Text: Thomas Masuch — 05.02.2021
Wenn es um den Bau von Raketen und Satelliten geht, ist die additive Fertigung unverzichtbar geworden: Wie nirgendwo sonst kann der industrielle 3D-Druck in der Space-Industrie seine Stärken in Gewichtseinsparung und komplexen Designs ausspielen. Kein Wunder, dass etablierte wie auch junge Unternehmen der Branche immer stärker auf AM setzen. So ist die Space-Industrie inzwischen ein wichtiger Markt für additive Dienstleister, Maschinenhersteller und Anbieter von Materialien und Software. Doch der Einstieg ist nicht einfach: Die Branche ist teilweise geprägt von nationalen Interessen, politischen Befindlichkeiten und gut gehüteten technologischen Geheimnissen. Grund genug, einen genaueren Blick in diese spannende, aber oft schwer zu durchschauende Boom-Branche zu werfen. Im ersten Teil der zweiteiligen Artikelserie geht es um additive Fertigung im Raketenbau.
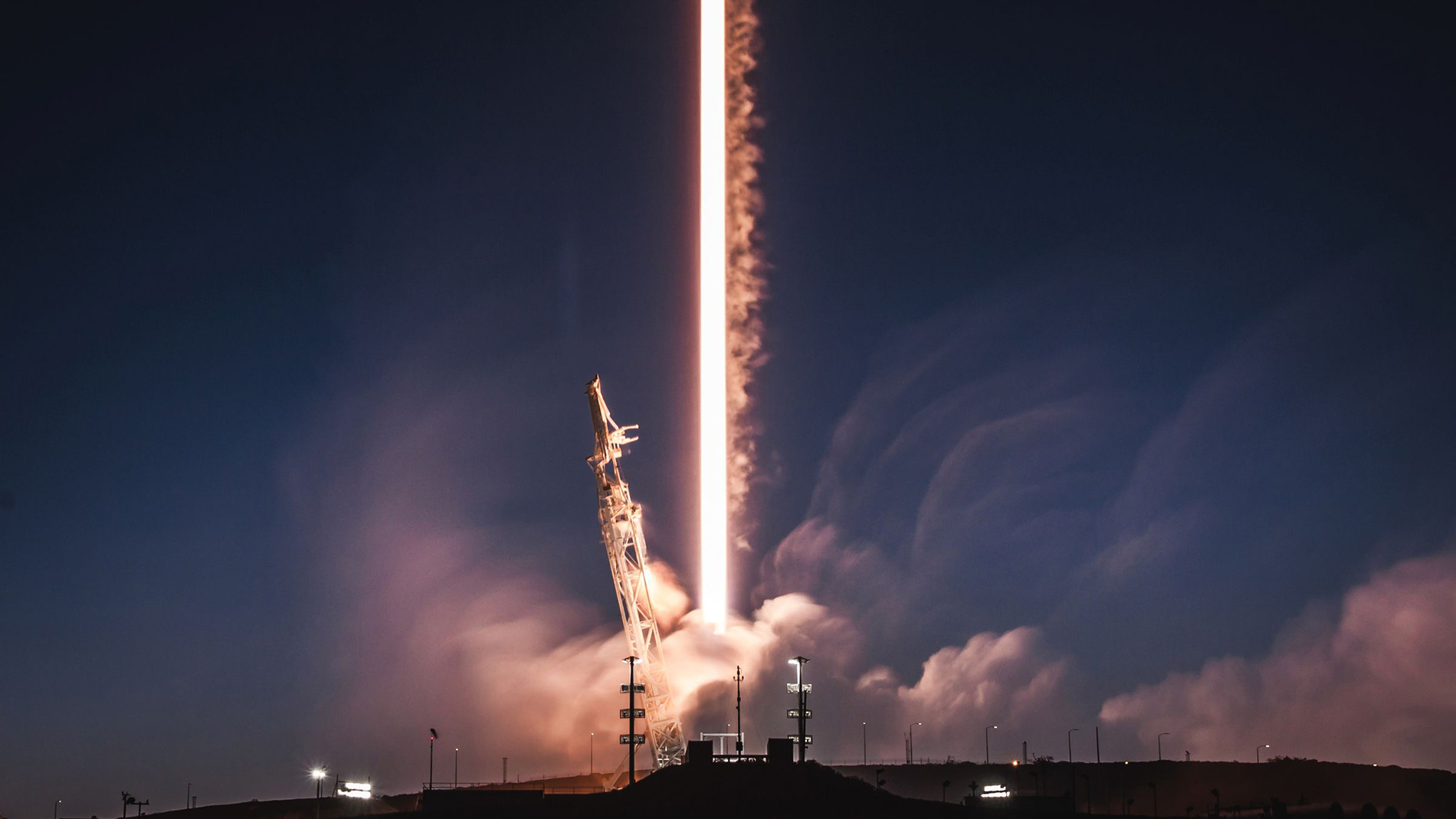
Bei den Anwendern von AM ging Relativity Space den konsequentesten Weg: Mit seinem selbst entwickelten Stargate-3D Drucker will das junge US-Unternehmen ganze Raketen größtenteils additiv fertigen. Das Unternehmen aus Kalifornien wirbt damit, mit seiner 35 Meter hohen Terran 1 „die weltweit erste 3D-gedruckte Rakete herzustellen – vom Rohmaterial zum Flug in 60 Tagen". Damit hat Relativity Space, das 2015 von Tim Ellis und Jordan Noone gegründet wurde und inzwischen 230 Mitarbeiter beschäftigt, in mehreren Finanzierungsrunden rund 550 Mio. Euro eingesammelt und eine Bewertung von knapp 2 Mrd. Euro erreicht. Damit ist es nach SpaceX (Bewertung rund 37 Mrd. Euro) das am zweithöchsten bewertete private Raumfahrtunternehmen. Der Stargate-Wire-Arc-3D-Drucker, dessen Name an ein Videospiel angelehnt ist, bei dem Maschinen andere Maschinen produzieren, ist laut Relativity der weltweit größte Metalldrucker. Ein rund 3,70 mal 2,10 Meter großer Treibstofftank wurde bereits produziert. Die Terran 1 soll Ende 2021 das erste Mal abheben und später bis zu 1,25 Tonnen Nutzlast in die Umlaufbahn bringen.
„Zeitersparnis wird einer der wesentlichen Faktoren sein, der Unternehmen in den 3D-Druck treibt."
Doch nicht nur technologisch leiten Startups wie Astra, Firefly Aerospace, Rocket Lab, Virgin Orbit und andere ein neues Zeitalter hin zu einer „softwaregetriebenen Fertigung" (Relativity Space) ein. Auch von den etablierten Denkstrukturen wollen sich die millionenschweren Newcomer verabschieden. Dazu zählen bei Relativity Space zum Beispiel monatliche „Lunch ’n’ Learn"-Meetings, wo auch schon Gastredner wie Rick Sternbach, der für Star Trek den Schlachtkreuzer der Klingonen konstruierte, oder Adam Mojo Lebowitz, VFX Supervisor bei Battlestar Galactica, aufgetreten sind.
Auch die etablierten Raketenbauer und Zulieferer haben ihre 3D-Druck-Kompetenzen ausgebaut – meist in Form eines eigenen AM-Zentrums und verschiedener Technologiepartnerschaften. 3D-gedruckt werden derzeit vor allem einzelne Komponenten – in der Regel rund um das Antriebssystem und die Brennkammer. Hier sind laut Branchenexperten die größten Kosteneinsparungen möglich. Zudem können die Produktionszeit und die Zahl der verwendeten Bauteile deutlich verringert werden. »Wenn ein Unternehmen wettbewerbsfähig bleiben will, ist AM bei der Herstellung von Antrieben ein Muss«, sagt AM-Experte Terry Wohlers, President Wohlers Associates. „Der Nutzen von additiver Fertigung ist deutlich höher als die Kosten. Deshalb sehen wir, wie diese Technologie zum Beispiel bei Aerojet Rocketdyne, Airbus, Boeing, NASA, Raytheon, Safran und SpaceX immer weiter Fuß fasst." Neben der Kosteneinsparung bietet der 3D-Druck für Branchenexperten noch einen weiteren entscheidenden Vorteil. „Der Wert der Zeitersparnis in der Produktion wird einer der wesentlichen Faktoren sein, der Unternehmen in den 3D-Druck treibt", so Eliana Fu, die als Senior Engineer mehrere Jahre für Relativity Space arbeitete und Ende 2020 zu Trumpf North America wechselte.
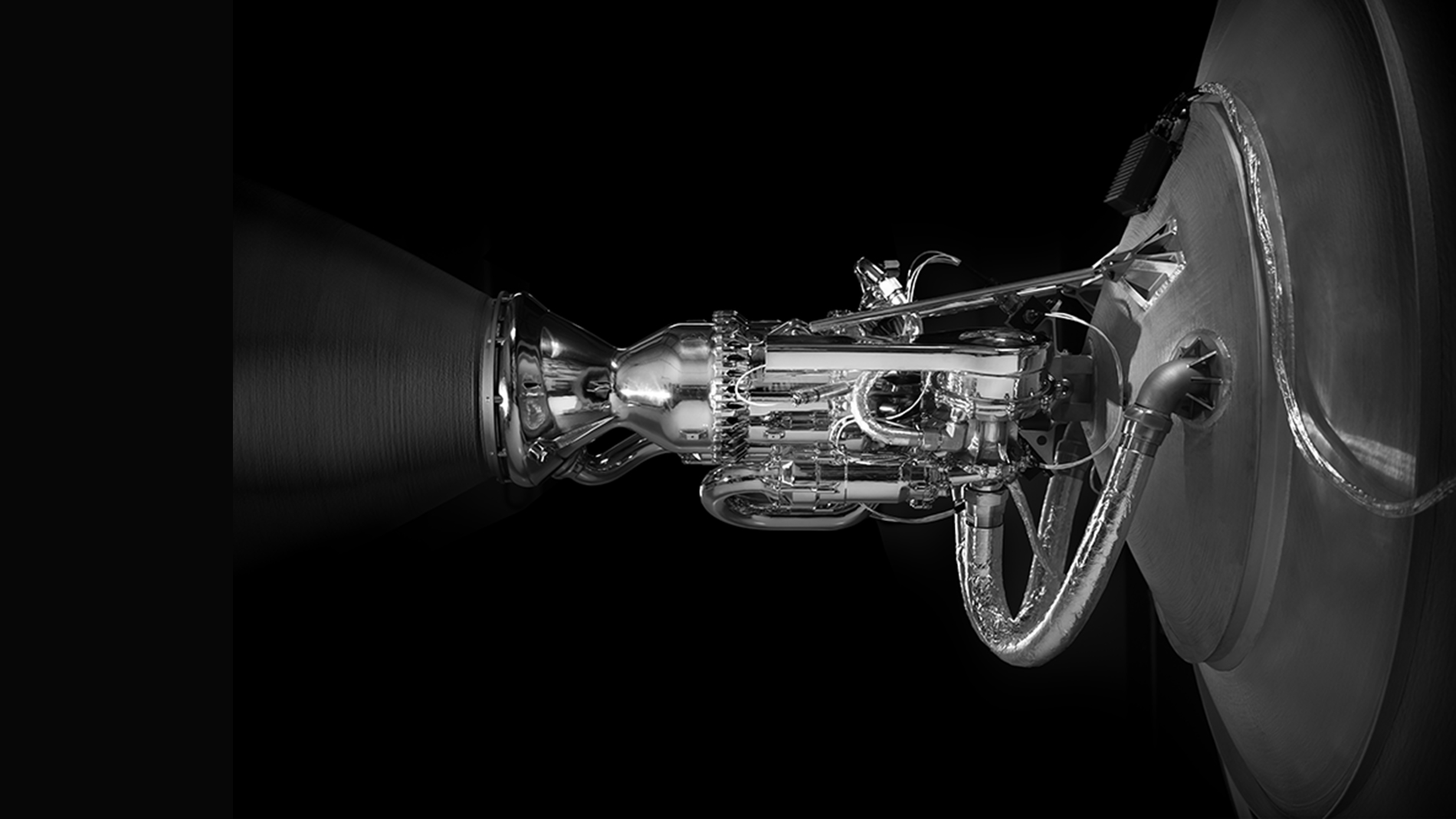
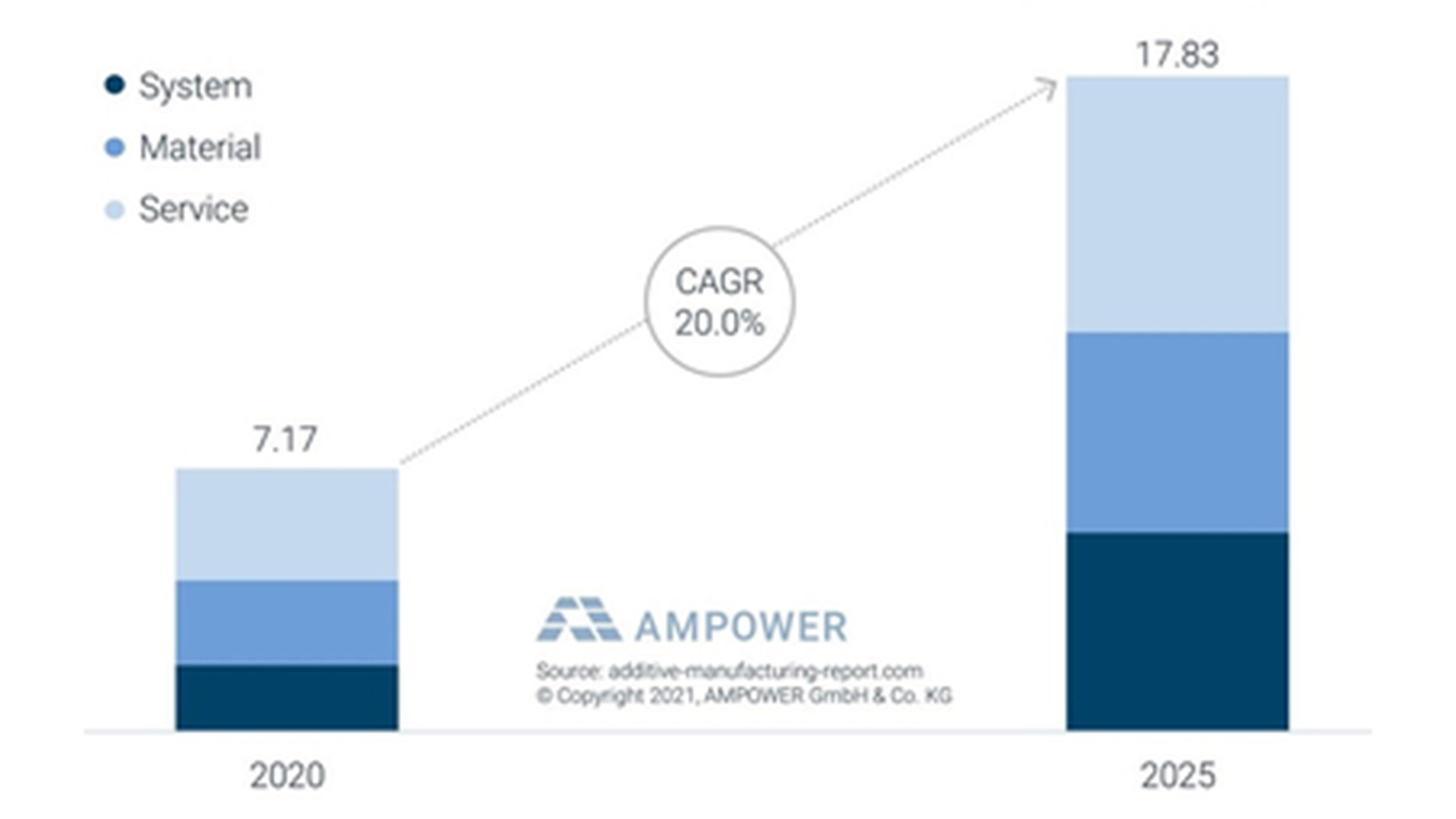
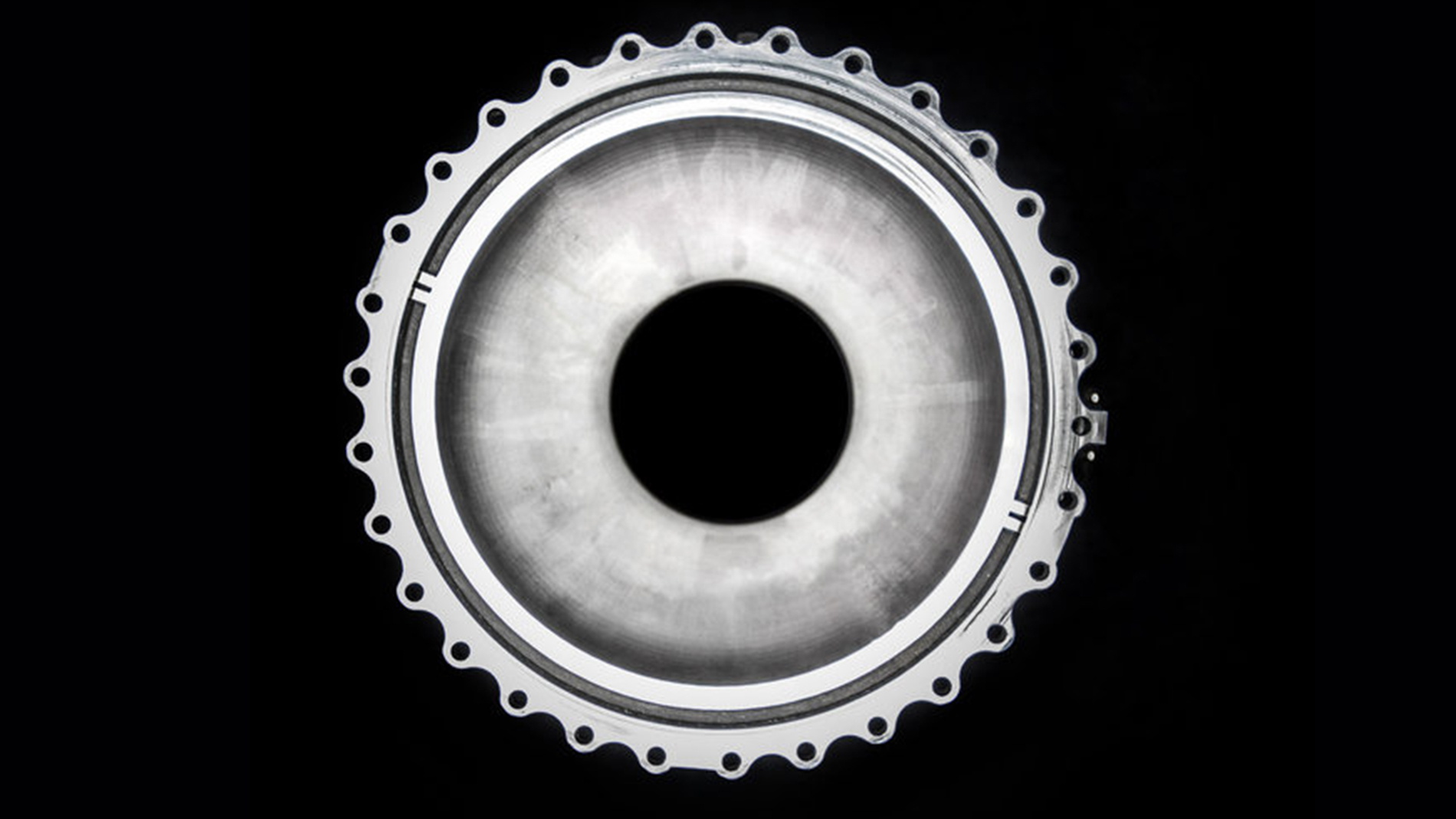
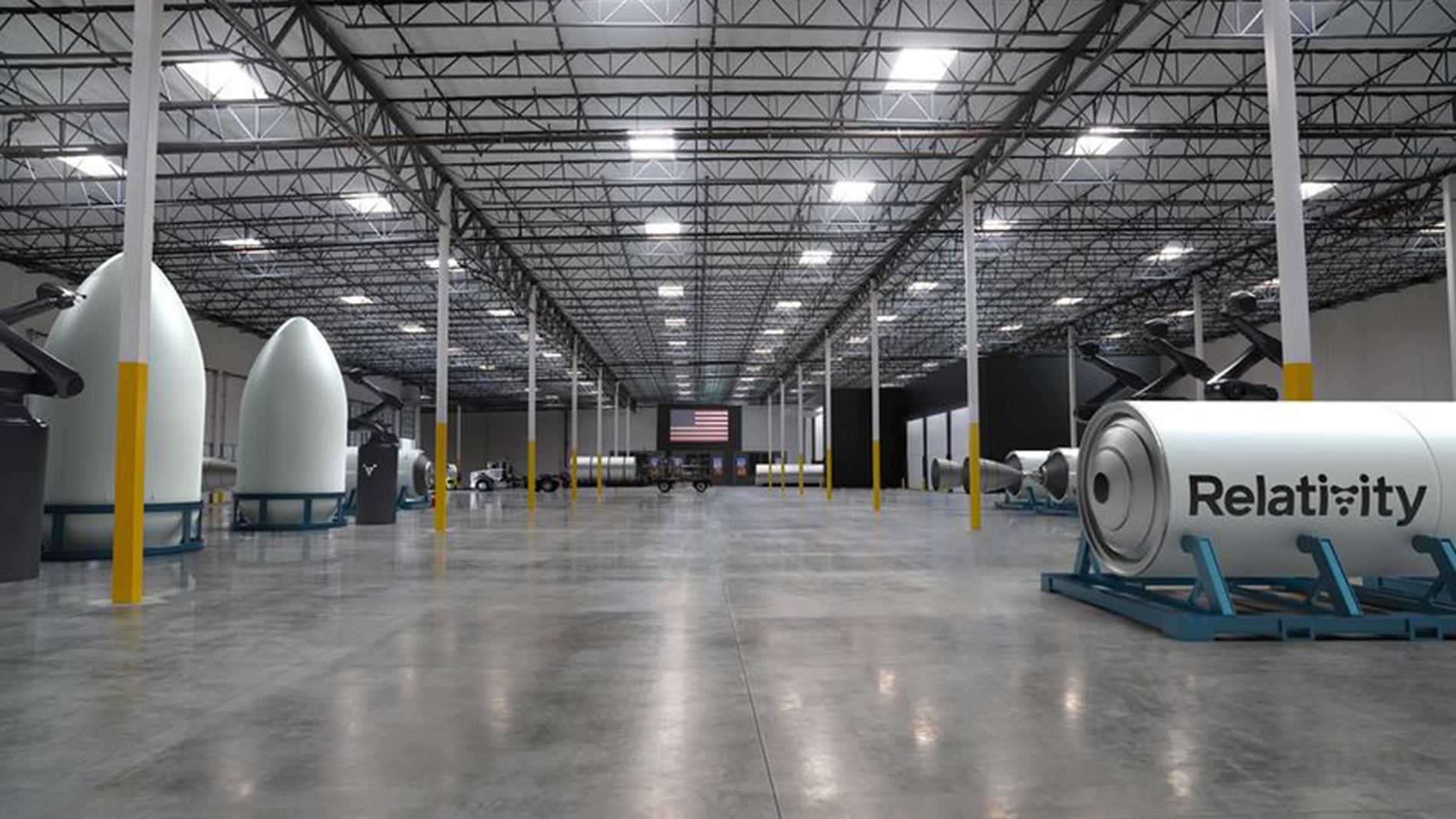
„UNTERNEHMEN TEILEN DIESE DETAILS NICHT"
SpaceX nimmt beim 3D-Druck im Raketenbau schon seit Jahren eine führende Rolle ein: Bereits im Januar 2014 hob eine Falcon-9-Rakete des US-Unternehmens mit einem 3Dgedruckten Ventilkörper in einem der neun Merlin-1D-Triebwerke ab. Inzwischen nutzt SpaceX bei seinem Raumschiff Dragon 2 auch acht 3D-gedruckte SuperDraco-Triebwerke. Laut einem Tweet von SpaceX-Gründer Elon Musk wurden die ersten SuperDracos aus Inconel auf einer EOS-Anlage 3D-gedruckt.
So offen wie SpaceX zeigen sich nicht alle Unternehmen der Branche. Zwar sind die Social-Media-Kanäle voll von „erfolgreichen" Tests 3D-gedruckter Raketenkomponenten oder Triebwerke. Doch wie viele 3D-gedruckte Komponenten und Bauteile letztendlich in Raketen verbaut werden und wie diese gefertigt werden, lässt sich oftmals nur vermuten. „Es ist fast unmöglich, die exakten Zahlen zu erfahren, denn die Unternehmen halten diese Details unter Verschluss", weiß Wohlers. Wie zugeknöpft ein Großteil der Space-Branche ist, hat sich auch bei der Recherche zu diesem Artikel gezeigt: Zahlreiche Anfragen bei Raketenherstellern oder Beratungsunternehmen blieben gänzlich unbeantwortet. In anderen Fällen waren angeblich wegen Corona die richtigen Ansprechpartner nicht verfügbar oder die Anfragen betrafen Bereiche, die der Geheimhaltung unterlagen, und blieben ergebnislos – übrigens mit den USA, China und Europa in sämtlichen relevanten Regionen.
Bei der Transparenz seiner Tätigkeiten ist SpaceX dagegen ein angenehmer Außenseiter der Branche: So lassen sich auf der Website des Unternehmens zum Beispiel direkt die Kosten für eine Fracht ausrechnen und man kann gleich einen Platz für einen der nächsten Flüge buchen. Demnach kostet beispielsweise der Transport eines 830 Kilogramm schweren Satelliten in den niedrigen Orbit (LEO) 4,63 Mio. US-Dollar (inklusive Adapter, 430.000 US-Dollar teurem Trennungssystem, Betankung am Startplatz und Versicherung).¹ Das entspricht einem Kilopreis von rund 5.500 US-Dollar. Damit hat SpaceX die Frachtkosten innerhalb von 15 Jahren inflationsbereinigt auf rund ein Zehntel reduziert. Im Space Shuttle kostete es umgerechnet sogar das 30-Fache, ein Kilogramm in den LEO zu bringen.
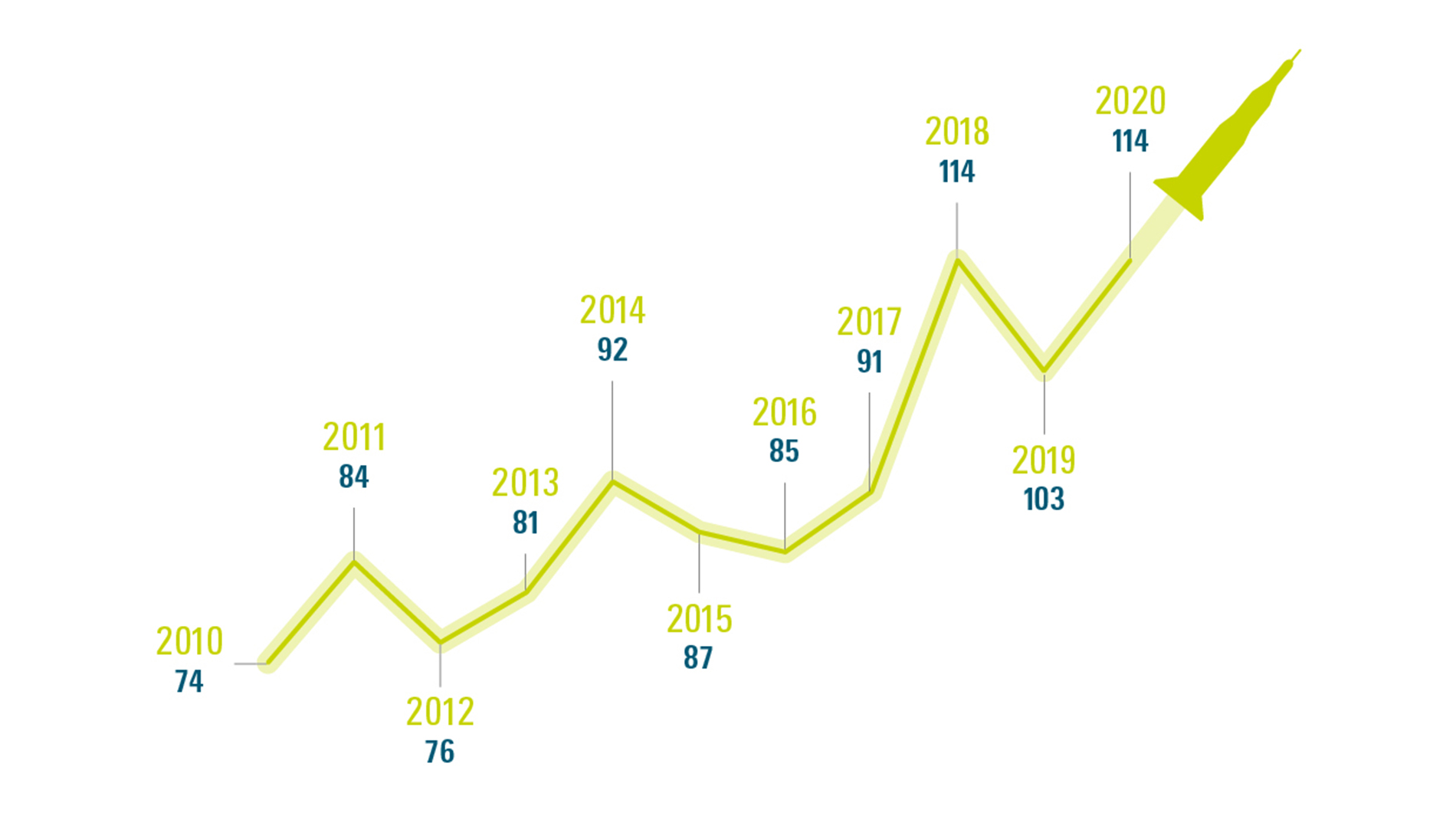
DYNAMIK UND HERAUSFORDERUNGEN
Die geringeren Frachtkosten haben auch dazu beigetragen, dass die Dynamik der Branche weiter zunimmt. Das zeigt bereits die steigende Zahl der jährlichen Raketenstarts in den Orbit: 2020 waren es schon 114 (siehe Grafik). Diese Zahl dürfte in Zukunft noch weiter steigen, wenn die Projekte, die sich derzeit noch in der Entwicklung befinden, buchstäblich abheben. Auch Trends wie weiter fallende Transportkosten, kleinere Raketen und Satelliten sowie Space-Tourismus werden der Branche weiteren Schub verleihen.
Doch bis dahin sind auch technologisch noch einige Hürden zu nehmen. Dass nicht alles, was erfolgreich getestet wird, auch tatsächlich zum Einsatz kommt, weiß auch Carl Fruth nur zu genau. Auf der Formnext 2019 hatte er mit seiner FIT AG der internationalen Fachwelt erstmals den additiv gefertigten Flüssigkeitsverteiler für das Vulcain-2-Triebwerk der neuen Ariane 6 vorgestellt. Mit der im WAAM-Verfahren (Wire Arc Additive Manufacturing) gefertigten Inconel-Komponente sollte die Leistung des Triebwerks erhöht und die Fertigungskosten gesenkt werden.
Um die hohen Sicherheitsanforderungen der Raumfahrt zu erfüllen, hatte die FIT AG, einer der weltweit größten AM-Dienstleister, gemeinsam mit der ArianeGroup ein passendes System zur Qualitätssicherung entwickelt. „Schließlich müssen bei einer neuen Technologie auch die Prüftechniken angepasst werden", so Fruth im Gespräch mit dem Fon-Magazin. Bei dem Flüssigkeitsverteiler wurde beispielsweise die 5-fache Menge per WAAM aufgetragen und an der Seite abgefräst, um Flächen für die Ultraschallprüfung zu haben. Der aufwendige Prüfprozess sorgte unter anderem dafür, dass die Bauteilkosten deutlich in die Höhe schossen und letztlich etwa das 8-Fache der Kosten der additiven Produktion betrugen. „In der Gesamtsumme war AM in dem Fall nicht mehr so viel günstiger. Dazu hatte man immer noch das Risiko, das mit der Einführung einer neuen Technologie verbunden wird", so Fruth. „Letztendlich hat man bei Ariane dann doch entschieden, es nicht mit AM zu machen."
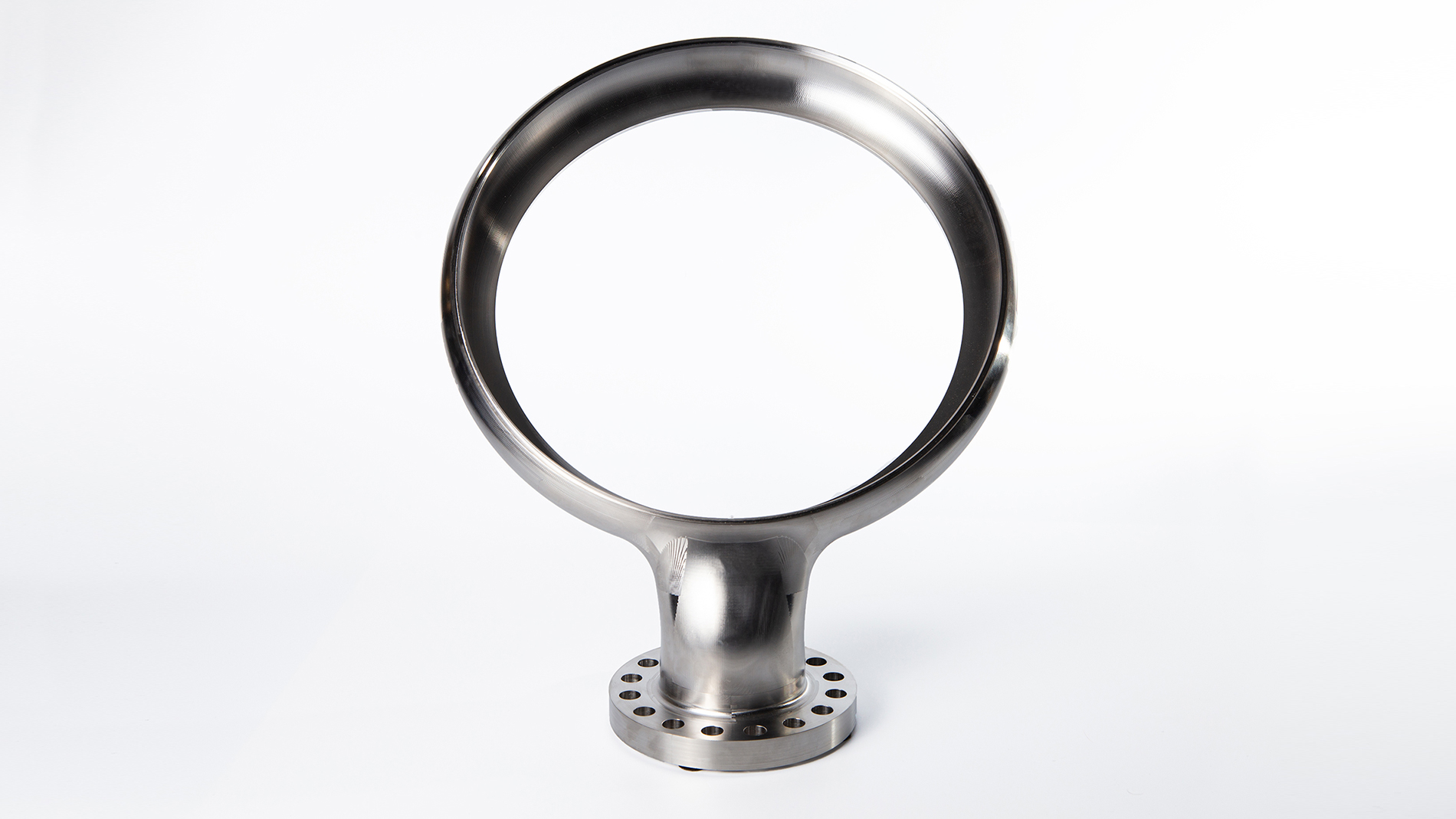
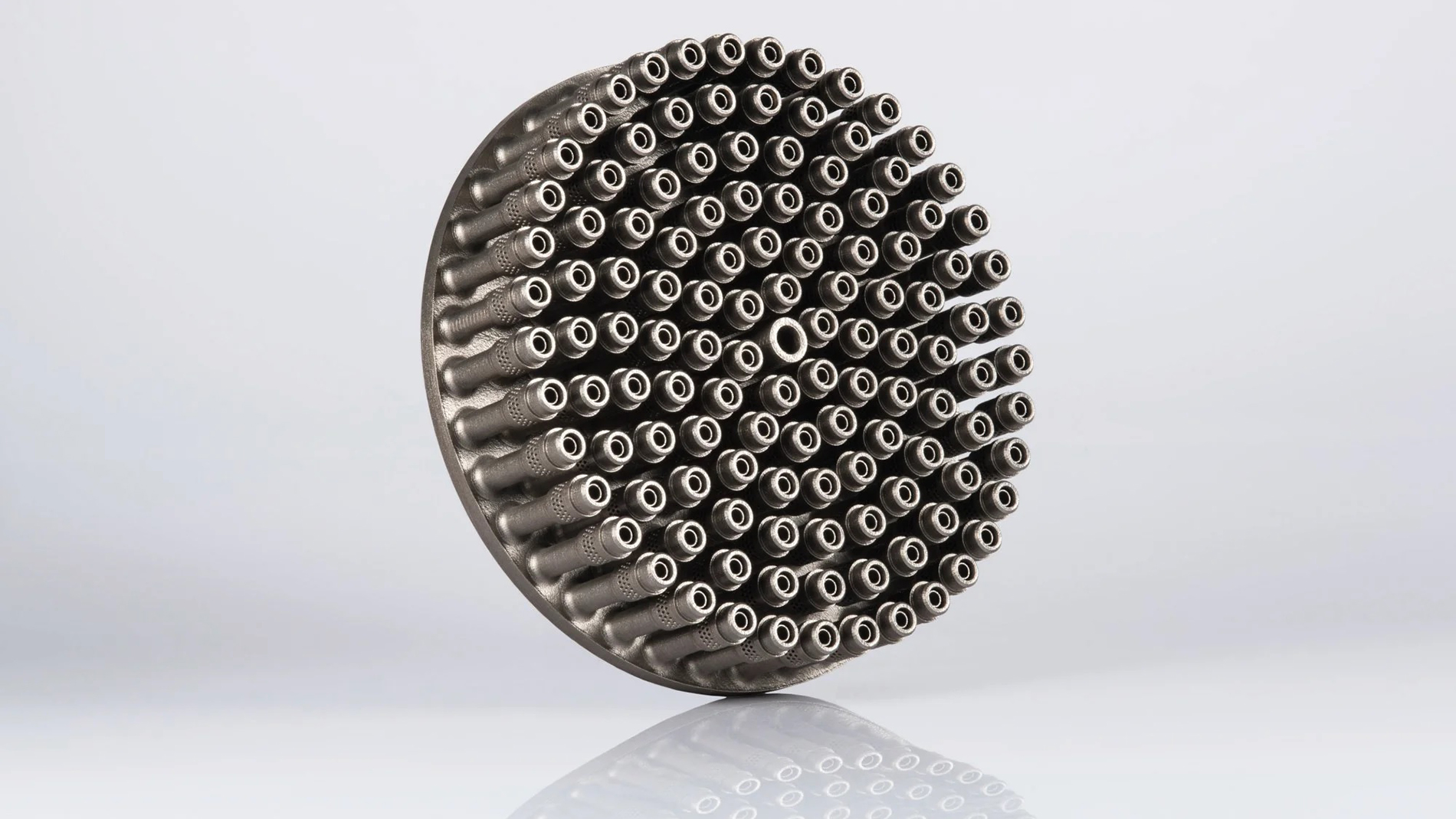
„SEHR KOMPLEXE THEMEN"
Das Beispiel zeigt auch, wie aufwendig und langwierig die Entwicklung verbesserter Bauteile und Komponenten für die Raumfahrt ist. „Das sind sehr komplexe Themen, das kann man nicht in wenigen Monaten lösen", erklärt Carl Fruth. „Als Dienstleister muss man die Produktion umstellen, die Fertigung muss für den Kunden zertifiziert werden. Und dabei geht es wirklich ums Eingemachte." Als Zeiträume für den Aufbau einer Partnerschaft nennt Fruth dann auch eher Jahre als Monate: „In den ersten zwei Jahren lernt man sich kennen, stellt seine Leistungsfähigkeit in kleineren Projekten unter Beweis. Echte, lukrativere Aufträge brauchen eine Vorlaufzeit von drei bis vier Jahren." Wie zeitintensiv die Entwicklung in der Raumfahrt ist, zeigt sich auch anhand der SuperDraco-Triebwerke vom nicht gerade als langsam bekannten Branchenprimus SpaceX. Bereits 2012 war die Entwicklung der neuartigen Triebwerke vollendet, aber erst nach einer siebenjährigen Testphase starteten sie zur ersten „echten" Mission.
Dabei verfügt SpaceX wie andere namhafte Raketenhersteller über eine eigene AM-Abteilung. „Die meisten Unternehmen der Space- Branche nutzen Systeme, die auf dem Markt verfügbar sind, wobei Software, Designprogramme und Materialien variieren", berichtet Wohlers. „Der große Unterschied zwischen den einzelnen Unternehmen besteht in der Fähigkeit und im Willen, sich ganzheitlich neue Wege im Denken über Design und Fertigung zu eigen zu machen."
Und hier kommt dann die Stärke von externen Partnern wie der FIT AG ins Spiel: In der Firmenzentrale in Lupburg verfügt das Unternehmen über eine ganze Reihe verschiedener AM-Produktionstechnologien einschließlich zahlreicher Messmethoden. Zudem sieht sich Firmengründer Fruth nicht nur als reiner AM-Dienstleister: „Wir fertigen zertifizierte Bauteile – dabei ist AM nur ein Bestandteil dieses hochkomplexen Prozesses. Das bedeutet, dass wir weniger im Wettbewerb zu anderen AM-Dienstleistern stehen als zu bestehenden Lieferantenstrukturen."
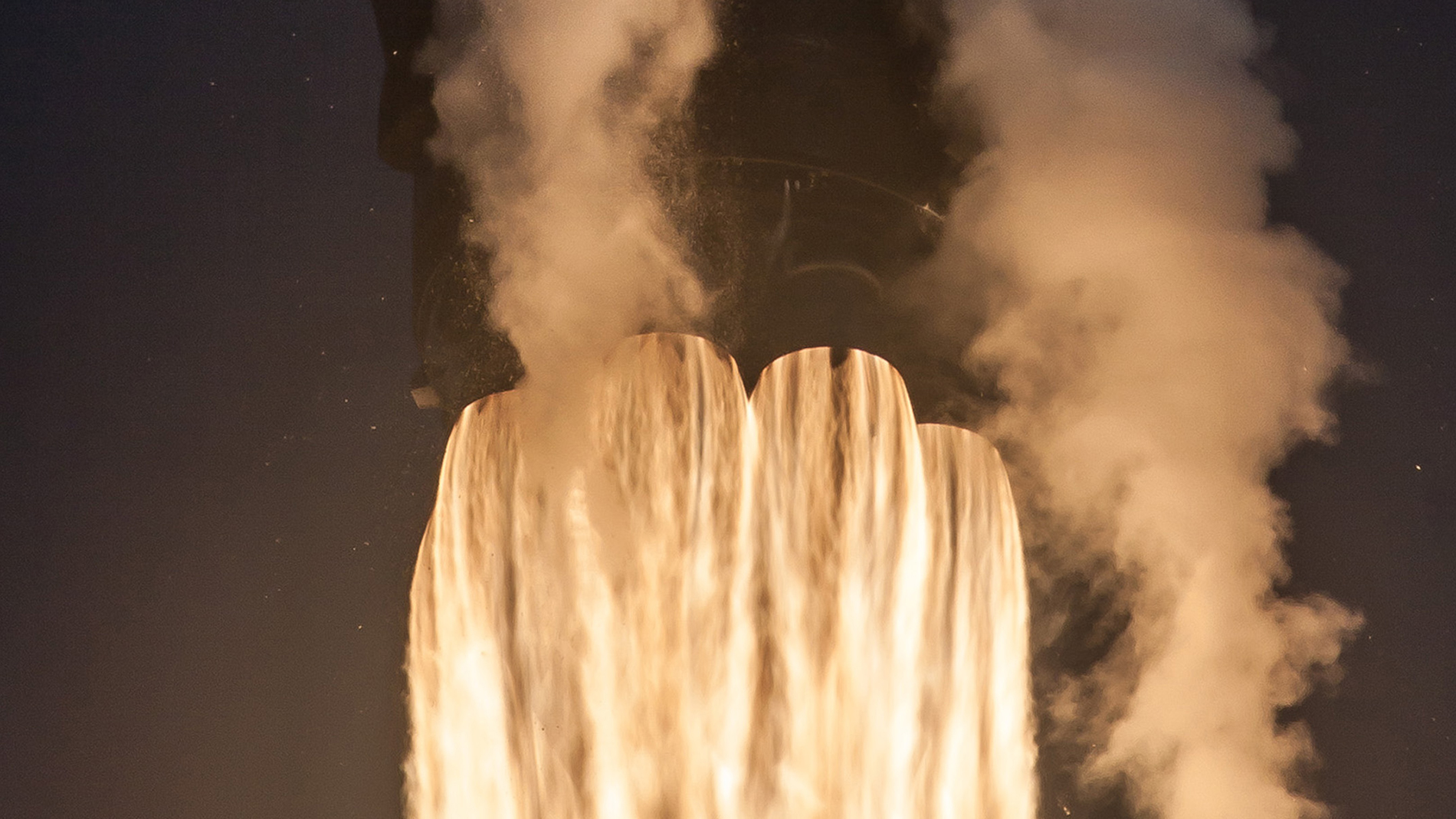
EUROPÄISCHE RAUMFAHRT UNTER DRUCK
Die europäische Raumfahrtindustrie hat dagegen stark unter den Folgen von Covid-19 zu leiden. Während SpaceX 2020 jeden Monat mindestens eine Falcon 9 in die Umlaufbahn schoss, wurde der Erstflug der neu entwickelten Ariane 6 von Ende 2020 auf 2022 verschoben. Als offizieller Grund wurden die Auswirkungen von Covid-19 in der Region rund um das Raumfahrtzentrum Guayana angegeben. Nicht besser wurde die Situation dadurch, dass die kleinere Vega-Rakete zwei Fehlschläge bei den letzten drei Starts hinlegte. Jahrelang führend, steht das europäische Unternehmen Arianespace SA, das die Starts beider Raketen vermarktet, unter massivem Druck, gegenüber SpaceX sowie der russischen und chinesischen Konkurrenz deutlich ins Hintertreffen zu geraten.
Neben dem Flüssigkeitsverteiler hat die ArianeGroup als Hersteller der Ariane-Raketen zahlreiche weitere AM-Entwicklungen für die Ariane 6 und künftige Raketengenerationen angestoßen, zum Beispiel einen Einspritzkopf, der zusammen mit EOS entwickelt wurde. Die Ziele von ArianeGroup sind ehrgeizig. Das künftige Prometheus-Triebwerk soll auch dank 3D-Druck nur noch 1 Million Euro kosten und damit 90 Prozent weniger als das rund 10 Millionen Euro teure Vulcain-2-Triebwerk der Ariane 5. Damit Prometheus wie geplant in einer wiederverwendbaren Nachfolgerrakete der Ariane 6 in rund zehn Jahren zum Einsatz kommt, hat die Ministerratskonferenz der europäischen Raumfahrtagentur ESA im Sommer 2020 ein Projektbudget von 82 Mio. Euro bewilligt. Auch die nächsten Generationen der Vega-Rakete sollen ab 2025 mit einer 3D-gedruckten Schubkammerbaugruppe des M10-Triebwerks in den Orbit fliegen.
Dies ist ein langer Weg für die additive Fertigung in der europäischen Space-Industrie. Immerhin war bei der Ariane 5 bisher schon ein 3D-gedrucktes Kupplungskreuz im Einsatz: Das weniger als 3 mal 3 Zentimeter große Bauteil wird zwar im Wettrennen mit SpaceX nicht entscheidend sein, „doch wir stehen kurz vor Einführung einzelner Bauteile", erklärte Steffen Beyer, Leiter Produktionstechnologie – Werkstoffe & Prozesse bei ArianeGroup, auf einem internationalen Fachkongress im Sommer 2019. Neben dem Laserschmelzverfahren nannte Beyer auch DED, LMD und Coldspray als interessante Fertigungstechnologien für die Raumfahrt. Dabei seien aber noch einige Herausforderungen zu meistern, etwa das Entfernen von Pulver aus Kavitäten oder die Reinheit des Pulvers.
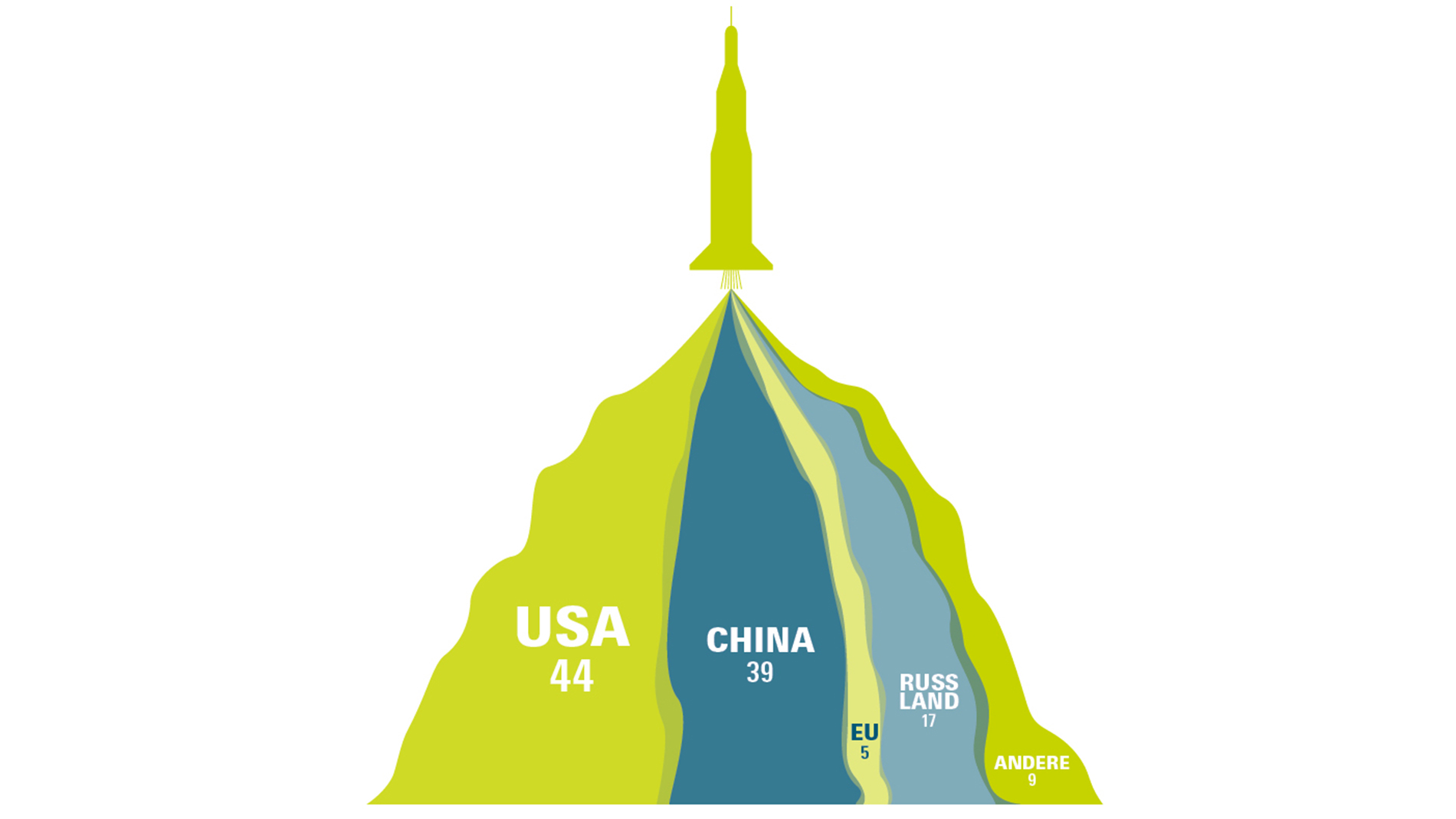
Die Probleme bei Ariane und Vega haben auch den europäischen Zulieferern zugesetzt. „Die Realität ist leider, dass für die europäische Trägerindustrie auf Sicht nur der institutionelle Markt mit rund vier bis fünf Starts pro Jahr nachhaltig planbar ist", stellte Hans Steininger, Vorstandsvorsitzender der MT Aerospace AG, eines der größten deutschen Zulieferer für die Luft- und Raumfahrt, im Sommer 2020 angesichts der Verschiebung der Ariane-6-Starts und der damit verbundenen geringeren Produktionsvolumen fest. In der Abhängigkeit von den ESA-Programmen sieht FIT-AG-Chef Carl Fruth allerdings einen weiteren Nachteil: „Es herrscht kein echter Wettbewerb. Dadurch fehlt auch der Druck, neue Technologien noch stärker zu implementieren."
BOOM IN DEN USA UND CHINA
Doch während die europäische Raumfahrtbranche Ende 2020 aufgrund der Ariane-Verzögerungen die Verluste von Jobs und langjährigem Know-how befürchtete, traten junge wie auch etablierte Unternehmen vor allem in den USA und China aufs Gaspedal.
Das chinesische Unternehmen Link Space, das 2014 vom damals 21-jährigen Zhenyi Hu gegründet wurde, hat inzwischen mit seiner zweistufigen und wiederverwendbaren 24 Meter hohen Rakete New Line 1 für Aufsehen gesorgt. Einen weiteren Meilenstein der Raumfahrt in China setzte die Beijing Interstellar Glory Space Technology Ltd. im Juli 2019, als erstmals eine private Mission den Orbit erreichte und dort das „Double Curve One Remote Launch Vehicle" (SQX-1 Y1) aussetzte. Mit einer im August 2020 abgeschlossenen Finanzierungsrunde über 1.192,5 Mio. Yuan (rund 150 Mio. Euro) will das Unternehmen unter anderem die Entwicklung der Rakete seiner Twin-Curve-Serie und eines wiederverwendbaren Triebwerks voranbringen.
Generell hat sich China längst zur etablierten Raumfahrernation entwickelt und mit rund 39 Starts im Jahr 2020 Russland überholt und mit den USA fast aufgeschlossen (siehe Grafik). Seit im Reich der Mitte 2014 private Unternehmen im Raumfahrtsektor zugelassen wurden, erlebt auch diese Branche einen Boom: Die Zahl der Unternehmen stieg von 30 im Jahr 2018 auf mittlerweile über 100. „Die 3D-Drucktechnologie hat sich dabei zum Rückgrat der Raketenherstellung entwickelt", so Kitty Wang, die mit ihrer Plattform 3D Science Valley seit Jahren die chinesische AM-Industrie intensiv untersucht.
MEHR INFOS UNTER:
spacex.com
arianespace.com
fit.technology
relativityspace.com
3dsciencevalley.com
¹Stand Januar 2021
Tags
- Luft- und Raumfahrt