04.03.2022
Schon seit Jahren werden im Werkzeug- und Formenbau 3D-gedruckte Formeinsätze genutzt. Durch additiv gefertigte Werkzeuge können die Produktionsprozesse im Kunststoff-Spritzguss oder im Aluminiumdruckguss deutlich effizienter werden. Dennoch vollzog sich der Einstieg der Additiven Fertigung in die eher konservativ geprägte Welt der Formenbauer im Vergleich zu anderen Branchen recht zäh. In der jüngsten Vergangenheit hat sich dies nun gewandelt: Durch neue Materialien und verbesserte Maschinenleistungen ist die Nachfrage nach 3D-gedruckten Formeinsätzen offenbar gestiegen. Auch für Hersteller von 3D-Druck-Anlagen ist dieser Markt mit einem Potenzial von mehreren Hundert Millionen US-Dollar wieder mehr in den Blickpunkt gerückt.
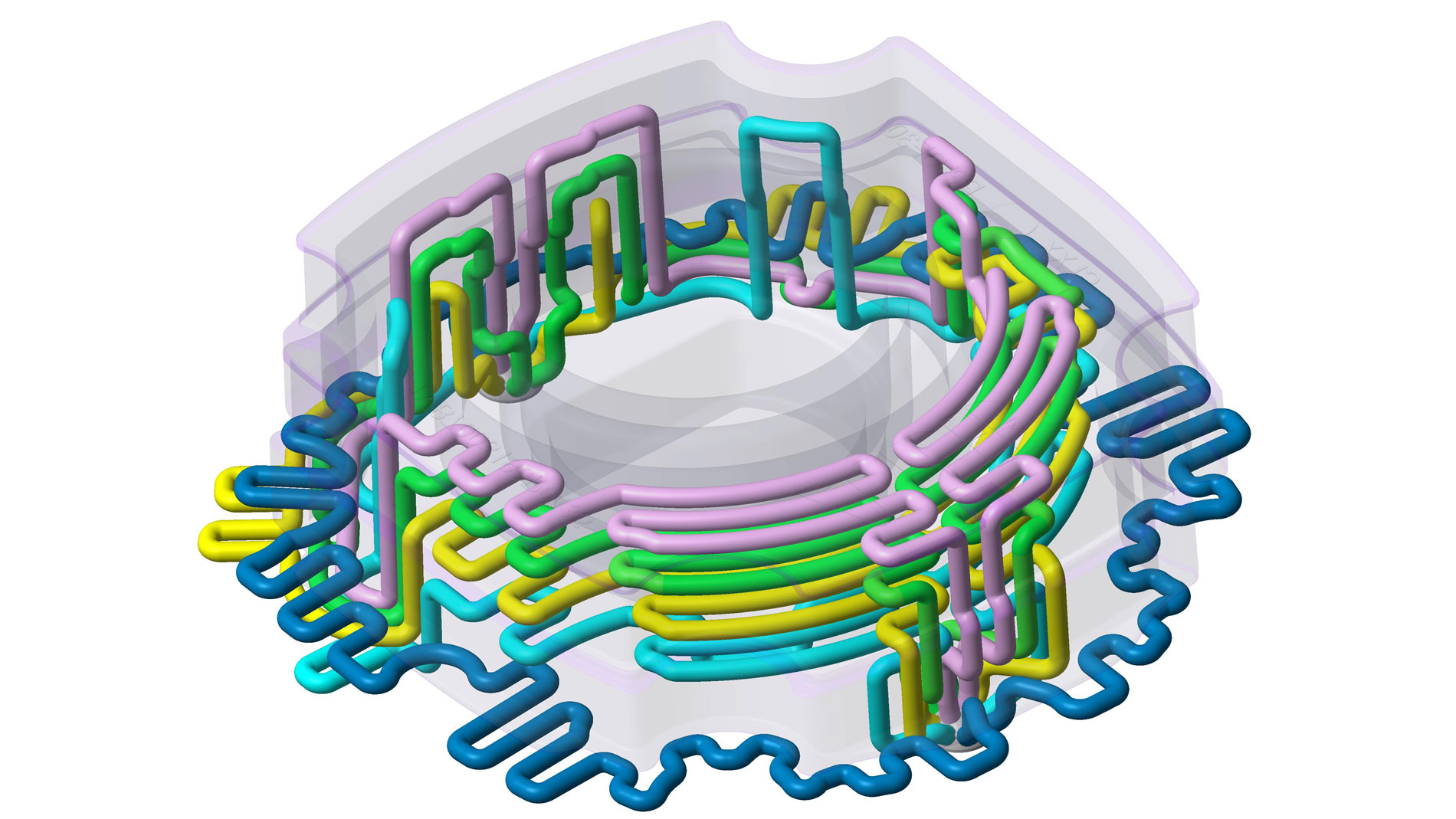
Auch wenn 3D-gedruckte Schuhsohlen deutlich mehr Style und Anziehungskraft besitzen, ist die weltweite Schuhproduktion konventionell geprägt: Für Sohlen, sofern sie nicht aus Leder sind, werden Formen angefertigt. Aus den Spritzgussanlagen fallen dann hunderttausend- oder millionenfach die Schuhkomponenten. Doch auch hier ist die Additive Fertigung mitunter nicht weit: Um ihre Spritzgussproduktion effizienter zu machen, nutzen Hersteller hin und wieder additiv gefertigte Formeinsätze. In der Regel werden diese im Powder-Bed-Fusion-Verfahren hergestellt.
In solchen 3D-gedruckten Formkernen sorgen intelligent platzierte und strömungsgerecht gestaltete Kühlkanäle für deutlich bessere Kühlraten und steigern so die Zykluszeiten. Das heißt: Die Kunststoffsohlen können die Spritzgussanlage schneller verlassen, die Produktionsrate steigt. Dieses recht einfache Prinzip gilt bei Schuhsohlen genauso wie bei Verschlusskappen von Kunststoffflaschen oder Bedienelementen in Fahrzeugen.
Eigentlich sind das beste Voraussetzungen, damit die Additive Fertigung im Werkzeug- und Formenbau in einem breiteren Umfang zum Einsatz kommen könnte. Und tatsächlich war der Formenbau eine der ersten Branchen, die den 3D-Druck für sich entdeckt hatten. Seit mehr als 15 Jahren sind 3D-gedruckte Formeinsätze auf dem Markt, doch aufgrund technologischer Einschränkungen und mangelnder Wirtschaftlichkeit tat sich die traditionelle Formenbaubranche in den Anfangsjahren recht schwer mit den Produkten aus dem 3D-Drucker.
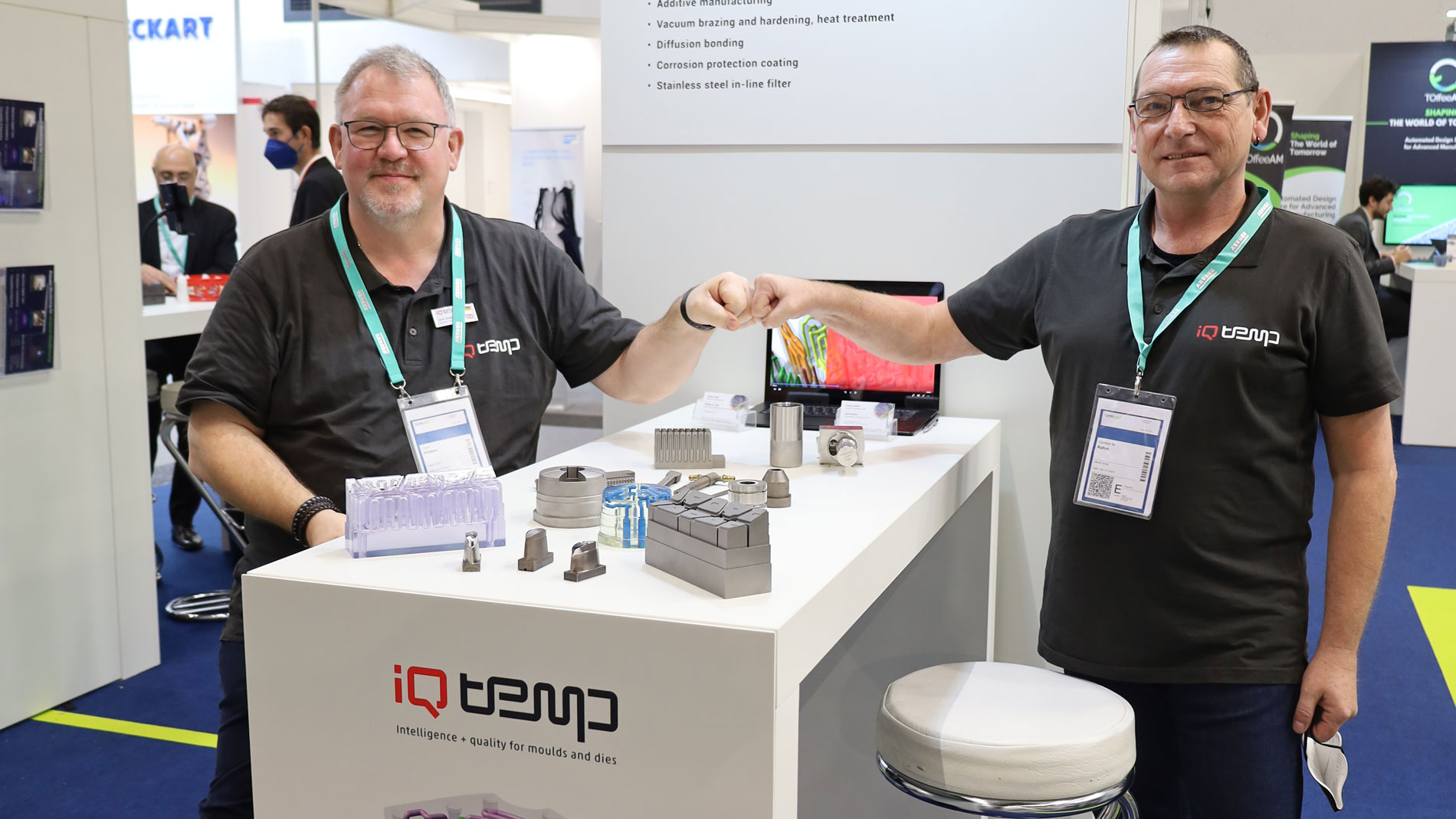
Trendwende durch mehr Vertrauen in Qualität und höhere Taktzeiten

Auf der Formnext 2021 war allerdings wieder eine leise Trendumkehr zu verspüren: An einigen Ständen zeigten Hersteller und Dienstleister 3D-gedruckte Formeinsätze. „Generell sehen wir ein gesteigertes Interesse im Markt. 3D-gedruckte Formeinsätze werden immer populärer“, berichtet Günther Rehm, Manager Sales & Marketing bei der Liechtensteiner Listemann Gruppe und Co-Gründer des Start-ups iQtemp GmbH, das sich auf additiv gefertigte Formeinsätze spezialisiert hat. „Die Formenbau-Branche gewinnt immer mehr Vertrauen in die Qualität.“
Mathias Schmidt-Lehr hat einen ähnlichen Trend im Bereich von Umformwerkzeugen ausgemacht: „Vor allem im Automobilbau ist uns ein verstärkter Einsatz von Werkzeugen mit 3D-gedruckten Komponenten aufgefallen“, so der Co-Gründer und Geschäftsführer des Hamburger AM-Beratungsunternehmens Ampower. „Bei Warm-Umformprozessen von Stahl scheinen aktiv, lokal gekühlte Werkzeuge mit additiv gefertigten Einsätzen einen Vorteil zu haben, weil man die Taktzeit optimieren, aber auch neue Umformgrade erreichen kann.“
Größere Materialvielfalt und schnellere AM-Anlagen
Dass nun im Formenbau die Nachfrage nach additiv gefertigten Formeinsätzen gestiegen ist, liegt auch an der technischen Entwicklung des 3D-Drucks, insbesondere in den Bereichen Pulverbettverfahren und Materialien. „So stand uns vor rund zehn Jahren für den additiven Formenbau zum Beispiel nur ein Material zur Verfügung: 1.2709 – ein Martensitstahl, der nicht besonders korrosionsbeständig ist“, erklärt Rehm. Heute seien rund fünf bis sieben für den Formenbau geeignete Stähle verfügbar – iQtemp nutzt für die eigene Arbeit drei davon: neben dem klassischen Martensitstahl den korrosionsbeständigen M789 und den W360, beide von Böhler, Letzterer ein weiterentwickelter 1.2343, der sich „besonders hoch härten lässt und sich deshalb besonders für den Aluminium-Druckguss eignet“, so Rehm.
Daneben haben sich auch die 3D-Druck-Anlagen in den letzten Jahren deutlich verbessert: Aus einem Laserstrahl wurden vier. Außerdem ist heute ein beheizter Bauraum verfügbar, was die Temperaturunterschiede bei der Produktion reduziert und dafür sorgt, dass die Werkstücke deutlich weniger spröde sind und weniger Eigenspannung aufweisen. „Dadurch sind nicht nur die Kosten für additiv gefertigte Formeinsätze deutlich gesunken, wir erzielen zudem ganz andere Materialqualitäten“, erklärt Rehm. „Wir erreichen heute ein Gefüge von gewalztem Stahl, die Oberflächen lassen sich hochglanzpolieren.“
Bei 15 Prozent der Spritzguss-Formen Additive Fertigung sinnvoll
Ob ein 3D-gedruckter Einsatz wirtschaftlich sinnvoll ist, „hängt sicherlich immer von der Anwendung ab“, sagt Rehm. Technisch gesehen würde sich bei rund 30 Prozent aller Formen der Einsatz additiv fertigen lassen (in den anderen Fällen sind die Bauteile zu groß). Bei der Hälfte davon sei das auch wirtschaftlich sinnvoll.
Bei einem weltweiten Marktvolumen der Formenbauindustrie von 68,5 Mrd. US-Dollar jährlich (2020, Quelle: Businesswire) entsprechen 15 Prozent der Formen einem Volumen von rund 10,3 Mrd. US-Dollar. Da die Kosten für den Formeinsatz 1 bis 5 Prozent der Kosten eines Werkzeugs ausmachen, ergibt sich daraus grob geschätzt ein Potenzial für additiv gefertigte Formeinsätze von rund 100 bis 500 Mio. US-Dollar jährlich.
Dies ist zwar deutlich weniger das Potenzial, das andere Branche wie Sportsware, Dental, Luftfahrt oder Automotive versprechen – aber ausreichend viel, damit auch Anlagenhersteller den Formenbau als interessanten Absatzmarkt entdeckt haben (zumal diese Branche konstante Wachstumsraten von rund 5 Prozent jährlich aufweist).
„Wir wollten den Unterschied machen“
„Der Bereich Werkzeug- und Formenbau ist für uns geschäftlich sehr interessant“, berichtet Frédéric Le Moullec, Sales Director Addup. Da der deutsche Markt laut Le Moullec etwa vier- bis fünfmal so groß ist wie der französische Heimatmarkt von Addup, hat sich Le Moullec mit seinem Vertriebsteam stark auf den deutschen Werkzeug- und Formenbau konzentriert. „Für uns als französisches Unternehmen war es wichtig, Maschinen im deutschen Markt zu platzieren – dabei wollten wir uns nicht in den bereits sehr umkämpften Industrien platzieren, auch wenn diese für uns natürlich auch wichtig sind. Wir wollten einen Unterschied machen, und haben uns deshalb sehr auf den Werkzeug- und Formenbau fokussiert.“
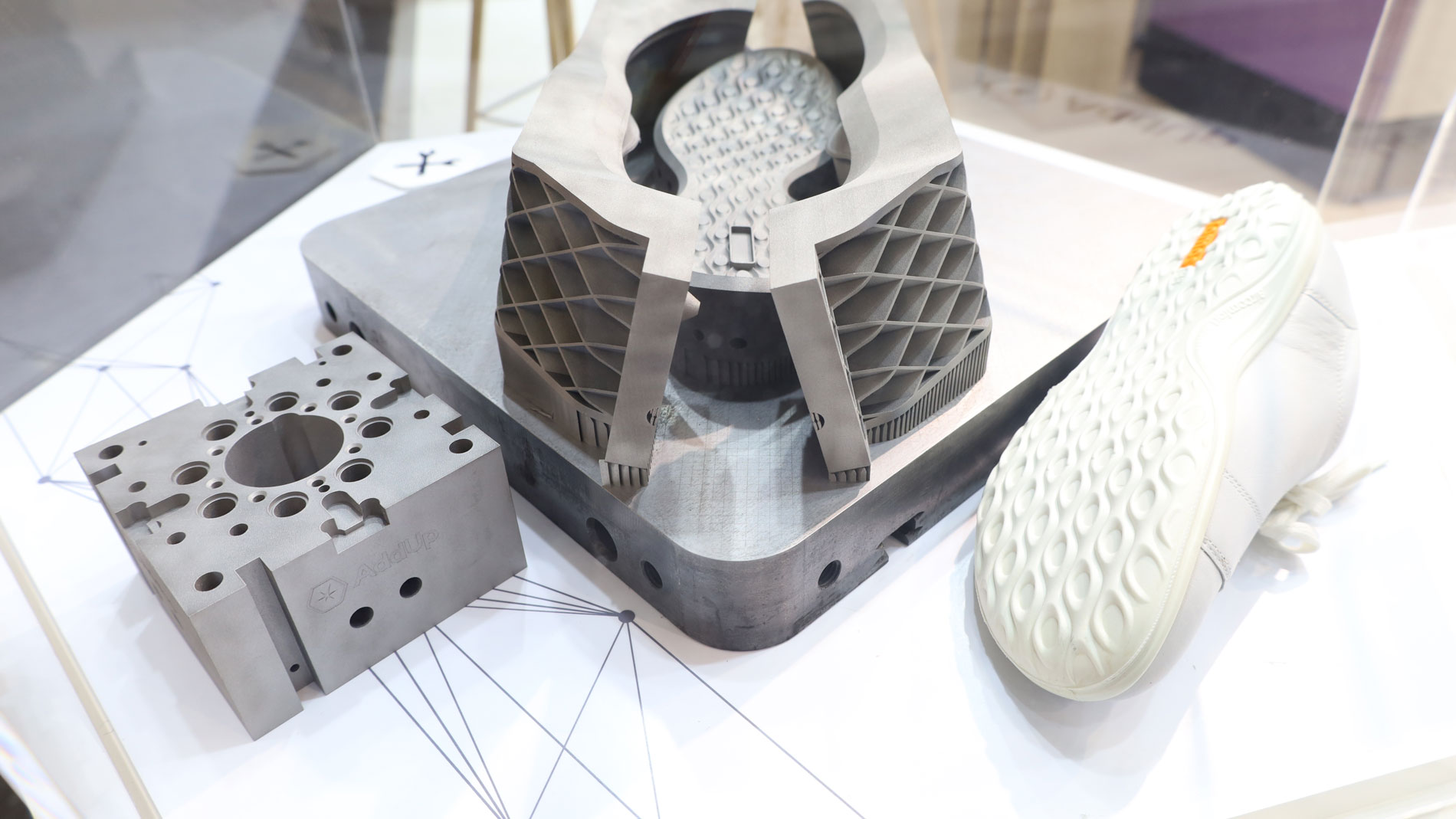
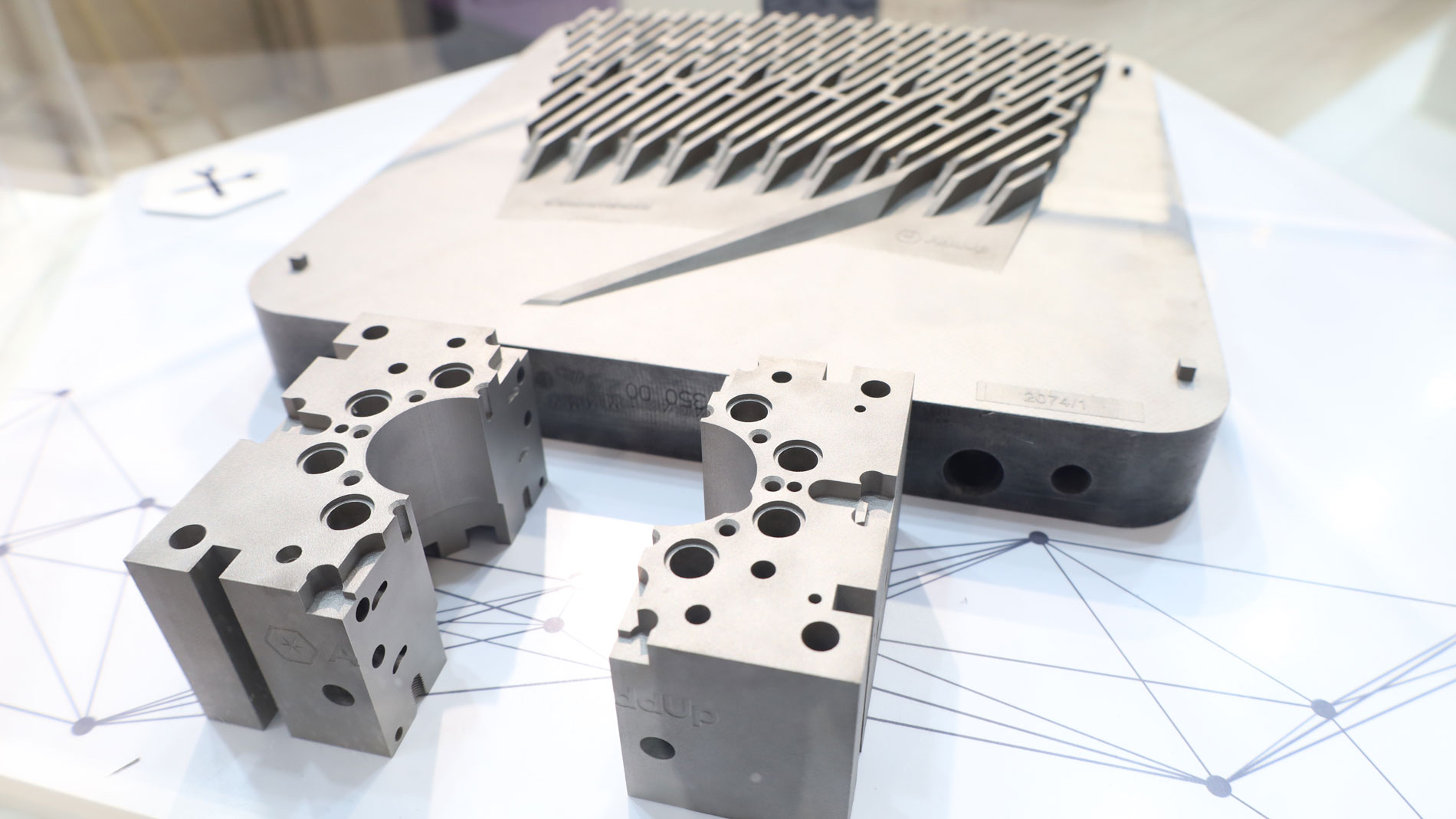
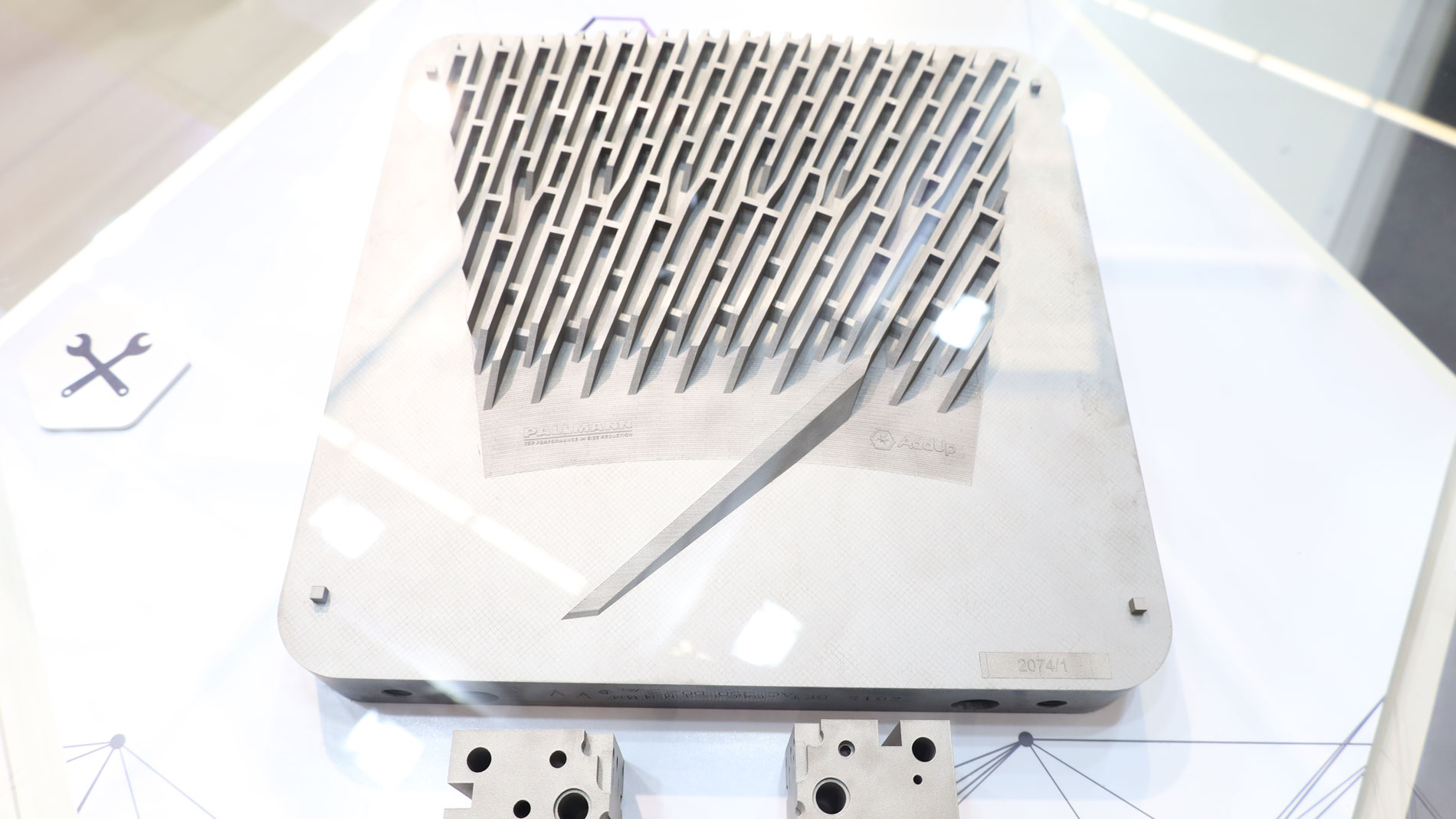
Die Ausrichtung zeigte sich auch auf dem Messestand von Addup auf der Formnext im November 2021. Hier präsentierte das Unternehmen Formeinsätze für Schuhformen oder auf FormUp-350-Maschinen 3D-gedruckte Formenkomponenten, die bei Michelin schon seit vielen Jahren in der Reifenproduktion eingesetzt werden.
Robust durch die Corona-Krise
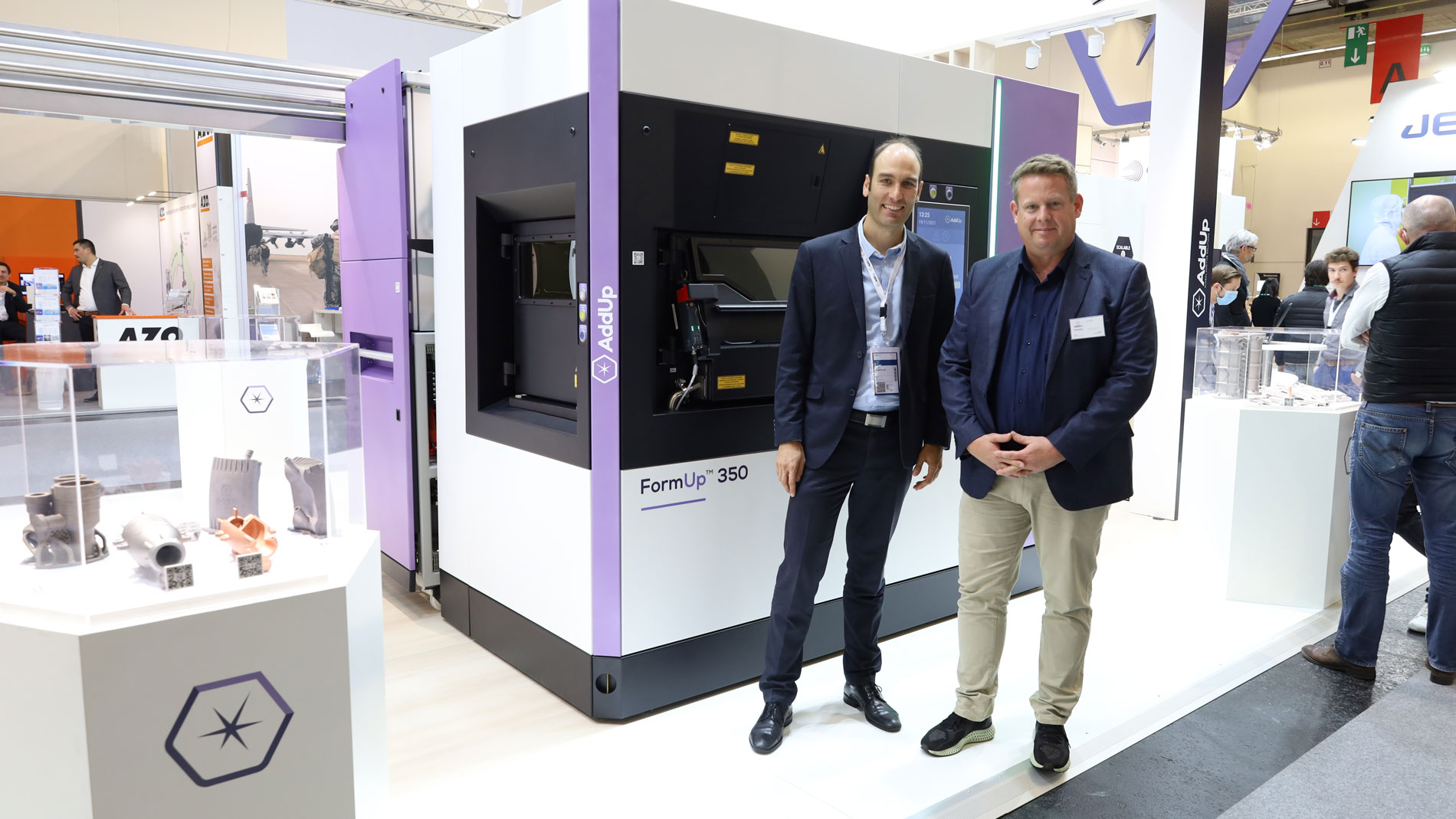
Auch Le Moullec sieht einen wichtigen Baustein für das Revival von AM im Werkzeug- und Formenbau in der Materialentwicklung. „Durch neue, zielgerichtete Materialien ist es noch besser möglich, die Qualität der additiv gefertigten Werkzeuge zu steigern und den Mehrwert im Vergleich zu den traditionell gefertigten Werkzeugen zu erhöhen.“ Das ist dann auch ein wichtiges Argument, wenn es um die wirtschaftliche Betrachtung geht – „denn diese entscheidet letztendlich darüber, ob ein Unternehmen in die additive Fertigung investiert oder nicht“.
Neben dem wirtschaftlichen Potenzial ist der Werkzeug- und Formenbau für Addup auch deshalb interessant, weil „wir hier die Chance haben, recht zügig in reale Anwendungen zu kommen, ohne – wie zum Beispiel in der Luftfahrt – einen 5- bis 10-jährigen Zertifizierungsprozess zu durchlaufen“, erklärt Le Moullec. Zudem scheint der Werkzeug- und Formenbau auch die Folgen der Corona-Krise besser weggesteckt zu haben als andere Branchen. „Während in der Luftfahrt die Investitionen deutlich zurückgefahren wurden, besteht weiterhin ein hoher Bedarf nach Werkzeugen und Formen – zum Beispiel für Schuhe oder neue Pkw-Modelle.“
Auf die Konstruktion kommt es an
Ob bei solchen neuen Formen der 3D-Druck sinnvoll ist, hängt neben den technischen Voraussetzungen noch von anderen Variablen ab. „Denn allein der Einsatz additiver Fertigung macht noch keine gute Form“, erklärt Formenbauexperte Günther Rehm. „Das Entscheidende ist die Konstruktion, da gibt es große Unterschiede.“ Wie groß der Leistungsunterschied zwischen additiv und konventionell gefertigten Formeinsätzen ist, lasse sich deshalb schwer beziffern. Erst wenn in der Konstruktion die vielfältigen Möglichkeiten der additiven Fertigung gekonnt ausgeschöpft werden, sei eine Reduzierung der Zykluszeiten im Produktionsprozess (gleichbedeutend mit höherem Output) von 10 bis 30 Prozent realistisch. „Im Idealfall erreichen wir sogar eine Verbesserung um 50 Prozent.“ Ein weiterer Vorteil sei, dass sich in der Regel zudem die Qualität der Kunststoffbauteile verbessere.
Laut Rehm hat die technologische Entwicklung der Produktionsanlagen auch die Kosten 3D-gedruckter Formeinsätze so weit nach unten gedrückt, dass der Unterschied zwischen 3D-gedruckten und konventionell gefertigten Formeinsätzen immer kleiner geworden ist. „Das liegt auch daran, dass wir bei den additiv gefertigten Bauteilen in der Regel einen deutlich geringeren Bedarf bei der Nacharbeitung nach dem Härteprozess haben, weil wir den Bauteilverzug in der Wärmebehandlung mit der additiven Fertigung vorab besser kompensieren können“, so Rehm. „Ganzheitlich gesehen müssen additiv gefertigte Formeinsätze deshalb nicht unbedingt teurer sein.“ Aber selbst wenn 10 bis 30 Prozent höhere Kosten entstünden, würden sich diese laut Rehm durch die höhere Produktionsleistung bereits nach wenigen Wochen oder Monaten wieder amortisieren.
AM-VERFAHREN:
Additive Manufacturing für Polymere - powder bed fusion
Einen strukturierten Überblick in die komplexe und vielschichtige Welt der additiven Fertigungsverfahren, Prozessschritte und Anwendungsfelder liefert Ihnen unser AM Field Guide.
MEHR INFOS UNTER:
iqtemp.com
Tags
- Werkstoffe und Halbzeuge
- Additive Fertigung
- Werkzeug- und Formenbau