1 November 2022
With the GMP300, Grob is presenting its Liquid Metal Printing (LMP) for the production of near-net-shape components for the first time. According to the manufacturer, the machine offers reliable, efficient and cost-conscious system technology with maximum production flexibility for one-off and small-batch production.
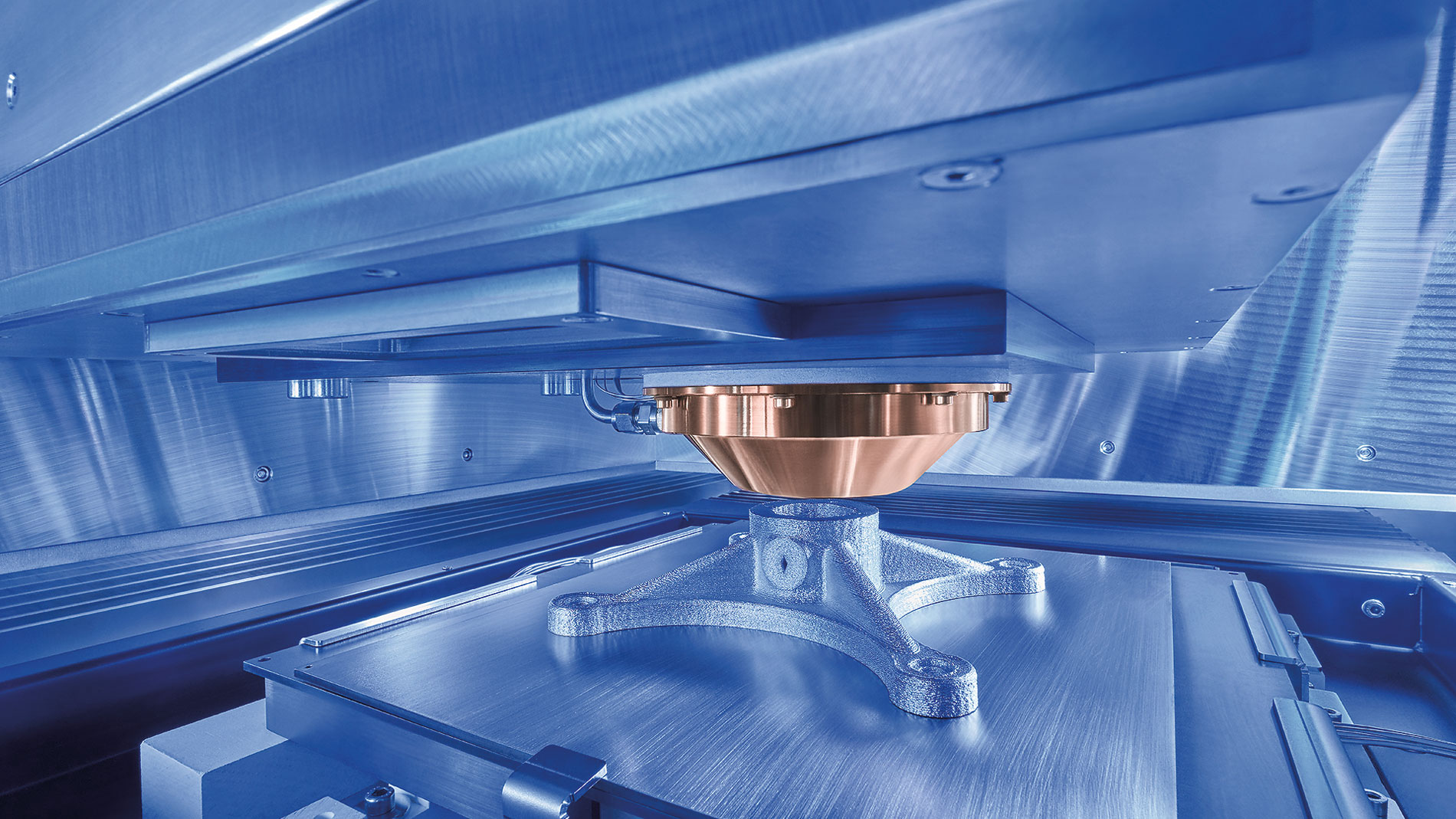
GMP stands for Grob Metal Printing and the 300 for the size of the work area 300x300x300 mm³. The GMP300 is equipped with 3-axis kinematics and offers a maximum axis speed of 30 m/min. The inert atmosphere serves to protect the component from oxidation and thus guarantees consistently good material properties.
According to Grob, the company has developed Liquid Metal Printing (LMP), a forward-looking, economical and at the same time flexible additive manufacturing process that eliminates the disadvantages of traditional, metalworking additive manufacturing processes. The development was sparked by increasing market demand for customized and near-net-shape products.
In the LMP process developed by Grob, the starting material is wire. The LMP process produces a homogeneous microstructure at yield strengths that are equal to or, in some cases, even higher than the values of the starting material. The droplet diameter can be adjusted between 380 µm and 700 µm by using different nozzles. In addition, the print head including nozzle can be changed quickly during the build-up process, as can the build plates between print jobs. At a maximum drop frequency of 500 Hz and a drop diameter of 700 µm, the build rate is up to 320 cm3/h, according to Grob.
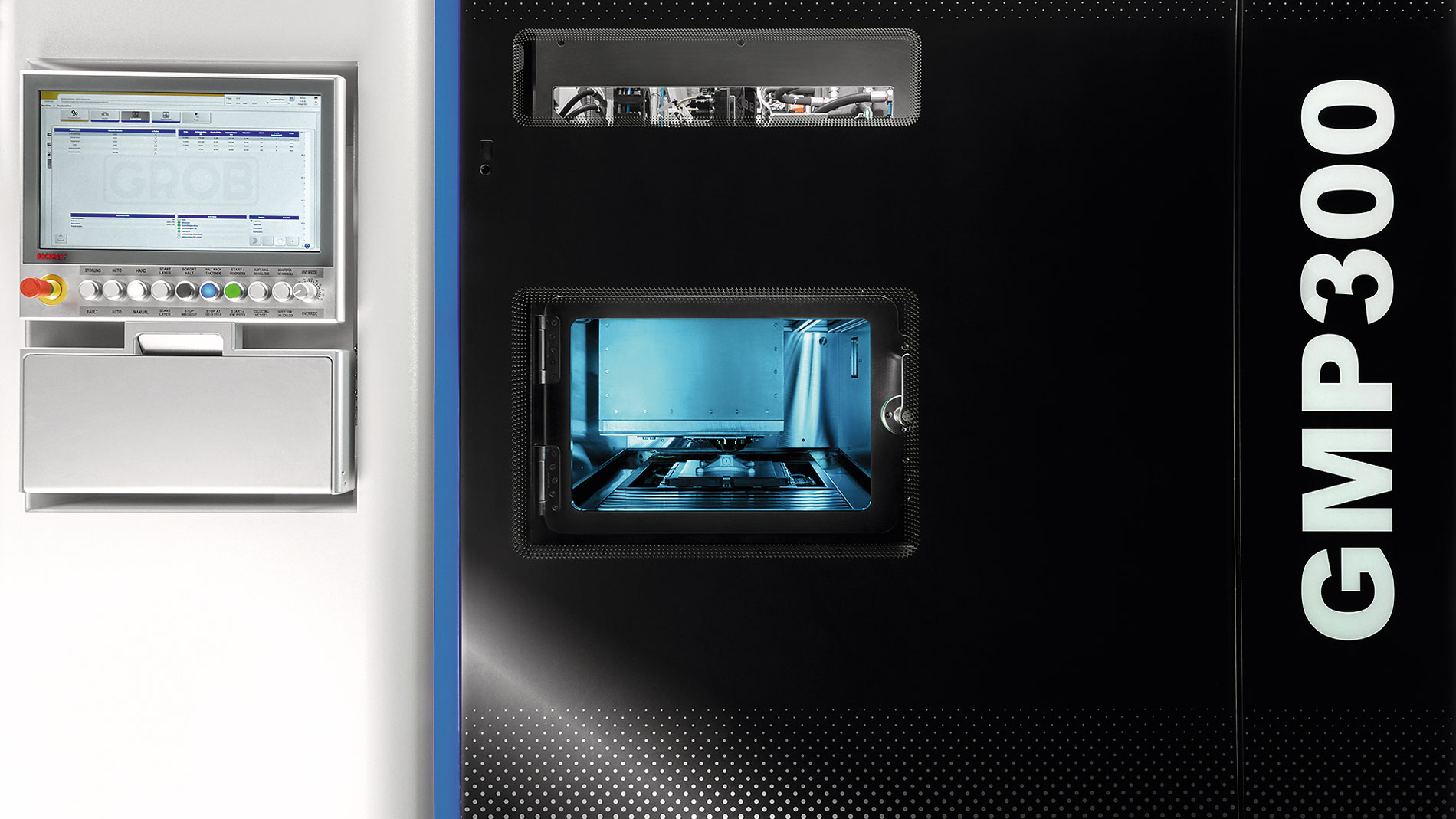
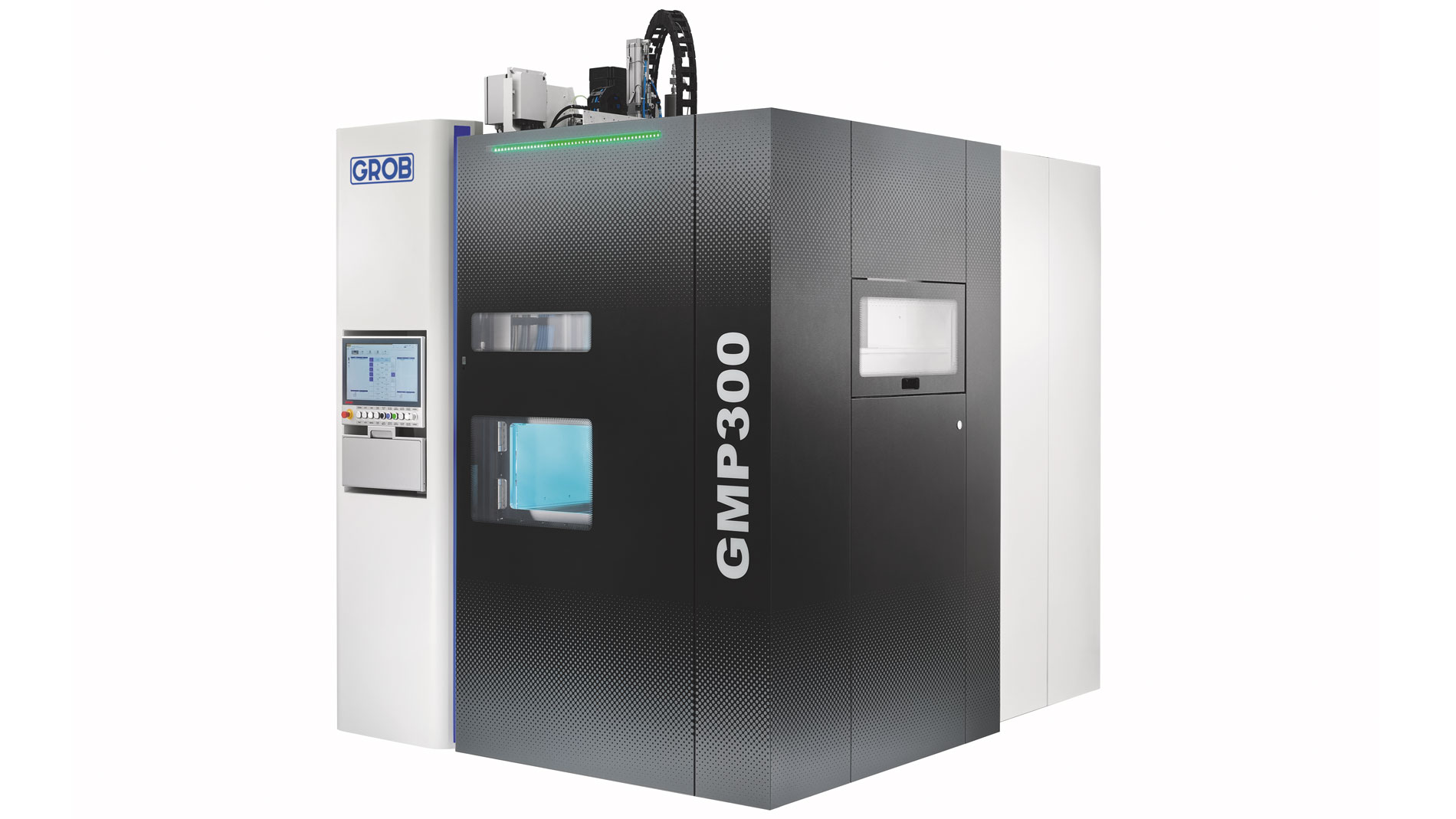
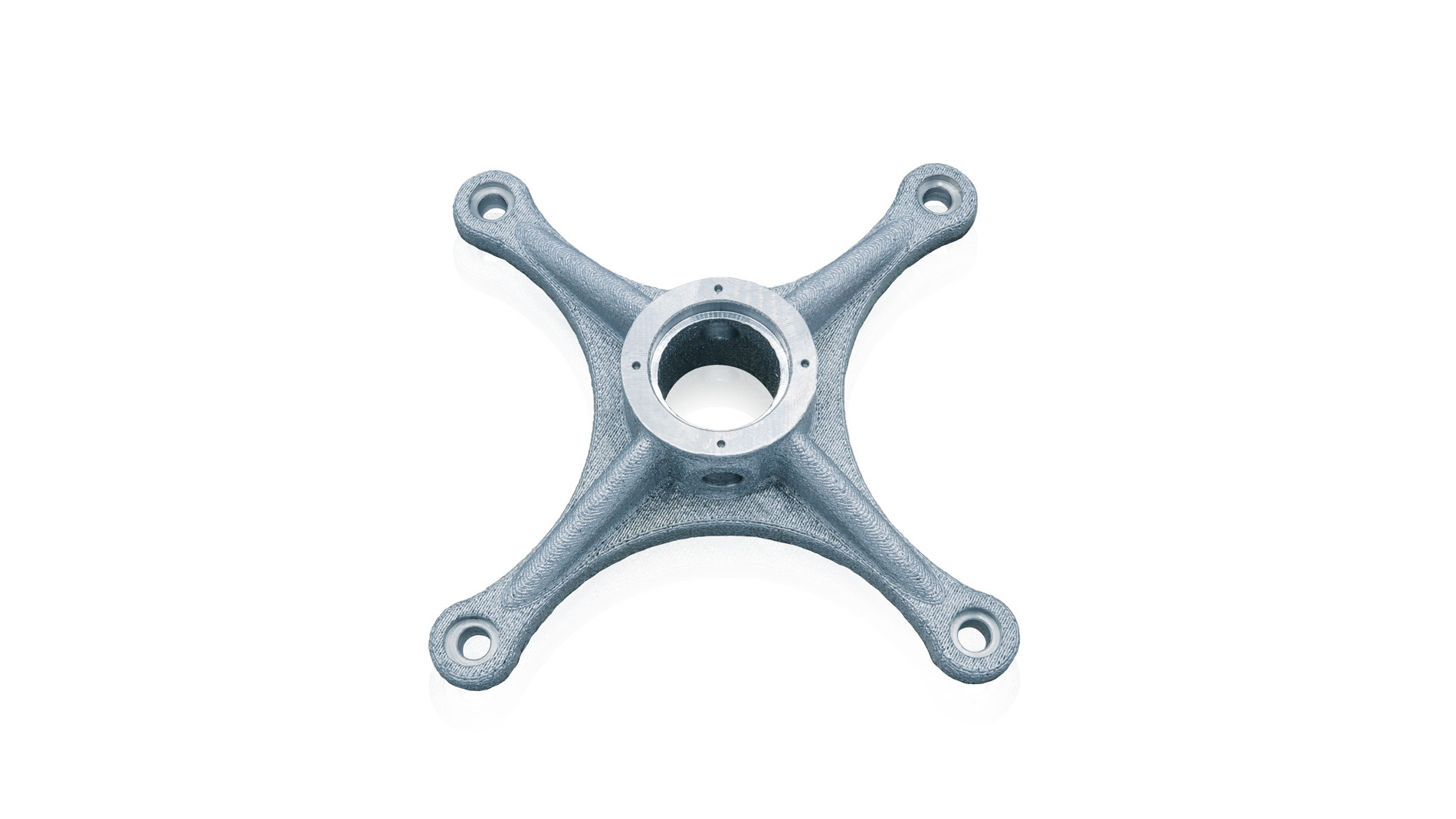
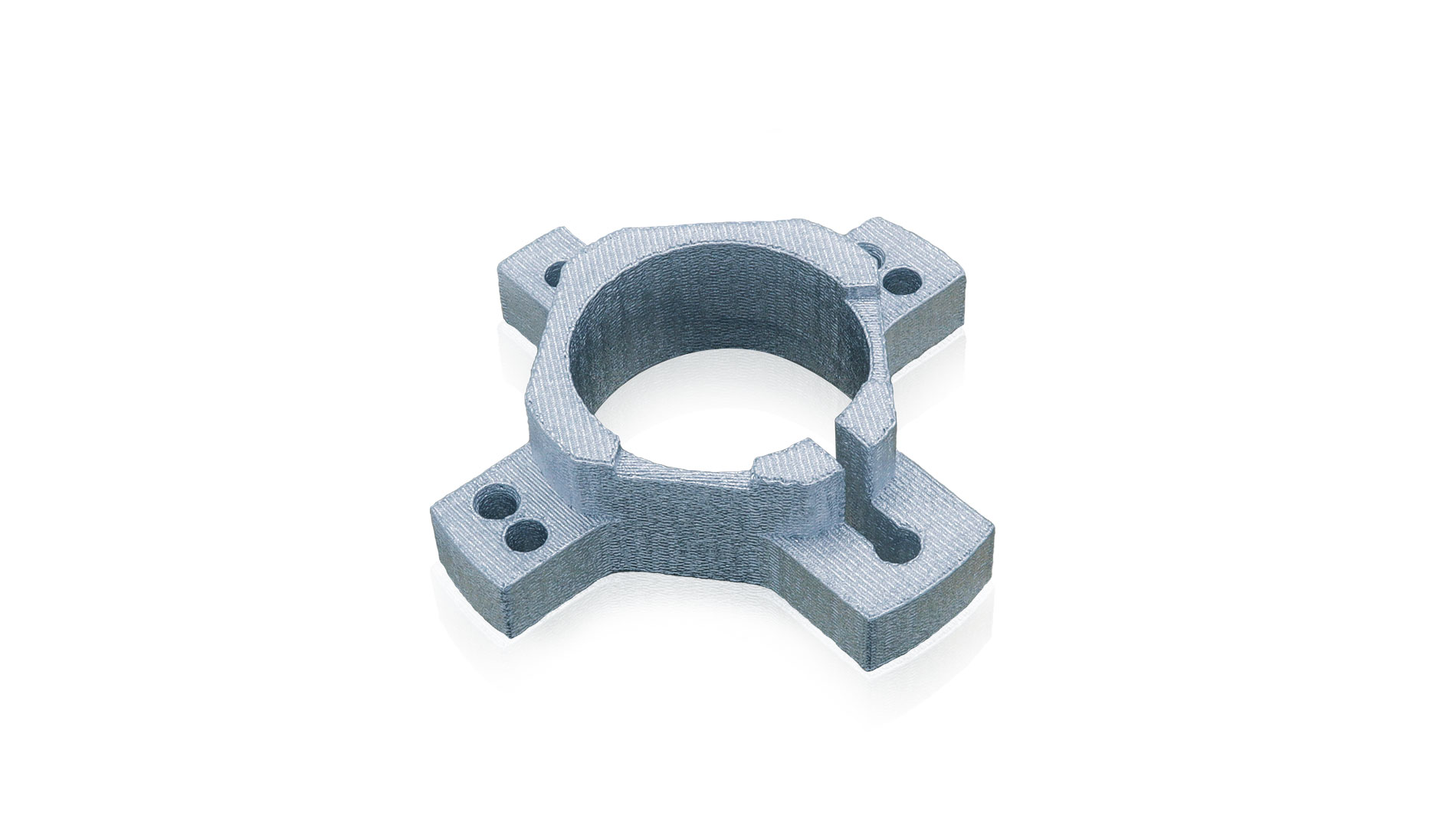
As advantages in comparison to previous AM processes, Grob mentions the higher build-up rate compared to PBF systems as well as a better component resolution compared to current DED processes. Another advantage is simpler operation. "With no powder handling and no need for any beam sources, the systems can be integrated into an existing production line without increased safety precautions," said Dr.-Ing. Johannes Glasschröder, team leader responsible for additive manufacturing at Grob.
Grob-Werke at Formnext 2022:
Hall 11.0, Booth C51
Tags
- Additive Manufacturing
- Formnext News