Text: Thomas Masuch; Fotos: Zikomm — 29.10.2020
Für mittelständische Unternehmen ist der industrielle 3D-Druck nicht nur eine Anwendungstechnologie, sondern ein echtes Geschäftsfeld. Bestes Beispiel dafür ist das Unternehmen Bernstein Mechanische Fertigung (BMF) aus dem sächsischen Grüna. Vor zehn Jahren noch reiner Lohnfertiger, entstehen hier abseits der Fräszentren jährlich 20 Anlagen zur Oberflächenbearbeitung und sorgen so für die Hälfte des Unternehmensumsatzes.
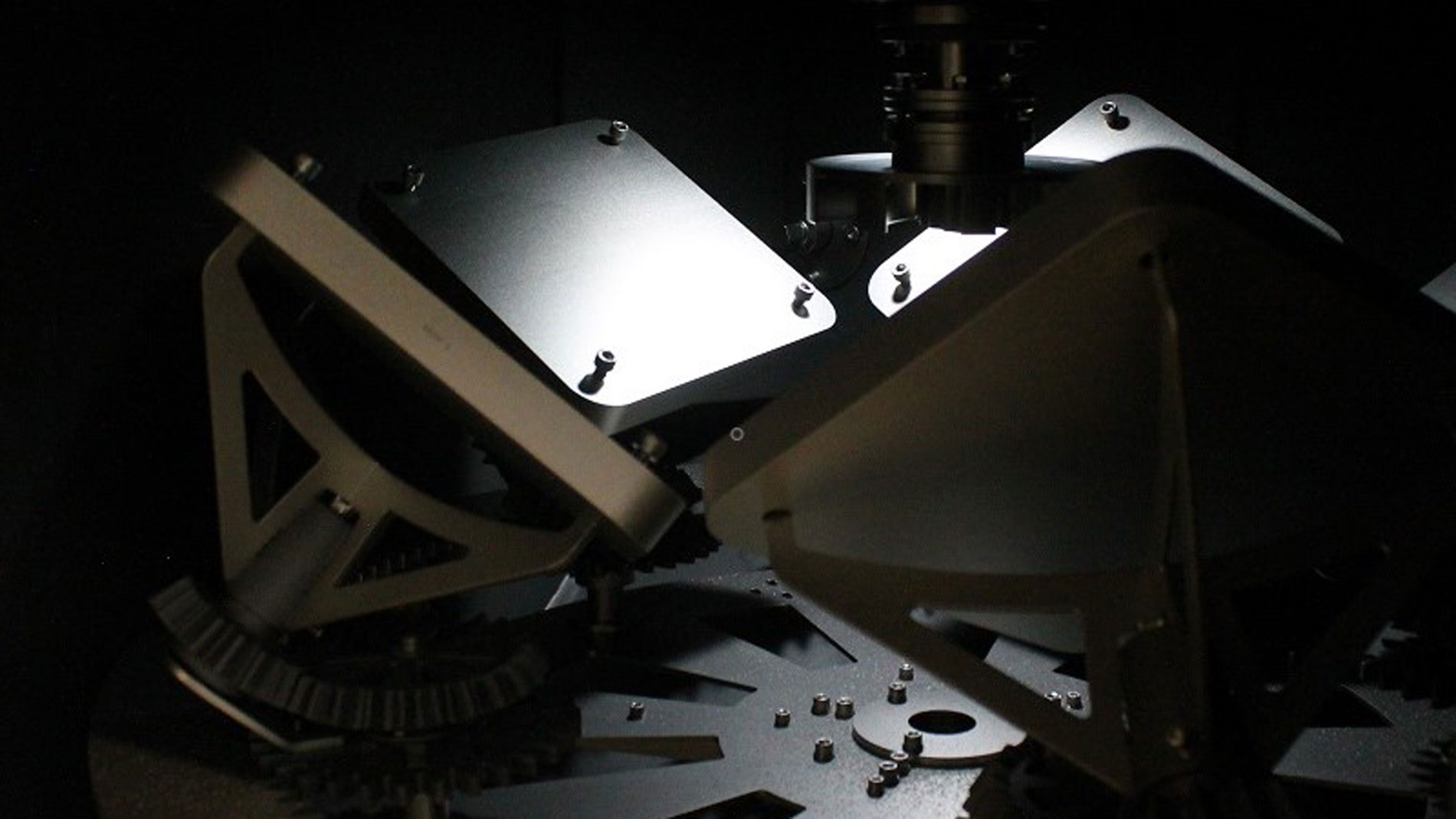
Wer nach Grüna fährt, rechnet nicht damit, hier ein Unternehmen zu finden, das in der Welt der Additiven Fertigung mitmischt. Im Westen von Chemnitz streckt sich das Dorf entlang einer der Ausfallstraßen der traditionsreichen Industriestadt, die sich mit langer Verzögerung wieder aus der Nachwendedepression herausgeschält hat. In das hügelige Vorland des Erzgebirges schmiegen sich hier Einfamilienhäuser mit blühenden Vorgärten. In dem Dorf, das von dem backsteinernen Kirchturm überragt wird, gibt es einen Bäcker und zwei Hotels.
Gleich neben einem Garten, in dem im Sommer Tomaten und anderes Gemüse gedeihen, liegt die moderne Firmenhalle von BMF. Mehrere Fräszentren, ein Ausbildungsbereich, ein Messraum, die Entwicklung und die Montage sind effizient in einem Gebäude vereint. Vor 13 Jahren wurde das Familienunternehmen gegründet und daraus ein spezialisierter CNC-Lohnfertiger entwickelt, der unter anderem anspruchsvolle Teile für Luxusartikel, High- End-Fahrzeuge und Medizintechnikunternehmen fertigt.
"Bei der Additiven Fertigung wird das Postprocessing immer wichtiger, auch in finanzieller Hinsicht."
»Allerdings kam es immer wieder zu Problemen durch das Sandstrahlen, weil Teile nach der Bearbeitung keine homogene Oberfläche aufwiesen«, erinnert sich der heute 41-jährige Geschäftsführer Ronny Bernstein. Gerade im Luxussegment seien Bauteile dann nicht verwendbar. Und ganz der unternehmerische Ingenieur, suchte Bernstein mit seinem Team eine eigene Lösung. Daraus entstand 2013 eine eigene Anlage, die im Unternehmen für den internen Bedarf genutzt wurde. »Als wir später einen Kunden zu Besuch hatten, fragte er, was das sei, und wollte letztendlich auch so eine.«
BMF entwickelte daraus ein eigenes Produkt: die Strahlanlage Twister. Herzstück der Anlage ist ein Drehteller, auf dem rotierende Bauteilaufnahmen angebracht sind. In der Mitte dieses Karussells verteilt eine schnell rotierende Scheibe (Schleuderrad mit patentierter Flügelgeometrie) das Strahlmittel gleichmäßig im Arbeitsraum.
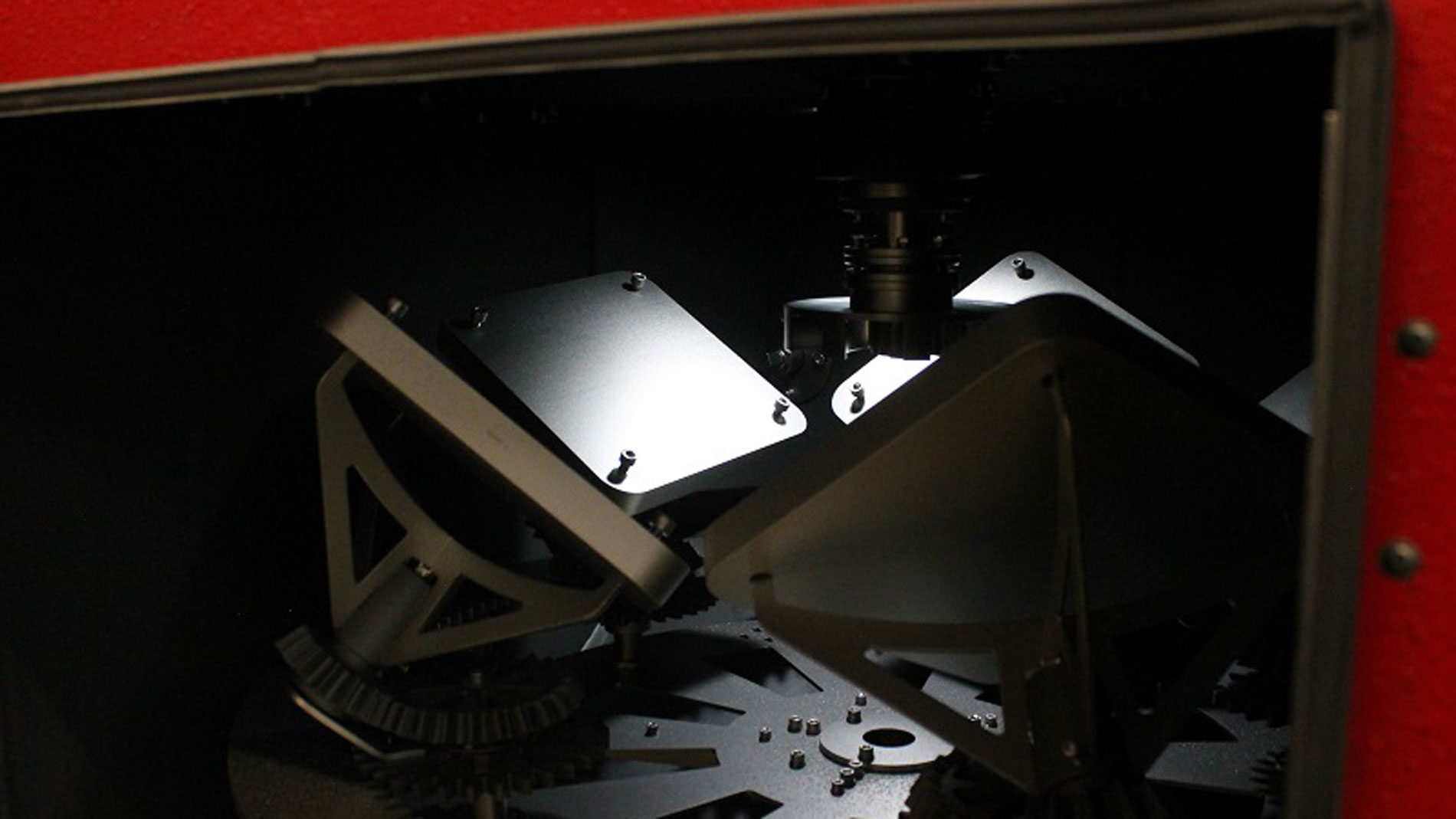
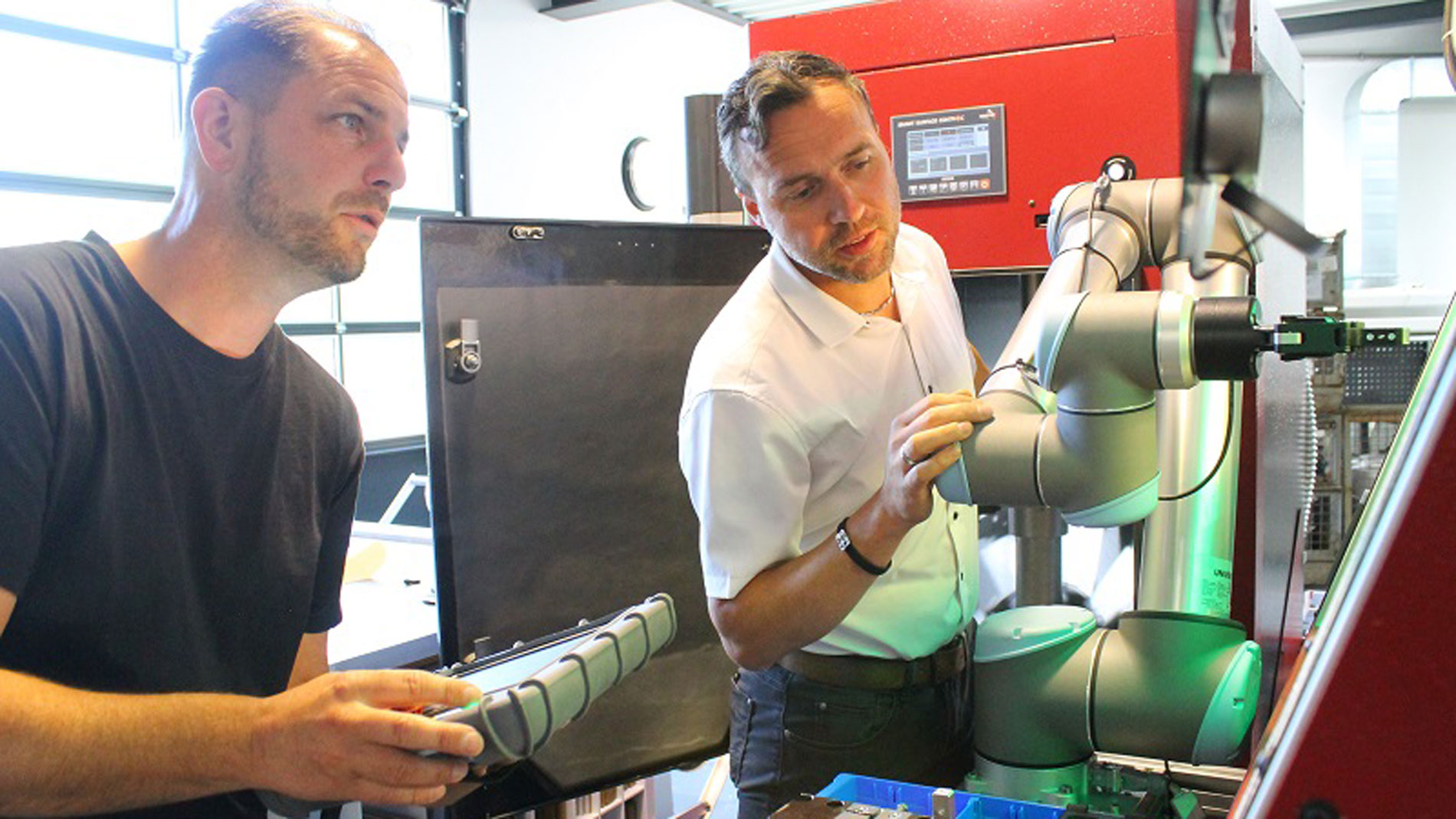
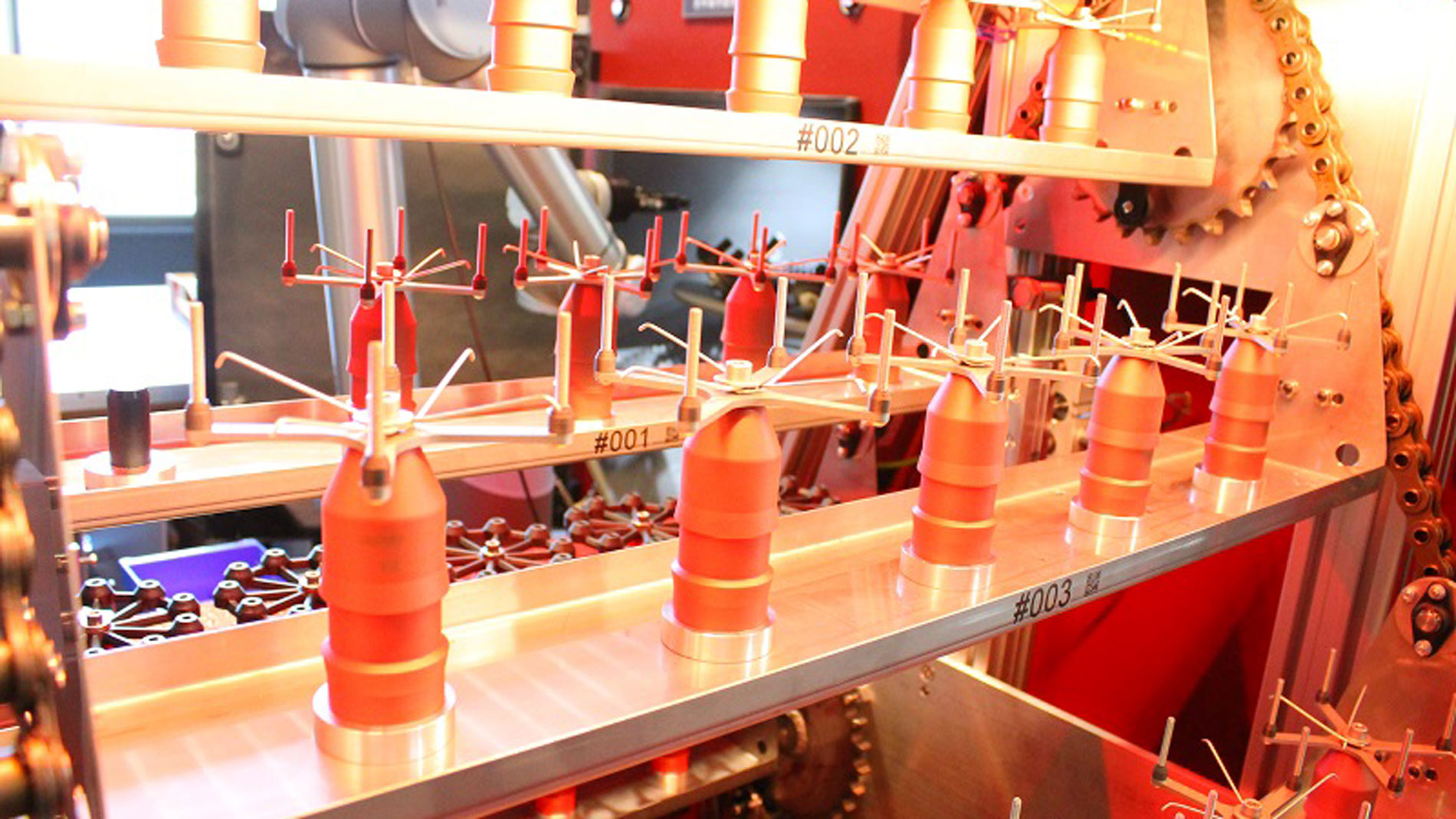
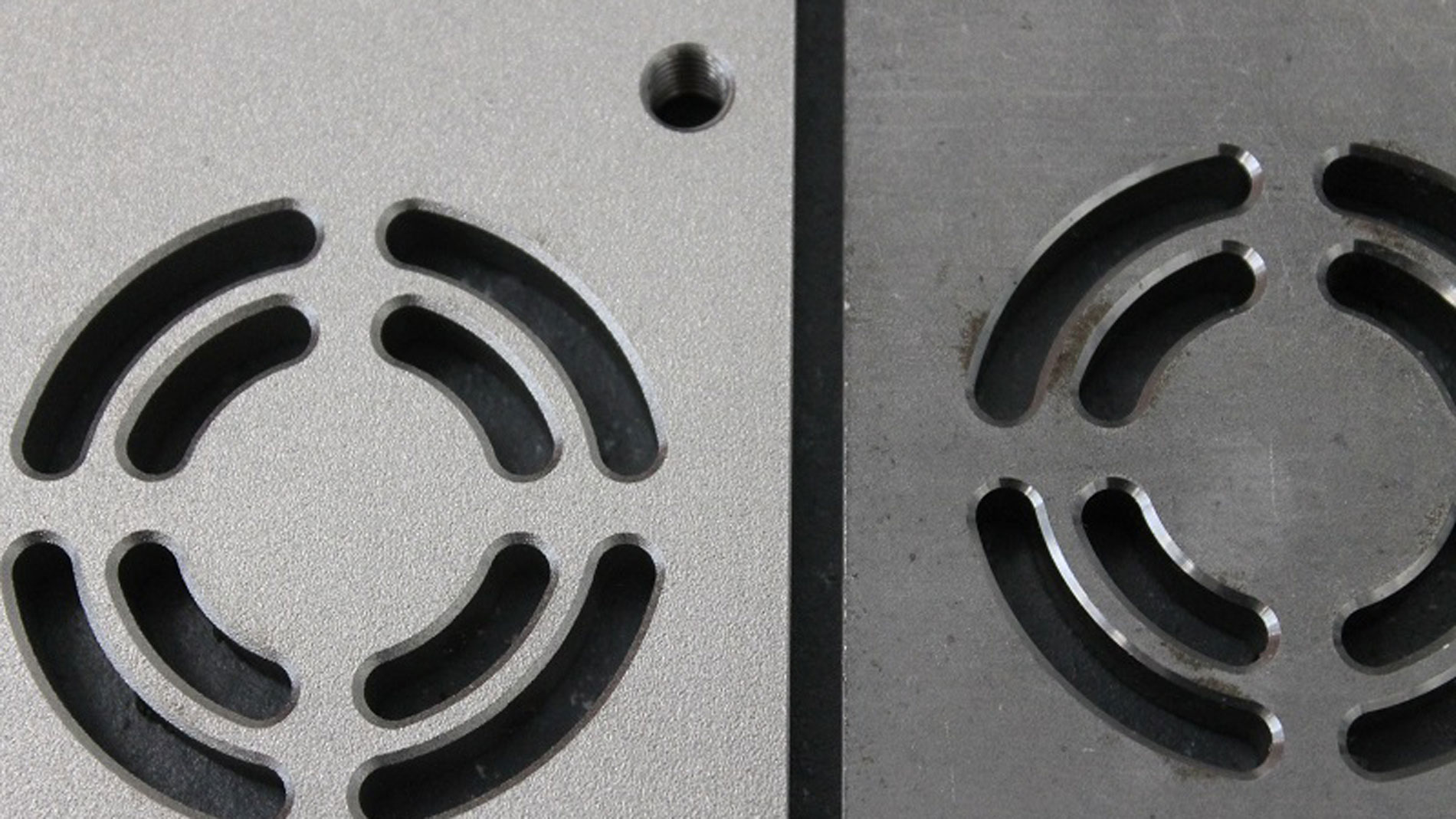
Die ersten Anlagen gingen an regionale Unternehmen aus der Fräsbearbeitung. Nach und nach erkannte man bei BMF, dass das Potenzial des Twisters noch größer ist. »Bei der Additiven Fertigung wird das Postprocessing immer wichtiger, auch in finanzieller Hinsicht«, erklärt Marc Krause, der sich als Mitarbeiter der BMF Vertriebs GmbH seit drei Jahren für den weiteren Erfolg des Twisters einsetzt und dabei den Vertrieb und die Prozessentwicklung betreut. »Bei additiv gefertigten Bauteilen liegt der Kostenanteil der Nachbearbeitung an den gesamten Produktionskosten inzwischen bei 30 bis 40 Prozent. Während der Druckprozess in den letzten Jahren immer günstiger geworden ist, blieb das Postprocessing etwa gleich teuer, da die Arbeiten hier zu 90 Prozent manuell getätigt werden.«
Seitdem BMF mit dem Twister auch die Additive Fertigung entdeckt hat und die Anlage auch auf Messen wie der Formnext präsentiert wird, hat der Verkaufserfolg deutlich angezogen. Inzwischen sind 80 Anlagen installiert – neben zahlreichen europäischen Ländern auch in Indien und seit Herbst 2020 in den USA.
Den Erfolg der Strahlanlagen, die zu 90 Prozent aus der eigenen BMF-Fertigung stammen, führt Krause im Wesentlichen auf die technischen Vorteile zurück, die sich wie der heilige Gral des Strahlens anhören: »Wir erreichen reproduzierbare Ergebnisse in einem automatisiertem Prozess, der auch in eine automatisierte Fertigung eingebunden werden kann«, schwärmt Krause. Zudem werde das Strahlmittel nicht per Druckluft, sondern mittels Schleuderrad beschleunigt, woraus eine hohe Energieeinsparung allein durch den Wegfall der Druckluft resultiere. Die Oberflächengüte in Form von Ra- (Mittenrauwert) und Rz-Werten (gemittelte Rautiefe) lässt sich anhand der Drehzahl des Schleuderrades in der Anlage einstellen.
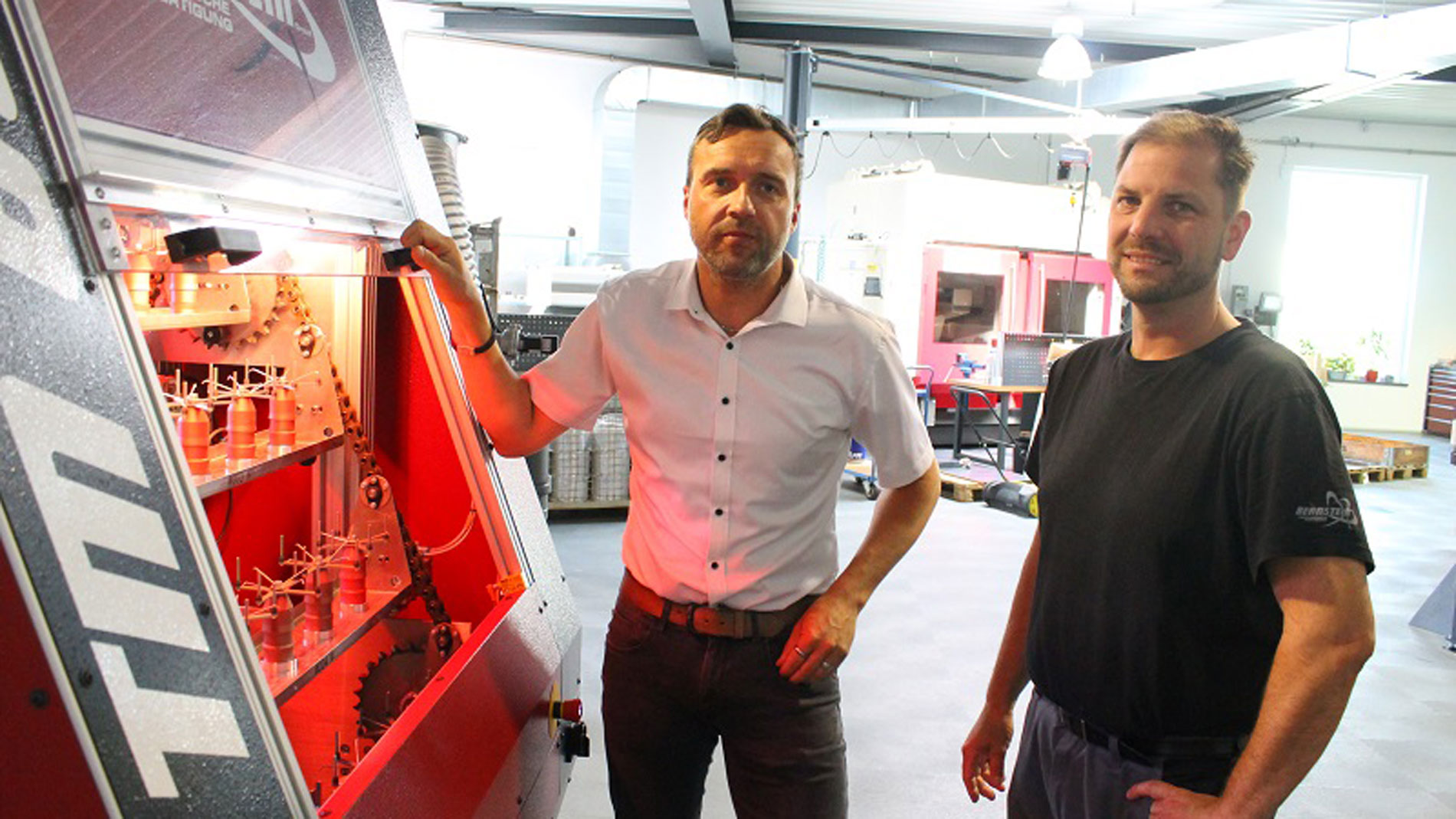
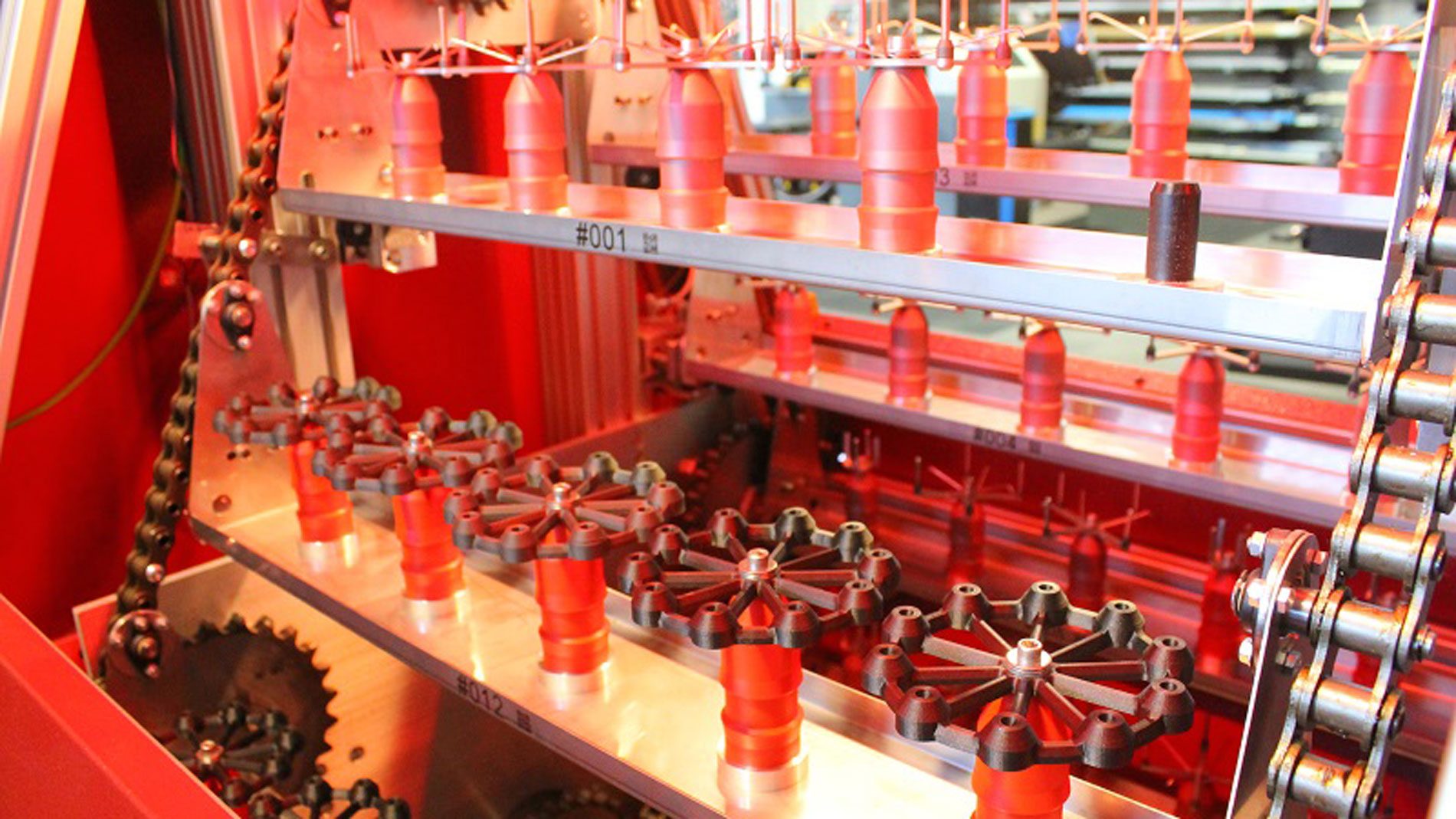
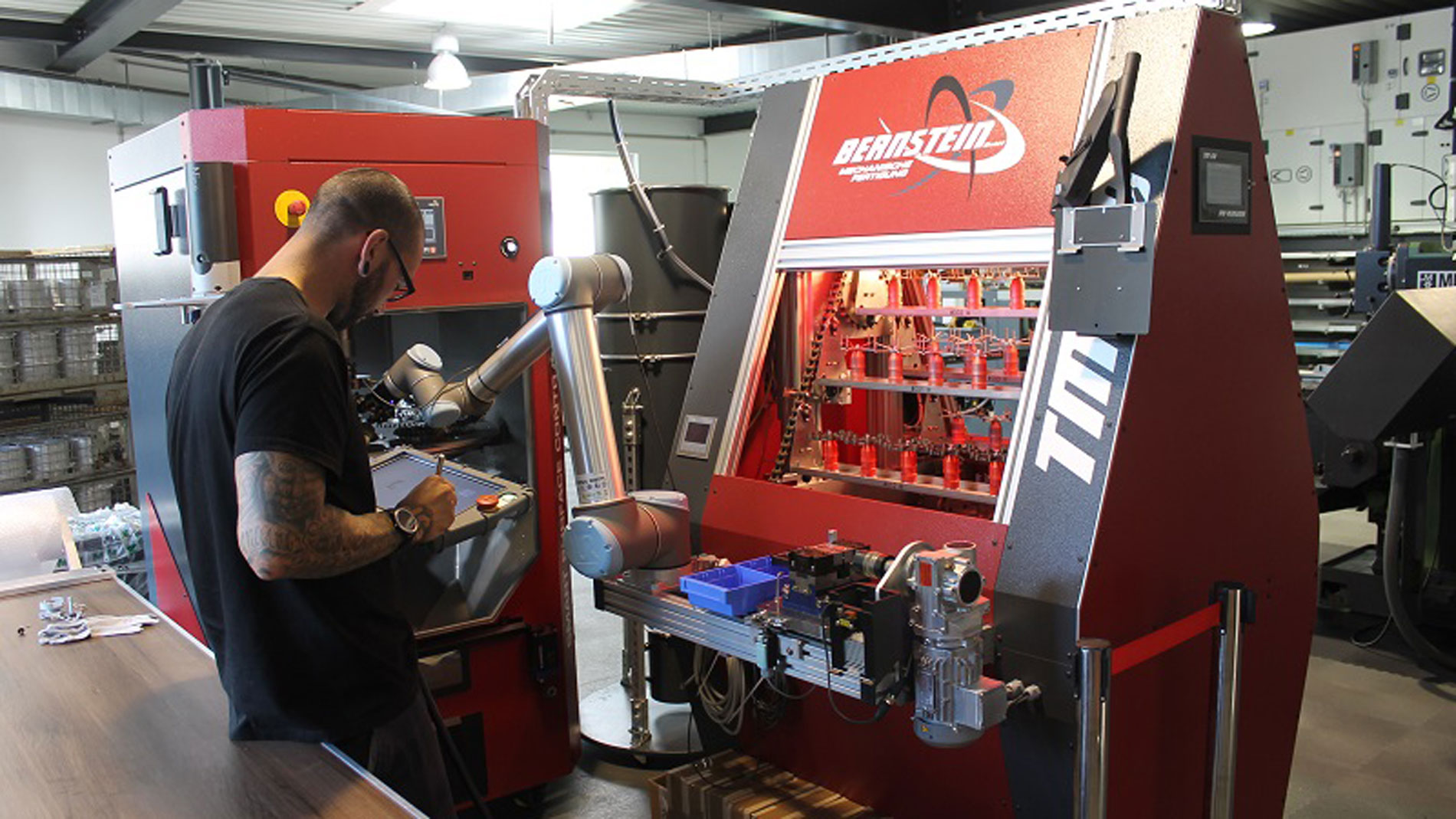
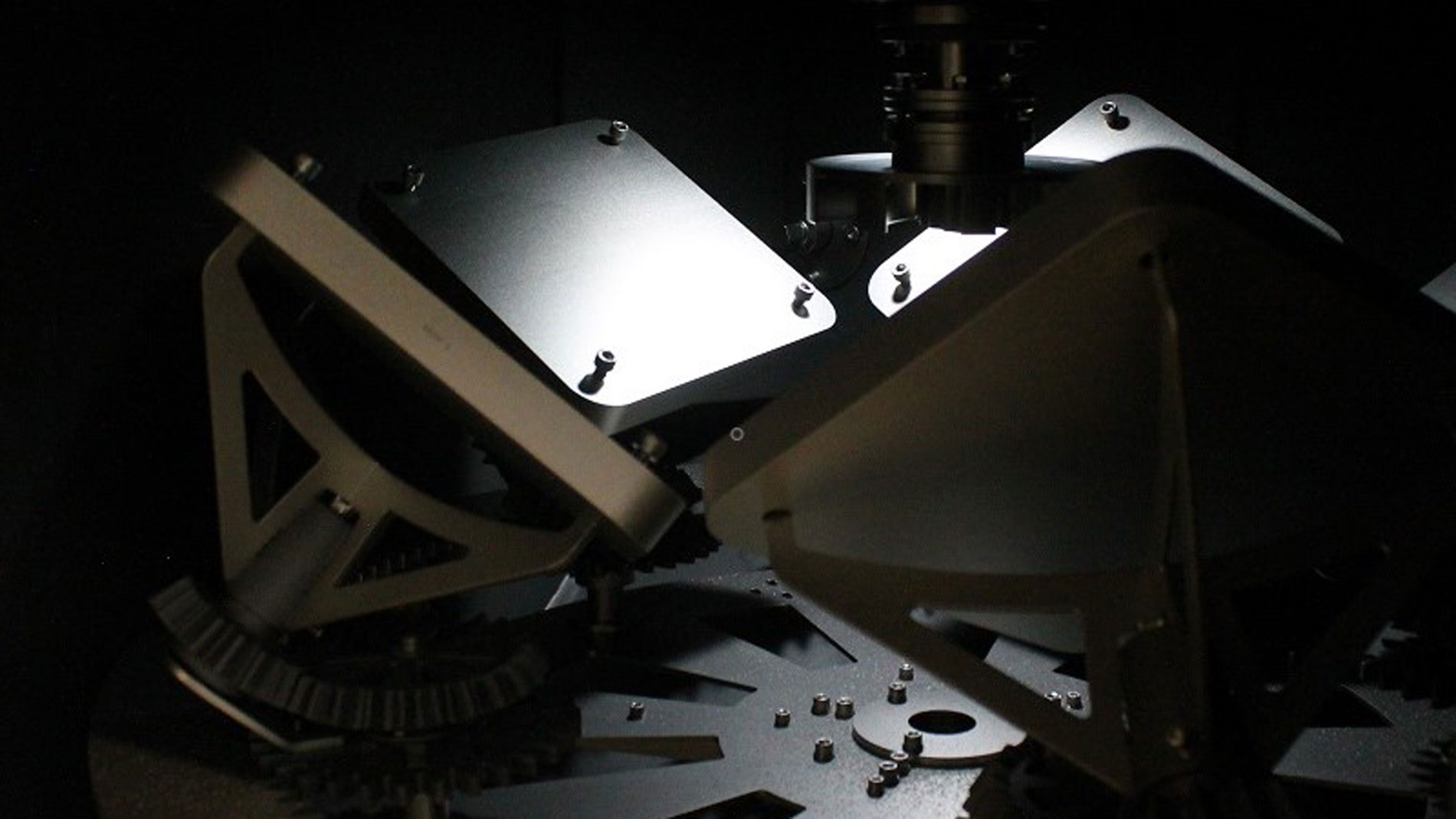
Ansprüche an Oberflächen sind gestiegen
So sorgen Twister und sein 2016 eingeführter größerer Bruder Tornado dafür, dass zum Beispiel Schaftgabeln für Getriebe, Schalen für Blutplasmazentrifugen, Zahnimplantate oder Retrofit von Motorenteilen in der Automobilindustrie die passende Oberfläche erhalten. Und auch bei Fräsbauteilen sind Anlagen weiterhin im Einsatz, denn »die Ansprüche der Kunden an Oberflächen sind in den vergangenen Jahren generell gestiegen. Verstärkt werden sogar nicht sichtbare Funktionsteile gestrahlt, um durch eine bessere Optik den Verkauf zu fördern«, so Krause. Gleichzeitig sieht der 49-Jährige, der schon 25 Jahre Erfahrung im Prototypenbau hat, einen höheren Bedarf bei AM-Dienstleistern, da sich dort der Anspruch der Kunden ebenfalls gewandelt habe: »Die Kunden bestellen nicht mehr nur ein Bauteil, sondern 50 oder mehr, und die müssen alle gleich aussehen.«
Wie innovativ BMF die Additive Fertigung zum eigenen Nutzen einsetzt, zeigt sich auch beim Thema Ersatzteile. Die Antriebsräder für die rotierenden Bauteilaufnahmen im Twister sind auf einem 3D-Drucker von Markforged entstanden. Um die Ersatzteilversorgung dieser Verschleißteile reibungslos zu gewährleisten, steht zum Beispiel bei Kunden in Dänemark und Indien ein baugleicher Drucker und liefert auf Bestellung die benötigten Ersatzteile vor Ort. Der 3D-Drucker wird von Grüna aus gesteuert, der Kunde muss nur die Spulen nachfüllen und die Bauteile entnehmen. »Da wird nichts mehr versandt, und es geht nichts mehr durch den Zoll«, freut sich Ronny Bernstein. Und auch für Markforged war diese Innovation so überzeugend, dass sich der global aufgestellte Hersteller aus Boston die Anwendungen im beschaulichen Grüna vor Ort ansah und sie in seine internationale Marketingkampagne aufnahm.
MEHR INFORMATIONEN UNTER:
Tags
- Oberflächenbehandlung