09.09.2019
Die junge Schmuckdesignerin Marie Boltenstern setzt bei ihren Kollektionen auf Additive Fertigung und arbeitet dafür mit Formrise und DyeMansion zusammen. Inspirieren lässt sie sich von der Natur.
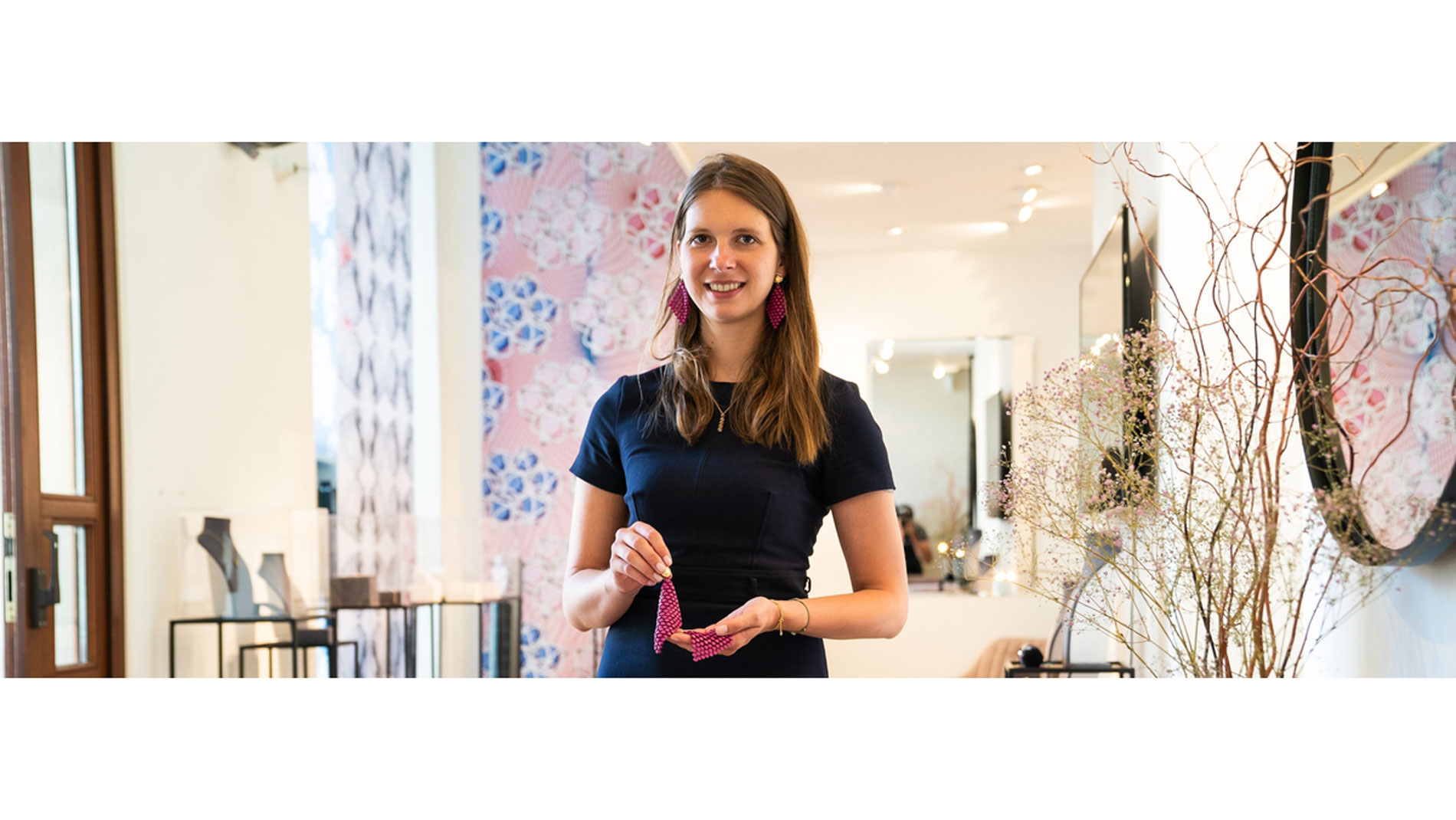
Der Name Boltenstern steht seit über 50 Jahren für hoch qualitative Schmuckstücke, ausgefallene Designs und feinste Arbeit mit Edelmetallen. Durch präzises Handwerk und den geschickten Umgang mit Gold schaffte es der Gründer Sven Boltenstern, sich in den 60er-Jahren auf dem globalen Schmuckmarkt zu etablieren. Seit 2015 weht nun ein frischer Wind. Seine Tochter Marie Boltenstern führt seitdem als CEO & Head of Design das Familiengeschäft in eine neue Richtung. Wer den von ihr 2017 eröffneten Showroom in der Wiener Bräunerstraße 11 besucht, merkt das bereits an der Auslage. »3D-printed fine jewelry« lautet der Slogan von Boltenstern heute. »Unser Ziel ist es, Innovation in jeden Bereich des Schmuckgeschäftes zu integrieren: vom Design der Schmuckstücke bis zum Kauferlebnis unserer Kunden.«
Alle Kollektionen der jungen Designerin werden mittlerweile im industriellem 3D-Druck produziert und anschließend um handgeschmiedete Elemente ergänzt. Inspiriert wird ihr Schmuck durch die Formen der Natur. »Die Natur an sich ist sehr geometrisch. Obwohl natürliche Artefakte organisch aussehen, befolgen sie feste mathematische Regeln und Muster. Das greife ich in meinen Designs auf.«
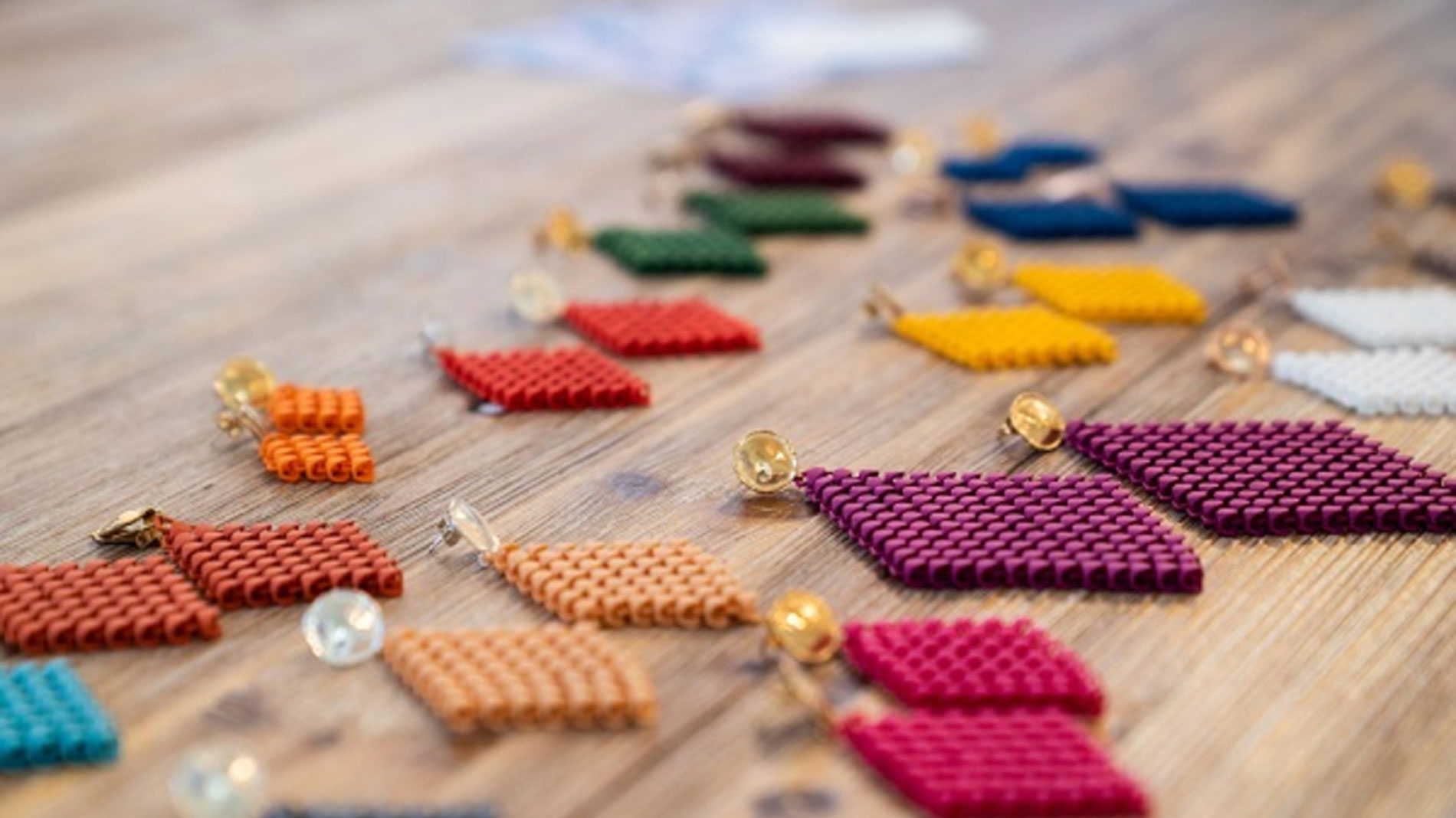
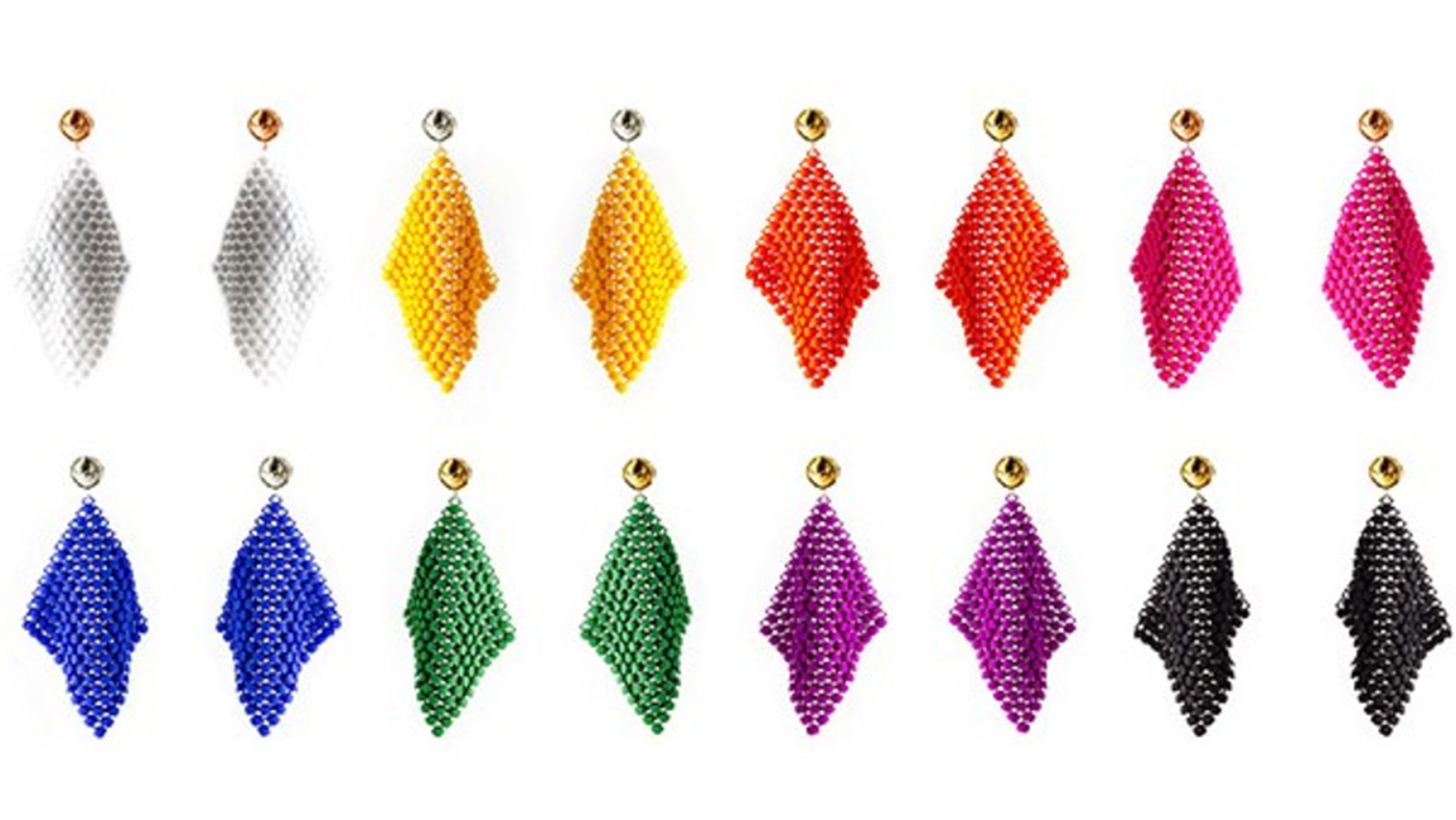
Die Suche nach dem richtigen Feinschliff
Marie Boltenstern druckt Schmuck aus verschiedenen Materialien, zum Beispiel auch aus Gold. Aber sie arbeitet schon immer mit Poly amid – früher allerdings nur für das Prototyping neuer Strukturen. »Polyamid war für uns immer eine Möglichkeit, neue Strukturen zu testen.« Neben der Freude am Umgang mit diesem Material erkannte die Designerin auch, dass es sich auch für die Serienproduktion eignet. Bei den ersten Versuchen mit dem Lasersinter-Verfahren waren allerdings noch die Schichten des Druckprozesses zu sehen. Auch die Haptik war für ein Produkt, das auf der Haut getragen wird, nicht ausreichend. Und darüber hinaus zerbrachen die Anhänger mit dünnen Wandstärken bei der Nachbearbeitung. Auch bei der geplante Farbvielfalt sorgten die weißen Polyamid-Teile aus dem 3D-Drucker für eine echte Herausforderung. Die Lösung dieser Herausforderungen fand der Schmuckhersteller schließlich in der Zusammenarbeit mit dem deutschen 3D-Druck-Dienstleister Formrise. Hier werden die späteren Schmuckstücke auf einer Formiga P 110 von EOS produziert. Für die Reinigung, Oberflächenveredelung und Färbung nutzt Formrise den Print-to-Product-Workflow von DyeMansion. Hier werden die Bauteile auf Powershot-C- und auf Powershot-S-Anlagen automatisiert und oberflächenschonend entpulvert und veredelt, um eine bessere Haptik und einen matten Glanz zu erzielen. Der Prozess dauert 10 Minuten und trägt kein Material ab. Schließlich erhalten die Ohrringe in der DyeMansion DM60 mit dem DeepDye Coloring die gewählte Färbung. Mit allen Partnern wurde so ein verlässlicher und reproduzierbarerer Produktionsprozess aufgebaut.

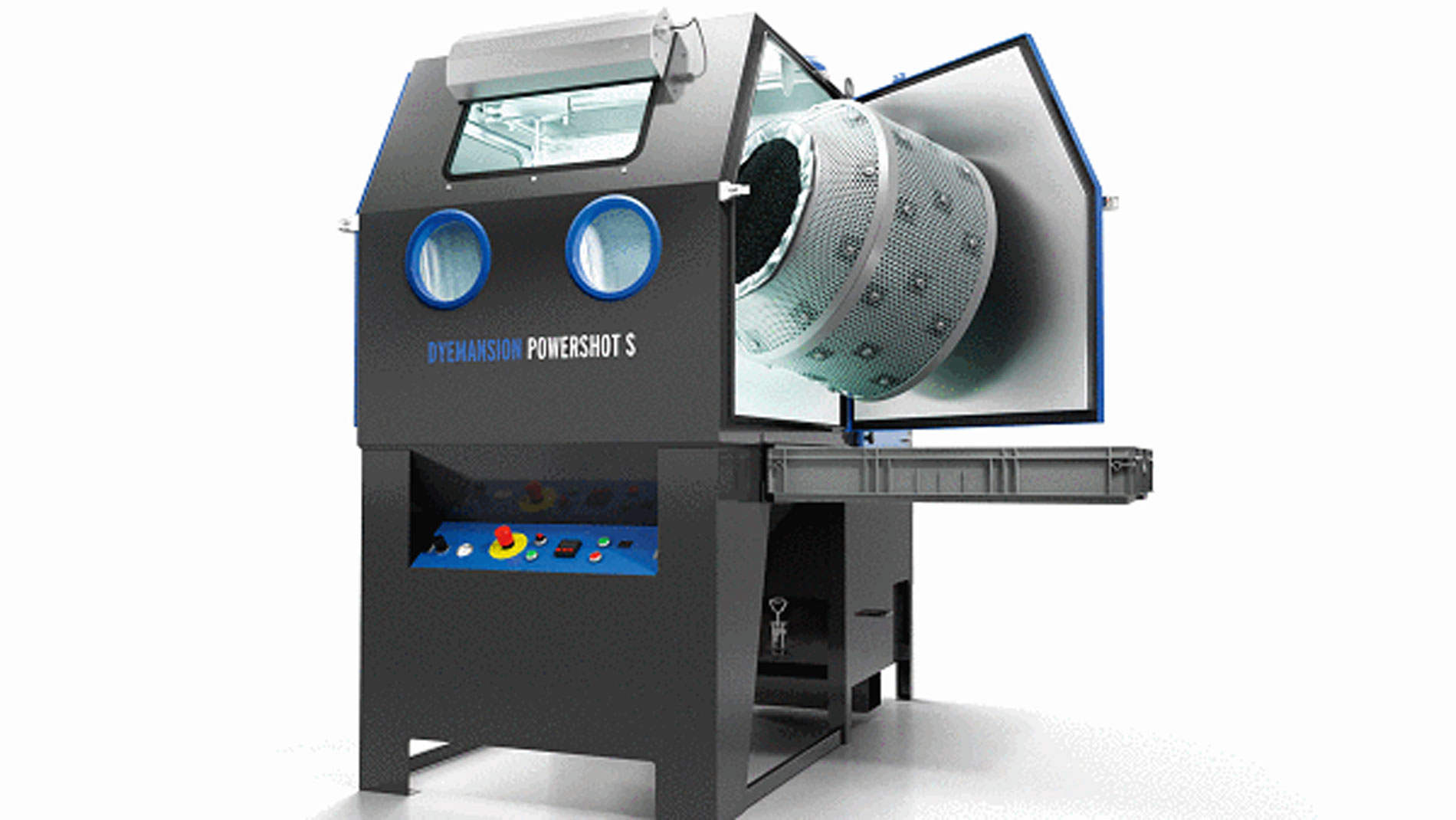
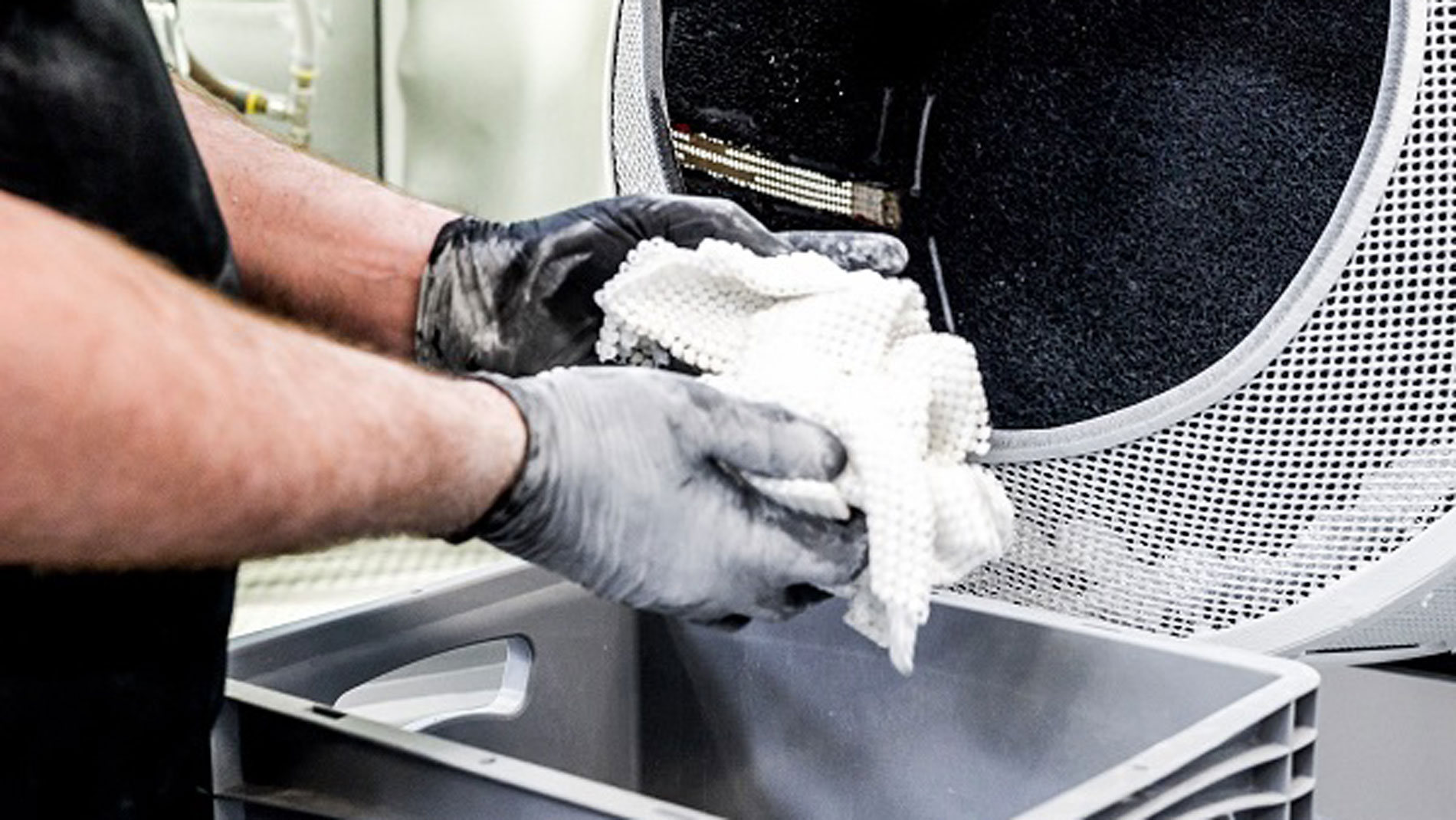
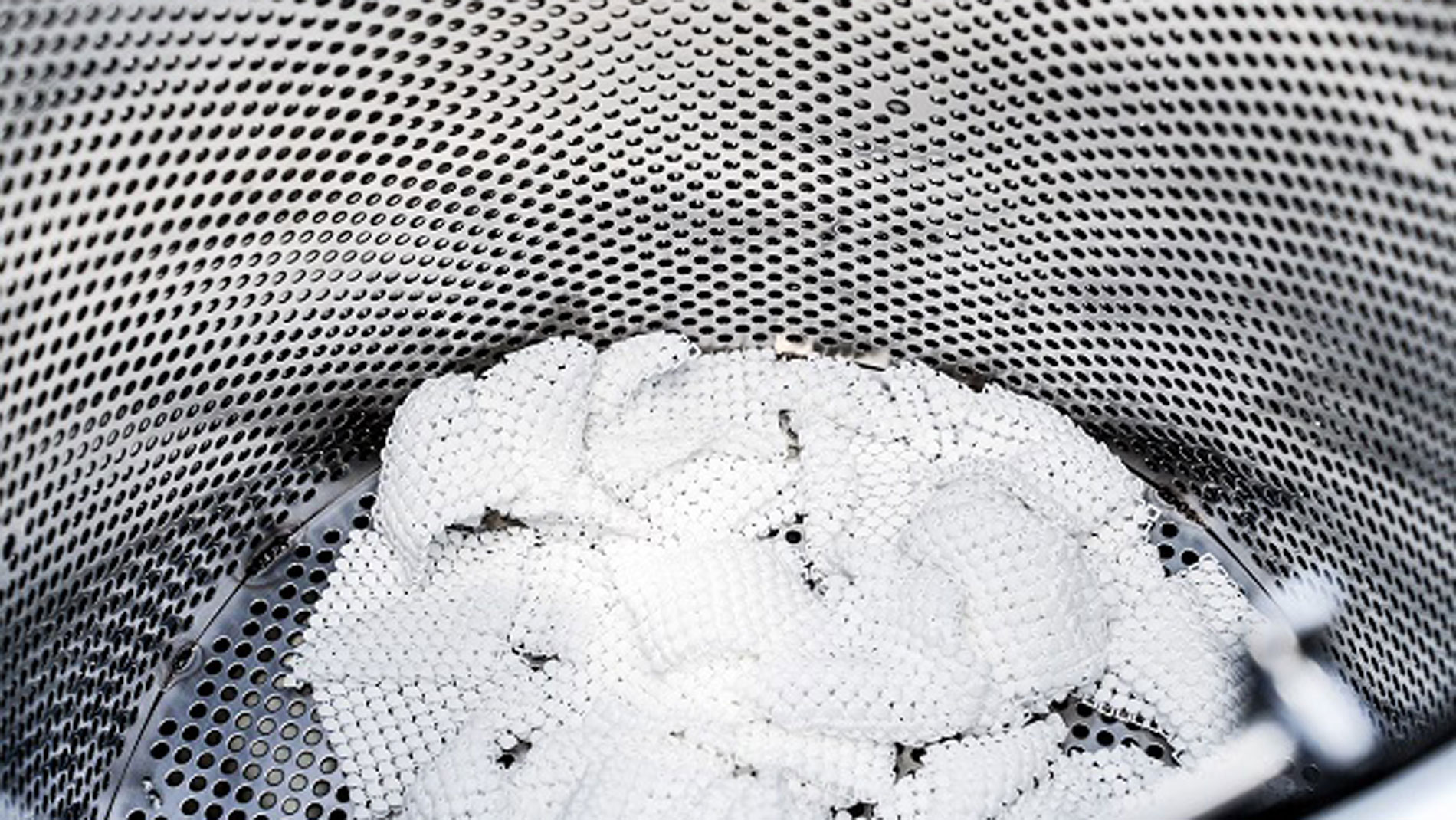
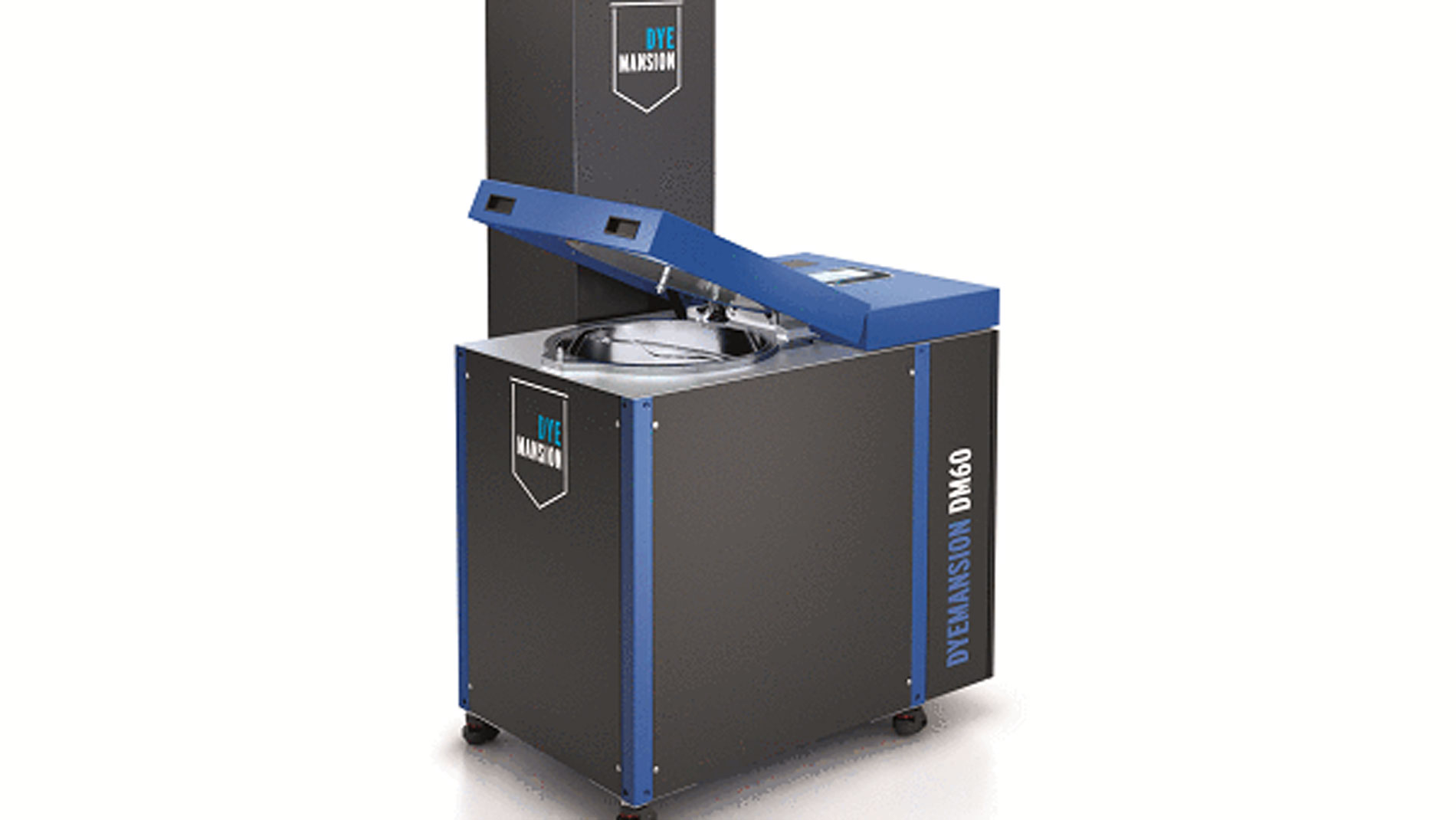
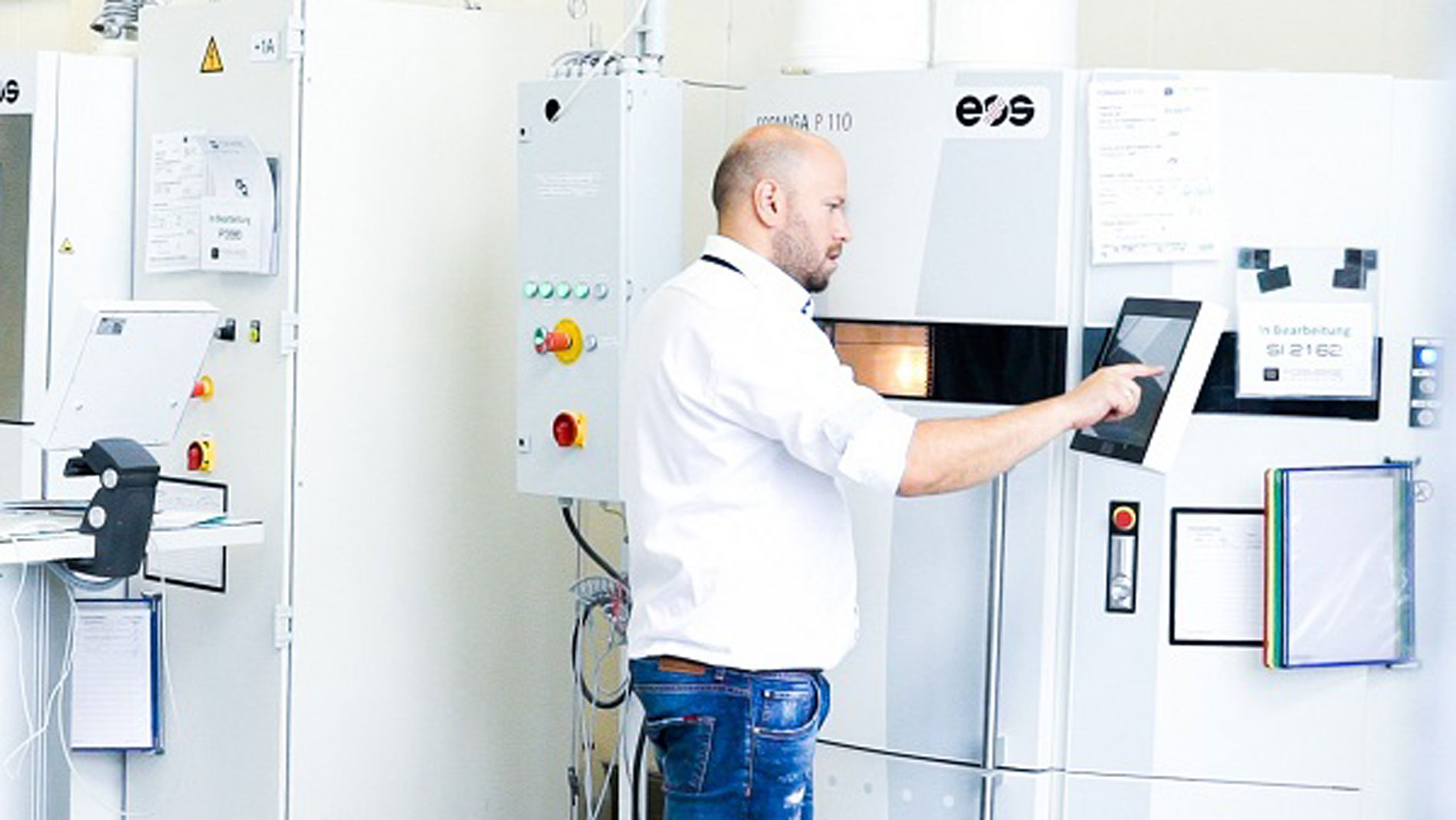
Saisonale Sonderfarben
Nachdem die Ohrringe in drei Stunden den Print-to-Product-Workflow durchlaufen haben, folgt die Zusammenführung mit dem handgefertigten Ohrstecker aus Gold oder Silber. Im Wiener Showroom beeindrucken die Ohrringe so in diversen Größen und Farben von Blau, Lila, Pink und Rot bis Orange, Gelb, Grün und Schwarz. Zu saisonalen Anlässen wird die Kollektion um weitere RAL- Farben ergänzt, zum Beispiel zu Weihnachten um Dunkelgrün und ein dunkles Rot. Da sich die Fabnora-Kollektion und die additive Produktion bewährt haben, plant Marie Boltenstern, die Kollektion zu erweitern. Dazu gehören weitere Farben, eventuell sogar individuelle Wunschfarben. Dank der beteiligten Technologien und Färbelösungen sind ihrer Fantasie und deren Umsetzung kaum Grenzen gesetzt.
Tags
- Werkstoffe und Halbzeuge
- Oberflächenbehandlung
- Uhren und Schmuck