Text: Thomas Masuch; Fotos: Gienanth — 15.05.2021
Der Wandel in der Automobilindustrie in Richtung Elektrifizierung betrifft kaum eine Branche so stark wie die Gießerei-Industrie. Derzeit werden noch mehr als die Hälfte der gegossenen Metallteile Deutschlands in Straßenfahrzeugen verbaut – bei künftigen Elektrofahrzeugen werden viele aber nicht mehr benötigt. Zwar bietet die E-Mobilität auch neue Geschäftsmöglichkeiten, doch "in Zukunft wird es in der Gießereibranche nicht genügend Alternativgeschäft für alle geben", prognostiziert Simon Geib, Head of Project Management & Business Development der Gienanth Group GmbH. Das traditionsreiche Gussunternehmen aus dem rheinland-pfälzischen Eisenberg hat deshalb seine Strategie bereits an die neuen Herausforderungen angepasst und könnte damit einen zukunftsweisenden Weg für die Branche vorzeichnen. Der 3D-Druck von Sandformen spielt dabei eine wichtige Rolle.
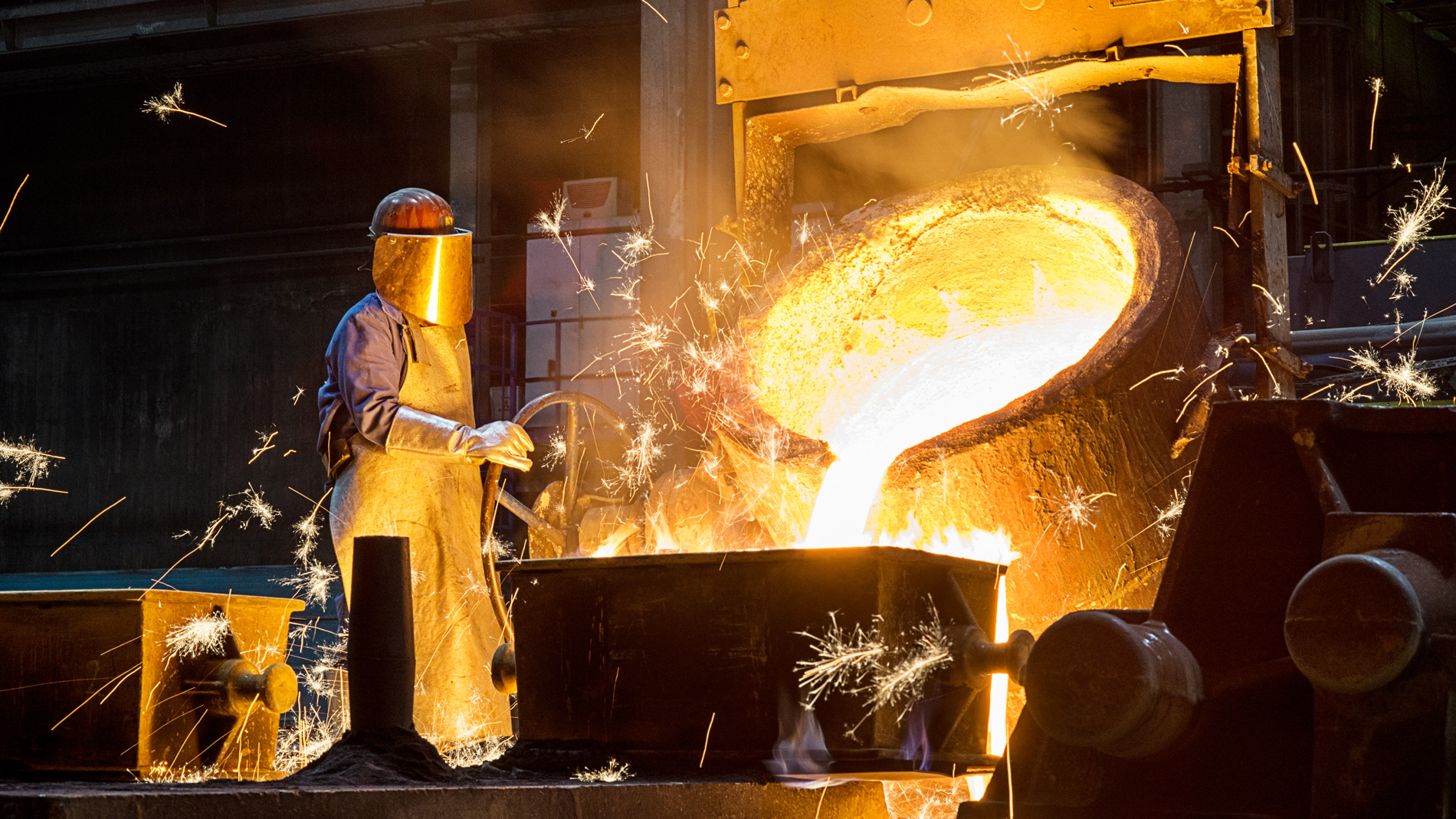
Bei E-Autos werden im Antriebsstrang nur noch rund die Hälfte der Bauteile eines Verbrennungs-Pkw benötigt. "Je mehr die E-Mobilität an Bedeutung gewinnt, desto mehr Überkapazitäten entstehen. Vor allem für die Gießereien, die zu einem sehr hohen Anteil die Automobilindustrie beliefern, wird die Zukunft eine echte Herausforderung", so Geib. Im Moment sei diese Entwicklung noch nicht ganz im Markt angekommen, und auch das Ersatzteilgeschäft werde die Effekte in den nächsten Jahren noch etwas abmildern. "Doch langfristig wird es eine natürliche Sondierung im Gießereimarkt geben, und Marktteilnehmer, die ausschließlich Teile für Verbrennungsmotoren liefern, werden unweigerlich aus dem Markt ausscheiden."
Die 1735 gegründete Gienanth Group ist mit einem Automotive-Anteil von 20 bis 25 Prozent von der Entwicklung eher moderat betroffen, hat sich strategisch aber bereits so aufgestellt, dass verstärkt Produkte in den Vordergrund rücken, die nicht mit dem Antriebsstrang eines Verbrennungs-Pkw verbunden sind. Gleichzeitig beschäftigt sich die Eisengießerei mit den Möglichkeiten von additiv gefertigten Sandformen und Sandkernen (Kerne sind der materialverdrängende Teil einer Form) und nimmt dabei vor allem neue Bauteil-Designs und kleinere Stückzahlen in den Fokus.
"3D-Druck ist ein Werkzeug, das das Engineering auf eine neue Ebene hebt."
EFFIZIENTERE VERBRENNUNG
Mit dem Ziel, Großmotoren noch effizienter zu machen, unterstützt Gienanth als Gießereipartner den Motorenentwickler AVL List GmbH aus Österreich in einem Forschungsprojekt. Die Verbrennung in den tonnenschweren Aggregaten, die beispielsweise in der Marine und oder als Stromaggregate Verwendung finden, soll durch höhere Zünddrücke des Treibstoffs wie z. B. Diesel, Erdgas oder eines alternativen Kraftstoffs optimiert werden. Das steigert die Effizienz, senkt den Verbrauch und verbessert so die Emissionen und Betriebskosten.
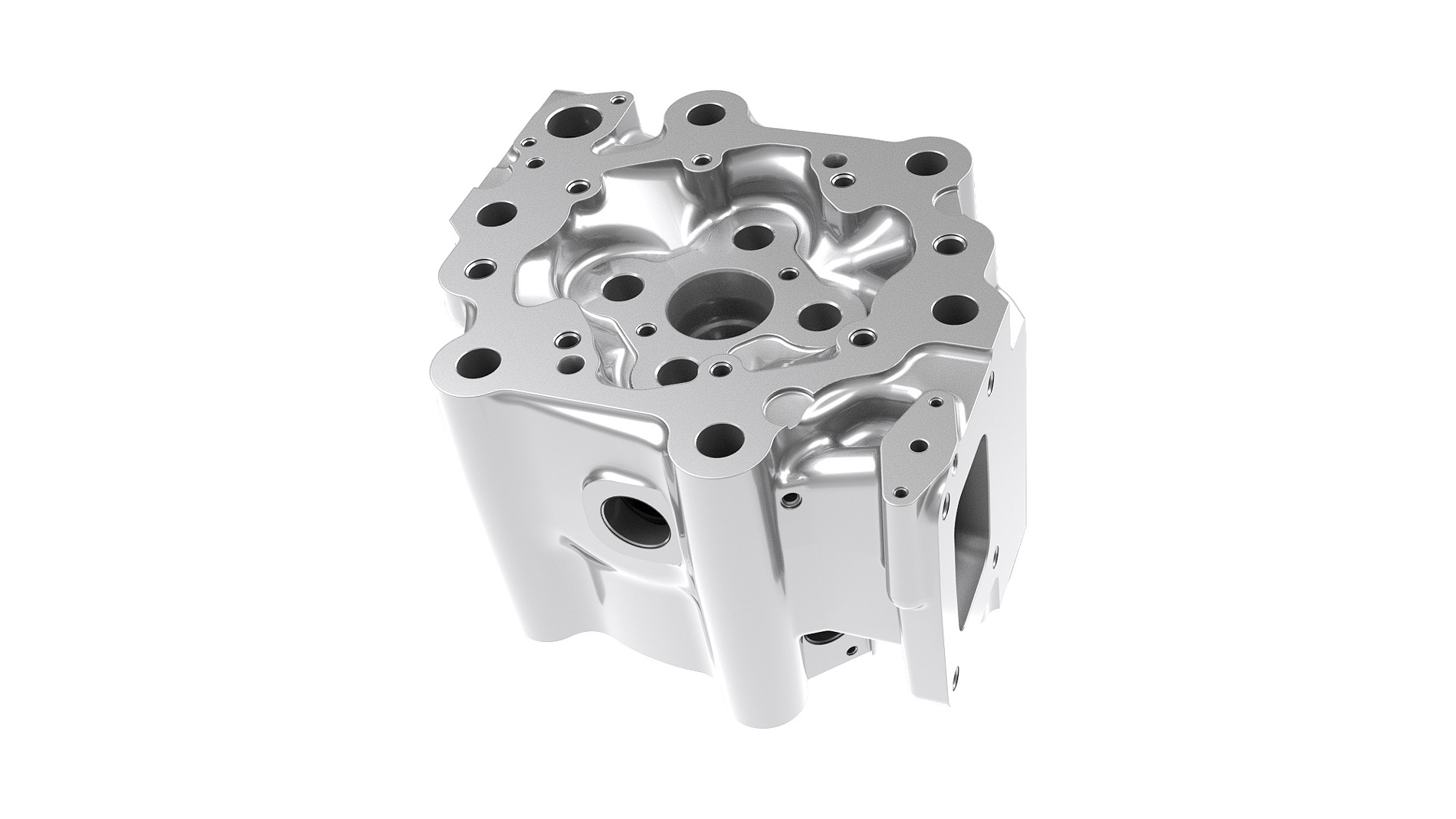
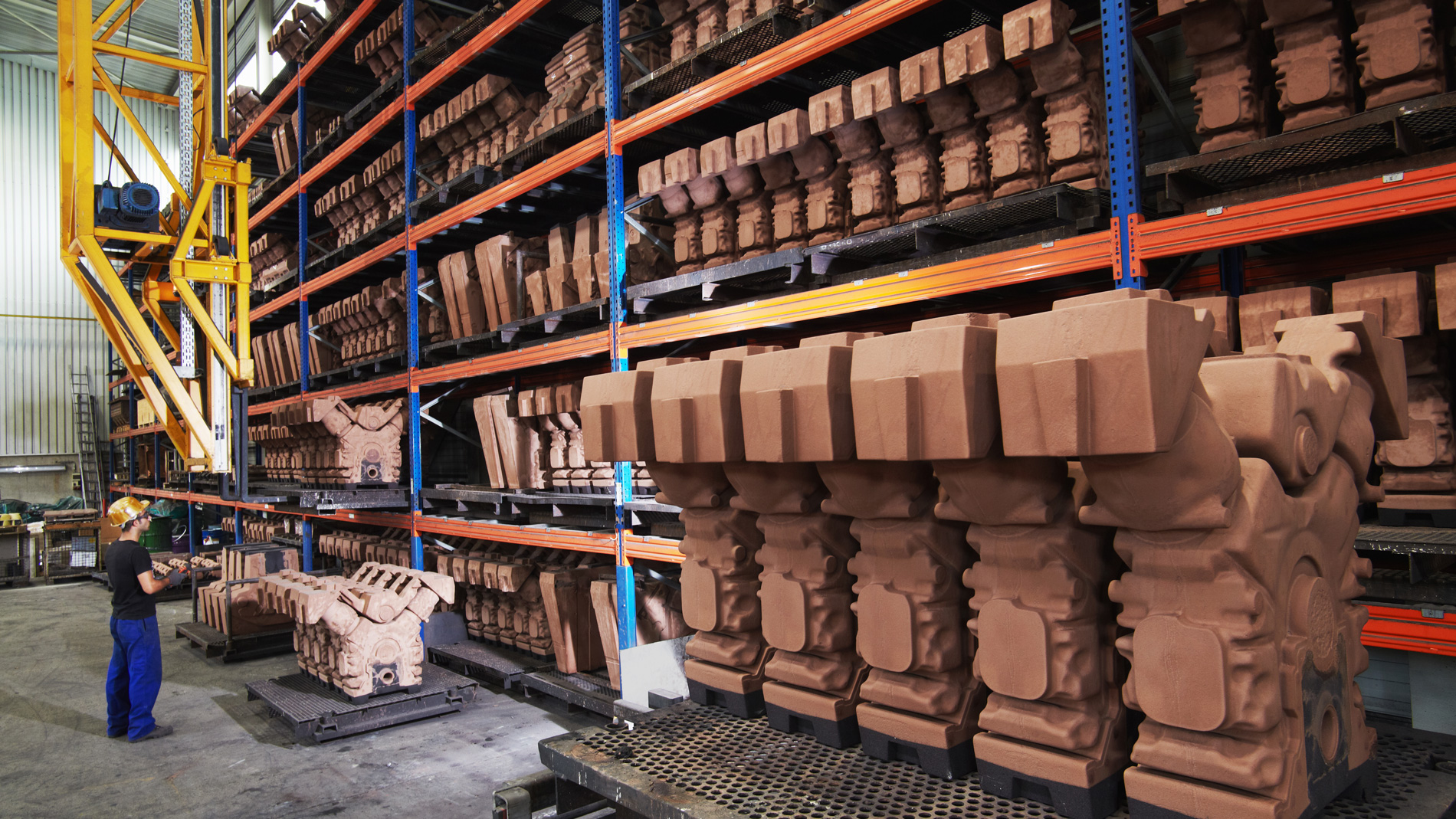
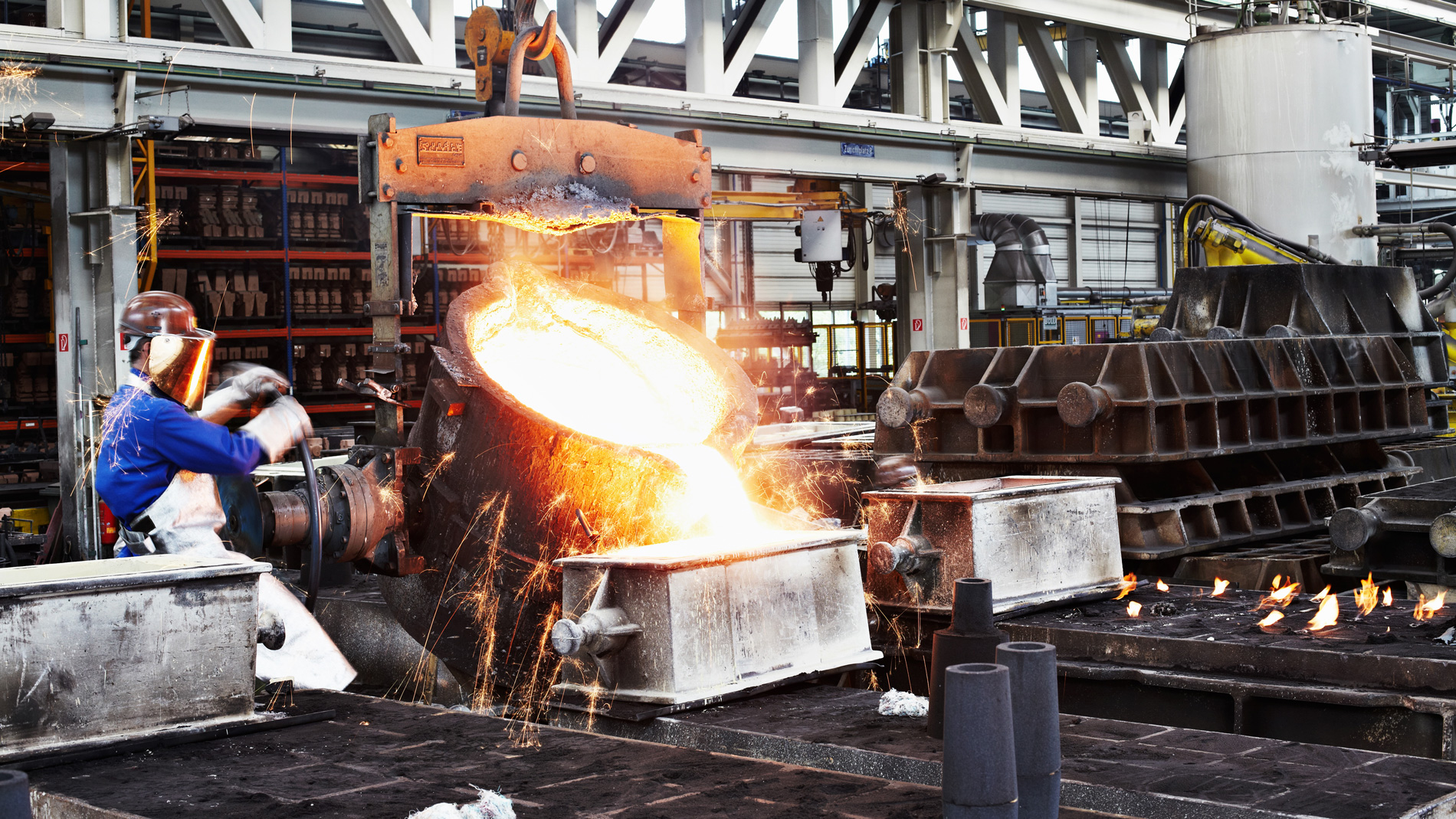
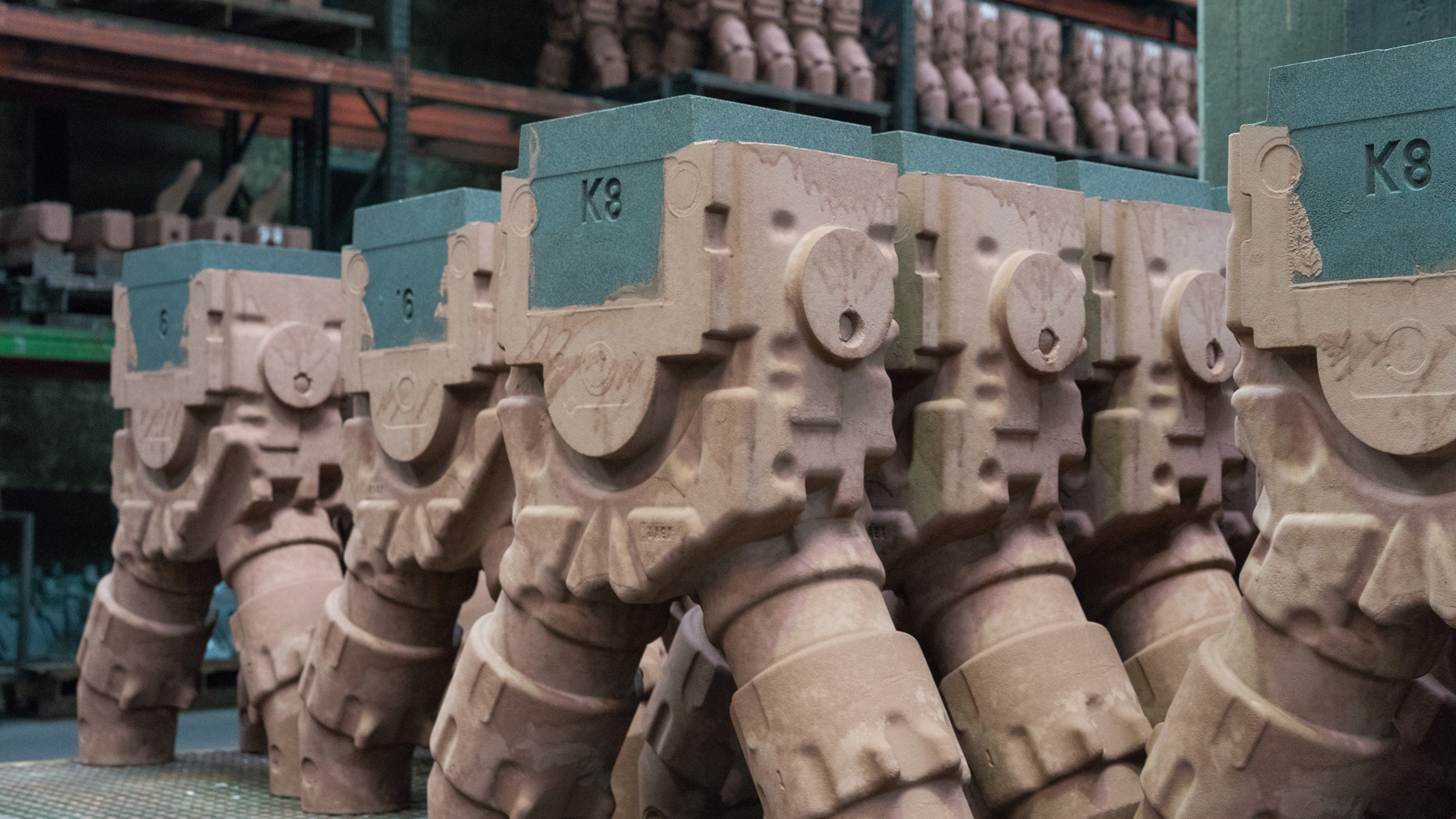
Was einfach klingt, birgt tiefgreifende technologische Herausforderungen: Der Anstieg des maximalen Zünddrucks über "den bisherigen Stand der Technik hinaus" beansprucht den Motor und insbesondere den Zylinderkopf viel stärker und würde bei gleicher Auslegung und gleichem Design die Haltbarkeit der Maschine erheblich verringern. Um dem entgegenzuwirken, wurde in dem Forschungsprojekt ein neuartiger Zylinderkopf mit einer deutlich höheren Kühlleistung und Festigkeit entwickelt.
Dafür sorgen geringere Wandstärken und engere Kühlleitungen, durch die das Kühlwasser optimal strömt und so mehr Wärme abführen kann. Das neuartige und durch AVL patentierte Zylinderkopfdesign "war früher technisch so nicht darstellbar und ist nun erst durch den 3D-Druck der Sandkerne möglich geworden", erklärt Benjamin Heil, Projektleiter Handformguss bei Gienanth. Deshalb schätzt er den 3D-Druck auch als "ein Werkzeug, das das Engineering auf eine neue Ebene hebt".
In dem von AVL angeführten Forschungsprojekt steuerte die Eisengießerei aus Eisenberg die Entwicklung rund um den Guss sowie die eigentliche Herstellung der zehn Zylinderköpfe bei. Die Herausforderung bestand dabei unter anderem darin, eine sehr präzise Oberflächengüte zu erzielen (wofür der spezielle synthetische Sand Cerabeads verwendet wurde) und die Sandreste rückstandsfrei aus den Gussteilen zu entfernen.
Die benötigten Gussformen und Kerne, in die später das über 1.370 Grad Celsius heiße Eisen fließt, bezog Gienanth vom Dienstleister Voxeljet. Eigene 3D-Druck-Anlagen will die Gießerei vorerst nicht betreiben, "da wir mit der Bestellung über Dienstleister einfach flexibler sind, was Größen und Stückzahlen angeht", erklärt Simon Geib.
NUR WENIGE MINUTEN
Für die Gussexperten aus Rheinland-Pfalz sind Stückzahlen im einstelligen Bereich eine Rarität, denn normalerweise liegen diese um ein Vielfaches höher: Zum Beispiel produziert die Unternehmensgruppe mit einem Umsatz von rund 250 Mio. Euro über 15 Millionen Bremskomponenten für Nutzfahrzeuge im Jahr und erreicht damit einen signifikanten Marktanteil in Europa, wie Geib berichtet.
Für die Großserien werden die Sandkerne mittels Kernschießmaschinen gefertigt. Die Produktionszeit liegt hier je nach Ausführung bei weniger als 3 bis 7 Minuten – auf dem 3D-Drucker dauert es ein Vielfaches. Allerdings erfordert die traditionelle Produktionsmethode, die über Jahrzehnte immer weiter optimiert wurde, recht aufwendig herzustellendes Werkzeug, das mehrere Hunderttausend Euro kosten kann. Bei geringen Stückzahlen können 3D-gedruckte Sandkerne daher deutlich günstiger sein. Gleichzeitig spielt auch der Zeitfaktor eine Rolle: Die 3D-gedruckten Kerne können innerhalb einiger Tage zur Verfügung stehen, die Werkzeuge für die Kernschießmaschine benötigen teilweise mehrere Monate in der Bereitstellung.
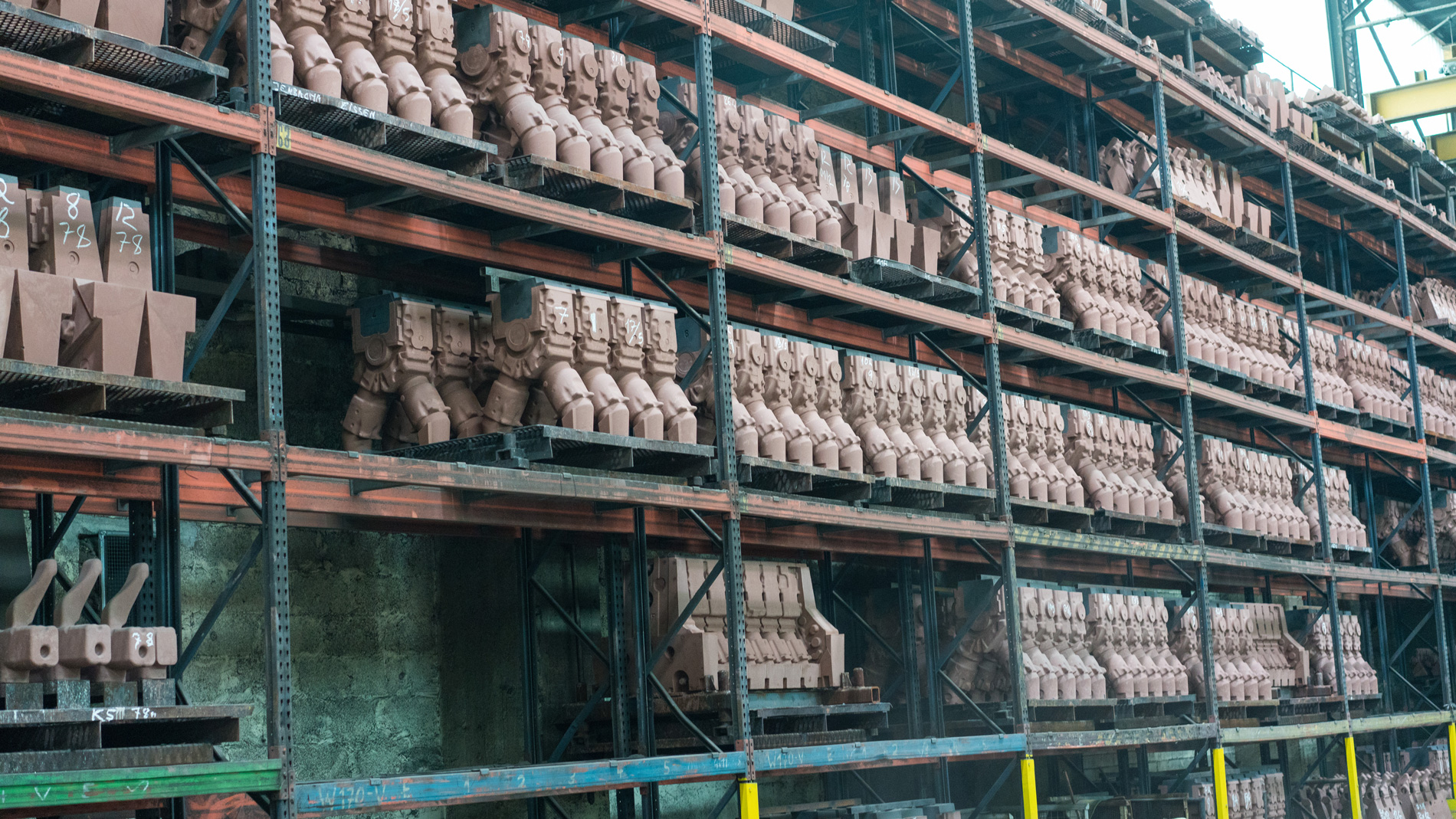
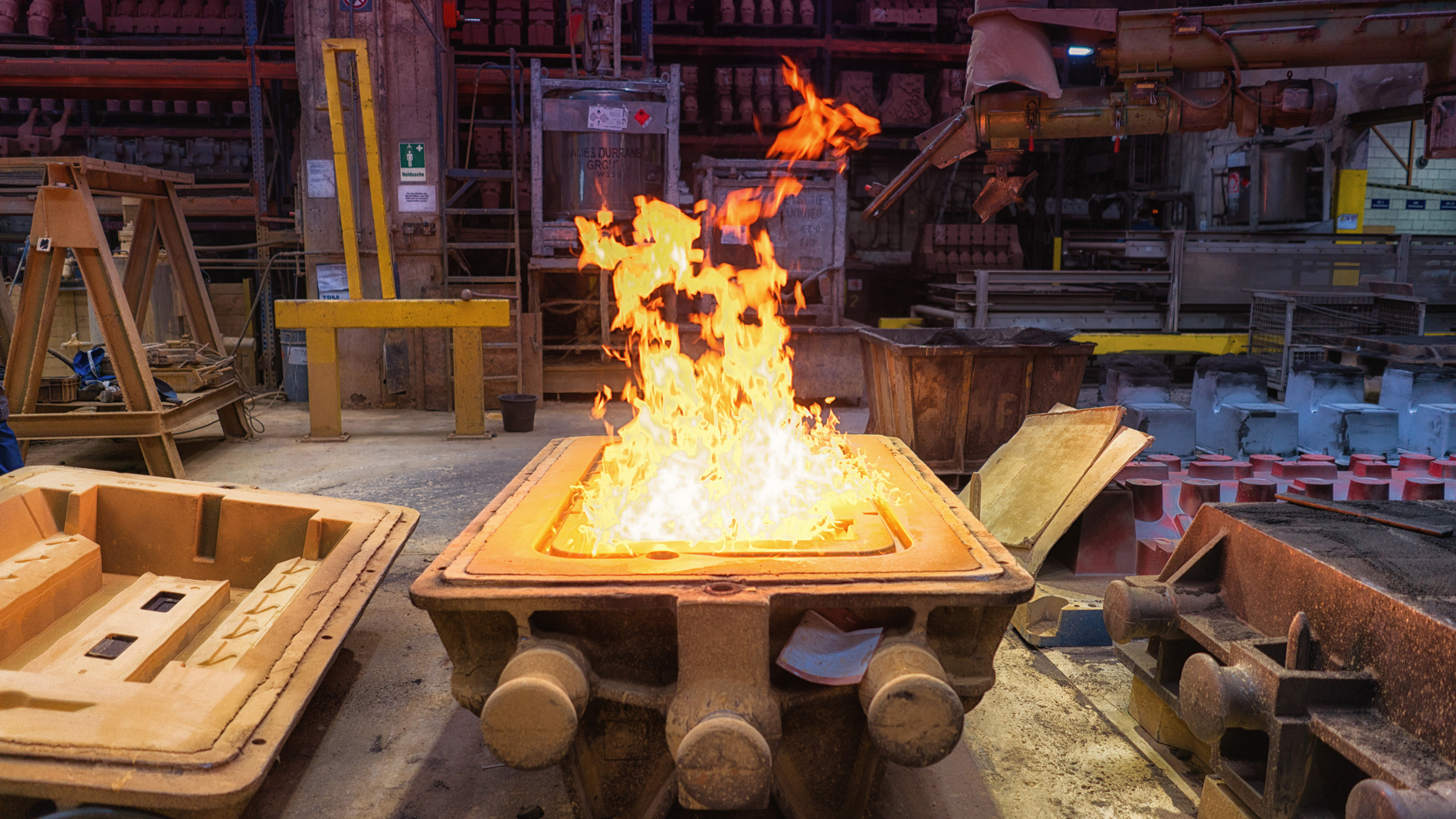
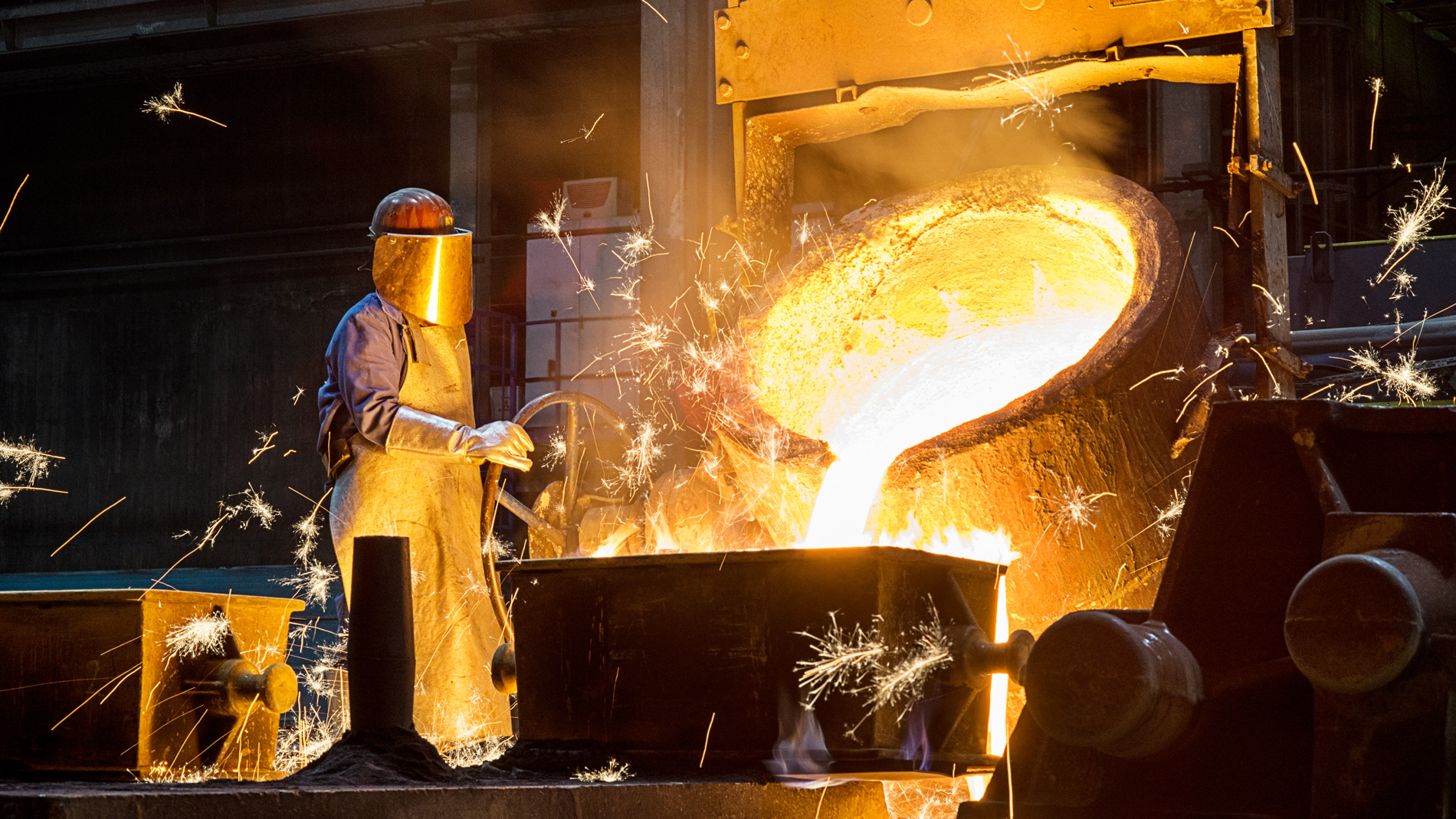
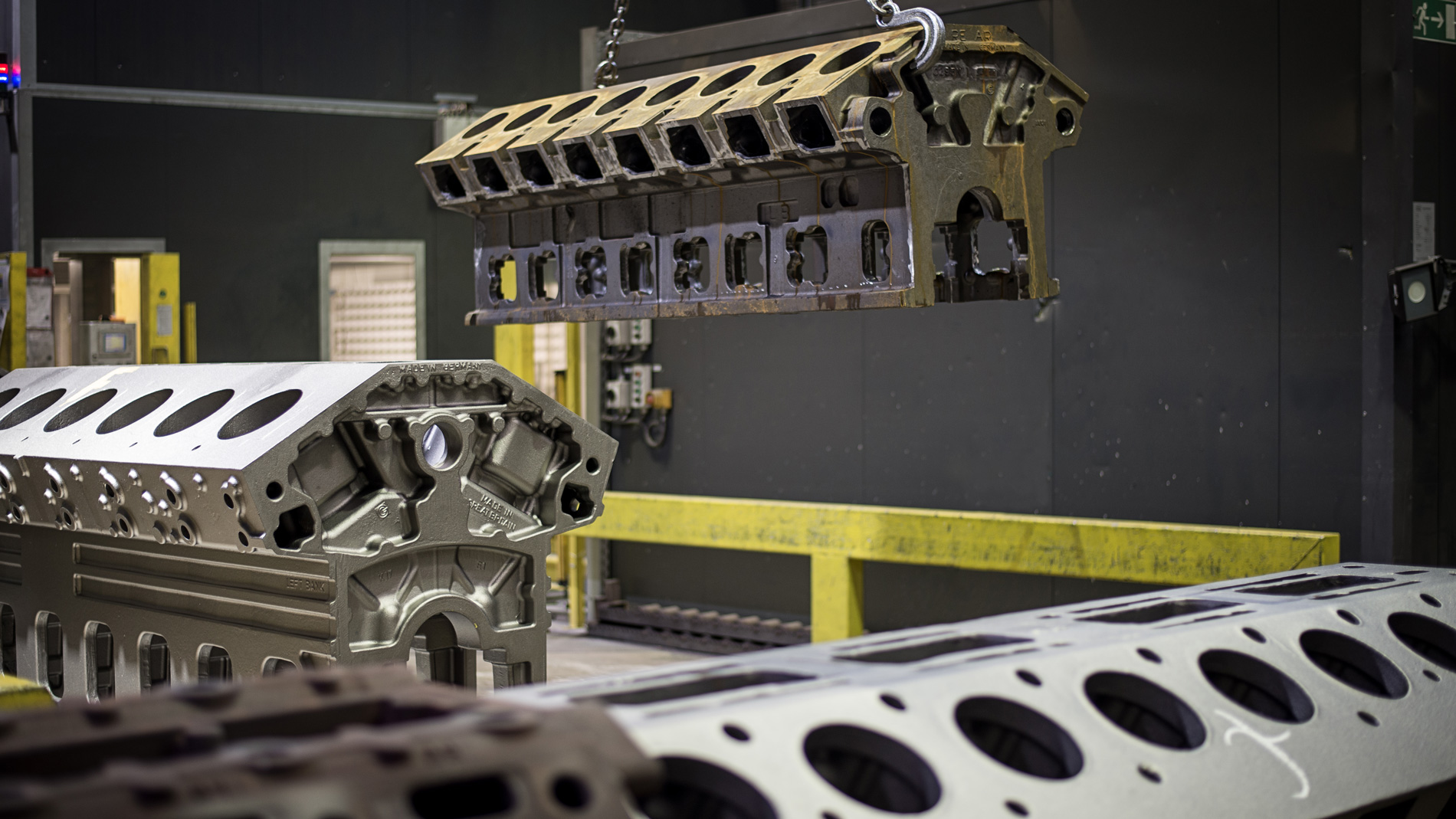
Trotzdem ist der Einsatz von 3D-gedruckten Sandkernen im Produktionsprozess noch recht überschaubar, was die Gussexperten von Gienanth vor allem auf "die deutlich höheren Kosten im Vergleich zur traditionellen Fertigung " zurückführen. Allerdings ist es möglich, einzelne 3D-gedruckte Sandkerne in eine aus mehreren klassisch hergestellten Kernen bestehende Form mit einzubringen. "Damit wäre der 3D-Druck eine sinnvolle Ergänzung in der Produktion großer Stückzahlen."
"VIEL BEWEGUNG IM E-BEREICH"
Gleichzeitig sorgt die Entwicklung effizienterer AM-Anlagen dafür, dass 3D-gedruckte Sandkerne auch bei größeren Stückzahlen rentabel zum Einsatz kommen können.Während sich z. B. bei Voxeljet Klein (< 1.000 Stück) und Kleinstserien (< 20 Stück) im Dienstleistungsbereich in den vergangenen Jahren zum Standard entwickelt haben, kann sich Geschäftsführer Ingo Ederer auch die wirtschaftliche Produktion von Stückzahlen im sechsstelligen Bereich vorstellen. "Dafür sind aber zum Beispiel automatisierte Entpackungslösungen erforderlich."
Auch beim bayerischen Pionier des 3D-Sanddrucks ist der von der Elektrifizierung angestoßene Wandel in der Automobilindustrie bereits spürbar. "Wir stellen durchaus fest, dass sich das Bestellvolumen seitens der Automobilindustrie reduziert bzw. umgeschichtet hat", berichtet Ederer. "Wir können schon seit einiger Zeit einen signifikanten Auftragsrückgang bei Projekten, die mit Verbrennungsmotoren in Zusammenhang stehen, feststellen. Allerdings durften wir letztes Jahr auch einige Großaufträge bearbeiten, die uns gezeigt haben, dass im E-Bereich sehr viel Bewegung ist." Ein Beispiel hierfür sind Formen für Karosseriekomponenten, die Voxeljet für größere E-Auto-Hersteller 3D-gedruckt hat. Diese würden, so vermutet Ederer, zuerst für die Produktion geringerer Stückzahlen verwendet und später durch Druckgusswerkzeuge ersetzt.
OPTIMIERUNGSDRUCK FÜHRT ZU EINEM UMDENKEN
bei Gienanth kann man sich zudem vorstellen, dass die neuen Zylinderköpfe später mittels 3D-gedruckter Sandkerne gefertigt werden – sofern die derzeit durchgeführten Test die gewünschten Ergebnisse liefern. Daraus entstünde dann eine kleine Serienproduktion: An einem Großmotor werden je nach Zylinderzahl bis zu 24 Zylinderköpfe einzeln aufgeschraubt. Bedarf entsteht sowohl bei neuen Motoren als auch im Ersatzteilbereich.
Der Megatrend hin zur Individualisierung und zu damit einhergehenden vergleichsweise kleineren Stückzahlen ist auch in der Gießerei- Industrie erkennbar, was laut Geib in der Vergangenheit kaum der Fall gewesen ist. Schließlich waren und sind große Serien häufig profitabler. Doch auch hier habe ein Umdenken eingesetzt, wobei der 3D-Druck künftig eine stärkere Rolle spielen könnte. Weiteres Zukunftspotenzial für die additive Fertigung in der Gießereibranche sehen Geib und Projektleiter Heil auch im kontinuierlichen Streben nach mehr Umweltschutz und Energieeffizienz, was nun auch bei Großmotoren zu einem höheren Optimierungsdruck und zum Umdenken bei Design und Fertigungsprozessen führe. "Allerdings sind in diesen Branchen die Entwicklungszyklen relativ lang, bei Großmotoren liegen sie bei einem Vielfachen von Nutzfahrzeugen oder auch Pkw", so Geib. "Aber es beginnt zu rollen."
GIENANTH GROUP GMBH
1735 als Hammerwerk in Eisenberg im heutigen Rheinland- Pfalz gegründet, zählt Gienanth zu den ältesten Unternehmen in Deutschland. Ein bayerischer Standort geht sogar auf das Jahr 1449 zurück. Inzwischen ist daraus eine internationale Unternehmensgruppe entstanden, die rund 1.800 Mitarbeiter beschäftigt und einen Umsatz von rund 250 Mio. Euro erwirtschaftet. Zu den Produktlösungen der Unternehmensgruppe zählen u. a. hochkomplexe Zylinderkurbelgehäuse und Zylinderköpfe für Großmotoren im Leistungsbereich von 1.000 bis 15.000 PS. Diese kommen zum Beispiel in Stromgeneratoren, Lokomotiven oder auch Schiffen zum Einsatz.
gienanth.com
AM-VERFAHREN:
Additive Manufacturing für Metalle/Binder Jetting
Einen strukturierten Überblick in die komplexe und vielschichtige Welt der additiven Fertigungsverfahren, Prozessschritte und Anwendungsfelder liefert Ihnen unser AM Field Guide.
Tags
- Automotive