von Thomas Masuch
Auf der Formnext stellt die Ponticon GmbH das Pontimat-Verfahren zur Entwicklung neuer metallischer Werkstoffe für die Additive Fertigung vor. Es macht erstmals die Herstellung und Erprobung unterschiedlichster Legierungsvarianten innerhalb kürzester Zeit möglich.

Mit dem Pontimat-Verfahren können anwendungsspezifische Werkstoffe schnell und mit geringstem Ressourceneinsatz hergestellt und erprobt werden. Durch seine Flexibilität bei der Auswahl der metallischen Legierungselemente und die gezielt einstellbaren Abkühlraten eignet es sich besonders für die Entwicklung neuartiger Werkstoffe für die Additive Fertigung, so Ponticon.
Basis des neuen Verfahrens ist das EHLA-3D-Verfahren (extremes Hochgeschwindigkeits-Laserauftragschweißen), das Ponticon in Zusammenarbeit mit dem Aachener Fraunhofer-Institut für Lasertechnik ILT und dem Lehrstuhl Digital Additive Production (DAP) der RWTH Aachen entwickelt und jetzt zur Marktreife gebracht hat.
Das für das Verfahren eingesetzte pE3D-System erzielt im Erstarrungsprozess Abkühlraten zwischen 100 K/s und 10 Millionen K/s. So kann das Gefüge in bisher ungekannt weiten Grenzen beeinflusst werden.
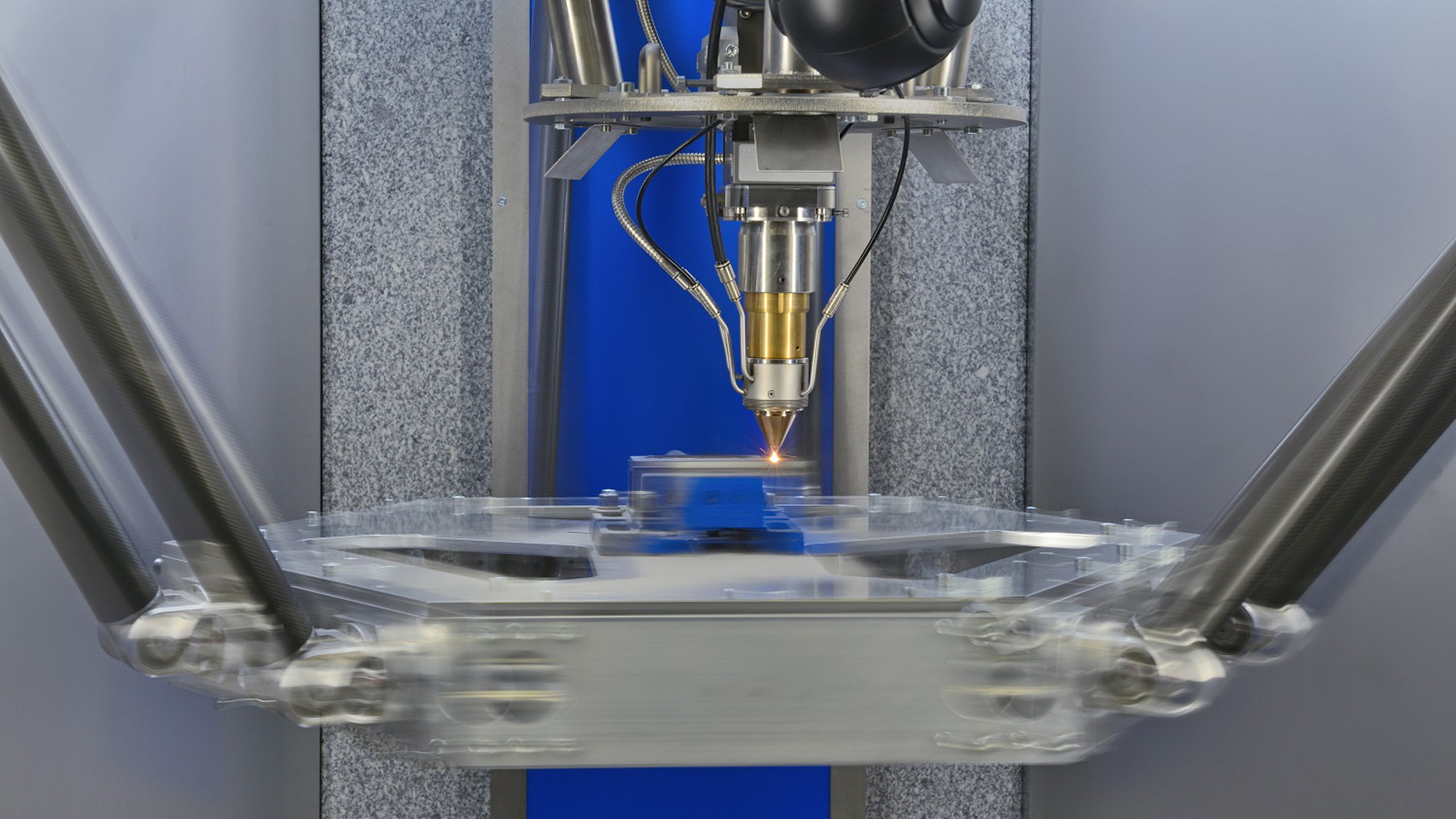
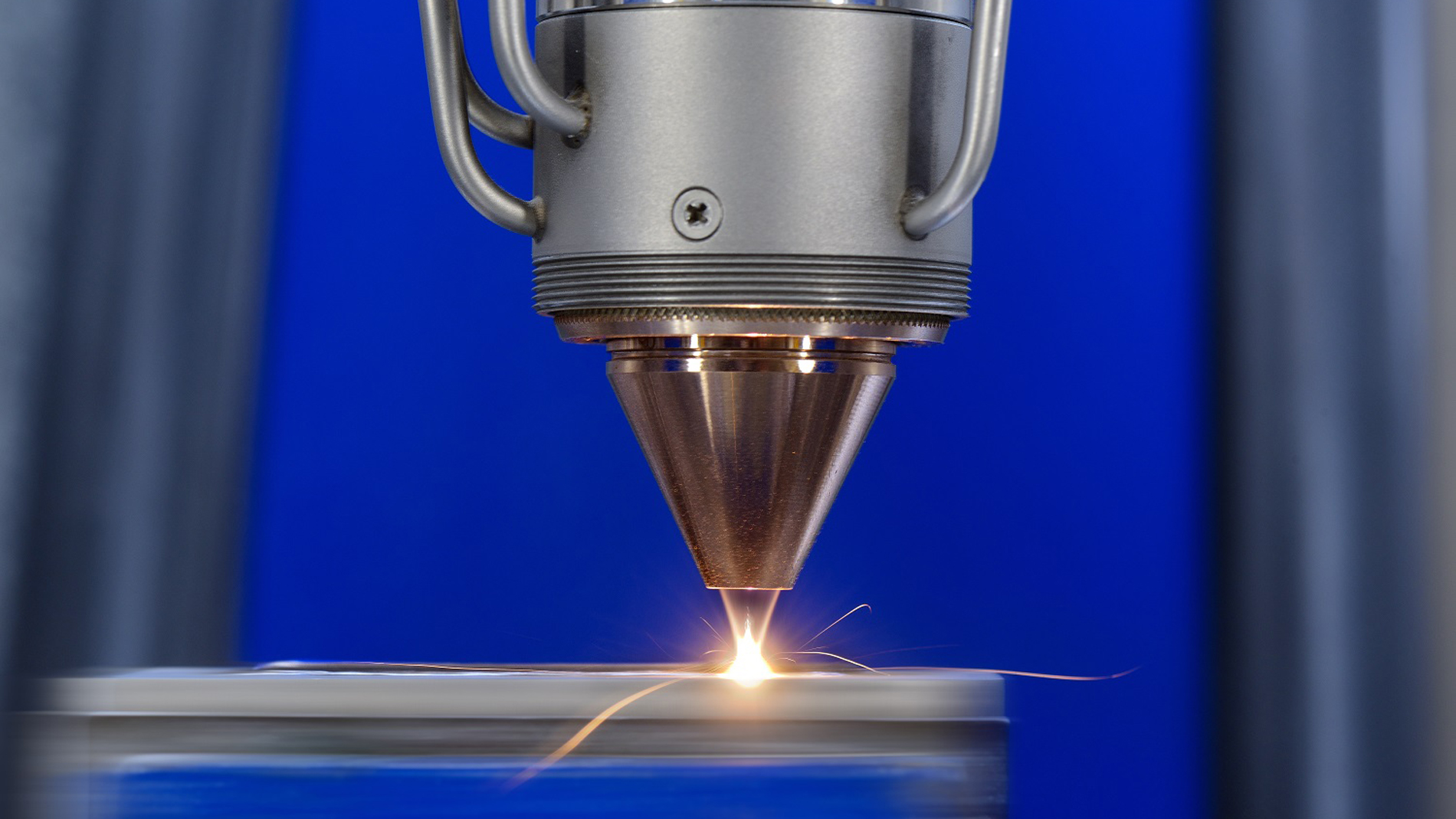
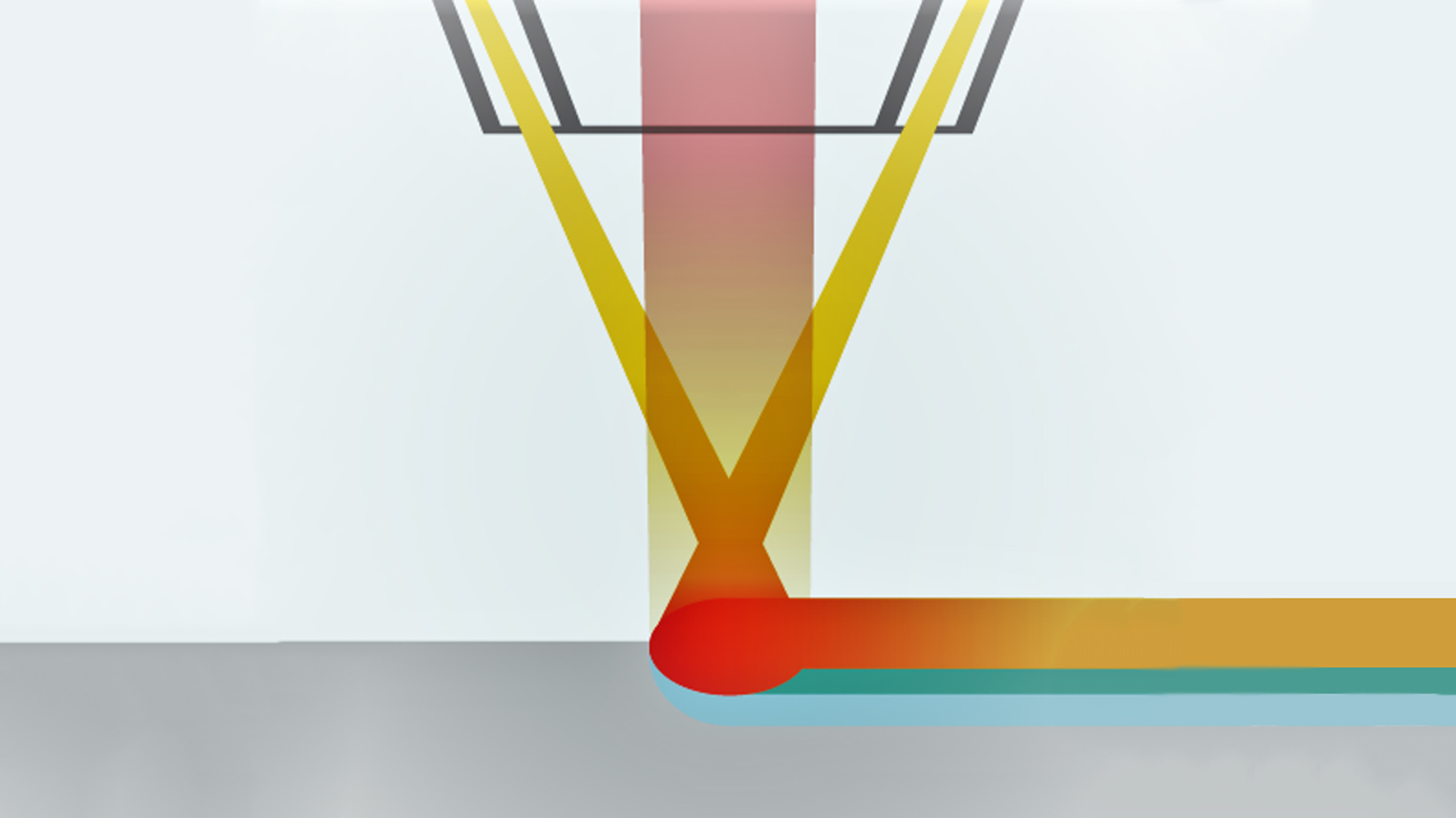
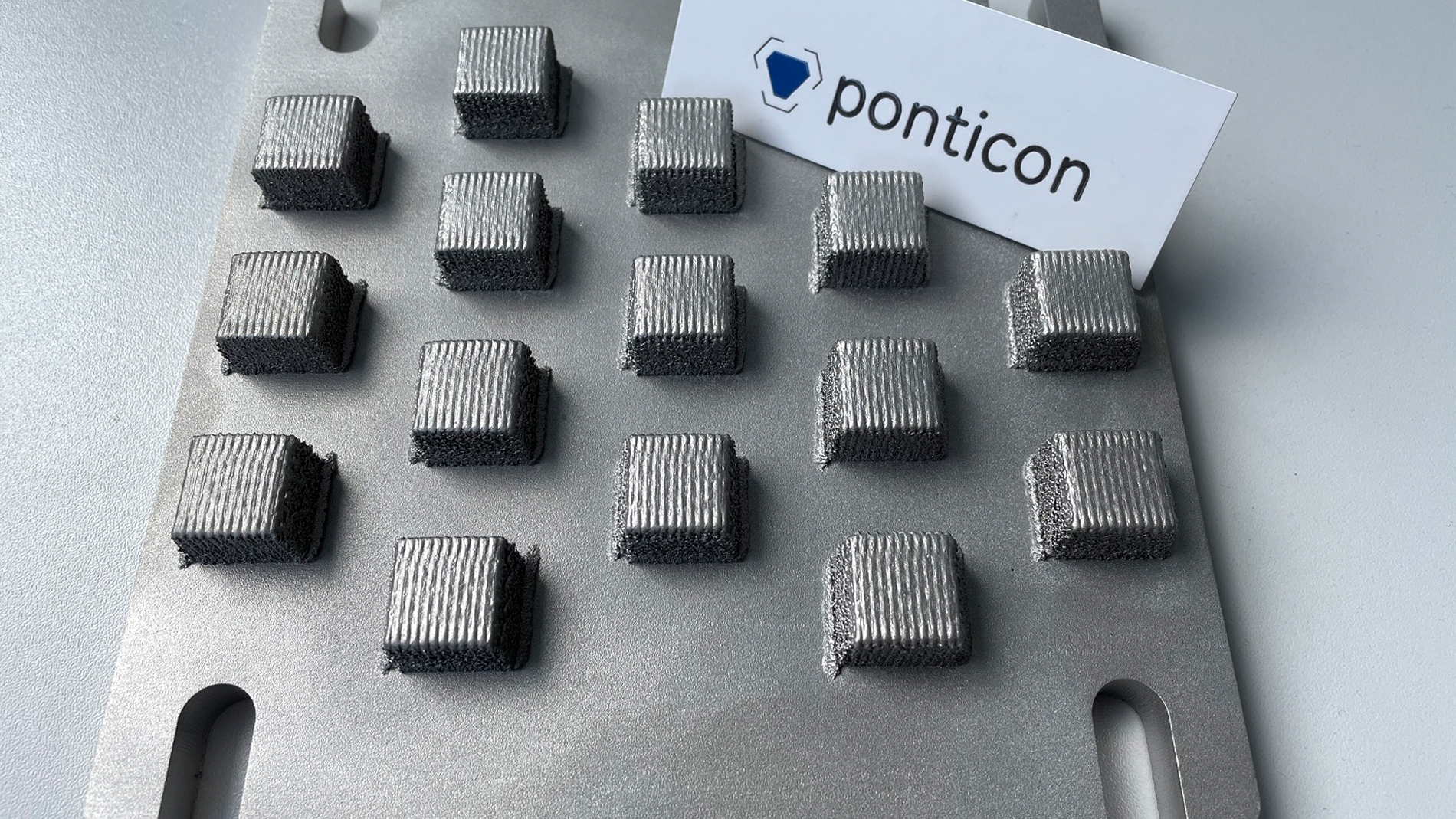
Für die Entwicklung anwendungsspezifischer Legierungen stellt das System auf einem Substrat innerhalb kürzester Zeit mehrere Probekörper von beispielsweise 1 cm³ Volumen her, die metallurgisch analysiert werden können. Auf diese Weise ist es möglich, pro Tag Hunderte Legierungsvarianten in einem agilen Ansatz zu verarbeiten und anschließend deren Eigenschaften zu erproben.
Tobias Stittgen, Geschäftsführer der Ponticon GmbH, sieht hohen Nutzen für seine Kunden: „Von der Konstruktion her sind viele Bauteile schon heute für die Additive Fertigung optimiert. Ein deutlich größeres Potenzial bei der Verbesserung der Funktionalität steckt jedoch im Werkstoff.“
Ponticon auf der Formnext 2021:
Halle 12, Stand A01C
MEHR INFOS UNTER:
Tags
- Werkstoffe und Halbzeuge
- Additive Fertigung