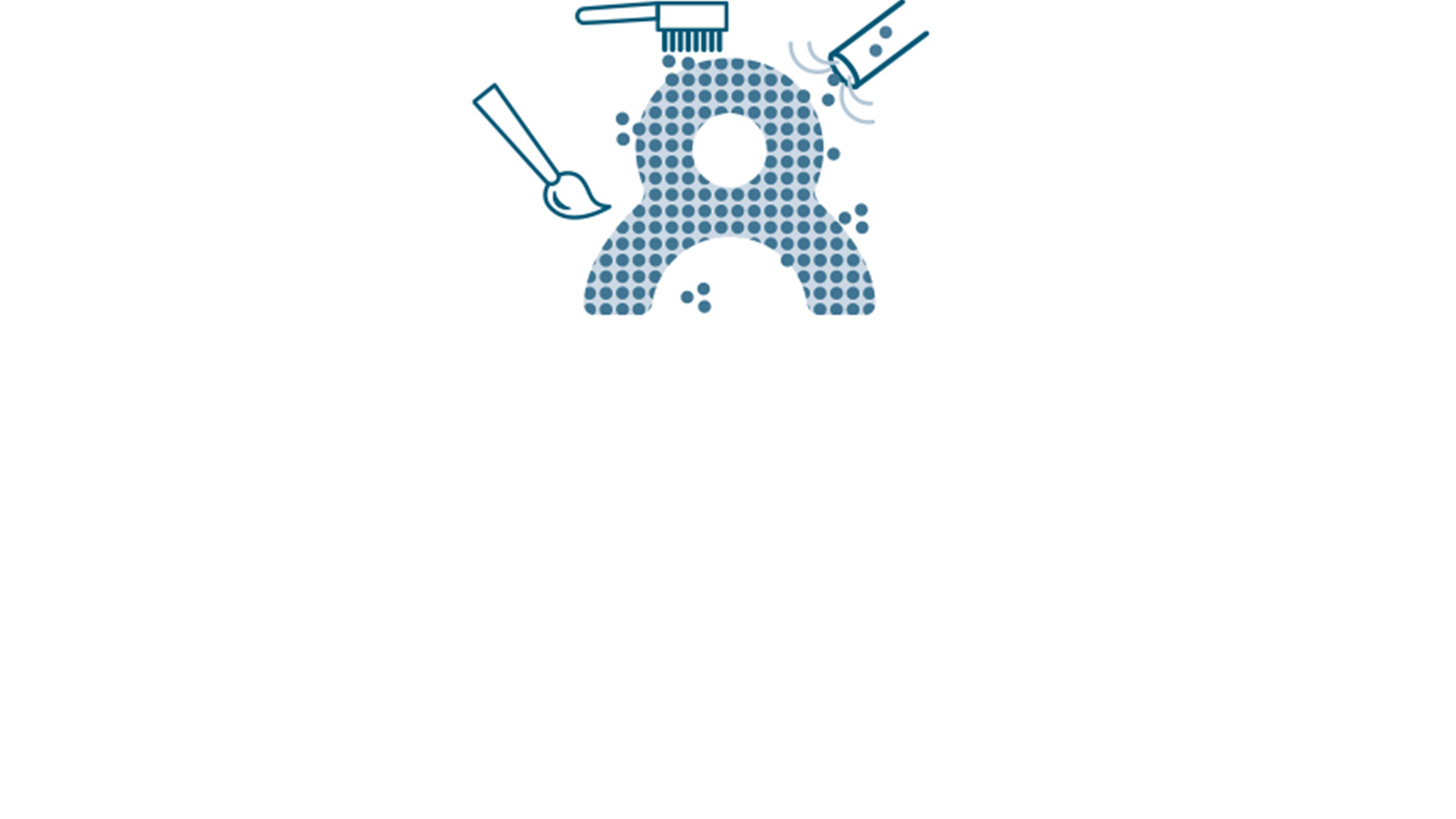
Cleaning
Components need to be thoroughly cleaned after Additive Manufacturing. Excess material, such as metal powder or polymer powder, is therefore removed.
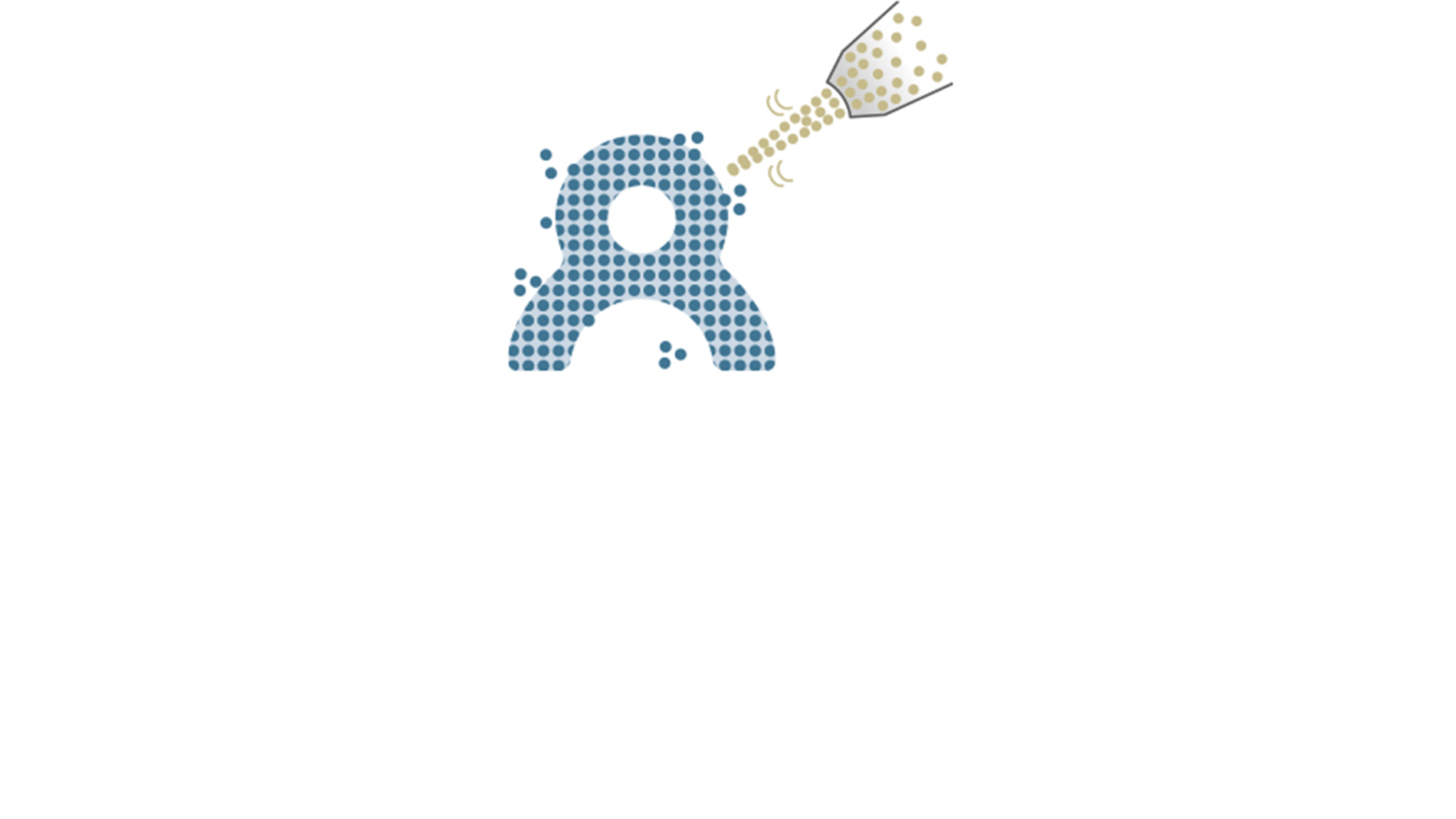
Sand blasting / vibratory finishing
Normal cleaning is not sufficient for powder-based processes. Various blasting processes (such as sand lasting) or vibratory finishing processes serve to clean and, in particular, smooth the surfaces of the component.
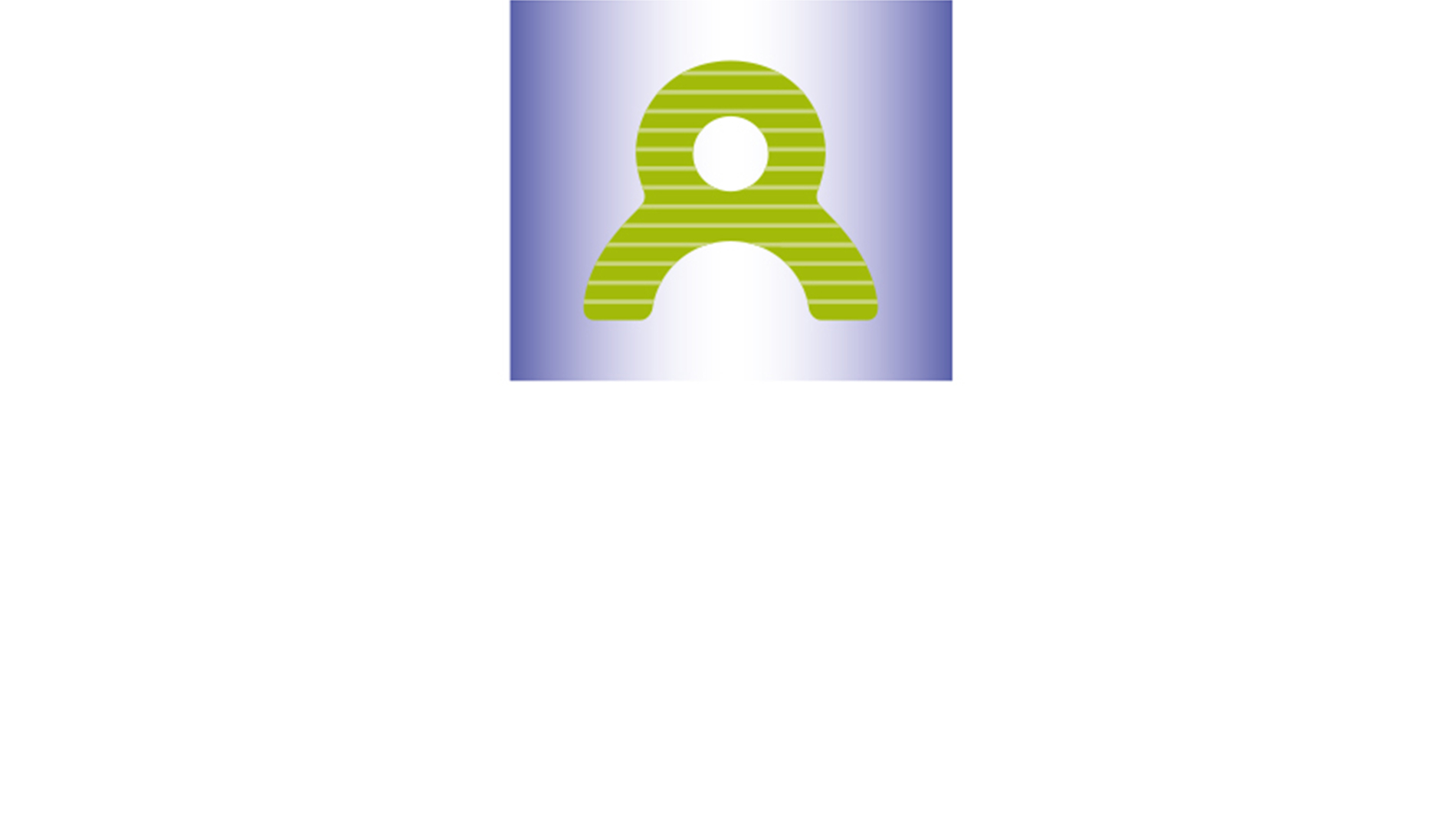
UV curing
Components based on photopolymers are exposed to UV light to fully cure them in order to achieve the ultimate material strength.
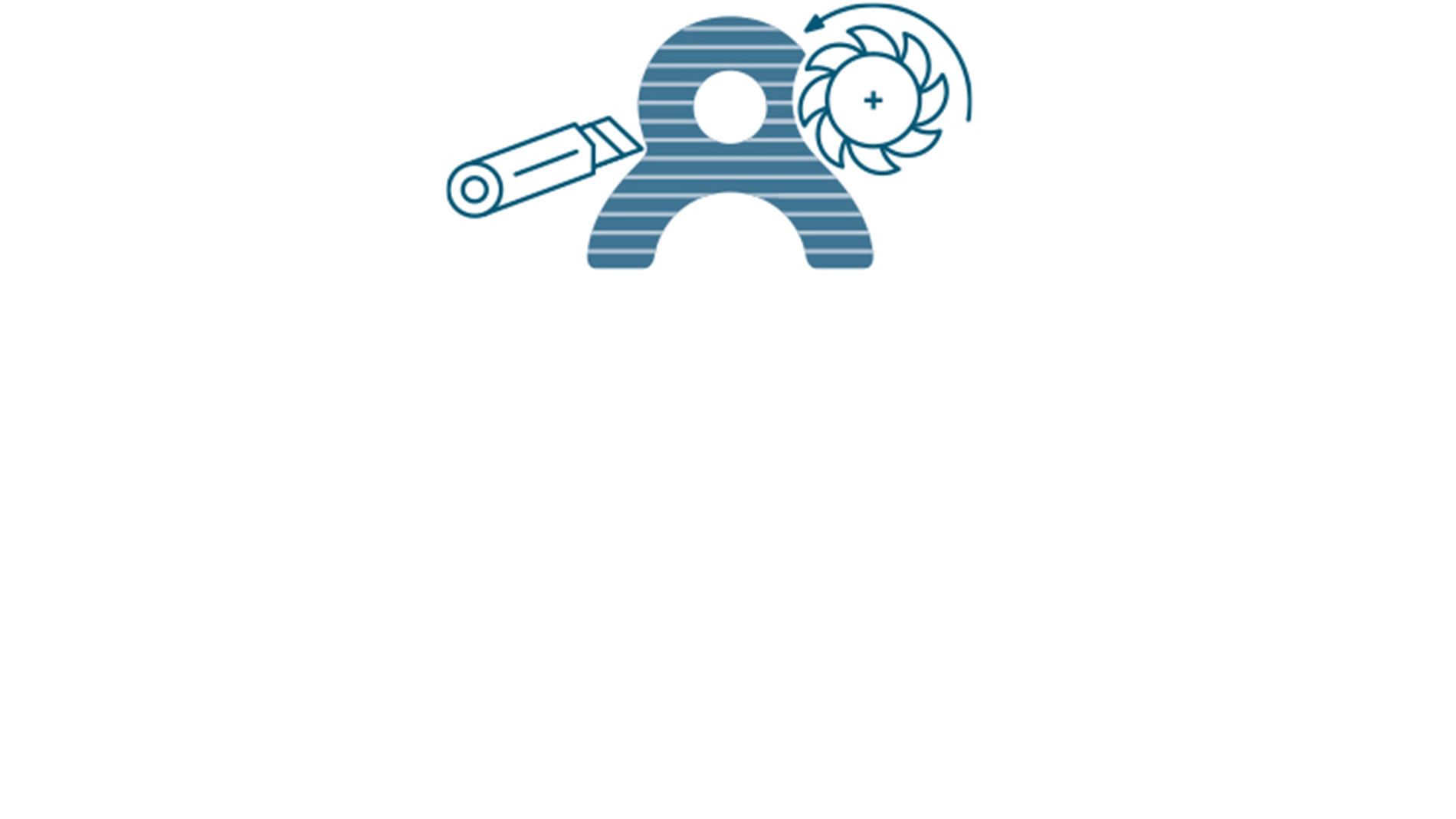
Machining
Machine post-processing can be done after practically all AM processes. It is absolutely essential for metal processes that are not really able to produce geometries that are close to the final contour.
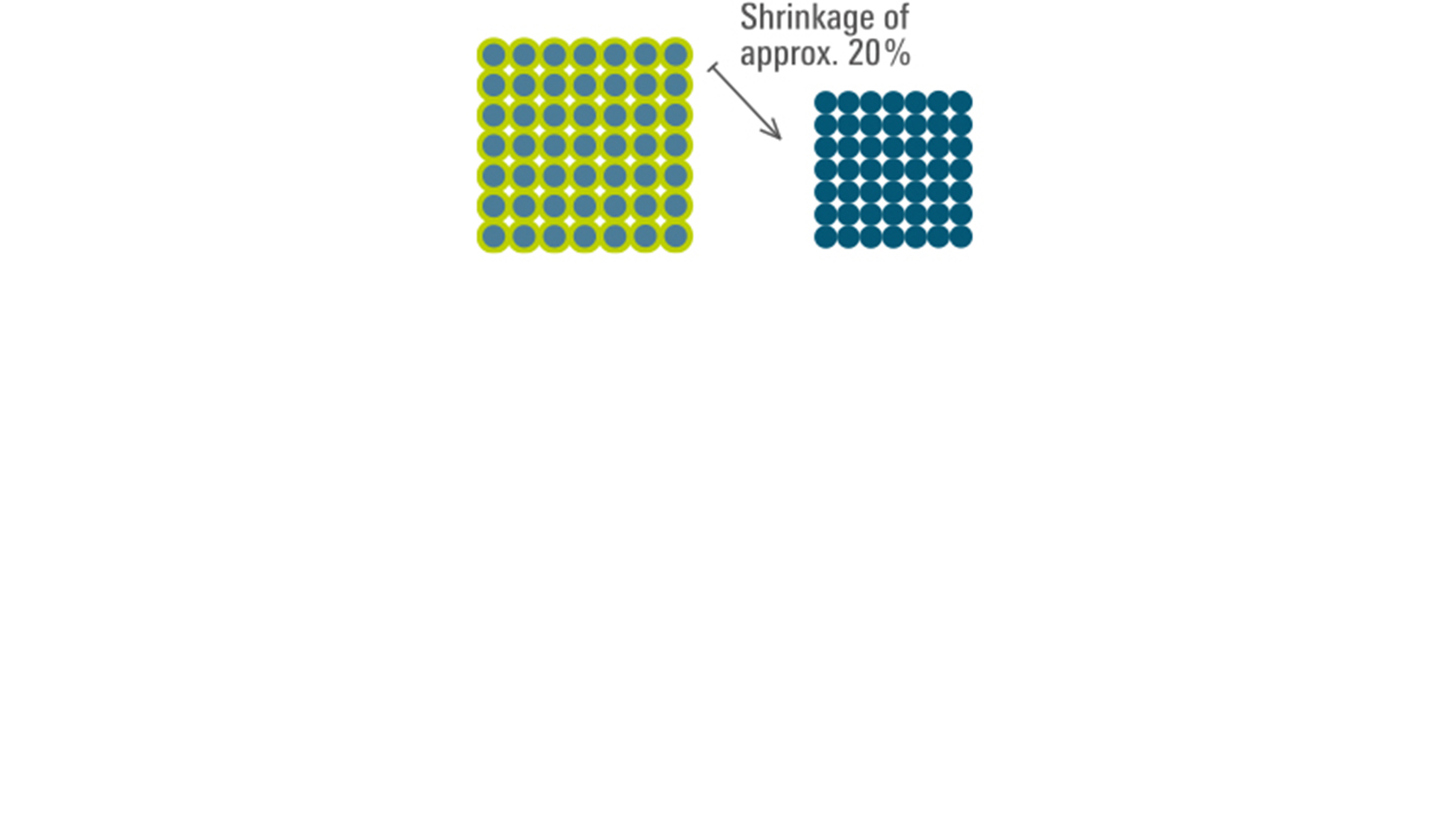
Sintering
Some processes only produce what are known as "green" parts, or blanks. The component itself is not created until the sintering post-process is performed. This method is always associated with considerable component shrinkage.
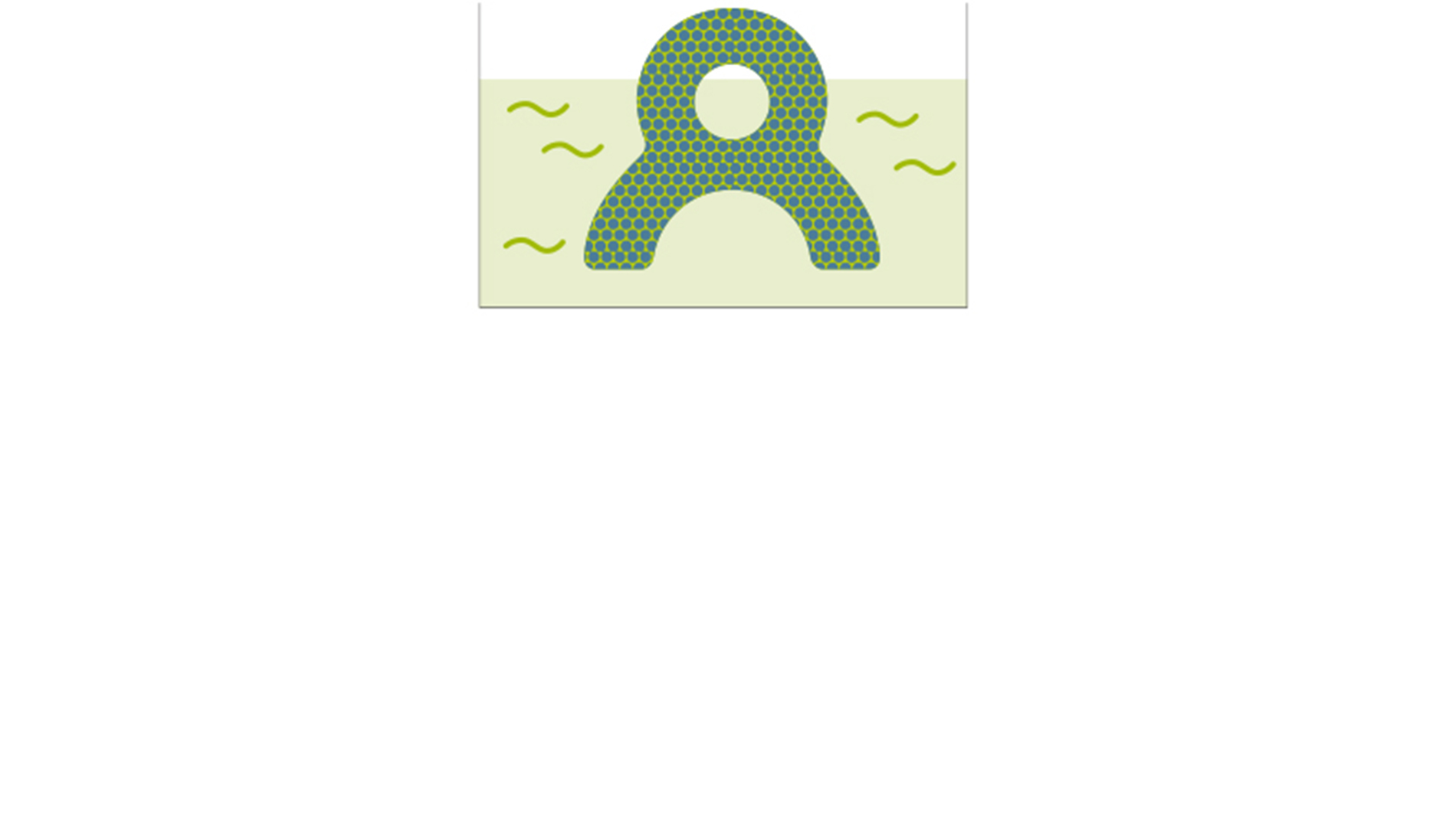
Coating or infiltration
Microporous components are infiltrated or coated with polymers to produce components that are completely gas-tight or liquid-tight.
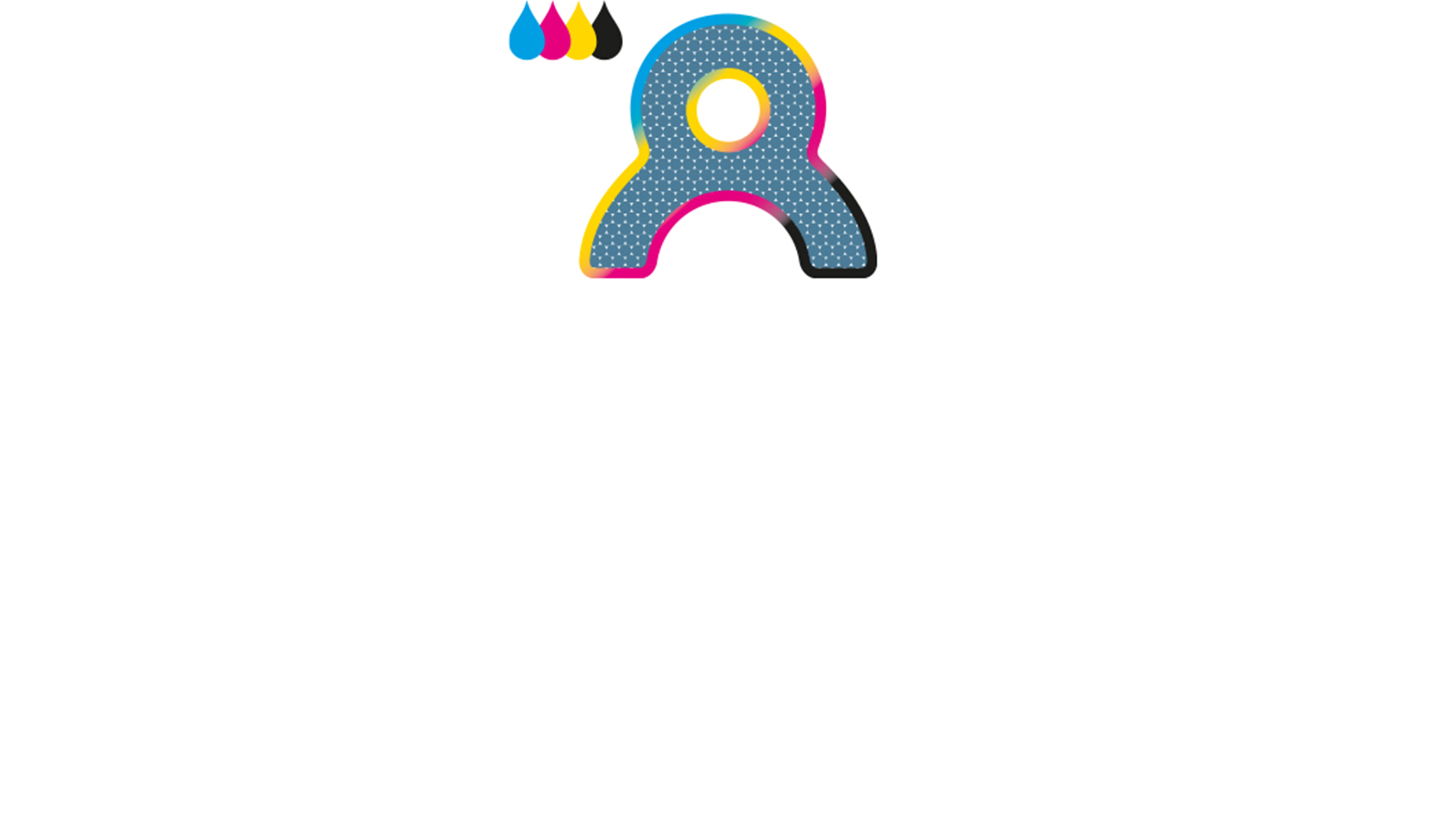
Dyeing
The visual appearance of powder- based polymer components can be vastly improved with a dyeing post-processing step.