Text: Thomas Masuch, 03.09.2023
Die Eisengießerei Römheld & Moelle aus Mainz hat sich mit dem Printed Casting einen neuen Produktbereich eröffnet und sieht im Gießen mit 3D-gedruckten Formen enormes Geschäftspotenzial.
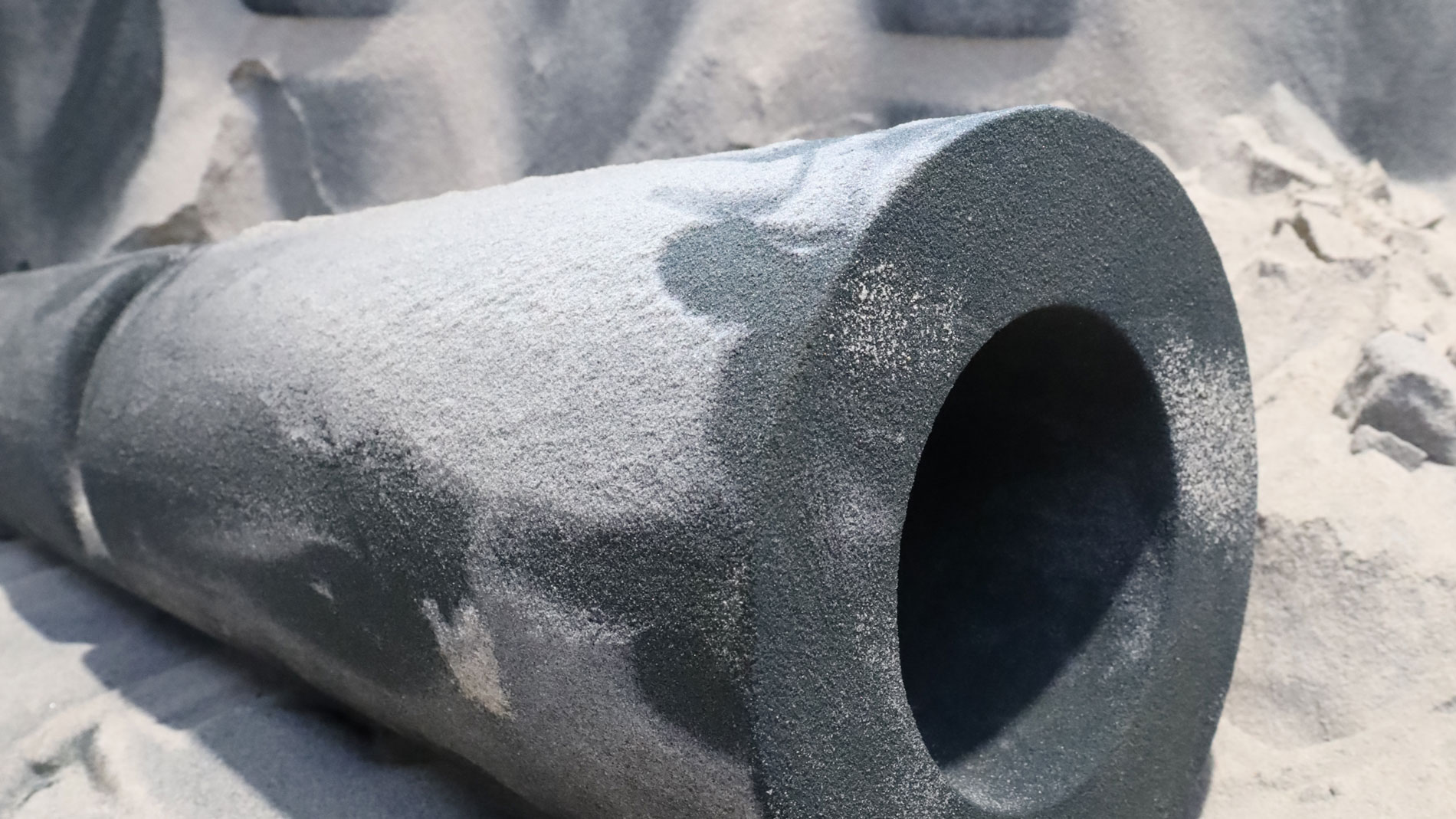
Die beiden Welten sind nur durch zwei Türen getrennt. Während wir gerade noch in einem gut beleuchteten Gebäude vor dem Touchscreen des neuen Sand-3D-Druckers standen, schreiten wir nun durch große und geschichtsträchtige Werkhallen, deren Wände und Böden von einer dünnen Schicht Staub dunkelgrau gefärbt sind. Stahlgestelle, sogenannte Formkästen, groß wie Eisenbahnwaggons, reihen sich hier aneinander, und hin und wieder fallen Sonnenstrahlen durch die Fenster des Hallendachs und erleuchten einzelne Flächen wie Spotlights im Theater. In einem der Formkästen steht ein kräftiger bärtiger Mann mit tätowierten Armen und füllt grau-schwarzen Sand hinein.
Im Inneren eines solchen mit Sand gefüllten massigen Formkastens ruhen verborgen filigrane 3D-gedruckte Sandformen, in die später in der Nachtschicht flüssiges Metall gegossen wird. In anderen Formkästen liegen Formen aus Styropor dicht umschlossen von dunklem Sand. Auch in diese fließt später flüssiges Eisen und füllt den Platz des Styropors aus, das bei den hohen Temperaturen vergast.
Fotos: Thomas Masuch
Vom ersten Tag an mit Aufträgen versorgt
In der Eisengießerei Römheld & Moelle in Mainz wird seit 1859 Metall gegossen und im Kern hat sich an der Technologie, die bereits seit der Antike verwendet wird, nicht viel geändert: Bis zu 1.400 Grad heiße Metalllegierungen (Eisen plus Kohlenstoff und verschiedene weitere Metalle wie Mangan, Kupfer oder Nickel) werden in Formen aus Sand gegossen. In dieser traditionellen Branche hat Geschäftsführer Rudi Riedel im vergangenen Jahr mit dem 3D-Druck von Sandformen eine kleine Revolution in Gang gesetzt.
Diese Technologie gehört eigentlich zu den ältesten additiven Verfahren (die ersten 3D-Drucker für Sandformen kamen vor rund 20 Jahren auf den Markt), doch „bisher wurde der additive Sanddruck nur für die Herstellung der Formenkerne und nicht für komplette Formen eingesetzt“, erklärt Riedel, der seit 2020 das Unternehmen am Mainzer Zollhafen leitet. „Wir dagegen haben uns aber von Anfang an entschlossen, die ganze Form zu drucken.“ Vor rund einem Jahr erwarb das Unternehmen die erste Anlage von ExOne, „und wir waren im Prinzip vom ersten Tag an mit Aufträgen sehr gut versorgt“. Die Auslastung der Maschine war so gut, dass Riedel die Werbekampagne, die er eigentlich vorbereitet hatte, in der Schublade ließ und stattdessen drei Wochen später auf der Formnext direkt die zweite Maschine bei ExOne bestellte. „Und jetzt sind die Kapazitäten im Prinzip schon wieder zu gering“, freut sich Riedel.
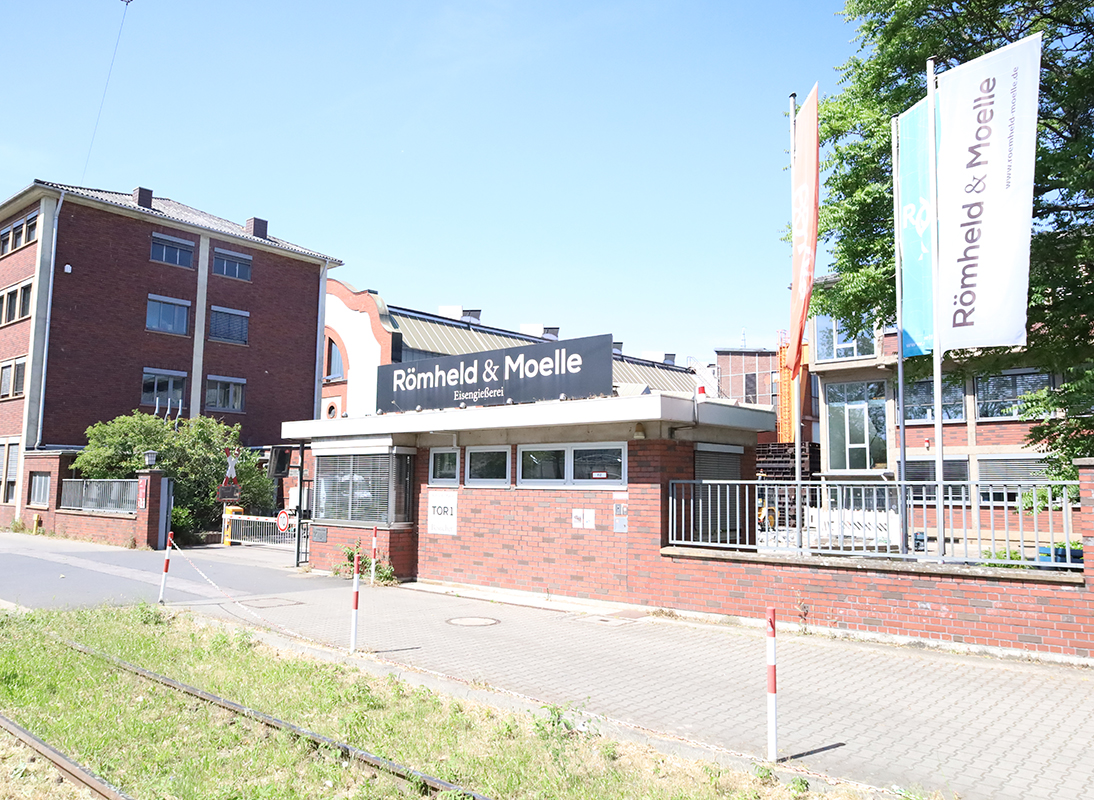
Traditionsunternehmen in Mainz: Römheld & Moelle. Bild: Thomas Masuch
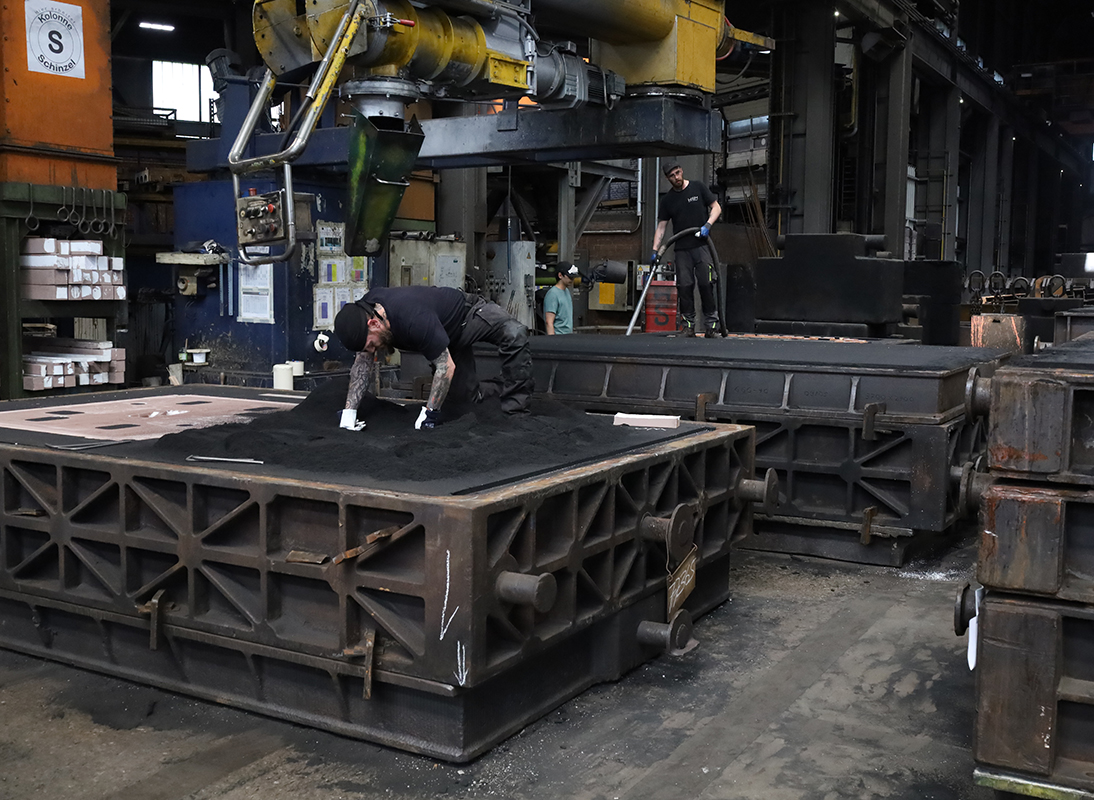
Harte Arbeit: Die Formkästen werden mit Sand gefüllt. Bild: Thomas Masuch
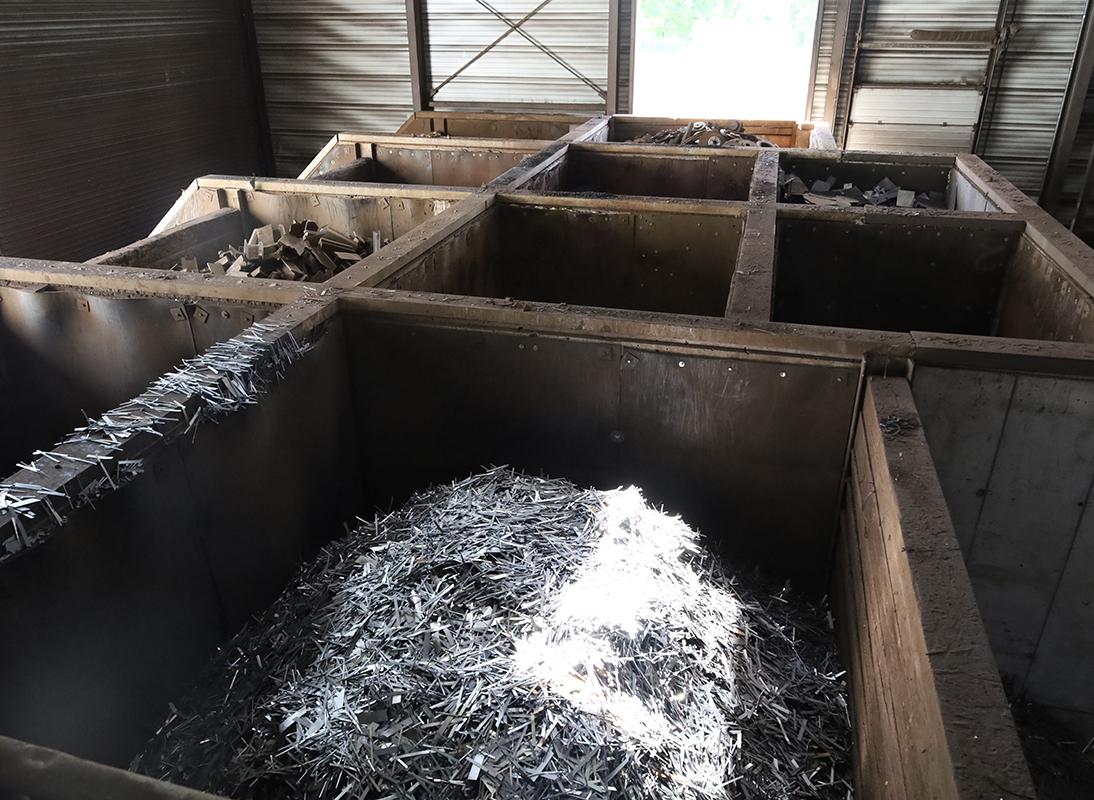
Die Rohstoffe, die der Ofen nachts verschlingt, liegen in zehn Silos bereit. Bild: Thomas Masuch
Stromverbrauch wie eine Kleinstadt
Wir steigen über eine schmale Leiter in den Kommandostand der Gießerei: Von einer engen Kabine aus wird der Induktionsofen gesteuert, in dem nachts bis zu 40 Tonnen Gusseisen auf Temperaturen von bis zu 1.400 Grad erhitzt werden. Das flüssige Gusseisen fließt eine Etage weiter unten in schwere Kessel, die dann am Kran durch die Halle schweben und von dort aus das gelb leuchtende flüssige Metall in die vorbereiteten Formen gießen.
Dass bei Römheld & Moelle ausschließlich nachts gegossen wird, liegt zum einen am günstigeren Strompreis zu dieser Stunde. „Außerdem würden wir zu bestimmten Jahreszeiten tagsüber einfach nicht genug Strom beziehen können“, erklärt Betriebsleiter Christian Elspaß. Immerhin hat der Induktionsofen eine Leistungsaufnahme von 9 Megawatt und verbraucht damit etwa so viel Energie wie eine Kleinstadt mit 8.000 Einwohnern. „Trotzdem sind wir damit schon sehr energieeffizient, insbesondere im Vergleich zu Öfen, die mit Kohle oder Gas befeuert werden.“ Außerdem wird der Strom laut CEO Riedel zu 100 Prozent aus Wasserkraft bezogen.
Die Rohstoffe, die der Ofen nachts verschlingt, liegen in zehn Silos bereit: In meterhohen Haufen warten hier glänzende Metallstreifen, zerkleinerte Platten oder Bremsscheiben. Die richtige Mischung wird automatisch mit einem Magneten in den Ofen verfrachtet. „Wir sind eine der modernsten Gießereien Europas“, erklärt Elspaß.
Digitalisierung und Transparenz
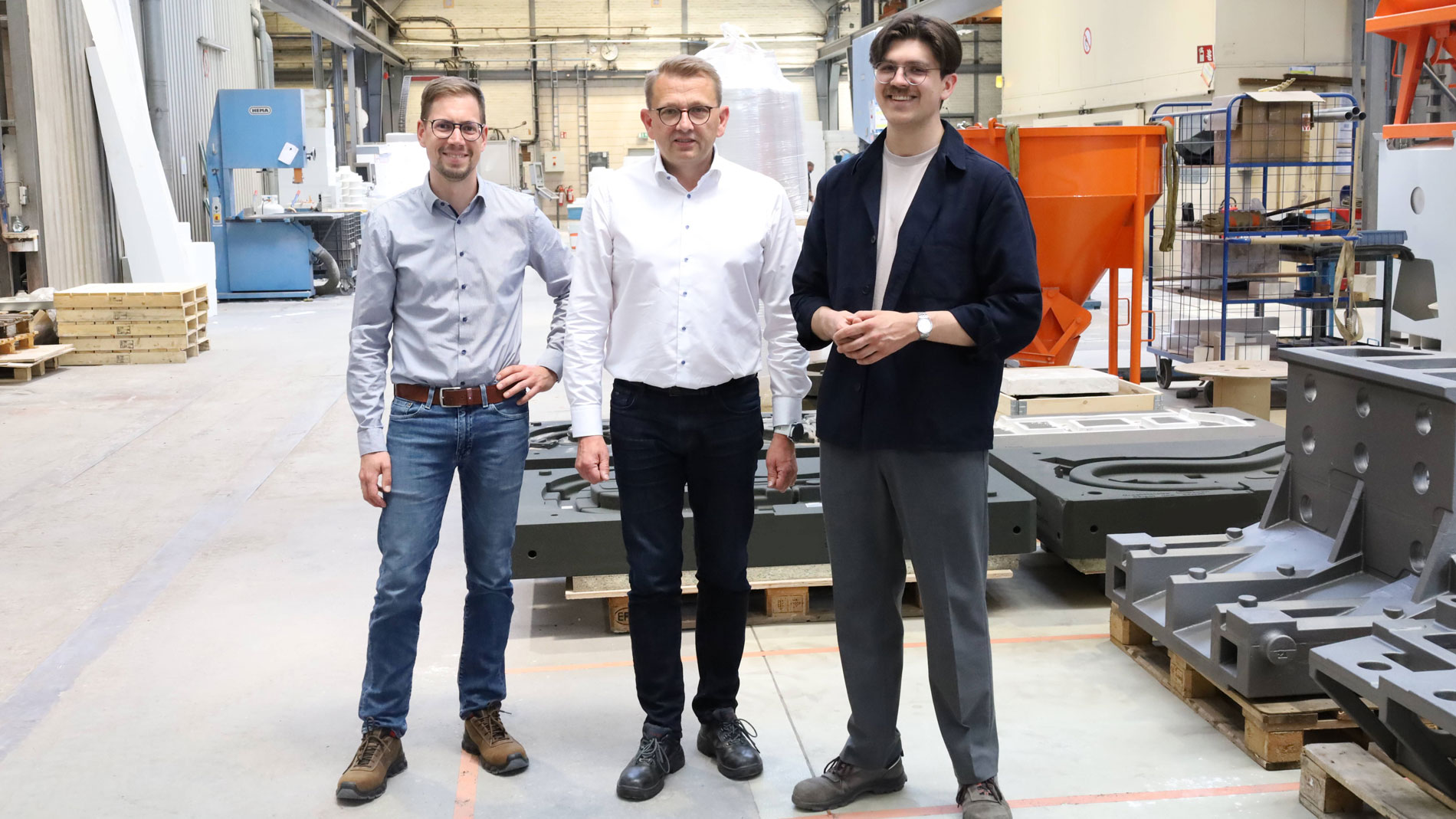
Diese Entwicklung der Gießerei will Geschäftsführer Riedel mit Printed Casting und einer konsequenten Digitalisierung weiter vorantreiben und nebenbei der gesamten Gießerei-Branche ein neues Image geben. Ein Baustein der Modernisierung ist, dass das Mainzer Unternehmen den Produktionsstand (von der Konstruktion über die Modellerstellung und den Guss bis zur Auslieferung) transparent macht und so über seine Liefertreue informiert. „Das hilft nicht nur Kunden bei der Planung, sondern sorgt auch intern für einen zusätzlichen Antrieb, wenn die angestrebten Termine knapp werden“, erklärt Riedel, der vor seiner Tätigkeit bei Römheld & Moelle bei verschiedenen anderen Industriebetrieben als Geschäftsführer tätig war. „In anderen Branchen ist diese Transparenz bereits etabliert, für die Gießerei-Industrie, in der sich in den letzten Jahrzehnten kaum etwas verändert hat, ist das noch etwas ganz Neues.“
Nach dem Gießen kühlen die gegossenen Teile – je nach Größe – einige Tage oder Wochen ab und werden dann nachbearbeitet – und zwar in einer rund sechs Meter hohen Sandstrahlanlage, die aussieht wie die Schuhschachtel eines Riesen. In einer weiteren Halle sammeln sich teilweise mehrere Meter große Bauteile: manche quadratisch und innen hohl, andere länglich oder rund, alle in der Regel mehrere Tonnen schwer. Männer entfernen mit Winkelschleifern Gussreste oder metallische Klötze, die zur gelenkten Abkühlung in die Formen integriert waren. Vergleichsweise winzig wirken die Gussteile an der Wand gegenüber, die mit den 3D-gedruckten Formen hergestellt wurden – obwohl auch diese mehrere Hundert Kilogramm wiegen.
10 Kilogramm bis 25 Tonnen
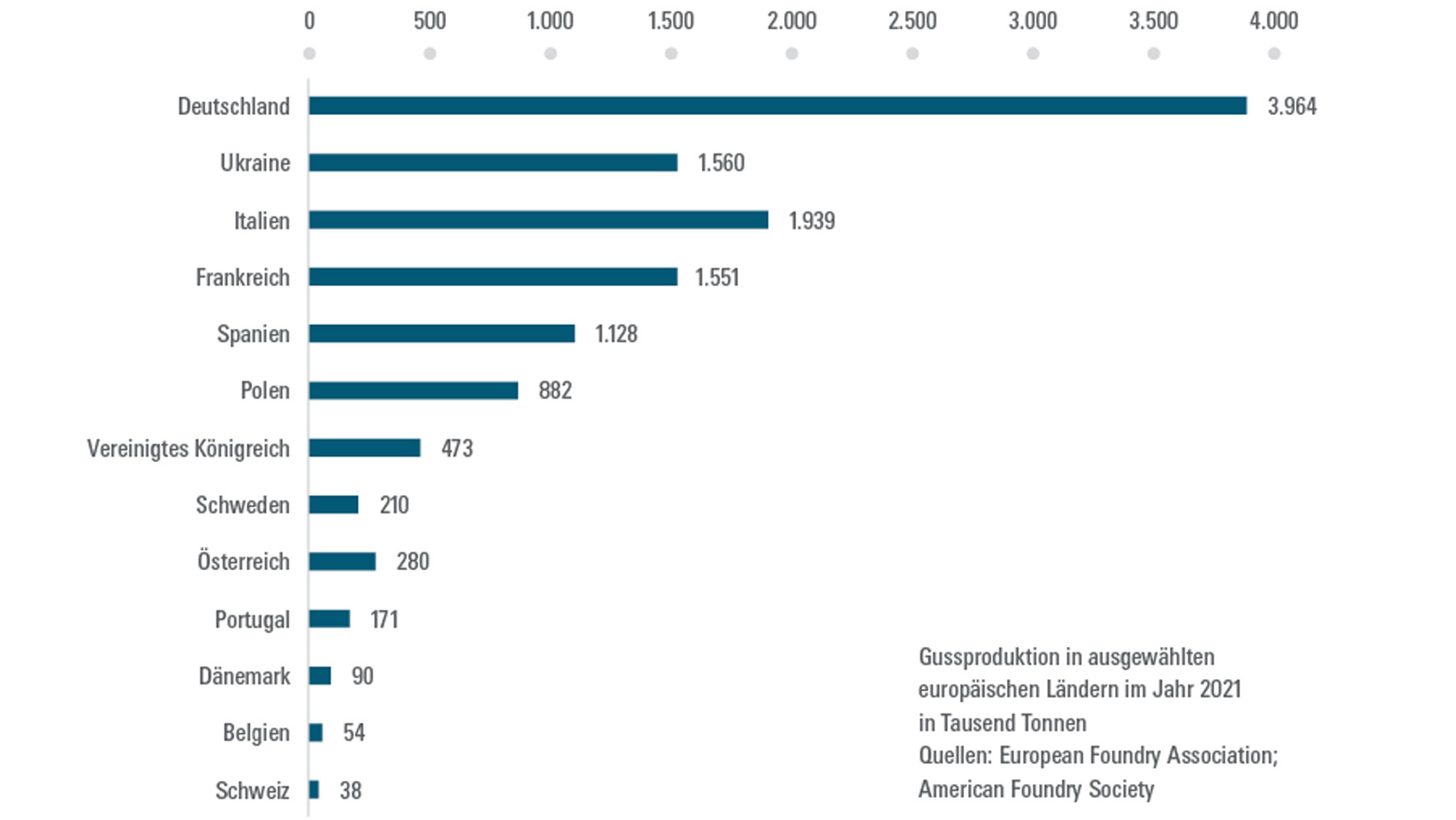
Doch diese Bauteile sind filigraner und deutlich komplexer gestaltet. Sie werden später in Werkzeugmaschinen oder großen Anlagen verbaut oder dienen als Bohrvorrichtungen. „Mit dem Printed Casting fertigen wir oftmals Sondergrößen zum Beispiel für einen der größten Hersteller von Werkzeugmaschinen weltweit“, erklärt Riedel. „Auch Teile, die vormals geschweißt wurden, gießen wir jetzt.“
Kerngeschäft der Großgießerei sind bis zu 25 Tonnen schwere Umformwerkzeuge für die Automobilindustrie, doch für diese Branche erwartet Riedel in den nächsten Jahren eher eine Stagnation. Umso erfreulicher ist aus Sicht der Mainzer Gießerei, dass sich mit dem Printed Casting ein neuer Produktbereich eröffnet hat. „Damit können wir jetzt auch Anfragen für Bauteile ab 10 Kilogramm bedienen – dabei stellten sich unsere Gießer für Bauteile unter einer Tonne normalerweise bisher nicht den Wecker“, schmunzelt Riedel. Schließlich sei der Guss so leichter Bauteile im klassischen Betrieb einer Großgießerei viel zu aufwendig.
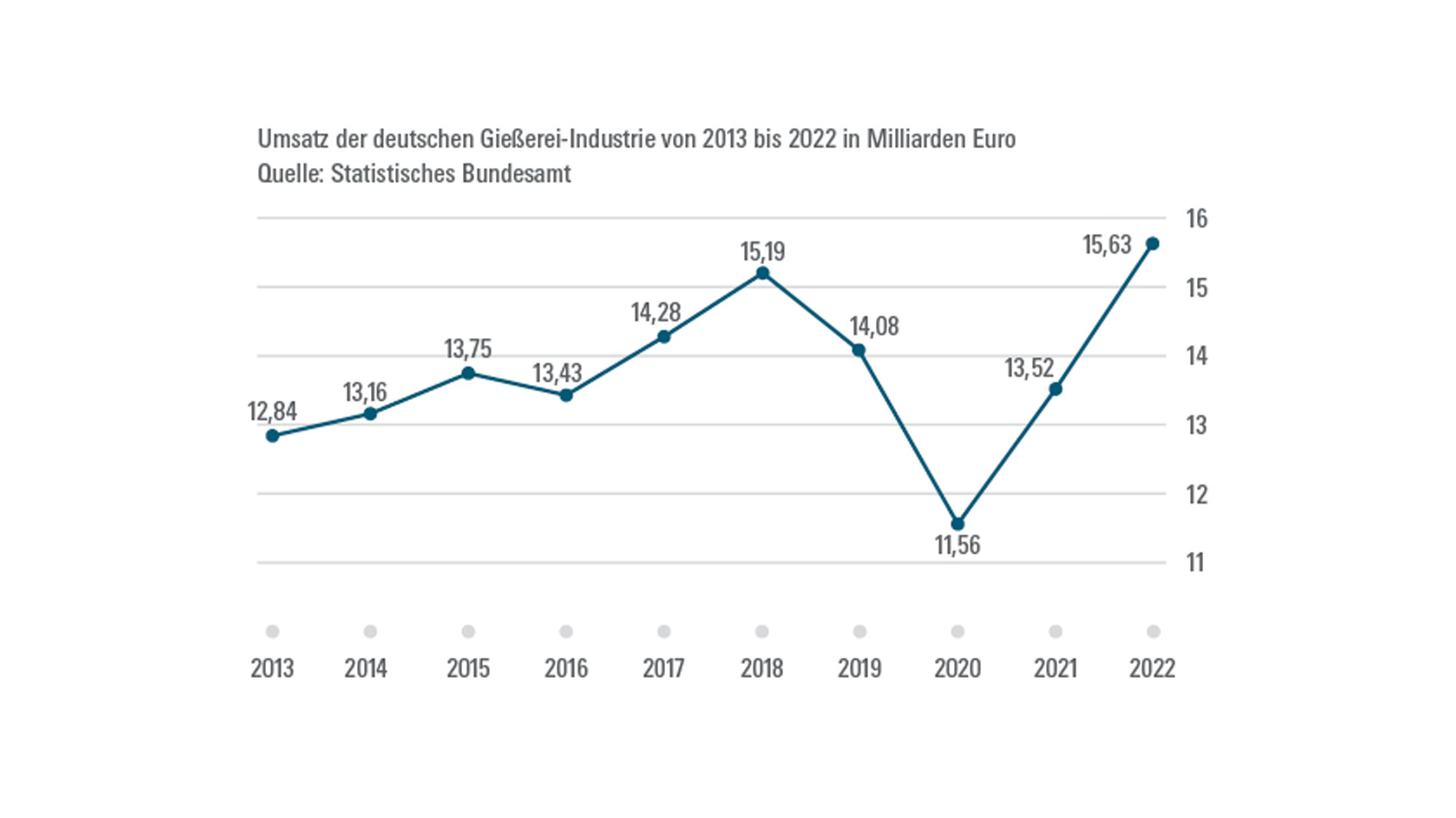
Dabei sieht Riedel das Printed Casting als ergänzende Fertigungsmethode, die aber auch in Konkurrenz zum Gießen mit Holzmodellen sowie zur additiven Metallfertigung steht. „Unseren Kunden können wir die Vorteile des 3D-Drucks bieten – nämlich Designfreiheit – und gleichzeitig zu einem Bruchteil der Kosten des Metall-3D-Drucks fertigen.“ Umgesetzt wurde dies zum Beispiel bei einer rund einen Meter hohen Bohrvorrichtung, die laut Riedel „mit einer anderen Gussmethode nicht herstellbar gewesen wäre. Auch die Zeitkomponente ist für den Geschäftsführer bei vielen Aufträgen ein sehr wichtiger Faktor. „Je nach Material und Größe des Bauteils können wir dank Printed Casting innerhalb von zwei Wochen liefern.“ In einer Branche, in der Lieferzeiten von mehreren Monaten zur Regel gehören, ist das sehr beachtlich. Durch diese Schnelligkeit und Flexibilität hat sich Römheld & Moelle auch als Zweitlieferant bei anderen Gießereien ins Spiel gebracht, wenn diese aufgrund eines hohen Auftragsbestands die Vielzahl der eigenen Bestellungen zeitweise nicht abarbeiten können oder vor dem Serienanlauf Prototypen benötigen.
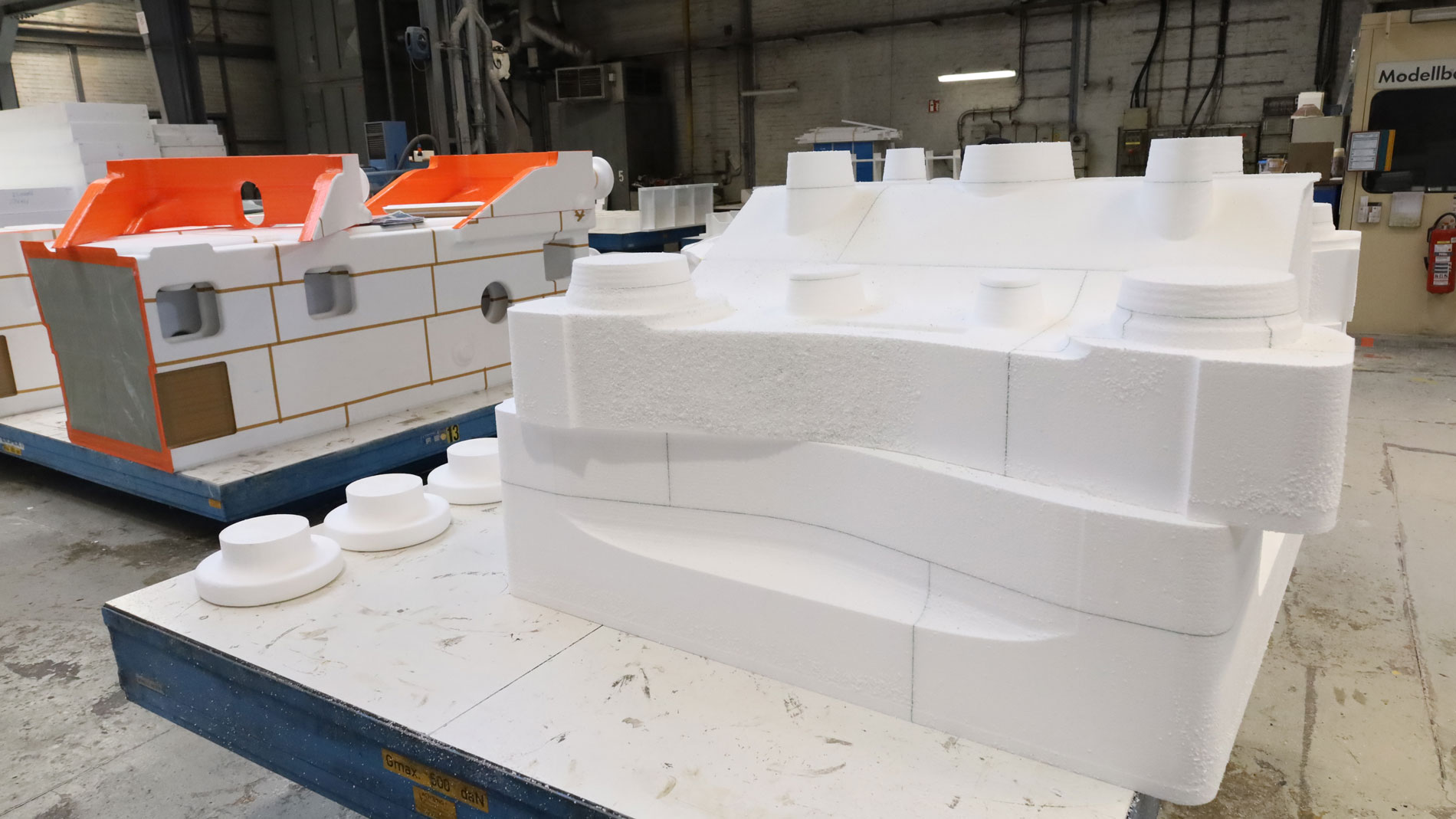
Diese klassischen Styropormodelle werden gefräst, später in die Formkästen gelegt und mit Sand dicht umschlossen. In diese fließt später flüssiges Eisen und füllt den Platz des Styropors aus, das bei den hohen Temperaturen vergast. Bild: Thomas Masuch
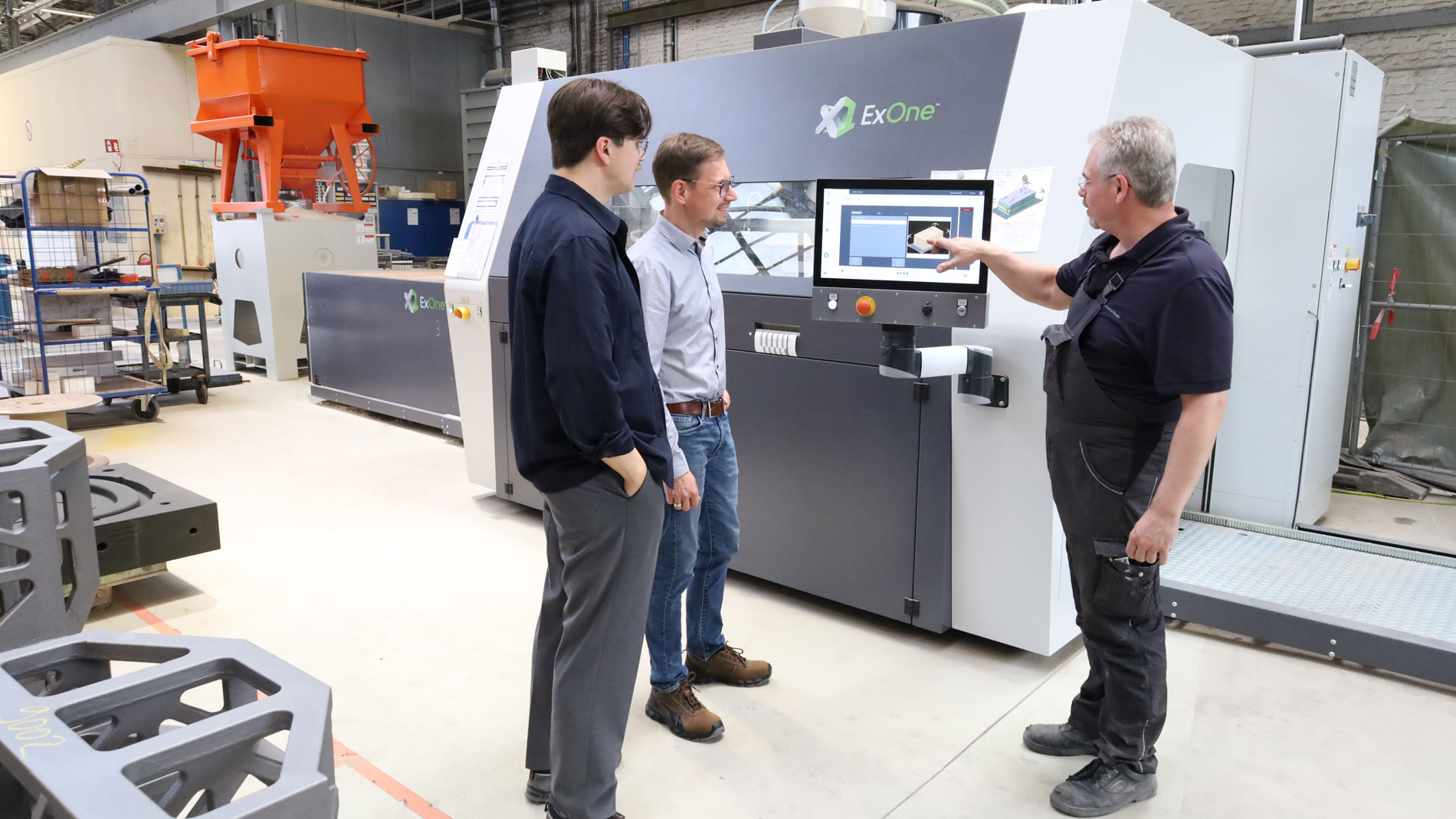
Christian Elspaß und Marcel Tschillaev im Gespräch am 3D-Sanddrucker von ExOne. Bild: Thomas Masuch
„Zu wenig Gießer, die dieses Verfahren nutzen“
Für Riedel ist es deshalb schwer verständlich, dass die Fertigungsmethode nicht viel häufiger eingesetzt wird – zum Beispiel auch im Ersatzteilwesen für Schienenverkehr, Baufahrzeuge oder Landmaschinen. „Oft wird sie aber nur für Formenkerne verwendet. Obwohl die Hersteller der 3D-Drucker für Sandformen inzwischen mehrere Hundert Drucker weltweit verkauft haben und auch selbst Sandformen anbieten, gibt es immer noch viel zu wenig Gießer, die dieses Verfahren nutzen.“ Weitere mögliche Anwendungsfälle sieht der Geschäftsführer bei Motorengehäusen, Komponenten für Pumpen, Propellern, Ventilen oder auch „bei Unternehmen, die heute noch gar nicht an Guss denken“.
Demzufolge ist für den Verfahrensingenieur Riedel die Grenze des Printed Casting in der gesamten Gussbranche bei Weitem noch nicht erreicht. Als Potenzial für den Guss mit 3D-gedruckten Formen hält Römheld & Moelle einen Marktanteil von 1 Prozent für realistisch. Das klingt erst einmal wenig, steht aber allein bezogen auf die Gussindustrie in Deutschland mit einem Umsatz von rund 15 Mrd. Euro immerhin für einen Betrag von rund 150 Mio. Euro (siehe Statistik). Bei Römheld & Moelle kann Printed Casting laut Geschäftsführer Riedel in naher Zukunft sogar einen signifikanten Umsatzanteil von vielleicht 25 Prozent erreichen – „und damit rechne ich nicht in zehn Jahren, sondern deutlich früher“.
Gleichzeitig sieht Riedel das Printed Casting auch als Alternative zum Metall-3D-Druck. „Wir können hier ebenso komplexe Strukturen erreichen und sind um den Faktor 10 und mehr günstiger.“ Darüber hinaus biete der Guss mit gedruckten AM-Formen auch einen weiteren entscheidenden Vorteil: Diese Technologie und die Materialien sind laut Riedel bewährt, seitdem es Guss gibt, „die Zertifizierung ist kein Thema“.
In die 3D-gedruckten Formen werden Kühleisen eingesetzt, die später, nach dem Gießen, beim Abkühlen die Temperaturverteilung beeinflussen und den Erstarrungsprozess verbessern. Fotos: Thomas Masuch
Große Formen aus 3D-gedruckten Segmenten
In der ruhigsten Produktionshalle, in der auf großen Portalmaschinen Segmente für die Styropormodelle gefräst werden, finden sich auch die beiden 3D-Sanddrucker von ExOne. Um 3D-Druck noch effizienter aufzustellen, wurde im Februar 2023 auch offiziell eine AM-Abteilung gegründet. Neben Abteilungsleiter Marcel Tschillaev, der nach seinem Maschinenbaustudium 2021 bei Römheld & Moelle einstieg, arbeiten hier drei Konstrukteure und vier Produktionsmitarbeiter.
Neben einer der Maschinen entfernen zwei Mitarbeiter vorsichtig den hellen Sand von kegelförmigen Luftpfeifen, die vom Bindermaterial dunkel eingefärbt sind. „Diese drucken wir mit, wenn noch Platz auf der Druckplatte ist. So können wir den Drucker noch besser ausnutzen“, erklärt Tschillaev. Die Luftpfeifen werden beim Gießvorgang auf die Formen gesetzt, sodass aus ihnen die mehr als 1.000 Grad heißen Gase in einer bunten Flamme kontrolliert entweichen.
Ein weiterer Kollege setzt in eine am Kran hängende Form vorsichtig ein Dutzend Stahlklötze, sogenannte Kühleisen, ein, die später nach dem Gießen beim Abkühlen die Temperaturverteilung beeinflussen und den Erstarrungsprozess verbessern. Bei den Styropormodellen werden die Kokillen per Hand so gut es geht an gekennzeichnete Positionen auf das Modell aufgelegt. „Beim 3D-Druck ist die Positionierung deutlich exakter. Hier stimmen Gießsimulation und Realität zu 100 Prozent überein“, so Betriebsleiter Elspaß.
Dank der 3D-gedruckten Formen lassen sich sehr komplexe und große Bauteile gießen. Fotos: Thomas Masuch
Ein weiterer Kollege setzt in eine am Kran hängende Form vorsichtig ein Dutzend Stahlklötze, sogenannte Kühleisen, ein, die später nach dem Gießen beim Abkühlen die Temperaturverteilung beeinflussen und den Erstarrungsprozess verbessern. Bei den Styropormodellen werden die Kokillen per Hand so gut es geht an gekennzeichnete Positionen auf das Modell aufgelegt. „Beim 3D-Druck ist die Positionierung deutlich exakter. Hier stimmen Gießsimulation und Realität zu 100 Prozent überein“, so Betriebsleiter Elspaß.
Gleichzeitig haben Tschillaev und sein Team auch eine Möglichkeit gefunden, wie sie im 3D-Druck sehr große Formen für Gussteile von bis zu mehreren Tonnen herstellen können. Dafür wird eine Vielzahl von Sandformsegmenten gedruckt und zu einer Form zusammengesetzt. Das erfordert allerdings eine sehr durchdachte Konstruktion, damit später das flüssige Eisen die Form behutsam und von Grund auf füllt. Auf diese Weise entstanden auch schon Gussteile für Industriepressen von Andritz Kaiser (wir berichteten in Ausgabe 02/2023).
Für Laien mag der Name vielleicht verwirrend sein, aber bei Gusseisen handelt es sich nicht um reines Eisen, sondern in der Regel um Legierungen. Der Unterschied zu Stahl besteht im höheren Gehalt von Kohlenstoff, was die Eigenschaften der Bauteile (z. B. Härte und Zähigkeit) verändert und zudem für den Gussprozess große Vorteile bringt: Denn der hohe Kohlenstoffanteil sorgt dafür, dass das Bauteil beim Abkühlen seine Form nur relativ wenig verändert, während ein gegossenes Stahlteil stark schrumpfen würde. Bilder: Römheld & Moelle
Eigene Plattform kalkuliert Preise und CO2-Ausstoß
Mit der eigenen Erfolgsgeschichte und den vielfältigen Möglichkeiten möchte Riedel auch andere Gießereien zum Printed Casting motivieren – schließlich sei der Markt groß genug, um genügend Geschäft auch für andere bereitzuhalten. Riedels branchenweite Überzeugungsarbeit, die die Hersteller von Sandformen-Druckern kaum genug würdigen können, ist aber nicht ganz uneigennützig: Riedel hat mit seinem Team die digitale Plattform Castfast aufgebaut, die automatisch Preise und CO2-Ausstoß kalkuliert und den Beschaffungsprozess für Gusskunden deutlich vereinfacht und beschleunigt. Derzeit sind Bestellungen in den Legierungen möglich, die bei Römheld & Moelle verarbeitet werden. Um das Materialportfolio von Castfast zu erweitern, sucht Riedel weitere Gießereien als Partner.
Reizvoller als Serienfertigung
Mit der digitalen Ausrichtung und dem 3D-Druck „wollen wir den Guss wieder cool machen“, erklärt Riedel, der auch beklagt, dass diese Technologie und gussgerechtes Konstruieren „in der Ausbildung leider vernachlässigt wird und zum Beispiel im Maschinenbaustudium keine große Rolle mehr spielt“. Dabei bietet das Printed Casting deutlich größeren Spielraum bei der Gestaltung von Teilen als andere Fertigungsverfahren, bestätigt Marcel Tschillaev. „Wir fertigen fast jeden Tag andere Teile, das hat wirklich seinen Reiz für uns Techniker – ganz anders als die Serienfertigung.“
Eine weitere durch den 3D-Druck ausgelöste Veränderung begegnet uns beim Abschied: Zwischen den Werkhallen reißen Arbeiter den Pflastersteinboden, über den seit mehreren Jahrzehnten die Formen über den Hof gefahren werden, mit dem Presslufthammer auf. Der rumpelige Untergrund war ein Risiko beim Transport der komplexen Sandformen aus dem 3D-Drucker. In Zukunft wird der Übergang zwischen den Hallen glatt und eben sein.
MEHR INFOS UNTER:
Weitere Informationen zum 3D-Druck von Sand im Binder-Jetting Verfahren im AM-Field-Guide.
Tags
- Werkzeug- und Formenbau