04.03.2022
Klebemittel erscheinen auf den ersten Blick recht unspektakulär, doch sind viele industriell hergestellte Produkte ohne sie heute kaum noch denkbar – weder Fahrzeuge noch Smartphones. Entsprechend hoch sind die industrielle Bedeutung der „Klebebranche“ und der Innovationsdruck. Kein Wunder, dass man auch hier auf die innovative Kraft der additiven Fertigung zurückgreift: So hat Tesa, eines der führenden Unternehmen aus der Welt des Klebens, zusammen mit Arburg 3D-gedruckte Klebelösungen entwickelt, die dem Unternehmen möglicherweise den Weg zu neuen Märkten und Geschäftsmöglichkeiten eröffnen.

Klebstoffe sind fast so alt wie die Kulturgeschichte der Menschheit: Bereits vor über 100.000 Jahren befestigten die Steinzeitmenschen zum Beispiel mit Baumharzen oder Birkenpech ihre Speere, Messer oder Axtklingen an einem hölzernen Schaft. Heute hat sich aus dem hohen Bedarf an Haftverbindungen eine bedeutende Branche entwickelt, die einen maßgeblichen Einfluss auf die Herstellung moderner Industrieprodukte hat. „In einem E-Auto können bis zu 130 Tapes von Tesa vorhanden sein – in einem Smartphone bis zu 70“, erklärt Frank Virus, Technology and Product Development bei Tesa SE. Das Tochterunternehmen der Beiersdorf AG mit Hauptsitz in Norderstedt bei Hamburg hat rund 4.800 Beschäftigte und ist Spezialist für Klebebänder (Tapes) und selbstklebende Klebelösungen.
Bei der Entwicklung neuer Produkte und Lösungen hat man bei Tesa seit einigen Jahren auch den 3D-Druck im Blick. Die ersten Ideen und Konzepte gab es bereits 2011. „Damals war die Technologie aber noch nicht weit genug und auch nicht industriell nutzbar“, erinnert sich Virus. Das habe sich inzwischen geändert: „In Bezug auf Technologie und Akzeptanz sind die Voraussetzungen nun ganz andere.“ So hat Tesa die Idee des 3D-Drucks von Klebebändern vor einigen Jahren wiederbelebt und setzt seit 2019 einen Freeformer von Arburg in der Produktentwicklung ein (zuerst auf Leihbasis einen 200-3X, inzwischen wurde ein größerer, ein 300-3X, gekauft). Darüber hinaus nutzt Tesa für einige Materialrezepturen auch Maschinen der Arburg-Tochter Innovatiq.
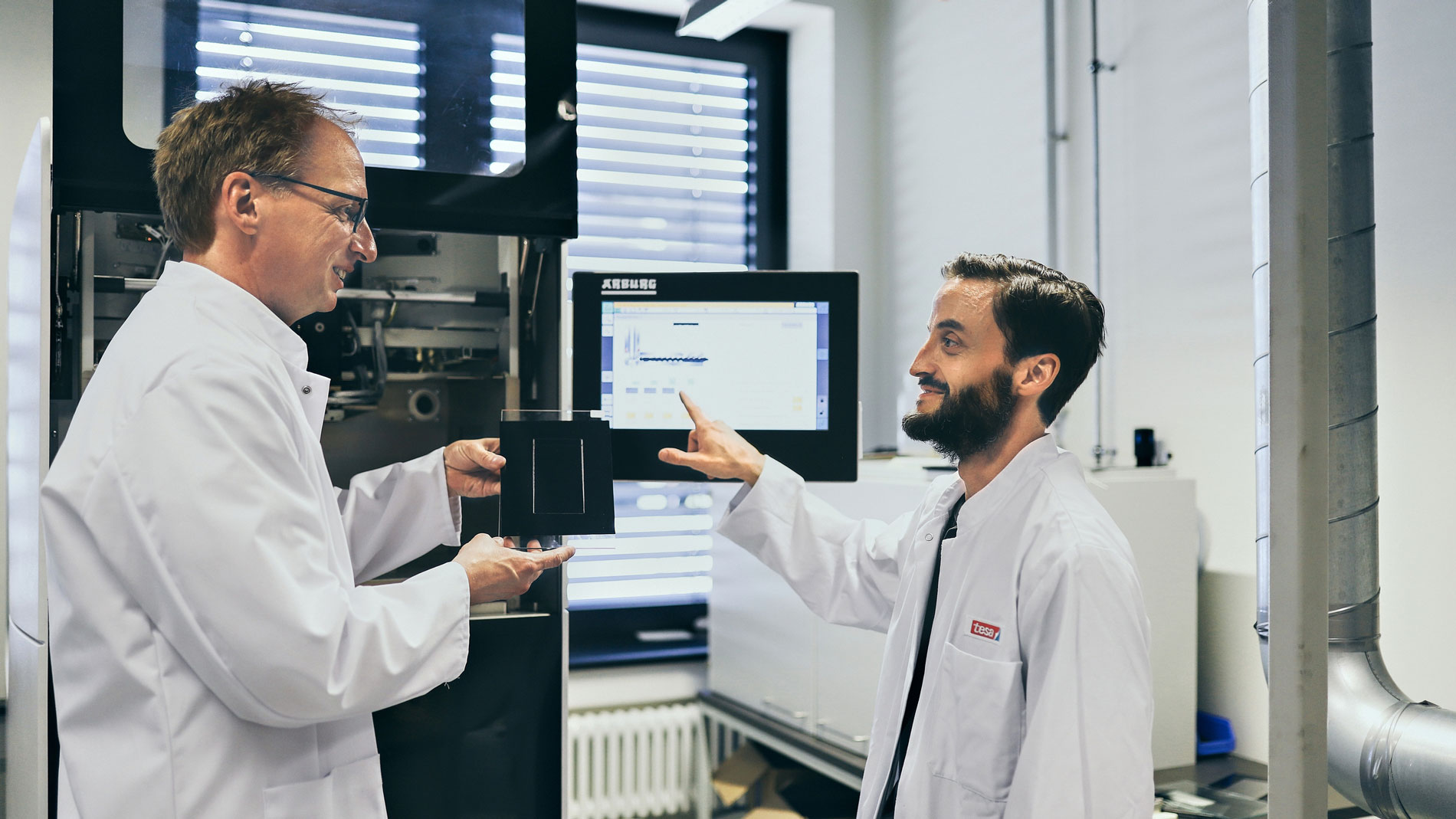
„Reaktiver 3D-Druck“ von Klebebändern
Der 3D-Druck von Klebebändern erfordert eine ausgeklügelte Systematik, schließlich steckt bereits in den Klebemitteln viel Basischemie, die zu einer Klebemasse verarbeitet wird. „Unser Prozess ist ein reaktiver 3D-Druck“, erklärt Virus, „das heißt, erst im Prozess entsteht der Klebstoff.“ Bei den 3D-gedruckten Tapes handelt es sich um Klebebänder, die bestimmte prozessbezogene Eigenschaften aufweisen. Im Gegensatz zu Flüssigkleber verfügen sie zum Beispiel über eine bestimmte Dicke und sind formstabil, was bei der Produktion von Smartphones oder dem Verkleben von Karosserieteilen bei der Pkw-Produktion notwendig ist.
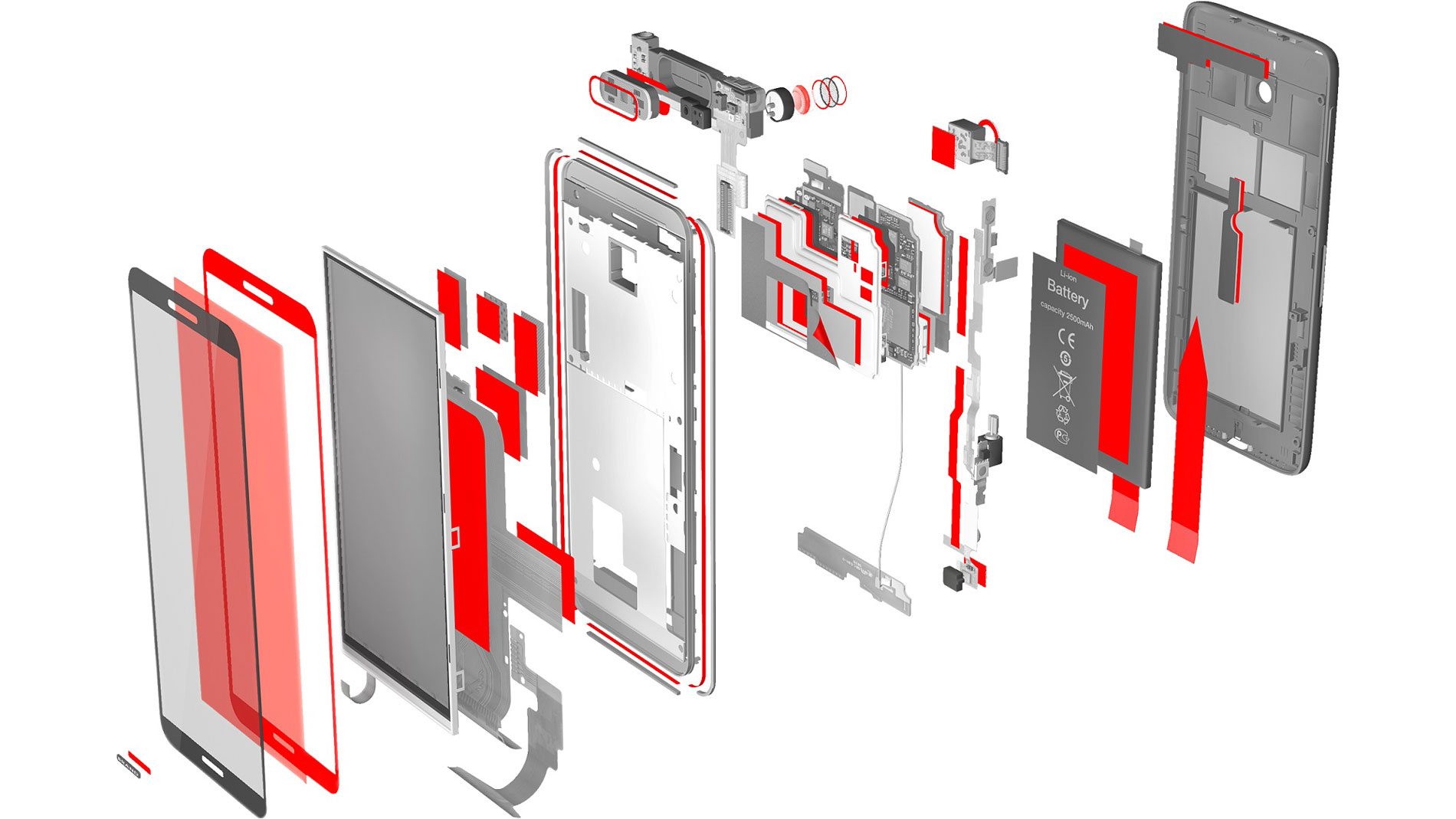
Um die Klebebänder mit einem Freeformer zu drucken, werden zuerst die Granulate in einem speziellen Verfahren hergestellt: Die sogenannte Unterwassergranulierung sorgt zuerst für die Abkühlung und eine konstante Benetzung des Granulats, das im trockenen Zustand wieder verkleben würde. In einem weiteren Schritt wird das Granulat benetzt (bzw. „gepudert“), sodass es gelagert werden kann. Beim Einsatz im Freeformer wird das Granulat erhitzt und durchmischt, sodass die Klebeeigenschaften wieder aktiviert werden.
Zusätzliche Mehrwerte lassen sich gut realisieren
Die bisherige Entwicklung des 3D-Drucks von Klebebändern ist bei Tesa bereits so weit gediehen, dass ein Großteil des bestehenden Produktportfolios theoretisch auch additiv gefertigt werden könnte. Allerdings ist der 3D-Druck im Vergleich zur traditionellen Herstellung der Klebebänder deutlich aufwendiger „und für die Herstellung unserer bisherigen Produkte in der Regel nicht wettbewerbsfähig“, so Virus, der die Chancen des 3D-Drucks eher bei Neuentwicklung von Produkten sieht. Entscheidend sei dabei, dass die neuen Produkte einen zusätzlichen Mehrwert im Vergleich zu bisherigen Klebelösungen bieten können.
Für solche weiter fortgeschrittenen Klebelösungen sieht Virus einen steigenden Bedarf, schließlich würden die Kunden von Tesa immer öfter mehr als eine reine Klebeverbindung verlangen, die zwei Oberflächen aneinanderfügt. Die Klebelösung sollte zudem noch elektrisch oder thermisch leiten bzw. isolieren oder ein Dichtmittel sein. „Solche besonderen Eigenschaften lassen sich mittels 3D-Drucks sehr gut realisieren“, erklärt Virus. So seien zum Beispiel Tapes in Sandwichbauweise mit mittleren Schichten aus ABS und TPU bzw. TPA denkbar, wodurch sich die mechanischen Eigenschaften des Klebebandes deutlich verstärken. Aufgrund dieser vielfältigen Möglichkeiten ist Virus davon überzeugt, „dass künftig 3D-gedruckte Klebelösungen nicht nur ein Nischenprodukt sein werden, sondern eine deutlich höhere Bedeutung gewinnen“.
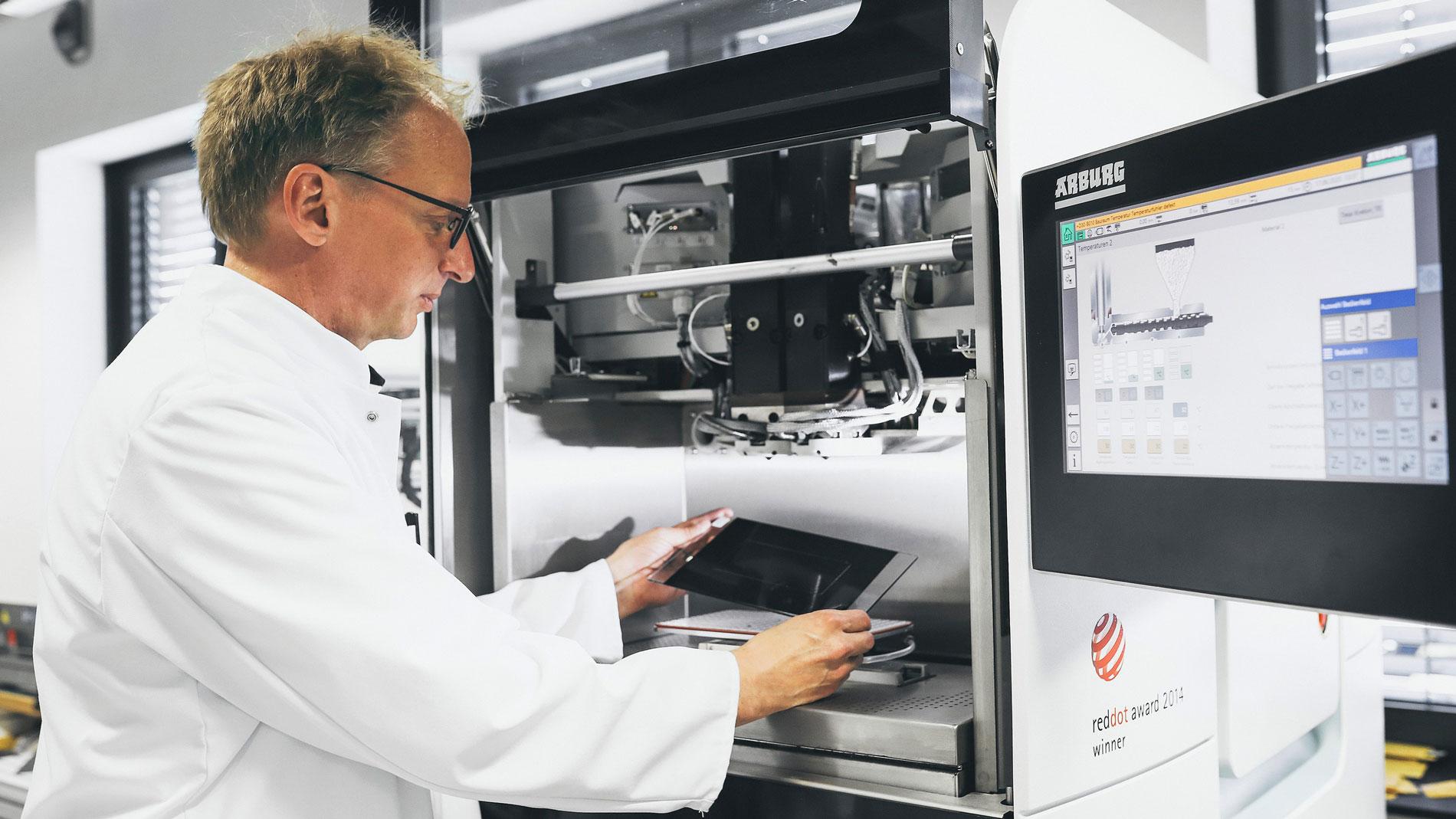
Ein weiterer Vorteil der mit dem Freeformer gedruckten Klebestreifen ist die deutlich höhere Nachhaltigkeit: Während beim bisherigen Ausstanzen der Klebestreifen bis zu 90 Prozent des Ausgangsmaterials im Abfall landen, „können wir mit dem 3D-Druck das Klebematerial zu 100 Prozent im Produkt einsetzen“, freut sich Virus.
Ein Beispiel für eine 3D-gedruckte Klebeanwendung war auf der Formnext 2021 auf dem Stand von Arburg zu bewundern: Hier wurde eine Verklebung von Mobiltelefon-Displays vorgestellt. Neben der Elektronik sieht Frank Virus das größte Potenzial für solche 3D-gedruckten Anwendungen in der Automobilindustrie, wobei hier die Potenziale sogar noch größer seien. „Denn in der Automobilindustrie ist der 3D-Druck schon länger ein Thema, und deshalb ist die Akzeptanz hier schon weiter entwickelt.“
Somit dürfte der 3D-Druck bei der Entwicklung neuer Produkte bei Tesa künftig eine wichtige Rolle spielen. Virus denkt dabei auch an weitere Vorteile wie zum Beispiel das Drucken in Wabenstrukturen oder die Möglichkeit, unterschiedliche Materialien in unterschiedlichen Schichten zu drucken. „Das kann mit dem Freeformer 300-3X und seinen drei Auftragseinheiten gut umgesetzt werden“, so Virus.
Von der Klebe- zur Systemlösung
Noch weiter in die Zukunft denkt Virus bei einer ganz neuen Produktkonzeption, „bei der wir uns teilweise von der Idee des Klebebandes wieder verabschieden“: Dabei geht es darum, festes Klebematerial direkt auf das Bauteil aufzutragen.
Mit dem direkten 3D-Druck auf Produkte würde Tesa sein Geschäftsmodell deutlich erweitern: Statt der auf Folien aufgebrachten Klebebänder, die zum Beispiel als Rollen an Kunden geliefert werden, würde dann ein ganzer Prozess inklusive 3D-Drucker, Material und Steuerung angeboten. Damit könnten sich dann zum Beispiel Automobilhersteller oder -zulieferer ihre individuelle Klebelösung direkt auf die Karosserie drucken.
Kein Wunder, dass diese Idee derzeit für viel Aufmerksamkeit im Unternehmen sorgt, denn damit würde Tesa vom reinen Anbieter von Klebelösungen zum Systemlieferanten und könnte sich womöglich ganz neue Geschäftsmöglichkeiten erschließen. Doch bis dahin ist noch viel Entwicklungsarbeit notwendig. Momentan beschäftigen sich Frank Virus und sein Team mit einer Vielzahl technischer Machbarkeitsstudien. Im nächsten Schritt für eine dezentrale Produktionslösung müssten noch weitere wichtige Hürden wie Zertifizierung, konstante Produktqualität und Datensicherheit genommen werden.
AM-VERFAHREN:
Additive Manufacturing für Polymere - material extrusion
Einen strukturierten Überblick in die komplexe und vielschichtige Welt der additiven Fertigungsverfahren, Prozessschritte und Anwendungsfelder liefert Ihnen unser AM Field Guide.
MEHR INFORMATIONEN UNTER:
Tags
- Additive Fertigung
- Elektrotechnik und Elektronik