See who is exhibiting or create your own watch list. Use the filter options to obtain a list of exhibitors for the respective product group.
Lortek S.Coop.
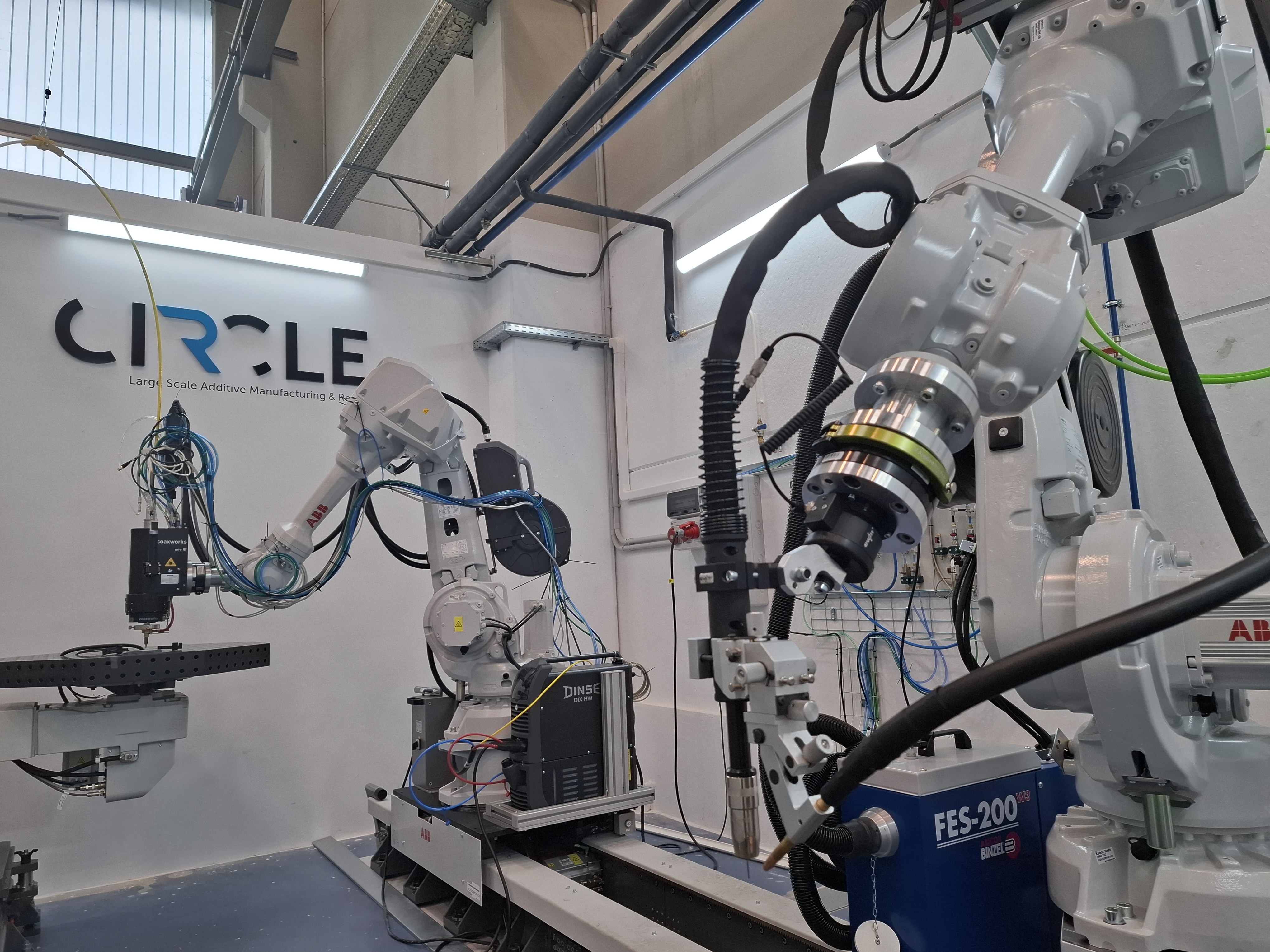
CIRCLE - Large Scale Additive Manufacturing & Repair
Explore product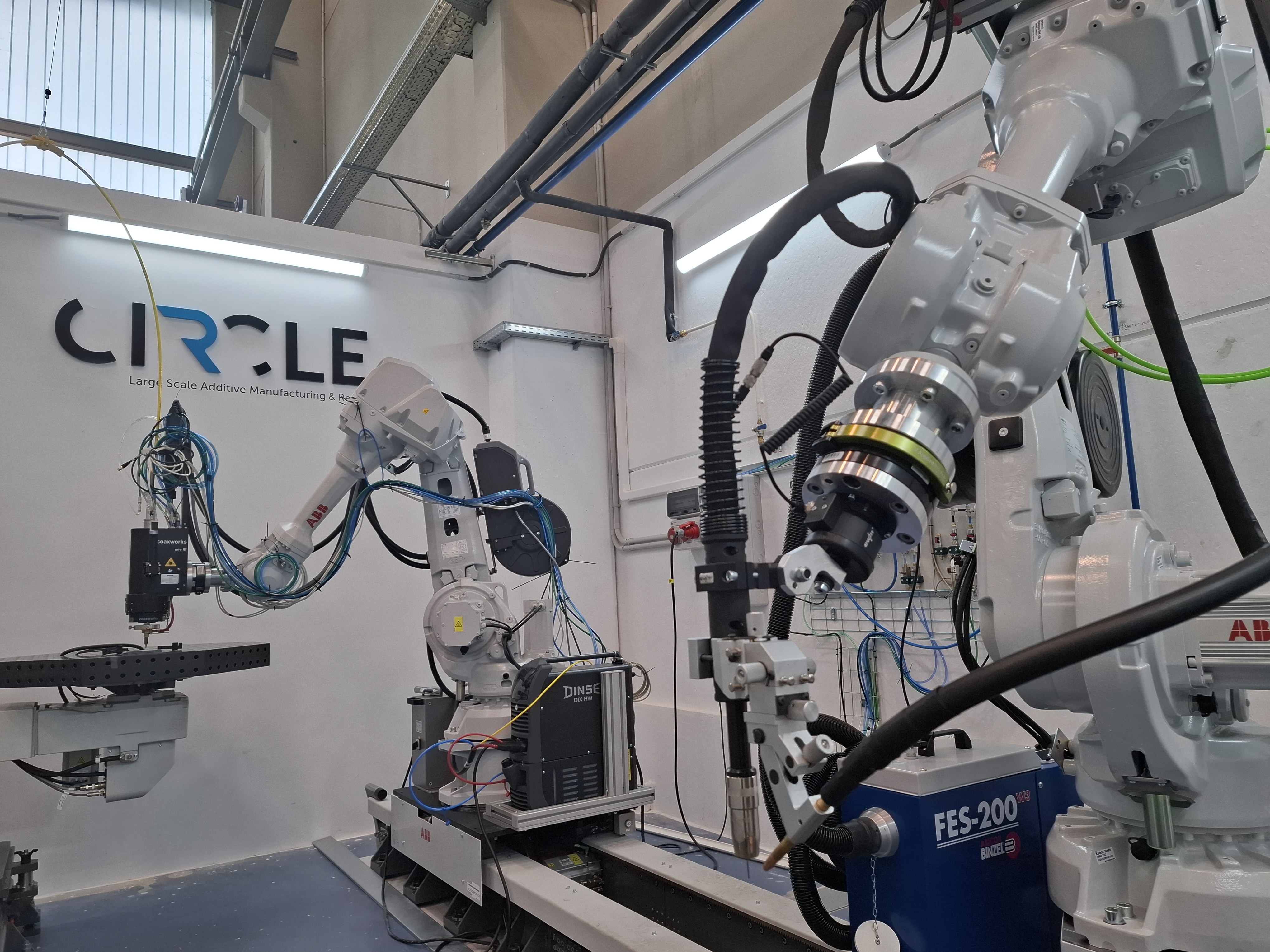
CIRCLE - Large Scale Additive Manufacturing & Repair
Explore product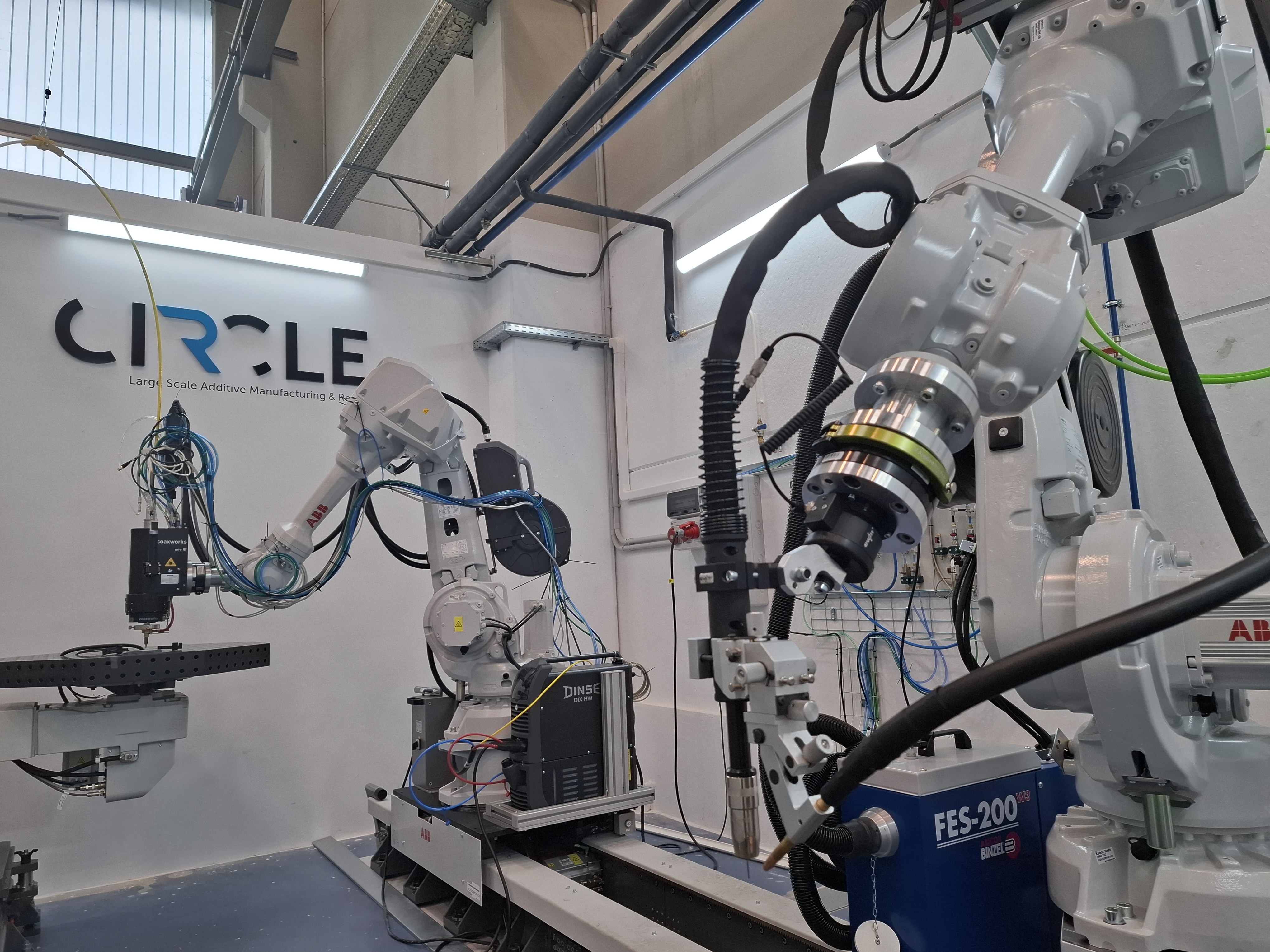
CIRCLE - Large Scale Additive Manufacturing & Repair
Explore productAbout us
Thanks to our detailed knowledge of manufacturing processes, metallurgy and metallic materials, we design products and systems, and research into advanced additive manufacturing and component repair processes, using state-of-the-art software and hardware and integrating digitalisation technologies. We develop solutions throughout the entire value chain, focusing on the needs arising from energy and digital transitions.
DED-Arc Directed Energy Deposition – Arc
Technological solutions:
- Support to configure and integrate portable machine/system/cell arrangements.
- Temperature control between layers for deformation control. • Generation of protective atmospheres to manufacture metallic parts.
- Adaptive trajectory software based on deposited geometry).
- Parameter library for specific materials and industrial applications.
- Redesign and optimisation of part geometry tailored for WAAM process.
Working on:
- Quality prediction systems based on monitored signals and NDT.
- Closed loop monitoring and control for detection and correction.
- Digital twin for real time simulation and data capture.
- Solutions for automatic manufacturing and repair.
- On-site portable repair systems for accessibility.
- Multi-robot manufacturing cell for hybrid DED.
DED-LB Directed Energy Deposition - Laser Beam
Technological solutions:
- Automatic repair methodologies for complex geometries.
- Additive manufacturing of preforms and functional parts.
- Process adaptation to new materials and alloys.
- HMI and Digitisation (data analytics, data visualisation, process monitoring, control and quality) - Flexible Digital Cell.
- Manufacturing of Multi-materials and Functionally Graded Materials (FGMs).
- Exploring DED-LB technology for new challenging applications and hybrid manufacturing.
Working on:
- Quality prediction systems based on data acquired and NDTs.
- High power DED-LB and extreme high-speed laser material deposition (EHLA).
- Processing new and challenging materials (MMCs, Cu, Ti).
- Digital Twin and AI models for DED-LB processes.
- Multimodal monitoring and closed-loop process control.
- Solutions for automated AM and repair processes with robots.
PBF-LB Powder Bed Fusion - Laser Beam
Technological solutions:
- PBF-LB online monitoring system: quality, traceability and repeatability.
- Powder characterisation methodology for quality assessment.
- Tailored mechanical properties through process and heat treatment optimisation.
- Development of new materials for high demanding applications.
- Process automation from printing to final product.
- New designs with complex structures.
- Custom FEM models for distortion prediction.
- Analysis of powder reuse and its impact on part quality.
Working on:
- Monitoring systems and closed loop control for quality assessment.
- Laser beam shaping to optimise material processability.
- Free-float concepts to reduce quantity of supports.
- Development of digital twins for real-time simulation and data acquisition.
- Components for sustainable mobility and hydrogen storage.
- Development of an hyperconnected and smart process platform.
FSAM Friction Stir Additive Manufacturing
Technological solutions:
- Design of tailored Al alloys for solid state processing.
- Effective repair methodologies for materials difficult to weld.
- Preform design and manufacturing that can be machined to their final shape.
- Implementing accurate process simulations to evaluate and predict residual stresses and deformations.
- Coating development for materials under extreme conditions.
Working on:
- Hybrid manufacturing combining FSAM and machining for enhanced production capabilities.
- Implementing temperature control to ensure high-quality parts during the FSAM process.
- Developing quality prediction systems based on real-time process data and monitoring.
- Advanced FSAM process simulation for the customisation of alloy properties, tailored and optimised for use in specific applications.
- Advanced material characterization, investigating material microstructure at different scales to understand multiphysic properties.
ADVANCED EQUIPMENT AND SOLUTIONS
Offering a comprehensive and unique range of technological infrastructures and capabilities for advanced research, design, testing, development of metallic additive manufacturing projects and applications.
CIRCLE – Large Scale Additive Manufacturing and Repair
Multi-robot single cell for fast additive manufacturing and repair of high value added and large components (shafts up to 3 metres long and moulds/dies up to 2.5 m2 surface area), combining 3d scanning and directed energy deposition additive manufacturing processes with laser, arc and metal wires (Hybrid DED concept).
Multi-material, flexible and fully digitised AM cell based on laser and powder (DED-LB)
Directed Energy Deposition -Laser Beam for development of new “LMD and Laser Cladding” Additive Manufacturing applications in different flexible machine/kinematic architectures, for new materials, advanced process monitoring, control and simulation, to offer robust and efficient repair and manufacturing route solutions for the industry.
Robotic and Cartesian LMD and Laser Cladding production, with the state of the art in sensors, data acquisition platform, monitoring and process control systems.
AM robotic cell based on High Deposition Rate with electric arc and wire (DED-ARC)
Directed Energy Deposition -Arc for development of “WAAM” Additive Manufacturing processes and applications. Manufacturing, repair, and hybrid production of large components, supported by digital solutions to ensure quality. Research in advanced deposition technologies, new materials, process control, non-destructive inspection, and simulation to optimise manufacturing and minimise defects.
PBF-LB/M Laboratory for the integral development of technological solutions in Powder Bed Fusion Metal Additive Manufacturing
Specialised technology solutions for additive manufacturing, focus on new materials, complex designs, tailored properties, and quality monitoring. Optimisation and characterisation of powder compositions, FEM-based simulations for distortion prediction, data-driven approach to PBF-LB processes, defect detection systems and post-processing improvements, to ensure quality and repeatability.
MCP Realizer 250, SLM 280HL, SAMYLABS Alba 300, Renishaw RenAM 500Q (Multilaser with melt pool monitoring system).
Advanced Software
For topological optimisation, design, simulation, manufacturing process preparation, and quality assurance.
Inspire, Optistruct, Tosca, 3D Experience, Magics, QuantAM, Sulis, InfiniA Spectral, etc.
Material Characterisation Laboratory
Particle size distribution, powder porosity analysis, powder flowability and spreadability.
Porosity size distribution, density, assessment of defectology, fabrication of specimens to determine oxygen content in manufacturing (reactive materials parts), microstructural analysis, mechanical characterisation, determination of manufacturing roughness.
Granudrum, FESEM equipped with EBSD system, PC/Optical, etc.
More about us
Special Interests
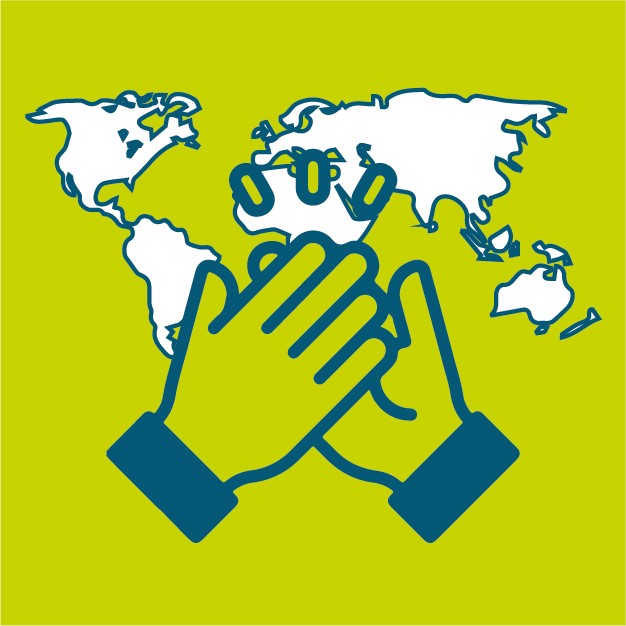
Keywords
- DED-Arc | WAAM Wire Arc Additive Manufacturing
- DED-LB | LMD Laser Metal Deposition
- PBF-LB | SLM Selective Laser Melting
Our Products
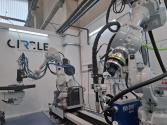
CIRCLE - Large Scale Additive Manufacturing & Repair
Multi-robot single cell for fast additive manufacturing and repair of high value added and large components (shafts up to 3 metres long and moulds/dies up to 2.5 m2 surface area), combining 3D scanning and directed energy deposition additive manufacturing processes with laser, arc and metal wires (Hybrid DED concept).
FSAM, Friction Stir based Additive Manufacturing
A solid-state process that enables the manufacturing and repair of complex parts, particularly those made from materials that are challenging to weld.