See who is exhibiting or create your own watch list. Use the filter options to obtain a list of exhibitors for the respective product group.
GRAFE GmbH & Co. KG
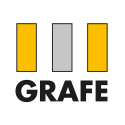
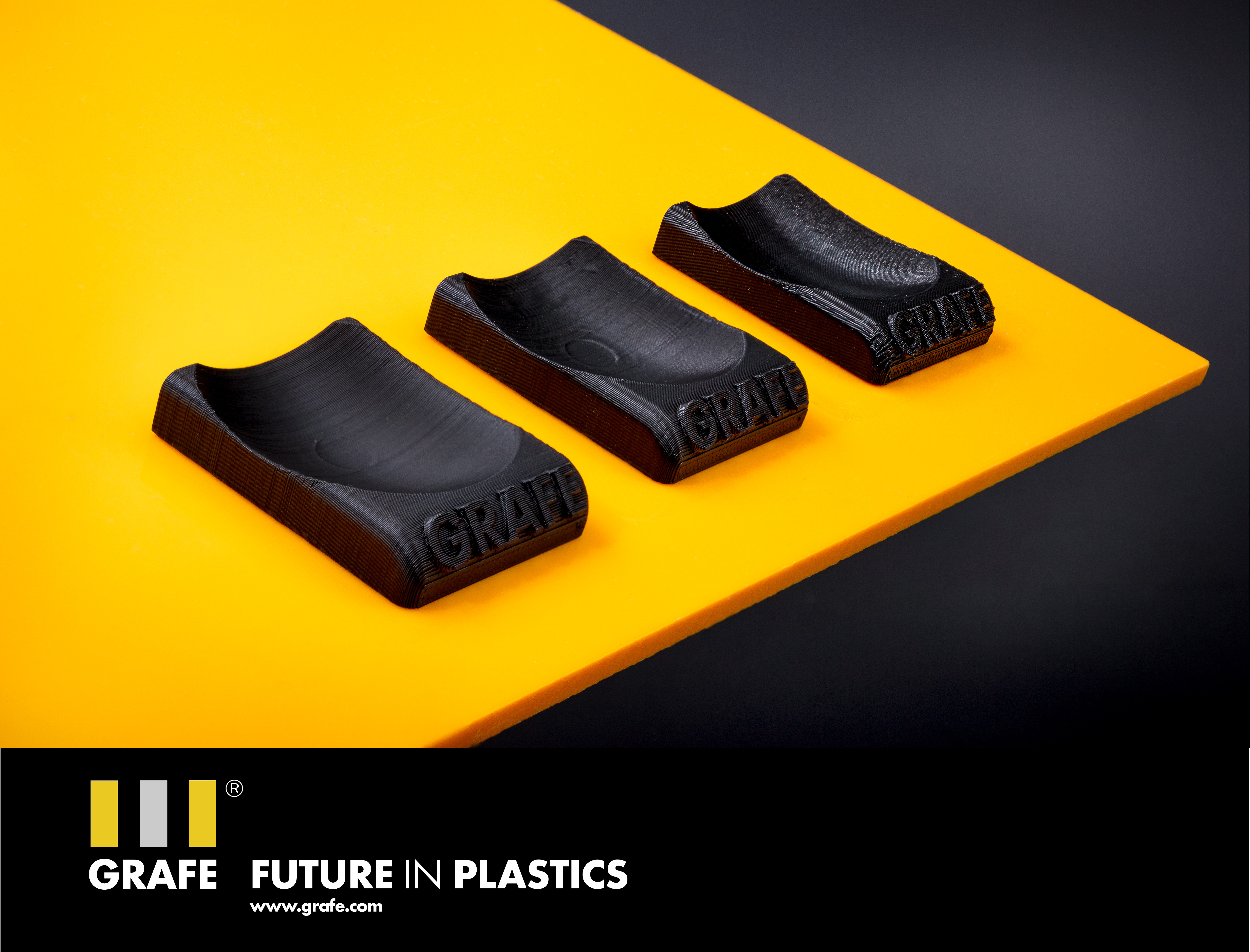
Matting agent
Explore product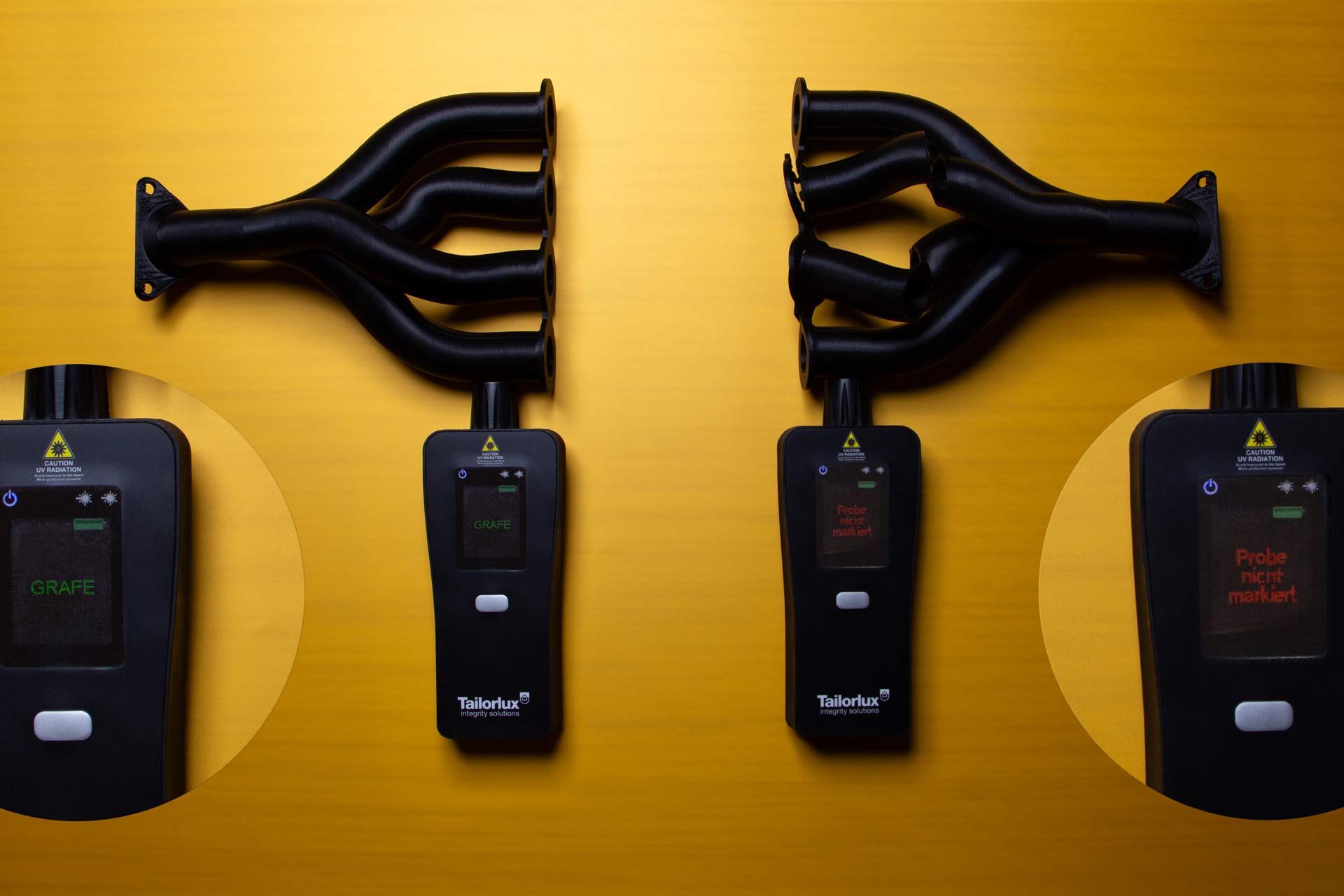
Filament identification directly in the plastic for originality check
Explore product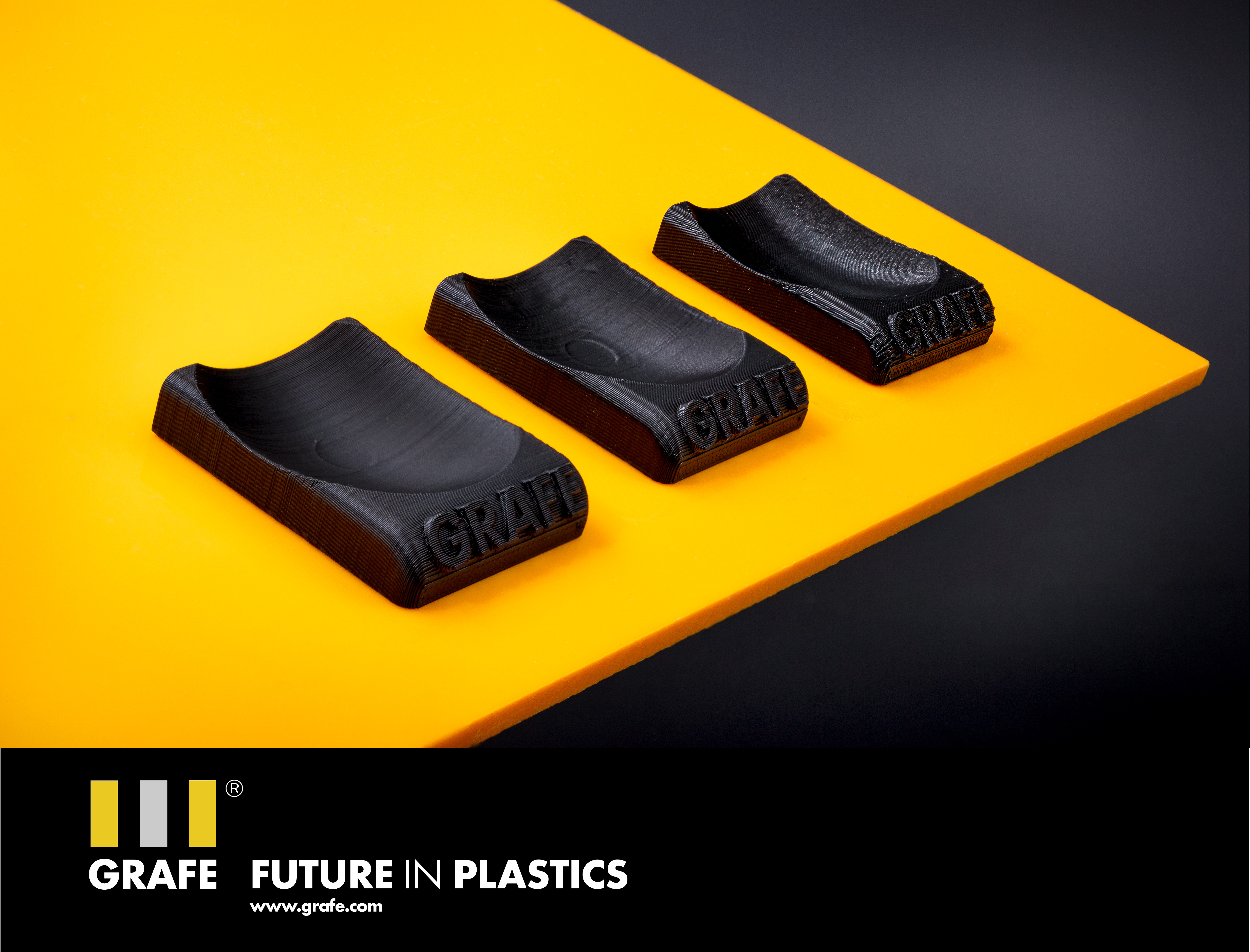
Matting agent
Explore product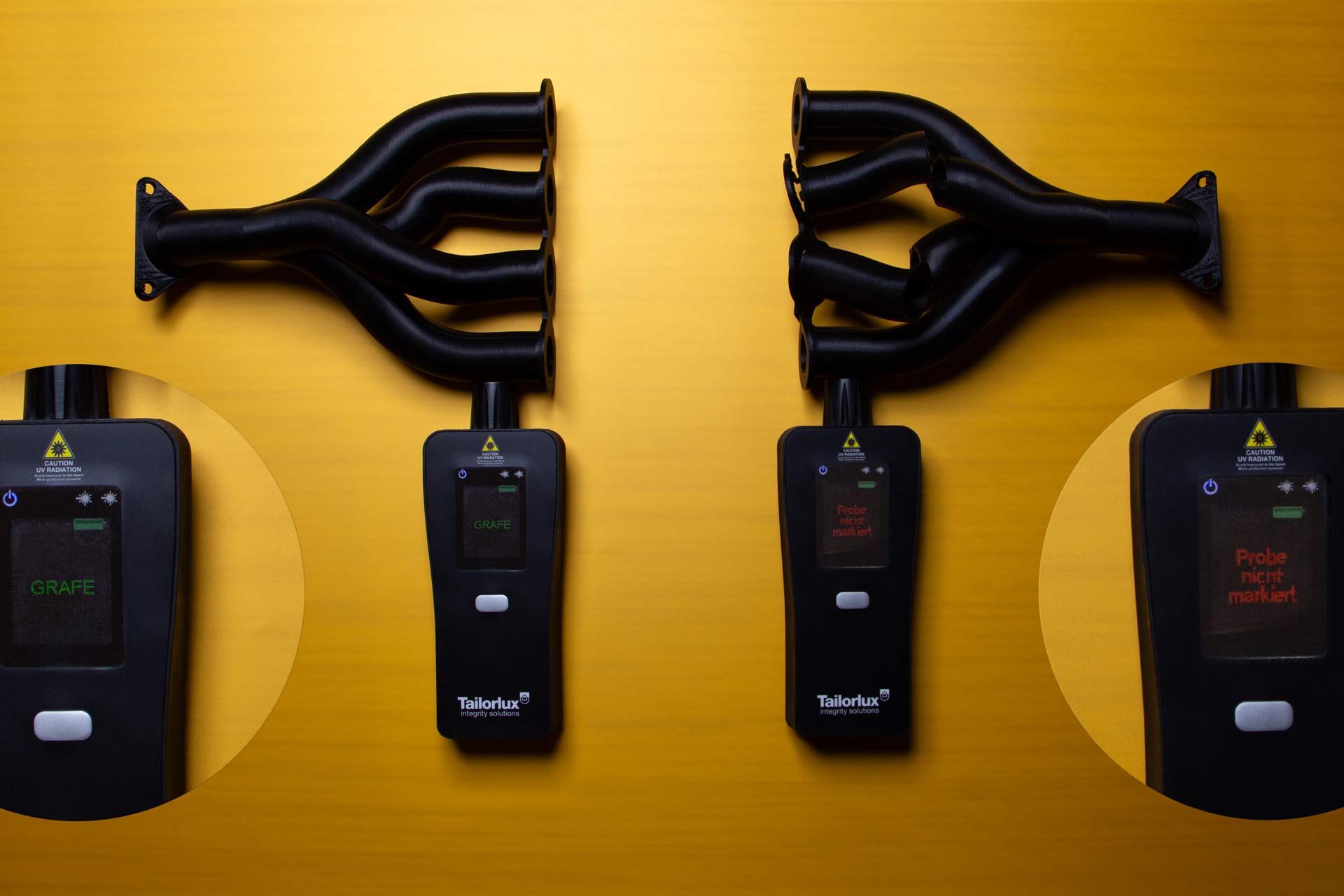
Filament identification directly in the plastic for originality check
Explore product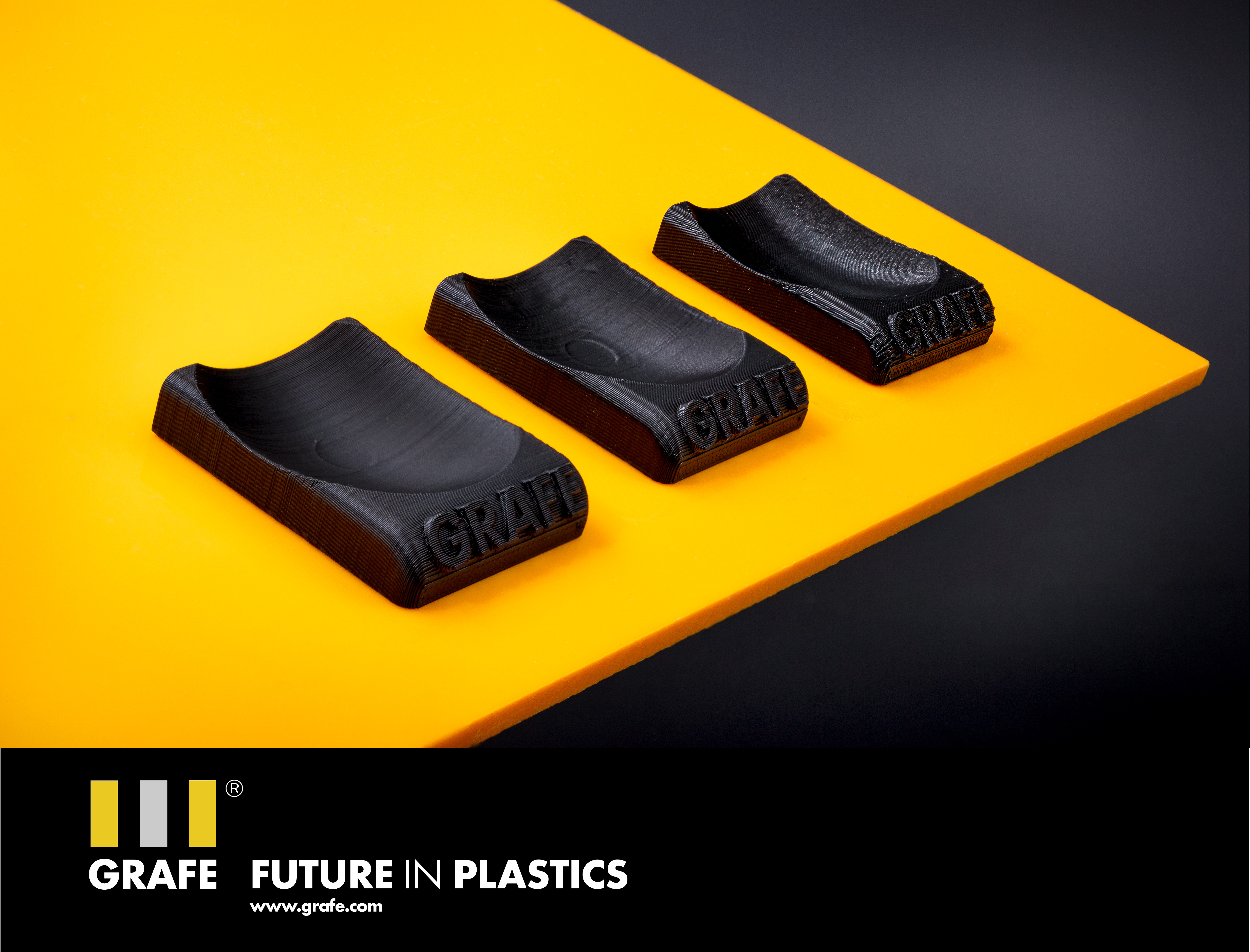
Matting agent
Explore product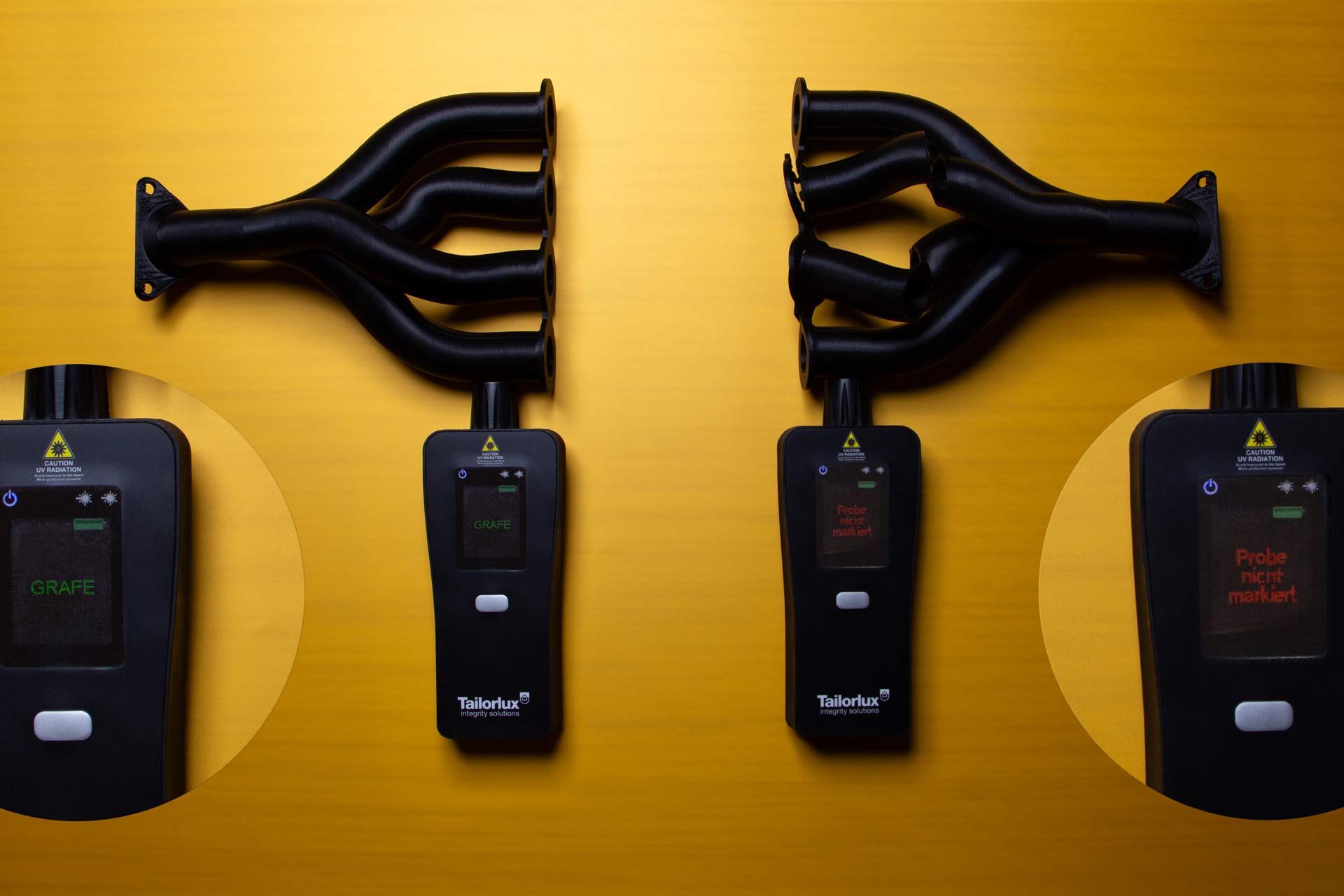
Filament identification directly in the plastic for originality check
Explore productAddress
GRAFE GmbH & Co. KG
Waldecker Str. 21
99444Blankenhain
Germany
Telephone+49 36459 450
Fax+49 36459 45145
Discover more from us
Follow us on
About us
For more than 30 years, we have been committed to making the world more colorful every day – working together, with the courage to create color and function.
As one of the leading German manufacturers of masterbatches, we not only produce color masterbatches, additive masterbatches and functional plastic compounds – we are the embodiment of German research, engineering and entrepreneurship, and our products reach satisfied customers in more than 60 countries.
GRAFE stands for quality, customer orientation and innovation, and at our Blankenhain site we have one of the largest research and development departments in the entire industry, which develops the latest technologies to modify plastics and provide them with intelligent functions.
Certified according to:
- DIN EN ISO 9001:2015
- IATF 16949:2016
- ISO EN 50001:2018
Keywords
- Masterbatch
- Additive
- Compounds
- Filamente einfärben
- Effektfarben
Our Products
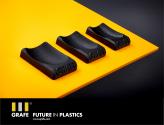
Matting agent
Shiny stores with less gloss
The continuous development of the matting agent for 3D printing is characterized by significantly improved matting effects compared to its predecessor and substantially higher print quality. GRAFE, headquartered in Blankenhain, Germany, has tested the product extensively with PETG material. “The trial phase has been completed, initial sampling is underway, and now commercialization begins,” said Lars Schulze, Head of Color Development and Material Sciences, who is overseeing the project. Possible applications include living room elements such as lamps, covers, or switches, as well as other applications in the home.
According to him, subjective examinations using test specimens and metrological analyses show a clear and verifiable reduction in gloss compared with the previous development. In tests at an angle of 60 degrees, the measured value for black-colored PETG was reduced from 8.8 with the help of the old matting agent to 2.6 and even to 1.3 thanks to the new product, the expert reports.
“We can therefore speak with a clear conscience here of a halving of the gloss level compared to the predecessor,” assures the project supervisor. He adds that the matting agent can be metered at 7.5 percent and combined with any color batch or compound – without any significant effect on the color. “This is an important property,” according to Schulze.
The matting effect is created by diffuse light scattering on the surface of the plastic, the expert said. Customers benefit from a velvety feel with corresponding components. The undesirable visual layer buildup, which often occurs in 3D printing, is barely visible. “The material almost looks like it was cast from a single mold,” Schulze reports. Tests have also shown no adverse effects on the UV resistance of the plastic, he adds.
“3D printing is a rapidly growing market for which we do extensive development work and offer a variety of solutions,” Schulze explains, pointing out that GRAFE works with all major filament manufacturers. PETG stands for PET, which has been processed with glycol. It enjoys great popularity in 3D printing. The solid and resistant material features good thermal stability and robust mechanical properties.
In addition, the matting agent has already been tested for PLA and PC, reports Schulze, who also announces trials with other materials. In addition, he says, trials in injection molding and extrusion processes have also shown significant effects in reducing gloss levels. “We would like to invite our customers to conduct further tests on their premises and see the matting effect for themselves,” the expert says.
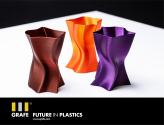
Infinite color variety for 3D printing
GRAFE develops varied silk gloss effect
With a broad spectrum of infinite color variations, GRAFE, Blankenhain, is bringing variety to the market for 3D printing applications and presenting this to its customers with a box at K 2022. This contains ten basic colors, of which a white polymer blend acts as a carrier. "The silk effect or gloss only really becomes visible in 3D printing," explains Lars Schulze, Head of Color Development and Material Sciences. "With the colors, we offer a tested base, the so-called silk effect with corresponding good printability and high gloss level." The project was specifically developed to reproduce this noble gloss effect. The selection of certain pigments avoids matting, which leads to the highest gloss level.
Two color combinations in a shapely vase look provide a preview for design inspiration. The two color models are presented in a high-quality box. A color table with 19 mixing examples is intended to serve as a stimulus among the infinite color combination possibilities and to represent the most diverse demands of users. It serves as orientation and should make it possible to meet customer requirements quickly. In addition, the customer receives corresponding dosing suggestions. However, the presentation samples only provide inspiration for users, because there are no limits to color fantasy with the basic colors and the user can mix his colors creatively and achieve individual color shades.
"We give our customers the opportunity to become imaginative themselves. Up to now, there has only been a small choice of colors for high-gloss filaments on the 3D printing market. We want to change that with our expertise in coloring plastics and offer a basis for customisation with our masterbatch," explains Schulze. GRAFE has its own filament extruder and 3D printer in house and can thus produce and test appropriate filaments itself. "In this way, we are able to try out our own developments. This significantly reduces development times, as the time-consuming testing process at the customer's premises is no longer necessary," says Schulze.
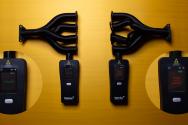
Filament identification directly in the plastic for originality check
In cooperation with Tailorlux, GRAFE launches a masterbatch for the identification of materials in industrial 3D printing
The GRAFE GROUP, Blankenhain, has developed a masterbatch for the identification of materials in industrial 3D printing. „This means that the authenticity of licensed materials can be reliably and unmistakably determined already in the filament processed in this additive manufacturing process“, explains Lars Schulze, Head of Colour Development and Material Sciences. At present, he sees the main areas of application as prostheses in medical technology, but also system-relevant machine or automotive parts that have to withstand warranty or recourse claims. Nevertheless, other sectors such as furniture, electronics, or consumer goods could also be interesting for the originality check.
„In the future, more and more products and spare parts will come from 3D printers. Already today, their number is increasing rapidly in private and industrial use. If one now imagines that spare parts for licensed products are printed from inferior and untested material, recourse claims or warranty claims would be forfeited and, in the worst case, property damage or personal injury would occur“, Schulze reports. This is where GRAFE's idea comes in: „We work a marker into the filament, which can be used to check whether the correct material has been used. It is permanently in the component and cannot be removed. Due to its nature, the marker offers perfect protection against counterfeiting and proof of originality.“
As an exclusive development partner, GRAFE relies on the security pigments from Tailorlux. The company also supplies the matching Tailor-Scan 4 hand-held measuring device, onto which a reference file set to the safety marking is loaded. It then indicates whether the respective marking is present or not. „The operation is very straightforward. The originality of the plastic used can be checked directly from the filament to the component - even through glass or foil packaging“, explains the expert. Furthermore, certification laboratories could also check the material. The inspection electronics to be used can also be integrated directly into an existing 3D printing system, apart from the hand-held scanner!
Schulze points to the significant basic idea with which the safety principle can be consistently applied when testing the filament takes place directly in the printing unit. However, this must be integrated by the manufacturers of the 3D printers. „When the spool is inserted, a sensor in the printer can check the safety markings in the filament. Printing starts only when it is ensured that the material is the right one. Unlike the principle of colour printers, which use electronics to determine whether the original colour cartridge has been inserted, the 3D printer can directly check the material” „Our solution is already developed and works“, says Schulze. So far, the marker has mainly been used for PLA and PETG (glycol). However, it can also be used in PA and PC. There is no influence on the colour. Due to a wide selection of markers, almost any plastic can be equipped, he assures. „The batch dosages are comparatively low and can be realised from one percent. The colour has the greatest influence. Components coloured with CarbonBlack require a slightly higher dosage than others. Carbon fibres also influence the result. Ultimately, it can be said that each filament can be marked with a maximum dosage of three percent.“
GRAFE is currently looking for industrial partners to develop appropriate products or printers. According to the Head of Colour Development and Material Sciences, the costs for marking depend on the desired protection. „A basic marker that is not developed specifically for a company, an industry, or a particular product is comparatively cheap. A solution that can be used worldwide exclusively for only one specific product is therefore more cost-intensive“, says Schulze.