Text: Thomas Masuch; Fotos: PFW — 06.09.2020
Während sich die Luftfahrtindustrie durch den Einsatz Additiver Fertigung bessere Designs und letztlich leichtere Jets verspricht, verfolgt der Luftfahrtzulieferer PFW Aerospace GmbH im pfälzischen Speyer eine ganz andere Strategie: Das Unternehmen, das unter anderem für Airbus und Boeing fertigt, will mithilfe von industriellem 3D-Druck schlicht und einfach Material sparen und damit seine Produktionskosten senken. Was recht simpel klingt, könnte in den nächsten Jahren den Wettbewerb in der Branche verändern.
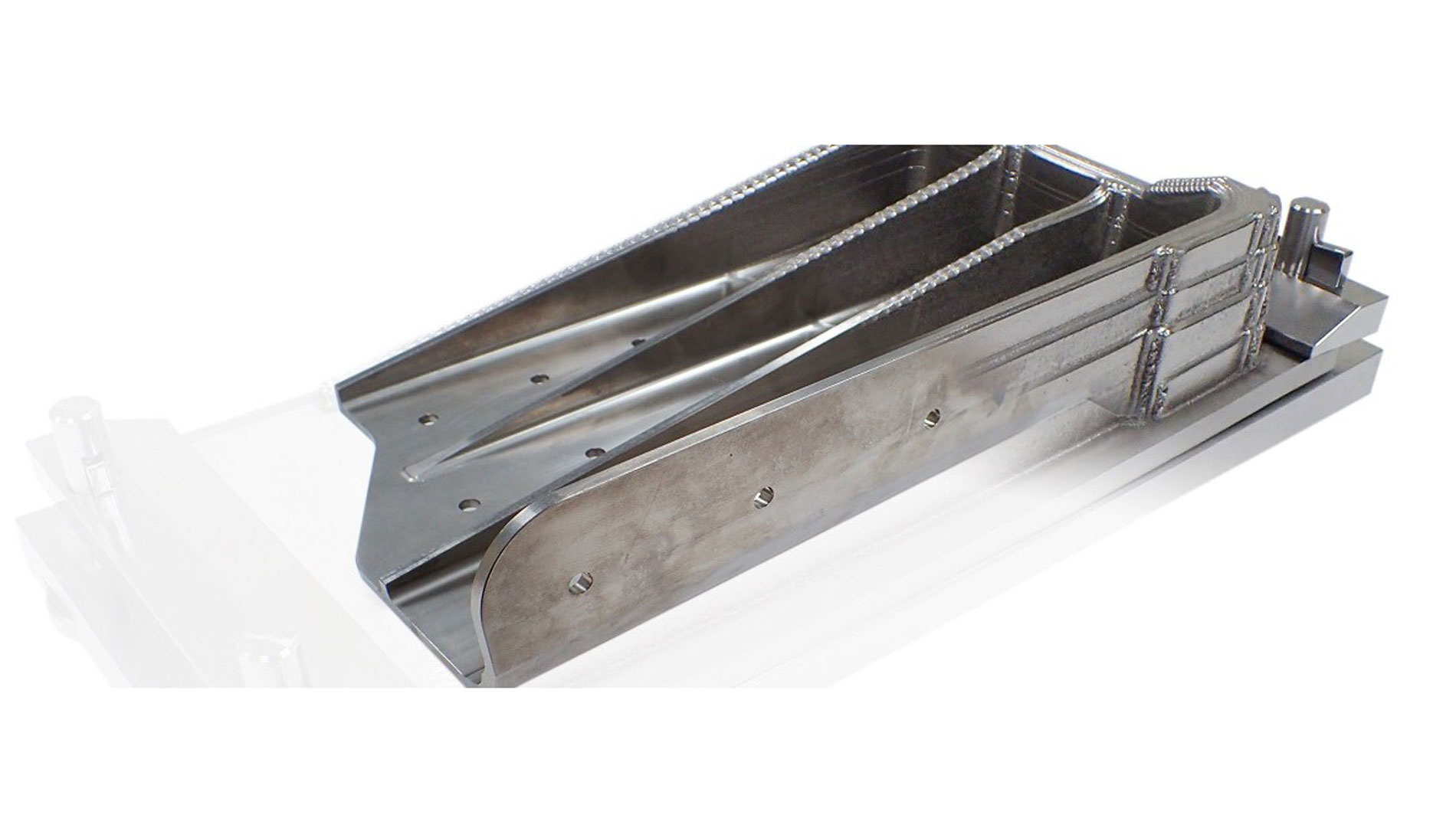
Seit sieben Jahren beschäftigt sich Dr. Markus Gutensohn, Leiter der Fertigungstechnologie bei PFW, in seiner Abteilung mit Additiver Fertigung. Zunächst wurden die Pulverbetttechnologien erforscht; die Erkenntnis daraus war anfangs ernüchternd, langfristig für das Unternehmen aber umso wertvoller: »Wir haben im Unternehmen keine Bauteile, bei denen der Einsatz von SLM-Technologie einen wirtschaftlichen Mehrwert bringen würde.«
Ein wichtiges Geschäftsfeld des Luftfahrtzulieferers mit 107-jähriger Geschichte und über 2.200 Mitarbeitern sind Rohre. »Da bringt zum Beispiel eine Topologie-Optimierung nichts – denn ein Rohr hat schon die bionisch perfekte Form«, erklärt Gutensohn. Anstatt hinter dem 3D-Druck einen Haken zu machen, suchten Gutensohn und seine Ingenieure nach einer anderen additiven Fertigungstechnologie und änderten ihre Strategie.
Tobias Theel ist einer der Ingenieure, die sich bei PFW hauptsächlich mit Additiver Fertigung beschäftigen. Der 27-Jährige fand heraus, »dass sich für uns die Technologien eignen, die eine höhere Aufbaurate haben – zum Beispiel das Pulverauftragschweißen«. Und anstatt Bauteile mit Designprogrammen zu optimieren, »betrachten wir unsere bestehenden Teile und schauen, wo wir durch den Einsatz additiver Fertigung günstiger werden können«.
"Unsere Wünsche fließen hier teilweise direkt in die Entwicklung der nächsten Maschinengeneration ein."
PFW sieht den Einsatz Additiver Fertigung vor allem dort, wo Titanbauteile aus dem Vollen zerspant werden. Hier hat herkömmliche Fräsbearbeitung mit zwei Herausforderungen zu kämpfen: Erstens lässt sich das feste und zähe Metall nur schwer zerspanen, was sich in langen Maschinenlaufzeiten und einem hohen Werkzeugverschleiß äußert. Und zweitens ist der Materialpreis mit rund 50 Euro pro Kilogramm Flugzeugtitan recht hoch. Da bisher in den Fräsmaschinen oftmals 90 Prozent der Materialblöcke in Späne verwandelt werden, ergibt sich das große Einsparpotenzial. Denn mittels DED (»directed energy deposition«) lässt sich die sogenannte »buy-to-fly ratio«, die das Gewicht des Rohmaterials und des gefertigten Bauteils ins Verhältnis setzt, von derzeit 9 : 1 auf 2 : 1 minimieren, so Theel.
Partnerschaft entlang des Rheins
Um dieses Ziel zu erreichen, gingen die Ingenieure aus Speyer als eines der ersten Unternehmen der Branche eine Partnerschaft mit BeAM ein. Der Sitz des jungen Herstellers von Anlagen zum Pulverauftragschweißen, eine Verfahrensvariante von DED, liegt nur etwa 120 Kilometer rheinaufwärts im französischen Straßburg. »Da ist auch schnell ein Techniker vor Ort, wenn wir mal eine Herausforderung haben«, erklärt Gutensohn. In seiner Abteilung werden zahlreiche Fertigungstechnologien des Unternehmens entwickelt und verbessert – wie Automatisierung, Industrie-4.0-angepasste Arbeitsplätze oder die Optimierung des Rohrbiegens. Von den 16 Ingenieuren kümmern sich vier ausschließlich um Additive Fertigung.
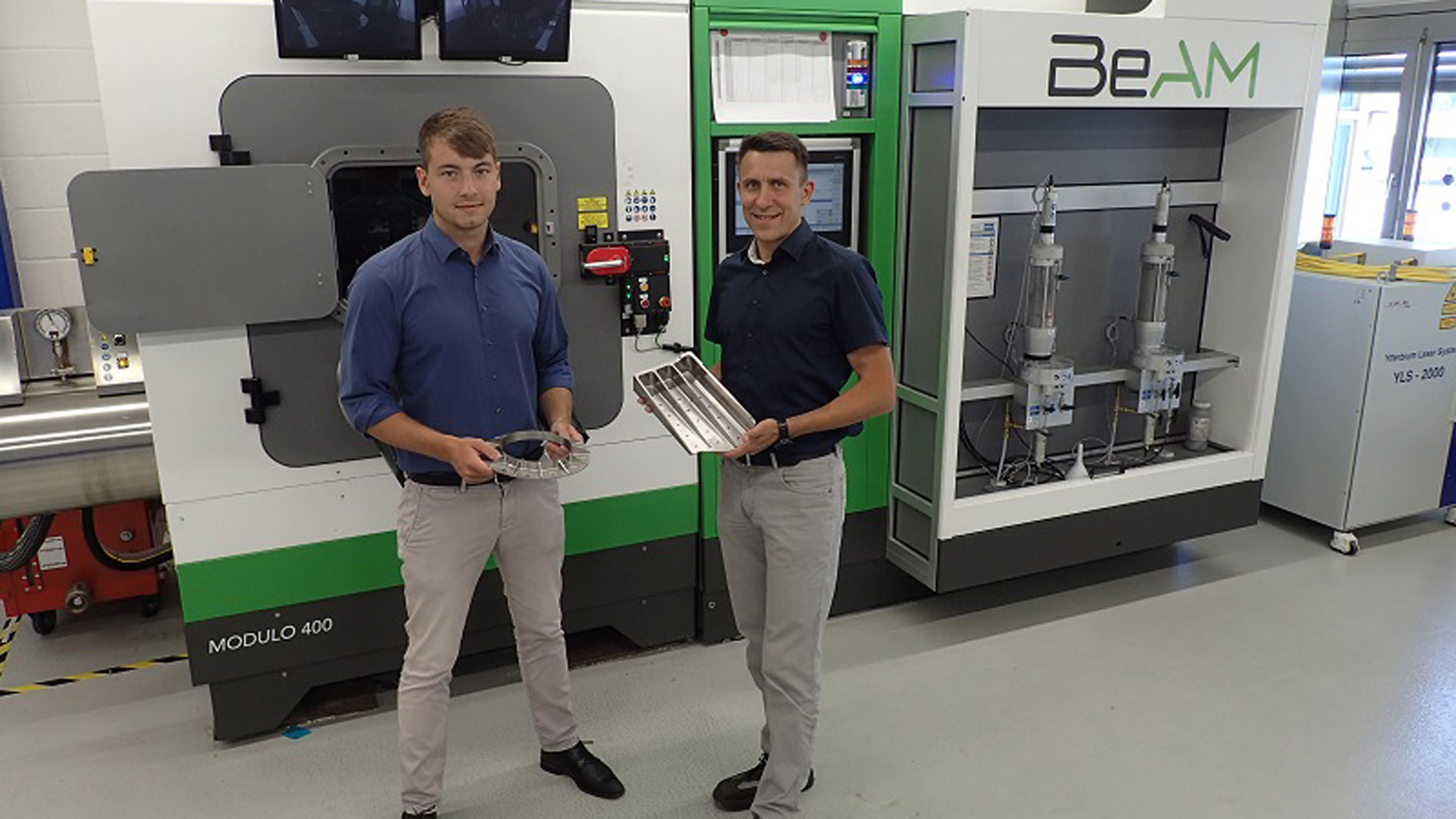
Seit Mitte 2018 steht eine Modulo 400 von BeAM bei PFW. Hier wurden inzwischen zahlreiche Bauteile sowie Probekörper für Zugversuche gefertigt und andere Untersuchungen vorgenommen. Gleichzeitig arbeitet PFW eng mit BeAM zusammen, »um die Maschine für die industrielle Serienproduktion weiterzuentwickeln«. Um die eigenen Anforderungen besser definieren zu können, haben die PFW-Ingenieure selbst eine AM-Anlage zum Drahtauftragschweißen entwickelt und gebaut. Die Maschine mit 3-kW-Laser kann unter globaler Schutzgasatmosphäre Bau- und Testteile 3D-drucken und »ermöglicht uns, einen Benchmark zwischen pulver- und drahtbasiertem Laserauftragschweißen zu erstellen«, so Gutensohn.
PFW ist laut Gutensohn bei der industriellen Nutzung der Laserauftragschweiß-Technologie weit vorn und kann so dem Anlagenhersteller wertvolle Referenzen liefern. So spezifiziert PFW zum Beispiel Anforderungen, die die Anlagentechnik weiter industrialisieren sollen. Dabei geht es unter anderem um die Verringerung der Rüst- und Nebenzeiten und um die Optimierung von Wartungen und Prozessüberwachungen. Gutensohn schätzt dabei auch die Flexibilität des jungen französischen Unternehmens: »Unsere Wünsche fließen hier teilweise direkt in die Entwicklung der nächsten Maschinengeneration ein. Bei einem großen Hersteller würde unsere Stimme sicherlich deutlich weniger zählen.«
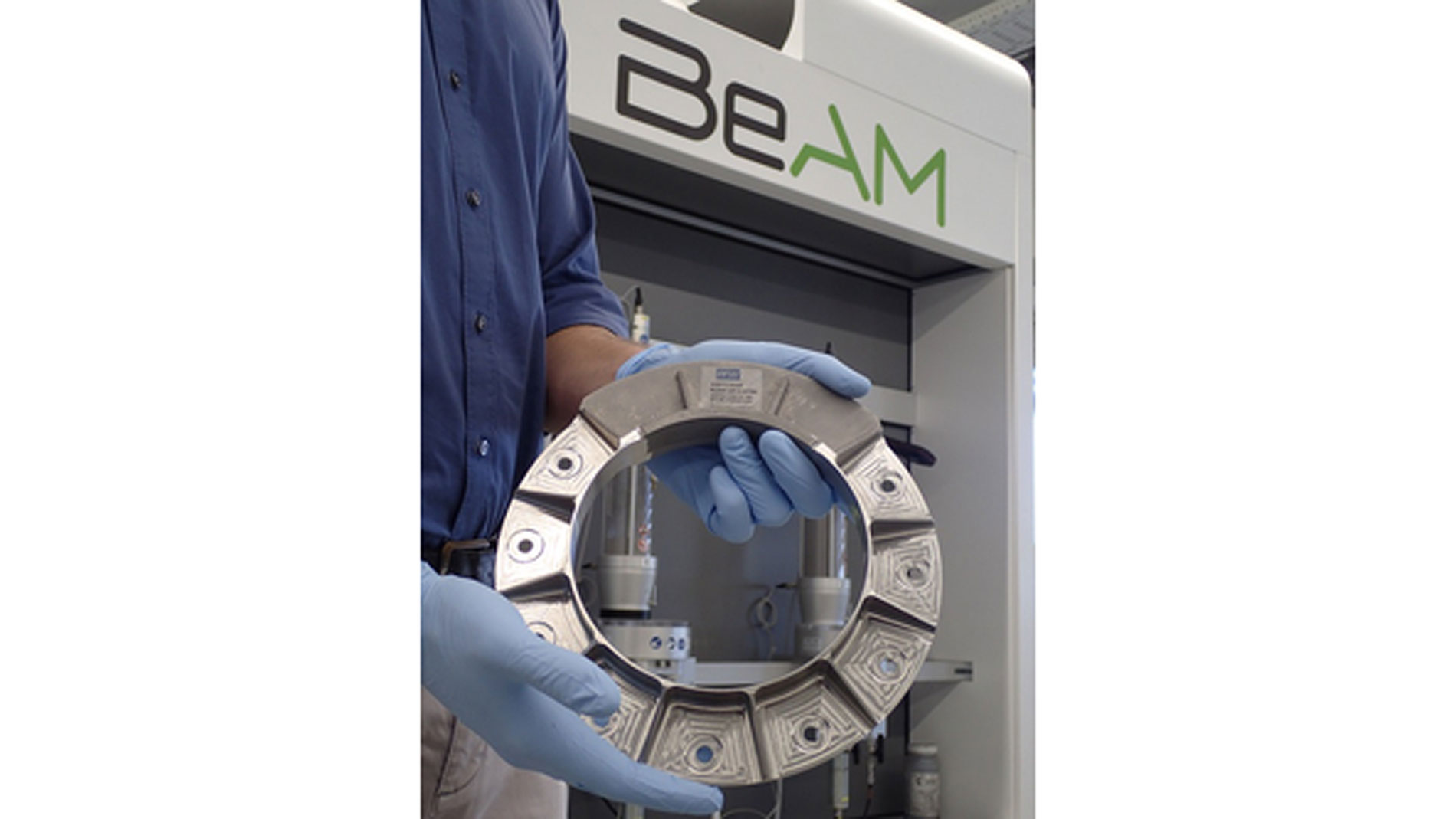
Für Frédéric Le Moullec, Business Development Director bei BeAM, steht »die Zusammenarbeit mit unseren Kunden und die Integration deren Feedbacks im Mittelpunkt unserer Entwicklungsstrategie.« Die DED-Technologie habe sich im Luftfahrtsektor seit langem für die Reparatur von Teilen etabliert und entwickle sich nun zu einem industriellen Verfahren zur Herstellung von Teilen mit hoher Wertschöpfung. »Die Partnerschaft mit PFW hat es uns ermöglicht, ein großes Fachwissen in diesem Bereich zu entwickeln und die Industrialisierung der Produktion bei PFW weiter zu begleiten. Durch den gegenseitigen Austausch konnte die Inertatmosphäre optimiert und Prozessparameter entwickelt werden, die es ermöglichen, Materialeigenschaften zu erreichen, die den Luftfahrtanforderungen entsprechen.«
Automatisierte Produktion als Ziel
Um sich nicht einseitig abhängig zu machen, wird PFW laut Gutensohn in den nächsten Monaten noch zwei weitere AM-Anlagen anderer Hersteller in den Entwicklungsräumen in Speyer installieren. Wohin die Reise führen soll, offenbart sich im gleichen Gebäude ein Stockwerk tiefer: Hier bestücken Roboter Dutzende Fräszentren. Die gesamte Prozesskette ist so weit wie möglich automatisiert.
Um in der Entwicklung der DED-Technologie so schnell wie möglich voranzukommen, versuchen die PFW-Ingenieure, den ohnehin schon sehr komplexen Prozess »so einfach wie möglich« zu gestalten. So wird ausschließlich ein Pulver der GE-Tochter AP&C verwendet, das bereits beim Elektronenstrahlschmelzen zum Einsatz kommt und dafür von Airbus qualifiziert wurde. Neben einzelnen Bauteilen wie einem Retainer oder Sternflansch stehen neben der Entwicklungsmaschine von BeAM auch zahlreiche Substratplatten zur Parameterentwicklung, mit deren Hilfe in den firmeneigenen Labors zum Beispiel Schliffbilder erstellt oder Zugversuche durchgeführt werden. Damit wollen Gutensohn und Theel statistisch nachweisen, dass DED über einen längeren Zeitraum verlässlich die gleiche Qualität liefert.
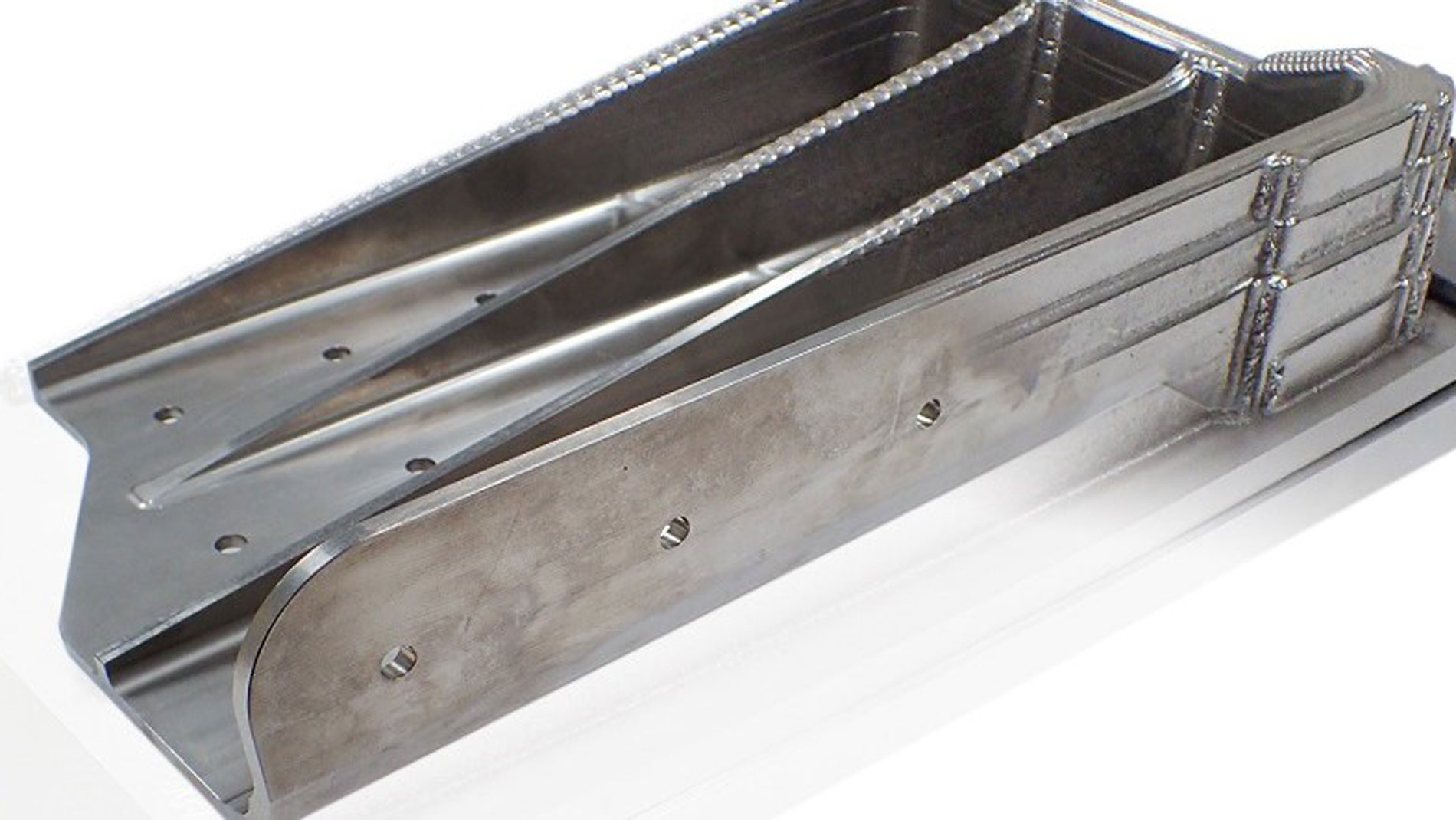
In dieser Prozesskette ist die Additive Fertigung nur ein Puzzlestück, wenn auch das wohl anspruchsvollste. Vom 3D-Drucken über die Wärmebehandlung, das Strahlen und das Fräsen bis hin zum Röntgen und zur Rissprüfung kommen mehr als 15 Prozessschritte zusammen, »und wenn man die Reinigungsprozesse dazurechnet, kommt man sogar auf 25«, erklärt Theel. Sein Chef Gutensohn sieht darin einen entscheidenden Vorteil für sein Unternehmen: »Wir haben viel Erfahrung in allen anderen Fertigungsprozessen und haben diese auch für die Luftfahrt zertifiziert. Dazu können wir sehr gut mit Titan umgehen und wissen, wie das Material in den jeweiligen Bearbeitungsschritten reagiert.«
In der Technologie-Roadmap fest verankert
Denn nur wer die Prozesskette beherrscht, kann Additive Fertigung industrietauglich einsetzen. Bei PFW will Gutensohn bis 2023 so weit sein, »aber vielleicht müssen wir sogar noch schneller werden«. Seine Abteilung entwickelt die Technologie bis zum »Technology Readiness Level« (TRL) 6 und übergibt sie danach an die Produktion. Im Moment ist der DED-Prozess bei PFW bei TRL 4 angekommen.
Dass es mit der Implementierung der Additiven Fertigung beim Speyrer Luftfahrtzulieferer vielleicht schneller gehen muss als geplant, liegt auch an dem enormen Potenzial, das in dieser neuen Produktionsmethode steckt. »Im industriellen Maßstab liegen die Bauteilkosten teilweise sogar unter den aktuellen Materialkosten bei der Zerspanung«, erklärt Gutensohn.
Bei den derzeitigen PFW-Produkten betreffe das weniger als 100 Bauteile. Doch Gutensohn sieht Chancen für mehrere Tausend in einem Flugzeug verbauter Teile. Hier könnte der Einsatz Additiver Fertigung also ein echter Wettbewerbsfaktor werden: Unternehmen, die nicht mitziehen, werden möglicherweise Marktanteile verlieren. Kein Wunder, dass der neue Firmeneigentümer Hutchinson, der Anfang 2020 die Mehrheit an PFW übernommen hat, das Metallauftragschweißen in der Technologie- Roadmap fest verankert hat.
AM-VERFAHREN:
Additive Manufacturing für Metalle - DED-Technologie
Einen strukturierten Überblick in die komplexe und vielschichtige Welt der additiven Fertigungsverfahren, Prozessschritte und Anwendungsfelder liefert Ihnen unser AM Field Guide.
PFW Aerospace GmbH
Bereits 1913 wurden die Flugzeugwerke in Speyer in Sichtweite des berühmten romanischen Doms gegründet. Nach einer wechselvollen Geschichte, zu der zwischenzeitlich auch die Produktion von Fahrzeugen gehörte, entwickelte sich PFW (Abkürzung für »Pfalz-Flugzeugwerke«) zu einem internationalen Zulieferer (sowohl Tier 1 als auch Tier 2), der im vergangenen Jahr einen Umsatz von rund 450 Millionen Euro erwirtschaftete. Rund 1,24 Millionen Teile werden jedes Jahr gefertigt – neben Rohrleitungen unter anderem Landeklappen, Zusatztanks oder Strukturbauteile. Neben dem Hauptwerk in Speyer betreibt PFW auch Werke in England und der Türkei. In seiner Geschichte gehörte PFW zweimal mehrheitlich zu Airbus – als 1996 das Unternehmen verkauft werden sollte, wurde es an die Mitarbeiter übereignet. 2011 übernahm Airbus wieder die Mehrheit und verkaufte 2020 die Anteile an die Hutchinson-Gruppe. Auch wenn die Beziehungen zu Airbus immer noch sehr eng sind, zählt PFW insgesamt 50 Unternehmen zu seinen Kunden, darunter auch Boeing.
Tags
- Luft- und Raumfahrt
- Additive Fertigung